Sean Hoefer
Plant Engineering Manager at Ford Meter Box- Claim this Profile
Click to upgrade to our gold package
for the full feature experience.
Topline Score
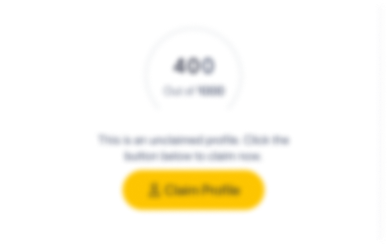
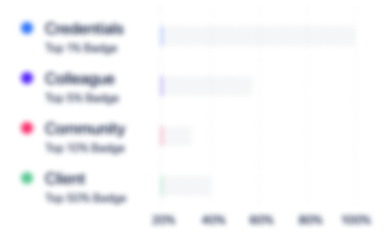
Bio


Experience
-
Ford Meter Box
-
United States
-
Construction
-
100 - 200 Employee
-
Plant Engineering Manager
-
Sep 2019 - Present
Manage Plant Engineering, Maintenance departments, Tool Manufacture in support of a three shift operation. Responsibilities include off site properties and 600,000 square feet multiple level manufacturing and office building and grounds. 18 direct reports and 112 indirect. Direct reports are mechanical, electrical, controls, environmental and facility engineers responsible for existing and new equipment design and manufacture. Ensure annual capital budget is within budget and on time.
-
-
Project Manager
-
Sep 2018 - Sep 2019
-
-
Process Engineer
-
Aug 2016 - Sep 2018
Plant engineering support for manufacture and assembly of Lead and No Lead Brass components for potable water use. Identify, prioritize and implement opportunities for process improvement. Purchase and validate equipment to ensure compliance for the Water Works Industry and improve process efficiency. Project lead with multi-discipline cross functional teams. Coaching continuous improvement teams consisting of Plant Engineers, Product Engineers, Quality and Production Teams.
-
-
-
Zimmer Biomet
-
United States
-
Medical Equipment Manufacturing
-
700 & Above Employee
-
Principal Manufacturing Engineer
-
Dec 2011 - Aug 2016
Engineering support for manufacture of Titanium (Ti-6Al-4V) Hips. Identify, prioritize, develop and implement opportunities for process improvement. Purchase new equipment. Work with safety, plant, facilities and maintenance engineering teams for modification of existing and new manufacturing cells. Validate equipment and processes to ensure compliance. Lead CAPA teams (Corrective Action Preventative Action). Create PFMEAs, work instructions, visual aids, bill of materials, manufacturing routings, in change management process. Project lead with multi-discipline (Regulatory, Post Market Surveillance, Quality, Purchasing, Development, Tool Engineer, CNC Programmers, Maintenance, Plant Engineering, Supervisors, Operators and Reliability Engineer) project activities. Coaching Six Sigma Green Belts and Manufacturing Engineers.• Reduced lot commingle non conformances by 99%. (2011) • Created electronic Kanban system saving $400K in inventory and reduced lead time from 24 days to 24 hrs. (2013)• Upgraded and validated aqueous cleaning processes to reduce down time and improve quality. (2013)• Manufacturing layout improvements resulting in piece per man hour increase of 25%. (2014) • New 5 axis cnc milling cell reducing down time and increasing pieces per man hour. (2015)
-
-
Senior Manufacturing Engineer II
-
Apr 2009 - Dec 2011
-
-
Senior Manufacturing Engineer I
-
2008 - Apr 2009
Manufacturing Engineer.
-
-
-
Dana Incorporated
-
United States
-
Motor Vehicle Manufacturing
-
700 & Above Employee
-
6 Sigma Black Belt
-
2004 - 2008
Lead Six Sigma and Lean Manufacturing teams to achieve business objectives. Train and mentor Green Belts. Work with operational leaders, identify projects, create business plans and coordinate project activities. Training of employees for project implementation, tool design recommendations, determine equipment purchase specifications, bid evaluation, project cost estimation, process design, supervised and directed company union employees and contract workers during project installations. Delivered Results: • $385K per year in savings in Expedited Freight. (2004) • $758K per year in savings on Perishable Tooling, Shipping Supplies, Scrap, Overall Equipment Effectiveness (OEE). (2005) • $1M per year in savings and increased business through quality improvements on Dana tubing manufacture. (2006) • $1.2M per year savings by implementing new aluminum aging process meeting AMS and AIAG standards. (2007)
-
-
-
Daimler Chrysler
-
United States
-
Motor Vehicle Manufacturing
-
700 & Above Employee
-
Project Engineer
-
2003 - 2004
Product testing using Engine Dyno, instrument vehicle for NVH (Noise Vibration Harshness), functional performance during road test and noise test stand. Support Transmission Plant with root cause analysis and containment of tear down audit non-conformances. Support Shainin Red X projects. Provided transmission and assembly plants with daily, weekly and monthly tear down audit performance. Delivered Results: • Created software allowing systemic quality issues to be identified resulting in $720K cost recovery on transmission returns. (2003) • Reduced transmission evaluation time by 25%. (2003)
-
-
-
Dana Incorporated
-
United States
-
Motor Vehicle Manufacturing
-
700 & Above Employee
-
Product Engineer
-
1999 - 2003
Advanced design and testing of axle tube assemblies, stamped, cast and forged sub components. Interface with Customer, Sales, Suppliers, Application Engineer, CAD Designer and FEA to develop product design. Create bill of material and manufacturing routing for samples and production build. Construct DVP&Rs, DFMEAs and DOEs to validate product design. Delivered Results: • Created Axle Application Analysis software reducing analysis time and improved collaboration between engineering teams. (2000)• 5 US patents for axle designs. US:6,322,061 (1999) US:6,460,268 (2001), US:6,729,207 (2002), US:7,121,972 (2002), US:7,137,183 (2002)• $8M per year savings in VAVE (Value Add Value Engineering) savings. (2002)• Invented MCS Modular Center Section. Design was shown on the Dana Corporation Annual report front cover for 2002. Design was also shown in the Auto Engineering International magazine February 2003 as an attached add circular.
-
-
Engineering Technician
-
1997 - 1999
Root cause analysis of axle proving ground durability failures.Benchmark competitor axles.Interface with Customers, Warranty, Application Engineers, Product Engineers and Material Engineers.Create technical reports detailing test results and benchmark analysis.
-
-
-
-
Student
-
May 1993 - Aug 1995
Aluminum foundry worker. Finishing, knock out shake out, blast line. Operate hand tools, grinders, riser saws, presses, and blast cabinet. Aluminum foundry worker. Finishing, knock out shake out, blast line. Operate hand tools, grinders, riser saws, presses, and blast cabinet.
-
-
Education
-
Purdue University Fort Wayne
BSME, Mechanical Engineering
Community
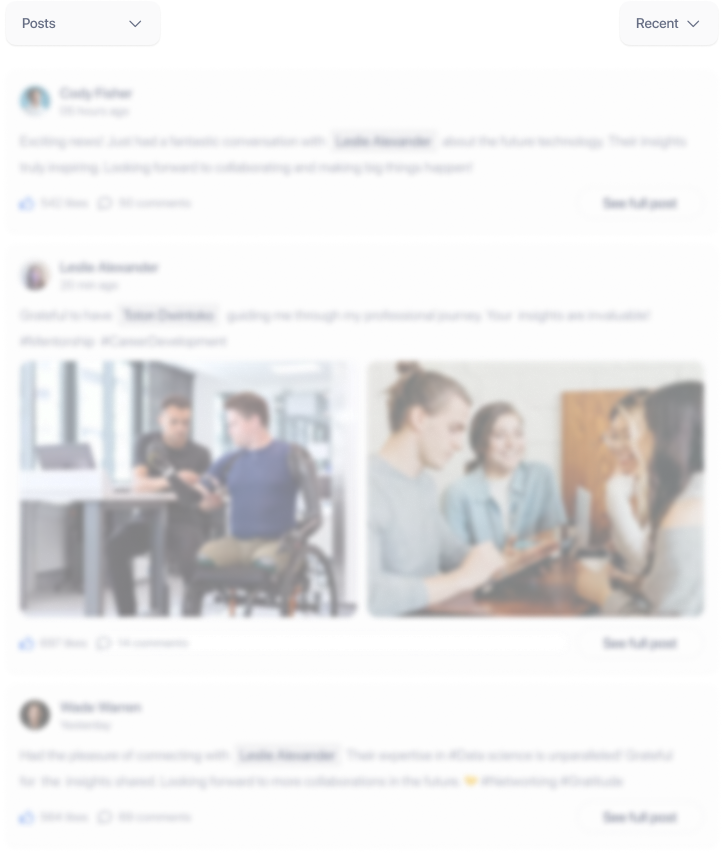