Shane Furness
General Manager - Contract Manufacturing at Halo Food Co. Limited.- Claim this Profile
Click to upgrade to our gold package
for the full feature experience.
Topline Score
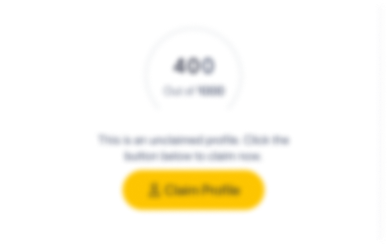
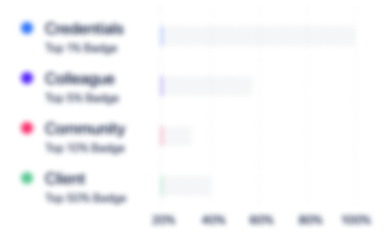
Bio

Donal O'Brien
I have worked with Shane Furness for 10 years in my capacity as senior finance manager at General Mills and can highly recommend his leadership skills, ability to build a team and hold them accountable to drive actions. Shane was a key driver behind the implementation of the Oliver Wight accreditation for not only the Mount Waverley plant but provided support for Sydney and Brisbane sites as well. Shane has a high financial awareness and implemented strategies to reduce costs. He has delivered significant results in his operations executive role in the New Zealand business, by developing and managing budgets, and initiating and implementing productivity initiatives.

Tara Sargis
For 3 years I worked closely with Shane leading the General Mills New Zealand business as members of the NZ Executive Team. Shane provided the New Zealand business with a hands on, collaborative and strategic leadership style and during his time successfully delivered a huge amount of positive change in the supply chain area. Shane was able to partner with all areas of the business locally and internationally to deliver outstanding results in both people and business growth. This was a testament to his proactive approach and focus on his team, suppliers and the customer. Shane is a well-respected member of the team and was great to work alongside.

Donal O'Brien
I have worked with Shane Furness for 10 years in my capacity as senior finance manager at General Mills and can highly recommend his leadership skills, ability to build a team and hold them accountable to drive actions. Shane was a key driver behind the implementation of the Oliver Wight accreditation for not only the Mount Waverley plant but provided support for Sydney and Brisbane sites as well. Shane has a high financial awareness and implemented strategies to reduce costs. He has delivered significant results in his operations executive role in the New Zealand business, by developing and managing budgets, and initiating and implementing productivity initiatives.

Tara Sargis
For 3 years I worked closely with Shane leading the General Mills New Zealand business as members of the NZ Executive Team. Shane provided the New Zealand business with a hands on, collaborative and strategic leadership style and during his time successfully delivered a huge amount of positive change in the supply chain area. Shane was able to partner with all areas of the business locally and internationally to deliver outstanding results in both people and business growth. This was a testament to his proactive approach and focus on his team, suppliers and the customer. Shane is a well-respected member of the team and was great to work alongside.

Donal O'Brien
I have worked with Shane Furness for 10 years in my capacity as senior finance manager at General Mills and can highly recommend his leadership skills, ability to build a team and hold them accountable to drive actions. Shane was a key driver behind the implementation of the Oliver Wight accreditation for not only the Mount Waverley plant but provided support for Sydney and Brisbane sites as well. Shane has a high financial awareness and implemented strategies to reduce costs. He has delivered significant results in his operations executive role in the New Zealand business, by developing and managing budgets, and initiating and implementing productivity initiatives.

Tara Sargis
For 3 years I worked closely with Shane leading the General Mills New Zealand business as members of the NZ Executive Team. Shane provided the New Zealand business with a hands on, collaborative and strategic leadership style and during his time successfully delivered a huge amount of positive change in the supply chain area. Shane was able to partner with all areas of the business locally and internationally to deliver outstanding results in both people and business growth. This was a testament to his proactive approach and focus on his team, suppliers and the customer. Shane is a well-respected member of the team and was great to work alongside.

Donal O'Brien
I have worked with Shane Furness for 10 years in my capacity as senior finance manager at General Mills and can highly recommend his leadership skills, ability to build a team and hold them accountable to drive actions. Shane was a key driver behind the implementation of the Oliver Wight accreditation for not only the Mount Waverley plant but provided support for Sydney and Brisbane sites as well. Shane has a high financial awareness and implemented strategies to reduce costs. He has delivered significant results in his operations executive role in the New Zealand business, by developing and managing budgets, and initiating and implementing productivity initiatives.

Tara Sargis
For 3 years I worked closely with Shane leading the General Mills New Zealand business as members of the NZ Executive Team. Shane provided the New Zealand business with a hands on, collaborative and strategic leadership style and during his time successfully delivered a huge amount of positive change in the supply chain area. Shane was able to partner with all areas of the business locally and internationally to deliver outstanding results in both people and business growth. This was a testament to his proactive approach and focus on his team, suppliers and the customer. Shane is a well-respected member of the team and was great to work alongside.

Experience
-
Halo Food Co. Limited.
-
New Zealand
-
Wellness and Fitness Services
-
1 - 100 Employee
-
General Manager - Contract Manufacturing
-
Oct 2022 - Present
Executive accountability for the contract manufacturing business including the 4 Australian manufacturing facilities & central warehouse. Responsible for the leadership, development & execution of business strategy & P&L across the sales and operational process for contract manufacturing.
-
-
Head of Operations (Australia & New Zealand)
-
Aug 2019 - Feb 2023
Executive accountability for the end to end supply chain and Operation at Halo Food Co (Formerly Omniblend performance nutrition & Keytone Dairy) across Australia & New Zealand & reporting to the company CEO. Responsible for the leadership & development of business & operational strategy as a key member of the Keytone & Omniblend executive team. Joint Accountability for the overall strategy, planning and execution of Human Resources, business improvement systems, people and process for logistics, supply chain, full P&L, cash management, capital, planning & procurement, S&OP, sourcing, Quality, food safety & compliance for our 7 manufacturing sites across Australia & New Zealand1 X Blending site in Melbourne's North1 X Powder packing and Toll packing site in Melbourne's South East1 X UHT bottling plant in Melbourne's West1 X Warehouse DC in Melbourne's South East1 X Healthy snacks & bar plant in Sydney's West2 X Powder blending, canning and packing plants in Christchurch New Zealand Show less
-
-
-
Omniblend performance nutrition (Acquired by Halo Food Co Limited)
-
Melbourne, Australia
-
Business Operations Manager
-
May 2017 - Aug 2019
Multi - site management of the Omniblend supply chain & operation including 3 manufacturing facilities consisting of powder blending, Contract manufacturing and packing and UHT bottling plant Key functional accountability for supply chain (S&OP process), site and functional management, logistics, transport, planning, purchasing & procurement, human & food safety, quality, production & warehousing, maintenance and engineering. Report to Managing Director/owner - Accountable for the strategic direction of the sites and their operations - Accountable for business improvement planning, development and execution - Accountable for the development & execution of the operational priorities including business & people objectives, continuous improvement, change management and new business implementation - Implementation and execution of objective setting & personal development system for functional managers and key business personnel. - Structured implementation of root cause analysis, corrective and preventative action techniques - Champion New Product Development and its implementation in to the business Acquisition execution and integration of new site and Toll packing business Show less
-
-
-
Ivan's Pies
-
Australia
-
Food and Beverage Manufacturing
-
1 - 100 Employee
-
Operations Manager
-
Jun 2015 - May 2016
Operations Manager accountable for Procurement, planning, manufacturing & warehousing Report to Managing Director/owner - Accountable for the execution of procurement, planning, manufacturing & warehousing for the plant - Responsible for development & execution of the operational priorities including people, process & KPI development, change management and new business implementation - Responsible for the management of maintenance, quality and safety systems - Objective setting & personal development for production managers with regular review - Liaise between cross functional departments to plan, execute and problem solve key priorities - Work closely with sales to develop timelines and priorities for NPD KEY ACHIEVEMENTS - Customer service level improvement from 74% to +95% - Performance to plan improvement from 69% to 92% - Packing efficiency improvement of 30% - Ground up development and implementation of full preventative maintenance system - Developed and executed restructure and change management of plant personnel - Negotiated and sourced contract maintenance team to reduce downtime and improve capacity Show less
-
-
-
General Mills
-
United States
-
Manufacturing
-
700 & Above Employee
-
Manager - Chilled Ready Meals Manufacturing (Business team /SBU member)
-
May 2013 - Jun 2015
Manager of Chilled Ready Meals manufacturing in the Melbourne plant. Accountable for the strategic planning and manufacturing of the make to order Chilled Ready Meals plant (new business with 4 week shelf life). - Accountable for the strategic planning and manufacturing of the make to order chilled ready meals plant (new business with 4 week shelf life)- Strategic Business team - Operations representative accountable for the strategic direction and execution of the chilled ready meals business. (Sales, Marketing, Finance, operations)- Accountable for the development and management of the chilled ready meals COGM (specifically labour, materials, usage, productivity, efficiency, production plan performance, NPD/capital implementation, Overheads, safety and quality) - Accountable for the development /execution of all Chilled Ready Meals KPIs and plant scorecard coupled with continuous improvement/productivity initiatives- Management of quality systems (AIB regulatory requirements, Implementation of ISO 22000) KEY ACHIEVEMENTS- 2014 productivity savings of $1.2MM in labour efficiency & $.800MM in overhead driven by process improvements, quick changeovers, labour utilisation & product re design.- Customer service level improvement from 82% to +95%- Performance to plan improvement from 87% to 95%- Implemented objective setting and personal development plans for key managers and chilled meals leaders- Lead the Chilled ready meals waste reduction initiative Show less
-
-
Supply Chain Operations Manager (New Zealand business unit executive)
-
Sep 2009 - May 2013
Supply chain operations manager for the NZ business unit. Executive leadership team member- Accountable for the end to end operation for the New Zealand business unit including all people & budgetary requirements.- Executive team responsibility to develop, support and deliver total business strategy and operational performance priorities- Accountable for the manufacturing site, the New Zealand supply chain leadership team & functional managers across procurement, safety, quality, production, maintenance, engineering, purchasing, HR, R&D, Vendor Managed Inventory (VMI/VRP), transport, logistics and customer service- Management of the supply planning from Australia, UK, Spain via 3rd party logistics partners - Accountable for the manufacturing plant scorecard (customer service, quality, safety, system performance, cost per case, maintenance, environment, people initiatives, community service)- Responsible for 1-5 year development and execution of site capital plans - Overall responsibility for holistic margin management program (productivity improvement)- Responsible for developing and executing total business cross functional people and organisational development plans (9 block system, 4MAT, Solution focus, LSI)KEY ACHIEVEMENTS- Lead the change management of the New Zealand operation improvement plan; Plant score card performance from 1.8 rating to a 4.5 rating (1 being unsatisfactory, 5 significant over delivery)- COGM productivity saving of 7% 2010, 5.5% 2011, 5.5% 2012- Safety behaviour culture change resulting in ZERO recordable injuries from 2011 – 2013 - NZ Supply Chain overheads held flat year on year from 2009 to 2013 (incl. 4% industry inflation) - Negotiated and executed a reduction of 5% chilled transport costs in 2012- 3 consecutive years of delivering favourable budget & a cost per case reduction of 2.5%- Successful negotiation of multiple Collective Enterprise Agreements (CEA’s)- Drive and manage a 40% reduction in Mould complaints Show less
-
-
Production Manager
-
Jan 2008 - Sep 2009
Production Manager of Latina pasta & sauce manufacturing.- Accountable for the manufacturing of the chilled production plant (Latina Pasta & Sauce – 8-10 week shelf life)- Responsible for the development and management of production strategies & cost (safety, labour, environment, usage, case fill, master schedule performance, inventory record accuracy, quality, planning, system performance, waste & yields, people growth)- Collaborate cross functionally to achieve manufacturing strategies and objectives- Responsible for weekly materials and scheduling requirements- Management of both Ready Workforce and Skilled recruitment agencies including monthly KPI meetings.KEY ACHIEVEMENTS- Successful management & support for the Mt. Waverley Enterprise Agreement (EBA)- Lead and manage the implementation of Continuous Improvement (CI), root cause analysis and solution focus- Lead implementation of Daily Management System (DMS) covering accountability, review and reporting of manufacturing KPIs - Lead the start up/integration of Bernards bakery co packer for production of Latina breads- Develop and drive production productivity initiatives resulting in 3% of COGM savings- Built succession and capability plans for key production personnel Show less
-
-
Production Manager - Business improvement & Oliver Wight systems implementation team
-
Aug 2006 - Jan 2008
Production Manager of the Pasta & Sauce manufacturing plant.Core team member for the Oliver Wight system and business improvement project and implementation- Implementation of Oliver Wight principals- Core team members for implementation of Inventory record accuracy - Core team member for production planning and shop floor control (Master schedule performance, Issuing materials to production work orders, Continuous elimination of waste programs, Daily management systems, Inventory managed systems improvements.)KEY ACHIEVEMENTS- Achievement of Oliver Wight Class A certification for Australian business- Master schedule performance improvement to 95%- Inventory records accuracy improvement from 23% to 95% warehouse managed- Significant change in manufacturing culture driven by behaviour and systems improvement Show less
-
-
-
Mars
-
United States
-
Manufacturing
-
700 & Above Employee
-
Manufacturing
-
Jun 1993 - Aug 2006
Worked across a number of roles including team leader of the cereal processing plant (9 extruders, dryers, coaters & coolers), Inbound raw materials receiving, testing and storage, R&D/NPD support, Maintenance, Quality assurance, Small volume specialty line leadership, Snacks & Pilot plant testing and commissioning of new product. Worked across a number of roles including team leader of the cereal processing plant (9 extruders, dryers, coaters & coolers), Inbound raw materials receiving, testing and storage, R&D/NPD support, Maintenance, Quality assurance, Small volume specialty line leadership, Snacks & Pilot plant testing and commissioning of new product.
-
-
Education
-
Western Institute of NSW
Certificate 4 - business management, HR, Industrial relations, report writing, recruitment, financial management, public speaking -
Xavier high school, Albury
Year 12
Community
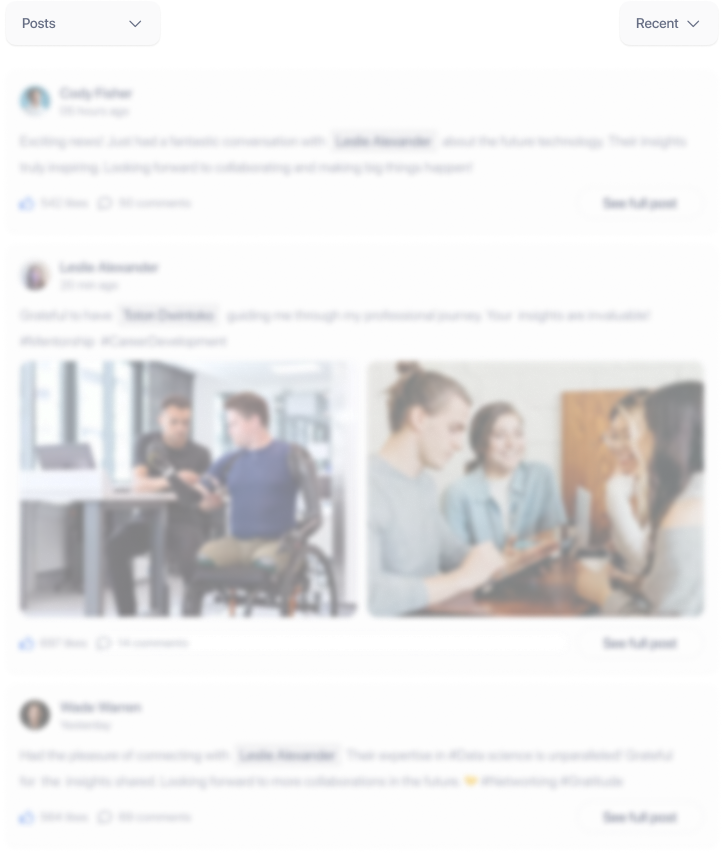