Sean Enderle
Environmental Health Safety Coordinator at TIMET- Claim this Profile
Click to upgrade to our gold package
for the full feature experience.
Topline Score
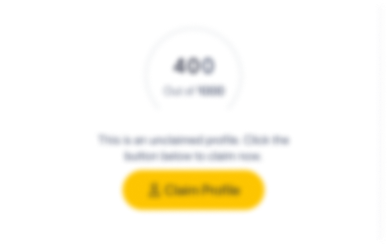
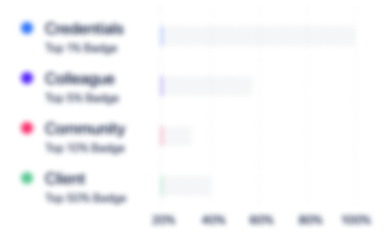
Bio


Experience
-
TIMET
-
United States
-
Mining
-
700 & Above Employee
-
Environmental Health Safety Coordinator
-
Jun 2022 - Present
TIMET has been leading the industry in mill and melted products, supplying nearly one-fifth of the world's titanium. TIMET has been leading the industry in mill and melted products, supplying nearly one-fifth of the world's titanium.
-
-
-
KBR Careers - Gov Solutions
-
United States
-
Defense and Space Manufacturing
-
700 & Above Employee
-
Sr. HSE Specialist
-
Sep 2020 - Jul 2022
-
-
-
DynCorp International
-
United States
-
Defense and Space Manufacturing
-
700 & Above Employee
-
Environmental Health Safety Specialist
-
Jan 2019 - Sep 2020
Provide oversight of all EHS programs and work with managers to ensure employees are complying with all applicable government, corporate and customer policies and procedures. Serve as the focal point for site environmental and safety compliance and as a resource to management to provide scientific or technical guidance for EHS programs. - Perform regular safety inspections and surveillances, and formal environmental and safety audits to ensure contract requirements are met or exceeded. - Evaluate violations or problems discovered during inspections to provide advice to management on implementing changes to be compliant with corporate and government EHS policies. Follows up to make sure they are effective and being followed by employees. - Review the site-specific EHS plans and procedures to establish validity and any need for amendment. - Investigate spills and accidents and prepares reports for submission to the customer. - Investigate personal incidents and vehicle accidents to determine root cause and any corrective actions to prevent a repeat occurrence. - Manage and administer compliance with all federal, corporate and customer environmental protection programs including required OSHA specific programs. - Recommend, implement, and assist in the execution of a variety of workplace safety, industrial hygiene, and safety training programs to prevent injury and occupational illness. - Coordinate safety committee meetings; produce and disseminate safety committee meeting minutes and tracks action items to completion. - Monitor the use and storage of hazardous materials in the workplace. - Responsible to administer the Environmental Protection Program and the Respiratory Protection Program. - Collates the site Hazardous Material Report and Safety Report for submission as required. - Perform other qualified duties as assigned. Show less
-
-
-
Raytheon
-
Fort Irwin, Ca
-
Maintenance Opoerations Manager, Team Lead II
-
Nov 2014 - Jan 2019
Mange and work with the Life Cycle Contractor Support for the Warfighter FOCUS (WFF) program under the Warrior Training Alliance (WTA) at the National Training Center (NTC). Provide maintenance operations support for NTC: to provide realistic joint and combined arms training focused on developing soldiers, leaders, and units of the United States military for success on the 21st Century Battle Field. - Manage, coordinate, and schedule the maintenance requirements with rotational units being supported and maintenance activities, to include coordinating the evacuation of equipment beyond immediate maintenance capabilities. - Manage, supervise, coordinate, schedule, and train organizational maintenance and shop operations for sub-contractors and assigned personnel. - Monitored daily reports on maintenance status of assigned vehicles and associated equipment, ensuring applicable licensing and training, to include Personal Protective Equipment (PPE) and vehicle equipment operations. - Manage and coordinate the preparation of readiness reports to ensure operational objects are achieved, to include providing input for unit status reports. - Responsible for project management to ensure the replacement vehicles, major assemblies, commercial/leased vehicles, and life-cycle management of the fleet at the site. - Project management of construction, demolition and relocation of various sites in support of video and radio communications. This includes power, HVAC, grounding, and inventory of all assets - Responsible for coordinating and scheduling of forward support elements, to include rapid recovery, evacuation, and repair of vehicles. - Manage, coordinate, and schedule all contract-identified facilities, to include structural safety, and heating, ventilation, air conditioning, and power systems. - Adhere to company and site directives, memoranda, policies and procedures. Support quality/ISO, security and safety training and programs. Show less
-
-
-
Marine Corps Recruiting
-
Armed Forces
-
700 & Above Employee
-
Maintenance Management Chief
-
Jan 2013 - May 2014
Principle advisor on all matters pertaining to material readiness; identified and rectified readiness issues with outside agencies; provide daily oversight concerning production and materials within the organization that encompassed more than $15 million in assets and parts.Managed the staffing and professional development of 200 employees.Managed a repair parts inventory valued at over $2.5 million.Assist the Field Service Representative (FSR) in his duties by providing quality control services and serving as liaison between the Marine Corps and program managers.Coordinated meetings with program managers to resolve safety issues pertaining to newly fielded equipment.Identified shortfalls and in policy.Improved processes and procedures to streamline production and parts acquisitions.Increases productivity by 25%.Design, develop and implement standard operating procedures for shop operations.Design, develop, implement and coordinate training for employees.Supervised inventory control of tool kits, sets, and chests.Supervised the safety/security program for employees and equipment. Show less
-
-
Analysis Team Lead/Ordnance Analyst
-
Jan 2011 - Feb 2013
Lead advisor on matters affecting logistical and material readiness of Marine Corps units from January 2011 – February 2013. Facilitated meetings with unit commanders to provide expectations and results of analysis that were conducted. Analyze and interpret individual and organizational logistical and material readiness capabilities. Provide training and education to unit personnel. Implemented new logistics technology, converting from Legacy systems to an Oracle system.Provided interpretation of policy and directives.Established new policy and procedure enhancing the knowledge base and operation of the newly fielded Oracle logistics system.Improved business practices throughout Marine Corps units throughout the region.Provided analysis for 30 Marine Corps units throughout the Western Pacific Region.Supervised the staffing and professional development of 12 employees.Coordinated travel and budgets plans for 12 employees for four business trips lasting 30 days. Show less
-
-
Faculty Advisor
-
Jun 2008 - Dec 2010
Provide professional military leadership and development for enlisted personnel in mid-level and upper level management positions within the Pacific Region of the Marine Corps. Provide training, mentorship and education for 1800 personnel throughout the Marine Corps. Monitor pass and failure rates of students attended the leadership course. Analyze and evaluate students work and provide feedback. Provided training, mentorship and education for 120 students annually.Design and develop curriculum for periods of instructionAnalyzed and evaluated student work.Provided feedback to all students concerning work, knowledge and proficiency.Developed training schedules. Show less
-
-
-
Machinist/Welding Shop Manager
-
1st Light Armored Recon Camp Pendleton
-
Machinist
-
Aug 2005 - May 2008
Principle advisor to the Maintenance Officer on matters pertaining to fabrications and repairs with the machine and welding shops. Provided daily oversight concerning production and materials within the organization. Managed the staffing and professional development of 120 employees. Established and managed a repair parts inventory valued at over $1.5 million. Managed consumable inventory for use during fabrications and repairs. Requisitioned new equipment to modernize technologies and capabilities. Coordinated meetings with program managers to resolve safety issues pertaining to newly fielded equipment. Designed, developed and implemented standard operating procedures for shop operations. Designed, developed, implemented and coordinate training for employees. Supervised inventory control of tool kits, sets, and chests. Supervised the safety/security program for employees and equipment. Show less
-
-
Education
-
Southern New Hampshire University
Business Management
Community
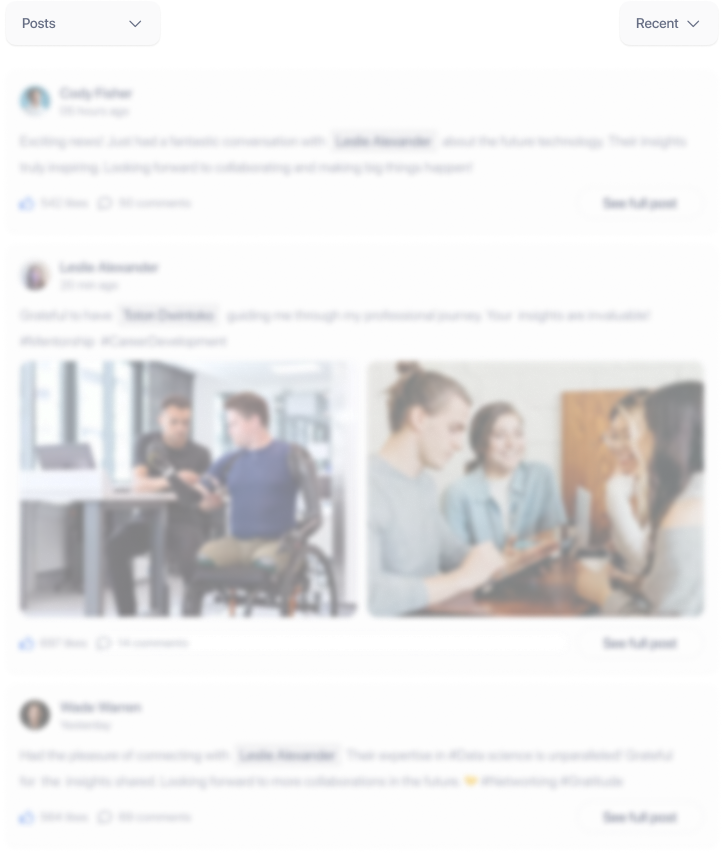