Scott Leo
Process Development Manager at Processall- Claim this Profile
Click to upgrade to our gold package
for the full feature experience.
Topline Score
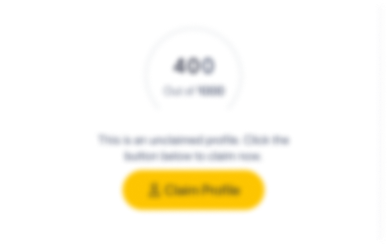
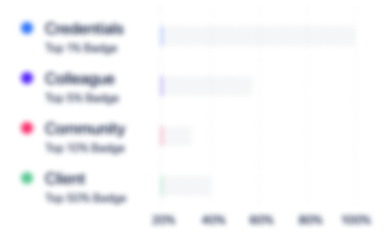
Bio
0
/5.0 / Based on 0 ratingsFilter reviews by:
Credentials
-
Green Belt
-
Experience
-
Processall
-
United States
-
Machinery Manufacturing
-
1 - 100 Employee
-
Process Development Manager
-
Feb 2021 - Present
-
-
-
DyStar
-
Singapore
-
Chemical Manufacturing
-
700 & Above Employee
-
Process Engineer
-
Jan 2019 - Oct 2020
• Developed plan to work-off 50,000 lbs of unused raw material on site and convert them into a viable product for commercial usage• Fixed the cost structures for the entire dispersions business to ensure accurate price points for our product line saving the company upwards of 50% on the cost of products• Developed cleaning plan that eliminated the usage of formaldehyde releasing chemicals enabling us to sell our highest volume product to Europe• Leading the outsourcing of one of our varnish business unit to an external firm resulting in a $240,000 cost saving annually• Used Route Cause Analysis to determine the why trans-oxide pigment was continuously failing for usage in one of the highest volume products• Training the new R&D Chemist and new lab technicians• Served as production supervisor whenever supervisors were absent Show less
-
-
Research And Development Engineer
-
Sep 2017 - Jan 2019
• Designed the layout for the new dispersion's laboratory • Acted as project manager for the building of the new dispersion's laboratory including handling all communications with outside contractors• Designed and launched new product for the site resulting is potentially $400,000 annually for the site• Updating all outdated batch sheets and to reflect true cost structures for all products on site• Using the principles of 5S to improve the work flow for multiple laboratories and storage spaces on site• Improved throughput time of high jet carbon black products dispersion by over 20% • Redesigned multiple products due to discontinuation of raw materials saving the company a potential lose of business of $80,000 dollars annually• Developed cleaning plan that eliminated the usage of formaldehyde releasing chemicals enabling us to sell our highest volume product to Europe• Organized meetings with outside sales and purchasing team to potentially identify lower cost materials on the market Show less
-
-
-
INX International Ink Co.
-
United States
-
Chemical Manufacturing
-
700 & Above Employee
-
Process Engineer
-
Aug 2015 - Mar 2016
• Identified and reported testing differences between the two locations • Located and identified multiple systemic issues that were in SAP resulting in different tests being conducted at each site • Performed Studies for Sales Personnel and Customers to determine the optimal ink system for their needs • Collected and began analyzing Mill data to determine optimal milling times for products • Performed study to determine bound strength of polyurethane film for differing substrates and ink systems • Aided and assisted laboratory personnel with Quality Control Tests Show less
-
-
-
Sun Chemical
-
United States
-
Chemical Manufacturing
-
700 & Above Employee
-
Process Chemist / Process Engineer
-
Feb 2007 - Jul 2015
• During Green Belt training, lead cross functional team to determine new processing method for high volume products • Worked on a cross functional team performing FMEA and Root Cause Analysis resulting in a corporate savings of over $700,000 • Managed the quality transition of moving a product line from a closing manufacturing facility to our plant without any disruptions to the customers • Using Lean Manufacturing Techniques enabled a department of 3 to produce higher quality and quantity of products than a department of 8 • Tightened Quality Specs for products using Statistical Process Control • Reduced nonconforming material in multiple failing departments from 35% to 0% • Update and Maintain sites Batch Operation Guidelines Database • Worked in conjunction with Technology and Technical services on new product development • Helped establish a Laboratory at ISO 9000 and conducted 5S audit. • Performed alternate raw materials evaluations to determine if the suppliers materials adheres to our product standards • Developed a Shelf life expiration test method to determine when UV materials are no longer acceptable • Worked off nonconforming materials in the plant and determined the amount usable that would not affect product quality • Wrote new ISO test procedures • Performed basic quality control functions for the UV lab and served as a primary back up to all other quality control on site Show less
-
-
-
-
Special Project Coordinator
-
Jul 2004 - Dec 2006
• Developed a system for workflow using the principles of lean manufacturing to reduce paperwork • Worked to implement asset management database • Trained engineers and foreman to use of Geographical Information System • Created new tracking databases for use by payroll and the stockroom • Aided in training of foremen and engineers in HazCom and confined space entry • Ran the Plant’s Quality Assurance Lab • Insured that the company’s products met the customers specifications • Examined laboratory results and corrected chemical compounding problems that arose in the plant • Wrote Certificate of Analysis for materials tested • Collected samples to test and insure the computers and instruments in the refinery were accurately calibrated Show less
-
-
Education
-
University of Toledo
Master of Business Administration (M.B.A.), Finance, General -
University of Toledo
Bachelor of Science (B.S.), Chemical Engineering
Community
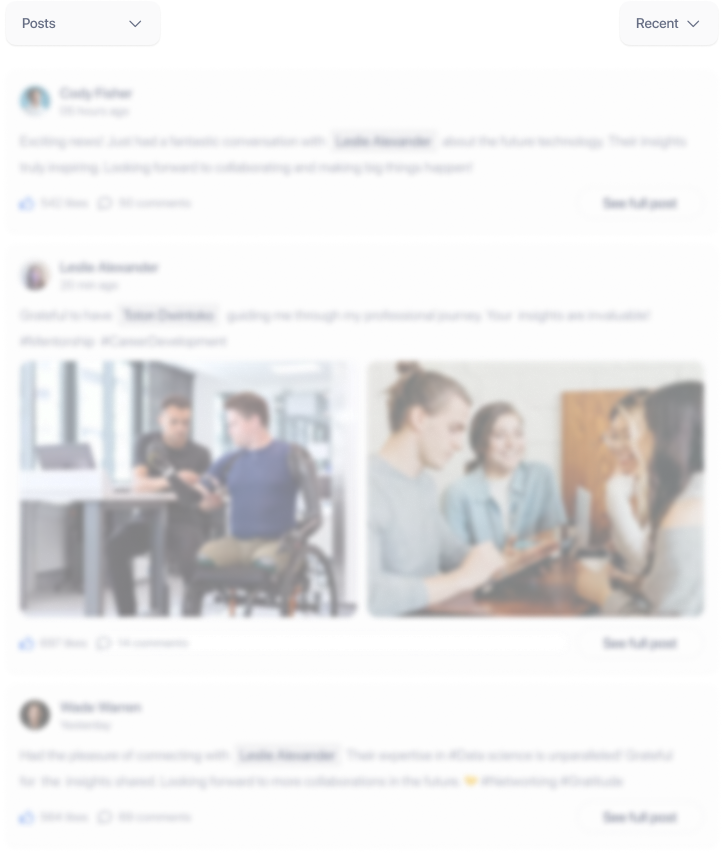