Sergey Lukin
Head of the Department at Inter RAO- Claim this Profile
Click to upgrade to our gold package
for the full feature experience.
-
Русский -
-
English -
Topline Score
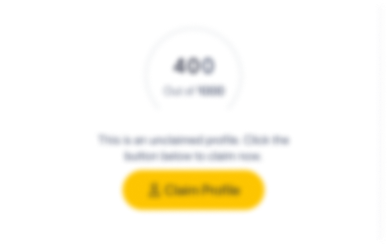
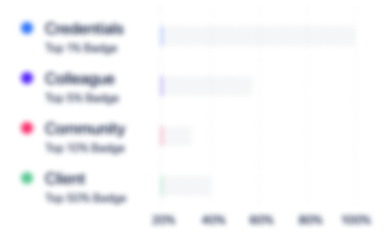
Bio


Experience
-
Inter RAO
-
Russian Federation
-
Utilities
-
200 - 300 Employee
-
Head of the Department
-
Jun 2014 - Present
1. To manage the process of Inter RAO "Energy Savings and Energy Efficiency Improvement" Programm. 2. To manage the Inter RAO "Creation of the system of company's production assets management, based on the assets life cicle cost minimization" Project. 3. To implement and manage Inter RAO continious improvement process/system "The Energy of a mind". 1. To manage the process of Inter RAO "Energy Savings and Energy Efficiency Improvement" Programm. 2. To manage the Inter RAO "Creation of the system of company's production assets management, based on the assets life cicle cost minimization" Project. 3. To implement and manage Inter RAO continious improvement process/system "The Energy of a mind".
-
-
-
Norilsk Nickel
-
Switzerland
-
Mining
-
700 & Above Employee
-
Company Financial Controller Deputy
-
Jul 2013 - Jun 2014
Analysis of the current production management system and the assessment of the Zapolyarny branch (Norilsk) operation results for the period of 2008-2013.: - Management reporting system analysis (adequacy and completeness for management decision making). - Production planning system analysis (including the analysis of the reasons for the production plan noncompliance). - Scheduled and unscheduled delays reporting system analysis (dynamics, root causes analysis). - Maintenance and repair planning system analysis (including the reasons for the noncompliance/rescheduling). - Analysis of the spare parts support system (including the critical spare parts and standardization). - Analysis of dynamic of the major consumables consumption rates. - CapEx program analysis (relevancy and validity). - Organizational chart and staff efficiency analysis (levels of subordination, qualification, work load, functions overlap, productivity, etc). - As the result of the analysis to provide recommendations with purpose to improve the operational effectiveness, equipment reliability, reduce manufacturing costs.
-
-
-
-
Head of the Project's office, Strategy
-
Aug 2011 - May 2013
1. To analyze and improve CapEx planning and implementation system: - Analyzing current procedures for CapEx planning and implementation. - Provide recommendations to improve procedures with purpose to guarantee CapEx projects implementation on time, on budget. 2. Project manager – “Pipe mill construction in Houston, TX, USA” Project: - Project Team creation. - Preparation of the Project schedule and control its implementation. - Participation in negotiations with engineering and construction companies, equipment suppliers. - Coordination of the construction site purchasing. - Participation in negotiations with the local authorities (permits required, possible tax incentives, grants, etc). - Preparation of the Project budget and financing plan. Control its implementation. - Control agreements and contracts execution.
-
-
-
Severstal NA
-
United States
-
Mining
-
300 - 400 Employee
-
Director, Continues Improvement
-
Oct 2009 - Sep 2010
1. To establish Continuous Improvement Department and process: - To develop departmental structure, objectives and responsibilities. 2. To establish goal setting: - to analyze company’s strategic business plan and to set top management goals and objectives. - to analyze capabilities of production and non-production divisions and processes (own statistic, benchmarking vs. “best in class”, zero based budgeting). - to determine major KPI’s, KPIV’s and KPOV’s. - to set goals and objectives for the divisions to support top management goals and objectives (X-Matrix). 3. To establish Continuous Improvement (CI) process: - To develop and implement the process of employees involvement in CI activity (divisional and cross-functional problem solving teams, employees meetings, etc). - To develop and implement CI communications and PR approaches (presentations, newsletters, articles, interviews, display boards, etc), - To develop and implement employees training of basic problem solving tools (statistical analysis, benchmarking, Pareto, SIPOC, ZBB, A3 worksheet, etc), - To develop and implement monitoring and rating approaches to the teams and divisions results (to establish internal competitiveness), - To develop and implement rewarding system for employees of different levels (division, team, employee). Approaches are based on results achieved. - To develop and implement CI customize IT support (CI ideas registration, control of implementation, results monitoring, knowledge sharing), Oracle based. - Kaizen implementation. - To organize Lean Six Sigma training and to implement Green and Black Belt projects.
-
-
Education
-
Northumbria University
Master of Business Administration (MBA), International Management -
Cherepovets State University
Mechanic Engineer, Lifting, transporting and road construction machines and equipment
Community
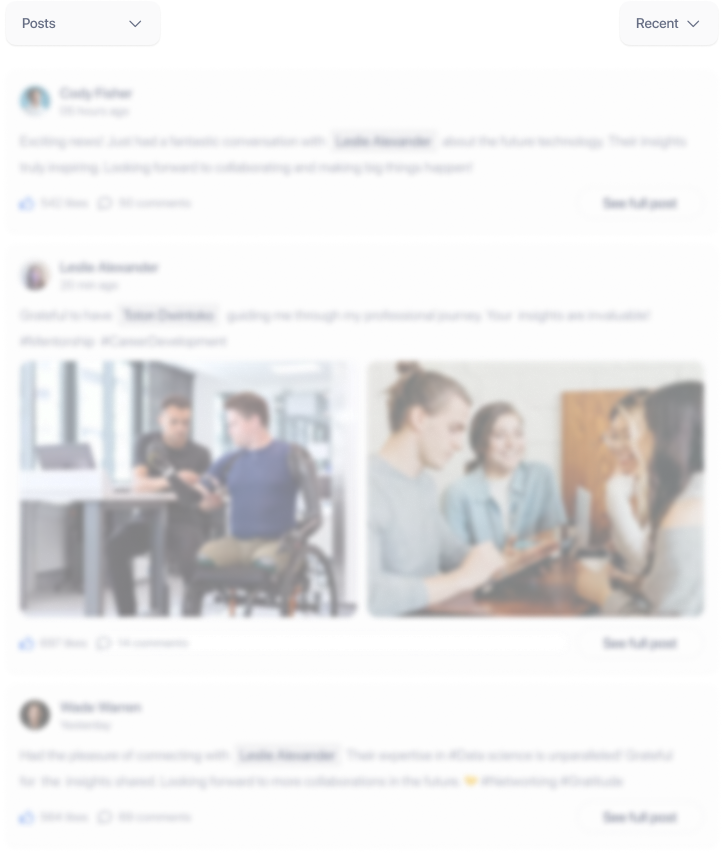