Shawn Radil
Production Manager at Gentex Corp.- Claim this Profile
Click to upgrade to our gold package
for the full feature experience.
Topline Score
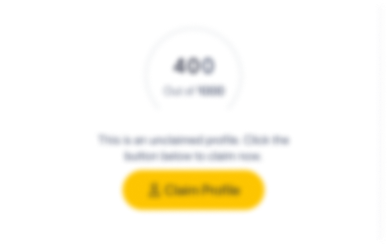
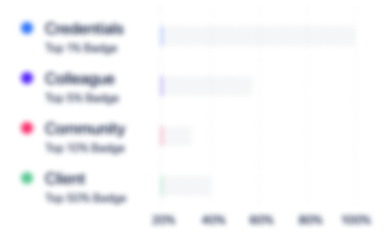
Bio


Experience
-
Gentex Corp.
-
United States
-
Defense and Space Manufacturing
-
300 - 400 Employee
-
Production Manager
-
May 2021 - Present
Manchester, New Hampshire, United States
-
-
-
Sealed Air Corporation
-
United States
-
Packaging and Containers Manufacturing
-
700 & Above Employee
-
Production Manager
-
Mar 2010 - May 2021
Ayer Ma. Sealed Air is the global leader in food safety and security, facilities hygiene, and product protection. Worldwide, the company generates $4.5 Billion in sales annually. The Ayer facility is the sole supplier for capital equipment for its Shrink Film, Stealth Film and Flowrap product lines. Facility is also responsible for the production of protective packaging machines including I-Pack, IMold, Pak-Tiger and Fasfil. (45) Direct Reports in a multi-shift union labor Production Facility. With the… Show more Sealed Air is the global leader in food safety and security, facilities hygiene, and product protection. Worldwide, the company generates $4.5 Billion in sales annually. The Ayer facility is the sole supplier for capital equipment for its Shrink Film, Stealth Film and Flowrap product lines. Facility is also responsible for the production of protective packaging machines including I-Pack, IMold, Pak-Tiger and Fasfil. (45) Direct Reports in a multi-shift union labor Production Facility. With the use of Lean Manufacturing practices and principles the following has been accomplished: Lean Six Sigma Certified through MoreSteam University (January 2015) Gold Key Award Winner January 2016 (Excellence in Operations) • 250 projects submitted world wide with 5 Gold Key Award Winners • Gross Profit increase from 18% to 23% L-Sealer product Line • EBITDA metric improvement .6% - 6.2% L-Sealer product line Improve On Time and Complete Metric from 67% to 98% • Creation of Process Maps for products and procedures • Implementation of visual factory tools and concepts • Lead morning Gemba walks to identify progress and opportunities throughout the production facility • Implemented Kanban pull signals and point of use inventory • Implementation of 5S • Improved production efficiency by 17% • Creation of Standard Work Documentation (SWIS) for 70% of active Sub-Assemblies $750K Labor and Inventory Savings from Kaizen Implementation • Project Lead for the creation of the Kaizen Process and FMEA • Assists in providing Kaizen training, including “Leading Kaizens” for all employees • Concentrated focus involving all employees in Continuous Improvement efforts Product Lead Times Improved by 70% • Implementation of Heijunka Visual Scheduling • One Piece Flow Systems in in 50% of the Production Facility • Inventory reduction of $700K over 3 year span • Rework Labor Hours reduced by 83% Show less
-
-
-
NCAA
-
United States
-
Higher Education
-
700 & Above Employee
-
Ice Hockey Referee
-
Sep 1997 - Mar 2019
Boston Ma. Officiate Junior and Collegiate levels of hockey on the East Coast of the United States.
-
-
-
-
Director of Manufacturing
-
Sep 2004 - Oct 2009
School Specialty – Delta Education Nashua NH September 1999 – October 2009 Director of Manufacturing (2004 – 2009) Provide leadership and business support for the industries leader in Hands on Science Educational Products and Equipment: consisting of strategic planning, implementation and operational management to various initiatives including: Reducing Direct Labor from 2.7M to 1.6M while increasing revenues from $68M to $131M Implementation of Cellular Manufacturing… Show more School Specialty – Delta Education Nashua NH September 1999 – October 2009 Director of Manufacturing (2004 – 2009) Provide leadership and business support for the industries leader in Hands on Science Educational Products and Equipment: consisting of strategic planning, implementation and operational management to various initiatives including: Reducing Direct Labor from 2.7M to 1.6M while increasing revenues from $68M to $131M Implementation of Cellular Manufacturing environment with Lean Manufacturing practices In collaboration with Planning and Materials Teams, developed and maintain detailed Planning, Scheduling and Capacity Systems via Oracle 11i Installation of automated packaging, counting and cutting equipment reducing $180K in Labor Cost Implementation of Self Directed Work Teams Increased annual efficiency ratings from 76% to 85.03% Increased customer on time delivery from 96% to 99.69% Implemented Kan-Ban back-flush system for high volume common parts. Reduced Warehouse Labor by $40K EBS (Electronic Business Systems) Manufacturing Project Lead Implementation of Oracle 11i Re-Implementation of Radio Beacon (RF Warehouse Management System) Created Paperless Warehousing and Distribution Facility Increase Capacity by 300% Created Operation System Sequencing with the use of Routings Controlled the delivery of product with use of demand pull signals Reduced staged material - inventory in queue by 40% Reclaimed 19,000 Sq Ft. for additional space required for production capacity Reduced completion of average job cycle times from 18 to 5 days
-
-
Production Manager
-
Oct 2001 - Sep 2004
Management and Leadership Staffed labor force of 200 during peak seasons Responsible for Development and Leadership of 4 Supervisors Conduct bi-annual performance reviews Lead weekly staff meetings New Business Acquisitions and Development Team member for Neo-Sci acquisition February 2005 Project lead for moving $12M business unit (Neo-Sci; Managed the installation of all production infrastructure to host System Developed BOM and Routing Standards for Frey… Show more Management and Leadership Staffed labor force of 200 during peak seasons Responsible for Development and Leadership of 4 Supervisors Conduct bi-annual performance reviews Lead weekly staff meetings New Business Acquisitions and Development Team member for Neo-Sci acquisition February 2005 Project lead for moving $12M business unit (Neo-Sci; Managed the installation of all production infrastructure to host System Developed BOM and Routing Standards for Frey Scientific Facilitated production implementation of sister company Frey in to Nashua Facility; Led a production team consisting of 100 direct reports. Setting strategic goals and objectives that comply with corporate initiatives. Creating career guidance for supervisory and leadership staff. Created cost spending allocation accounts in order to track labor by product lines. Managed the re-structure of BOM's (Bills Of Materials) to accurately and clearly define labor cast and requirements Increased customer on time delivery from 83% to 96.34% Increased overall Quality rating from 96% to 99.2% Assisted on original Oracle and Radio Beacon implementation teams Implemented $6M of automated-mechanical warehouse and distribution equipment Created and adhered to controlled spending budgets Managed Turn-Key outsource program consisting of high volume sub-assembly activity
-
-
Manufacturing Process Engineer
-
Aug 1999 - Oct 2001
Responsible for process improvements and operating cost reduction for a 337,000 Sq. Ft. manufacturing facility. Implemented measurement and metrics systems in which to track production efficiency, quality and operating costs Assisted on "Factory of the Future" designs and ROI's. This project was meant to fully automate a pick-pack and ship process. Reduced warehouse picking cycle time by 150% Developed process times and applied timing standards to over 35,000 part numbers… Show more Responsible for process improvements and operating cost reduction for a 337,000 Sq. Ft. manufacturing facility. Implemented measurement and metrics systems in which to track production efficiency, quality and operating costs Assisted on "Factory of the Future" designs and ROI's. This project was meant to fully automate a pick-pack and ship process. Reduced warehouse picking cycle time by 150% Developed process times and applied timing standards to over 35,000 part numbers and 9,000 Finished goods in which to track labor cost, efficiency and productivity standards
-
-
-
-
Project Facilitator
-
Jan 1998 - Aug 1999
Responsible for continuous manufacturing and process improvements for the Capacitive business unit Responsibilities include leading the implementation team of DFT (Demand Flow Technology) in assistance with the JCIT (John Costanza Institute of Technology) teams Working in a team based environment with the common goal of reducing manufacturing costs by 15% Managing, designing and implementing new production concepts and equipment Measuring improvement of processes, procedures and… Show more Responsible for continuous manufacturing and process improvements for the Capacitive business unit Responsibilities include leading the implementation team of DFT (Demand Flow Technology) in assistance with the JCIT (John Costanza Institute of Technology) teams Working in a team based environment with the common goal of reducing manufacturing costs by 15% Managing, designing and implementing new production concepts and equipment Measuring improvement of processes, procedures and equipment (Quality, productivity and Cost)
-
-
Manufacturing Team Leader
-
Jan 1993 - Jan 1998
Led and managed 50 - 70 Manufacturing Associates in a multi-shift Touch Screen manufacturing operation. This operation is responsible for supplying Microtouch facilities world wide as well as domestic and international customers with Touch Screens and supporting devices. Writing and communicating performance reviews Adhering to a detailed build plan Implementing and supporting continuous improvement efforts Maintaining and adhering to ISO 9001 Standards Working closely with… Show more Led and managed 50 - 70 Manufacturing Associates in a multi-shift Touch Screen manufacturing operation. This operation is responsible for supplying Microtouch facilities world wide as well as domestic and international customers with Touch Screens and supporting devices. Writing and communicating performance reviews Adhering to a detailed build plan Implementing and supporting continuous improvement efforts Maintaining and adhering to ISO 9001 Standards Working closely with Manufacturing and Application Engineers in which to troubleshoot process or product concerns
-
-
Repair Tech - Assembler
-
Jan 1991 - Jan 1993
-
-
Education
-
MoreSteam University
Greenbelt Lean Six Sigma -
John Costanza Institute of Technology
Certificate, Demand Flow Technology -
Shawsheen Regional Vocational Technical High School
High School Diploma
Community
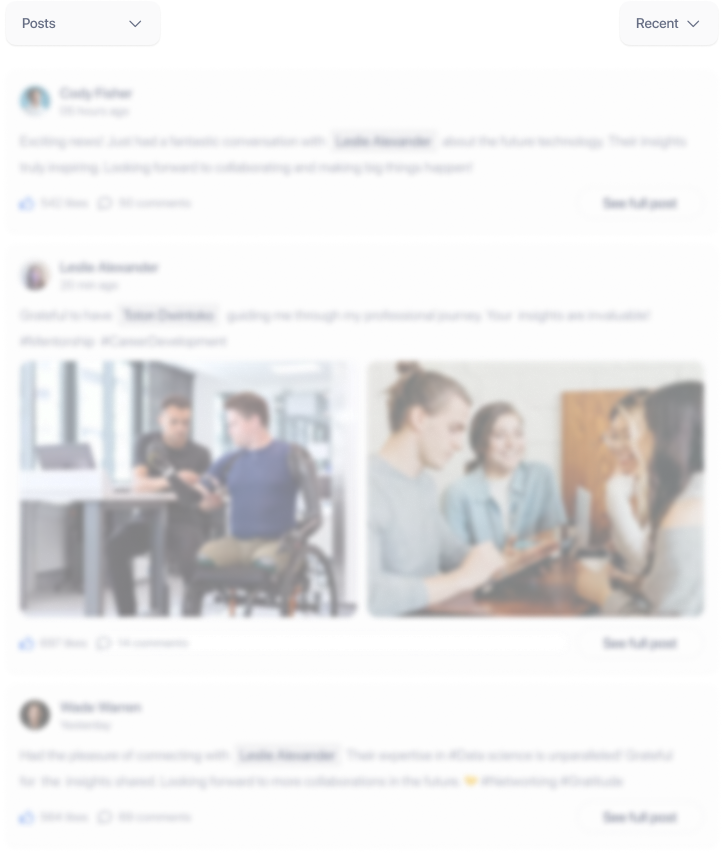