Shawn Treacy
Staff Mechanical Engineer at Kulicke & Soffa- Claim this Profile
Click to upgrade to our gold package
for the full feature experience.
-
English -
Topline Score
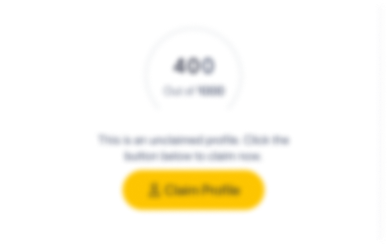
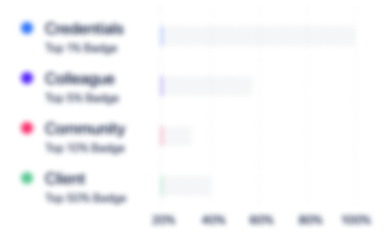
Bio


Experience
-
Kulicke & Soffa
-
Singapore
-
Semiconductor Manufacturing
-
700 & Above Employee
-
Staff Mechanical Engineer
-
Jan 2022 - Present
1. Testing and analysis for ball bonder machine design2. Servo stability and digital filter design3. Motion performance characterization and improvement
-
-
Senior Mechanical Engineer
-
Jan 2019 - Dec 2021
1. Testing and analysis for ball bonder machine design2. Servo stability and digital filter design3. Motion performance characterization and improvement
-
-
Advanced Mechanical Engineer
-
Aug 2017 - Dec 2018
1. Testing and analysis for ball bonder machine design2. Servo stability and digital filter design3. Motion performance characterization and improvement
-
-
-
Penn State University
-
United States
-
Higher Education
-
700 & Above Employee
-
Graduate Research Assistant (LORD Corporation Graduate Fellow)
-
2014 - Aug 2017
Pitch-Flap Stability of an Articulated Rotor with Fluidic Pitch Links (2016 AHS Technical Meeting on Aeromechanics Design for Vertical Lift conference paper and presentation)• Researched the aeroelastic stability of a medium duty, articulated helicopter with fluidic pitch links• Applied dynamics principles to derive the perturbation equations of motion for a rigid blade with pitch and flap degrees of freedom and an attached fluidic pitch link (4-DOF overall system) in hover and forward flight• Using Matlab, designed a program to determine the stability of the systemo Eigenanalysis techniques were used to determine the stability of the system for a helicopter in hover (constant coefficient A-matrix) while Floquet theory techniques were used for a helicopter in forward flight (periodic terms appear in the A-matrix)o Parallel computing techniques were used to increase the speed of the Matlab simulation in order to perform a significant parametric studyo Created x-y plots, 2-D and 3-D histograms, and contour plots for analysis purposesTesting and Model Verification of a Double Pumper Fluidic Pitch Link• Assumed lumped parameters and linear elemental equations to develop a model for the double pumper fluidic pitch link• Used Autodesk Inventor to modify an existing fluidlastic® isolator, which is used to represent the fluidic pitch link, in order to enable the connections of a newly-designed swappable inertia track and pressure transducers for the fluid chamberso Designed three circuits with varying inertia track length in order to vary location of the first notch frequencyo Designed a fourth circuit with a needle valve in order to vary the resistance of the system and to change the shape and depth of the notch• Developed and executed a test plan using static and dynamic stiffness tests on an MTS single-axis test machine • Compared experimental results to a Matlab simulation to ensure the veracity of the model for frequency-domain and time-domain simulations
-
-
Teaching Assistant
-
Aug 2013 - May 2017
Spring 2017Teaching assistant for ME 300 - Thermodynamics with the following responsibilities:• Grading of homework assignments, quizzes, and exams• Weekly office hoursFall 2013-Spring 2014Teaching assistant for ME 370 - Vibration of Mechanical Systems with the following responsibilities:• Designed homework assignments• Performed grading of homework assignments and exams• Held weekly office hours and study sessions for exams
-
-
-
Parker Lord
-
United States
-
Industrial Machinery Manufacturing
-
700 & Above Employee
-
Student Associate in Mechanical Technology and Development
-
Oct 2016 - Nov 2016
This was a short internship as part of my LORD Corporation Graduate Fellowship to work on the design and testing of a fluidic pitch link for my PhD research project. Additional short trips were also needed to complete the required work. Design: •Used Autodesk Inventor to modify an existing fluidlastic® isolator in order to enable the connections of a newly designed swappable inertia track and pressure transducers for the fluid chambers •Ensured that all of the necessary parts were machined or ordered and that the fluidic pitch link was correctly assembled Testing: •Devised a test plan that consisted of running static and dynamic stiffness tests on an MTS single-axis test machine while recording time, position, force, and the pressures in both chambers for each frequency
-
-
-
Cytec Industries - Coating Resins
-
North Augusta, SC
-
Engineering Intern
-
Mar 2012 - Aug 2012
Process Engineering: • Studied cooling tower flow and issues with cooling tower draining • Evaluated applicability of variable frequency drives for cooling tower and hot oil pump applications • Completed product design specification for a polymer coating chemical process including development of a budget proposal for equipment based upon calculated throughput requirements Program Management: • Managed project bids and awards for electrical, mechanical and insulation contractors
-
-
-
Paulstra CRC
-
Grand Rapids, MI
-
Mechanical Engineering Co-op
-
Oct 2009 - Jul 2011
Three month co-operative education rotations occurred in October 2009 - January 2010, April-July 2010, October 2010 - January 2011, and April-July 2011. Experience included: • Familiarization with the process of injection molding rubber engine and transmission mount components and testing of these components on MTS single-axis test machines; created reports for product engineers • Designed fixtures for GM engine mounts and transmission mounts using Solidworks • Thesis – “Guidelines for Reduced Decoupler Noise on Paulstra Hydromounts” • Electric Rep Press molding of decouplers • Tested and compared dynamics (phase levels, initiation of damping, frequency, stiffness) of hydraulic engine mounts • Employed LMS data acquisition system to record force, displacement, and pressure data and used impact hammer to test engine mount components for resonant frequencies and coherence • Processed data for vibration (force) comparisons, Fast Fourier Transforms of time data, and analysis of pressure data using LMS Test.Lab
-
-
-
Eaton
-
Ireland
-
Appliances, Electrical, and Electronics Manufacturing
-
700 & Above Employee
-
Mechanical Engineering Co-op
-
Apr 2008 - Jan 2009
Three month co-operative education rotations occurred in April-July 2008 and October 2008 - January 2009. Experience included: • Developed product line knowledge through teardown and build-up of superchargers • Assisted mechanical and quality engineers in performing durability, noise, and performance testing on superchargers • Supported Noise, Vibration, and Harshness engineers by using LMS Test.Lab to analyze noise and vibration levels • Analyzed and created customer reports for supercharger failures
-
-
Education
-
Penn State University
Doctor of Philosophy (Ph.D.), Mechanical Engineering -
Penn State University
Master of Science - MS, Mechanical Engineering -
Kettering University
Bachelor of Science (BS), Mechanical Engineering
Community
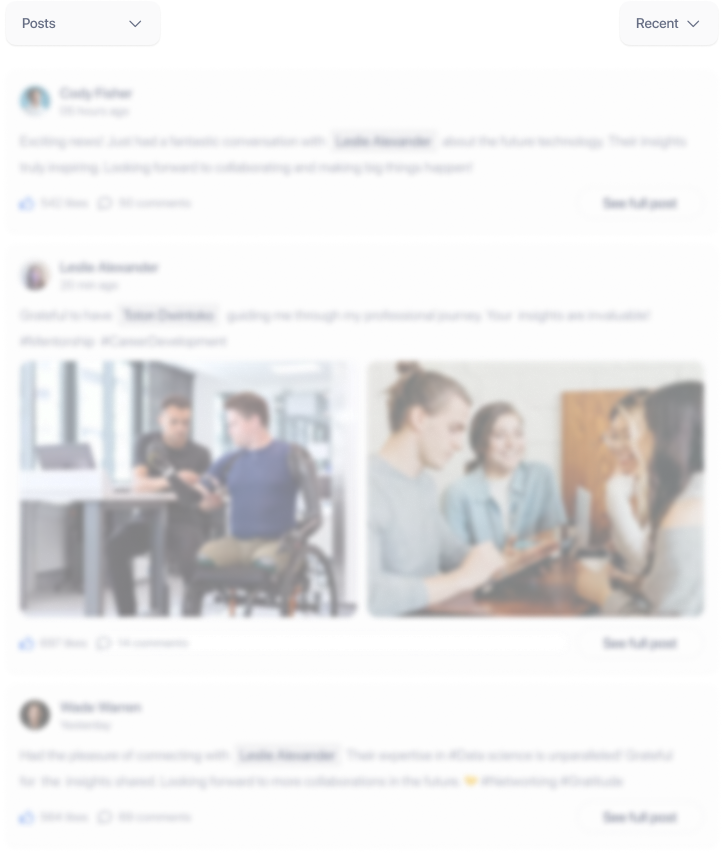