Seth Wilbanks
A/V Technician at YMCA of the Rockies- Claim this Profile
Click to upgrade to our gold package
for the full feature experience.
-
English -
Topline Score
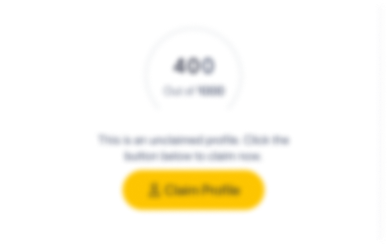
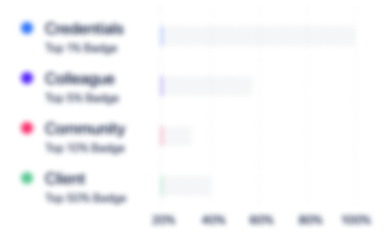
Bio


Experience
-
YMCA of the Rockies
-
Hospitality
-
100 - 200 Employee
-
A/V Technician
-
Feb 2016 - Present
Overseeing and supervising audio/visual equipment. Delivering, setting up and taking down A/V equipment. Assisting other departments if needs arise. Overseeing and supervising audio/visual equipment. Delivering, setting up and taking down A/V equipment. Assisting other departments if needs arise.
-
-
-
Koontz-Wagner
-
United States
-
Facilities Services
-
1 - 100 Employee
-
Electrician
-
Oct 2015 - Dec 2015
• Rotate through all the tasks required including; screwing panels together, installing insulation, using power tools such as drills, grinders and plasma cutting equipment, etc. • Operate heavy equipment such as forklifts and overhead cranes. • Determine project requirements, including scope, assembly sequences, and required methods and materials, according to blueprints, drawings, and written or verbal instructions. • Lay out, measure, and mark dimensions and reference lines on material, such as roofing panels, according to • drawings or templates, using calculators, squares, and measuring tapes. • Fasten seams and joints together with bolts, rivets, caulks, and metal drive clips to assemble components into product. • Drill holes in metal, for screws, bolts, and rivets. • Assemble and fit prefabricated parts to form sub-assemblies. • Sweep and organize work areas. • Knowledge of machines and tools, including their uses, repair, and maintenance. • Knowledge of materials, methods, and the tools involved in the construction or repair of sheet metal structures. • Interpret blue prints and drawings. • Utilize mathematical skills such as adding, subtracting, multiplying, dividing, fractions and using a tape measure. • Effectively interact and communicate with individuals at all organizational levels. • Conduct self in a respectful and appropriate manner. • Safely perform tasks and produce a quality product in an efficient and productive manner to meet schedule. • Reason and apply principles of logic to a wide range of factors when monitoring and working on jobs. • Being reliable, responsible and dependable. • Being careful about detail and thorough in completing work tasks. Show less
-
-
-
ABB
-
Switzerland
-
Automation Machinery Manufacturing
-
700 & Above Employee
-
Electrician
-
Feb 2015 - Oct 2015
• Assist in production of company products which typically encompass such methods as machining, fabricating, assembly, inspection, test and overhaul. • Supervise a group engaged in various activities involving skilled trades and related functions. • Resolve or participate in resolving technical and logistics problems and assist to develop and implement measures to improve operations and customer relations. • Provide instruction and direction for third party non ABB skilled crafts. • Plan, establish schedules and assign work, considering requirements and priorities. • Utilize most effective equipment, considering skills of staff, to cost-effectively achieve objectives while concurrently implementing efforts to continuously improve performance. • Monitor activities and initiate actions to eliminate problems. • Resolve semi-complex technical or human resource issues, and work with senior supervisors and human resource representatives to resolve more complex issues. • Maintain awareness of new developments and technologies. • Review equipment capabilities, methods and processes, and make recommendations regarding feasibility of utilizing alternative approaches, modifying or replacing equipment to reduce costs or improve quality. • Provide guidance and training and ensure fair and equitable treatment of staff. • Manage and document employee performance and develop associated recommendations. • Manage third party non-ABB staff and skilled crafts to deliver maximum productivity, meet customer requested delivery dates and cost estimates. Show less
-
-
-
DataVox
-
United States
-
IT Services and IT Consulting
-
100 - 200 Employee
-
Lead A/V Technician
-
Oct 2014 - Feb 2015
• Managed multiple teams on site to complete tasks safely and efficiently. • Maintained the ability to work in a construction environment and follow all of the general contractor’s rules and regulations. • Understood, designed, and installed audio/visual, display, and video conferencing equipment and tested functionality. • Adhered to all OSHA standards. • Coordinated with construction crew and electricians. • Troubleshot complex audio, video, switching and control system problems. • Kept upper management informed of progress and communicated clearly to client and project management staff. • Completed all cable/power terminations necessary for installed equipment to operate. ie: pulling wires through conduit, crawl spaces, ceilings, walls, etc. • Fabricated equipment racks. • Checked out and checked in any special tools needed for each specific job. • Maintained company vehicle. • Performed general maintenance, repair and upkeep on hardware and tools. • Maintained a working knowledge of commercial construction environments. • Maintained excellent communication and computer skills. • Performed heavy manual tasks for extended periods of time. • Knowledge of PPE equipment. • Studied plans, drawings, specifications and work orders to determine work requirements and sequence of repairs and/or installations. • Knowledge communicating with appropriate personal to optimize equipment performance. • Participated in manufacturing process improvement initiatives. • Maintained a strong attention to detail and technical and mechanical aptitudes. • Provided personal tools and most other tools needed for each job. • Performed all other duties assigned. Show less
-
-
-
-
-
Jun 2011 - Apr 2014
• Oversaw the production design/build process, drew up a production schedule. • Ensured that the correct equipment was pulled for each job and loaded efficiently into trucks so that it was able to arrive to its destination on time and safety. • Worked with management to ensure that the production would be cost effective. • Made sure that the production was on time and ran smoothly. • Worked out the human (direct employees as well as contract hires) and material resources needed for load-in, event, and load-out. • Drafted a timescale for each job. • Coordinated with designers and event planners to ensure the happiness of the client and the smooth execution of the event. • Estimated costs and set quality standards. • Monitored the work process and adjusted the schedule as needed. • Was responsible for the selection and maintenance of equipment and shop trucks. • Monitored product standards and implemented quality-control programs. • Liaised among different departments, e.g. management, sales. • Worked with management to implement the company's policies and goals. • Ensured that health and safety guidelines were followed. • Supervised and motivated a team of workers. • Reviewed worker performances. • Identified training needs. • Worked with management during hiring and employee termination processes. Show less
-
-
-
May 2010 - Jun 2011
• Managed production shop floor. • Ensured that all production equipment was stored in its designated place on the shop floor. • Worked with employees to maintain shop cleanliness and safety guidelines. • Thoroughly reviewed event pull lists to ensure that all of the materials needed for the event were packed for transport to the site. • Made sure all heavy equipment (scissor lift, forklift, etc.) were operating properly and safely at all times and before each use. • Kept up maintenance/repair on all trucks and equipment (speakers, microphones, sound boards, monitors, projectors, stage lighting, etc.), as well as all shop tools and equipment (rigging equipment (trussing), brackets for speakers/lighting equipment, power cables, all power tools needed for assembly, etc.). • Maintained an inventory of all items on the shop floor. • Completed all duties of crew member. Show less
-
-
-
May 2004 - May 2010
• Be available to work every event assigned.• Assist in loading trucks with gear.• Assist in the load-in process for an event (bringing in equipment to the venue and setting up according to the production managers instructions).• Assist in the load-out process for an event (tearing down and removing equipment from the venue according to the production manager’s instructions).• Build stages as well as truss structures.• Ensure that power is brought in correctly and safety to all the equipment that require it.• Set up all equipment and run multiple tests with client to ensure no surprises during the event.• Monitor equipment during the event and make sure equipment is not harmed during event and loading/unloading;• Coordinate with other vendors also working the event (caterers, designers, etc.).• Maintain a flexible work schedule to adhere to late night events or out of town events.• Complete permanent installations that require crawling in tight spaces to run wire/cable.• Follow all management instruction and work well as part of a team.• Complete all administrative employee duties. Show less
-
-
Education
-
Lutheran High North
High School Diploma
Community
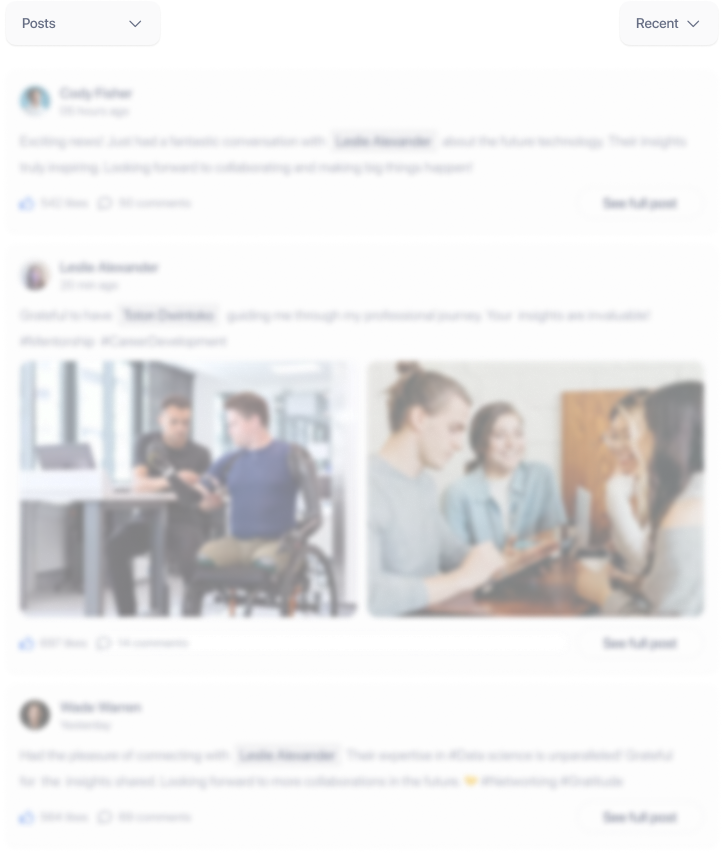