
Scott Crotty
Fixture / Metrology Engineer at Bullen Ultrasonics, Inc.- Claim this Profile
Click to upgrade to our gold package
for the full feature experience.
Topline Score
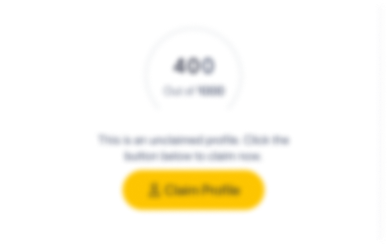
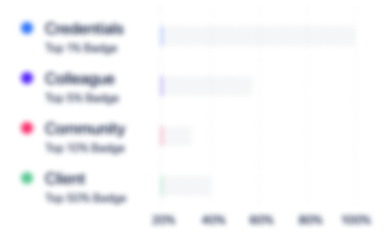
Bio


Experience
-
Bullen Ultrasonics
-
United States
-
Aviation and Aerospace Component Manufacturing
-
1 - 100 Employee
-
Fixture / Metrology Engineer
-
Oct 2017 - Present
-
-
-
Hohman Plating
-
United States
-
Aviation and Aerospace Component Manufacturing
-
1 - 100 Employee
-
Quality Engineer
-
Jan 2009 - Oct 2017
- Develop, Organize and Execute APQP activities for new Business (PPAP, PFMEA, Process Control Planning, FAI)= Establish and maintain the Periodic Testing system to demonstrate ongoing conformance of chemical processes to functional testing requirements set forth in industry and customer specifications. Ensures requirements to Nadcap standards- Establish and maintain the Calibration system to evaluate precision and accuracy of testing, measurement, and analytical equipment. Ensures requirements to calibration standards- Develop and maintain QMS documentation to ensure consistent compliance with Quality certifications- Develop and Implement Quality standards and methods for inspection, testing, and evaluation of products and processes- Identify Continuous improvement opportunities through trend analysis of quality performance data, Implements continuous improvement projects based upon trending- Review Industry and Customer Technical specifications/documentation for compliance. Performs gap analysis to identify areas of systems requiring improvement to maintain compliance and implements required systemic changes to achieve compliance- Evaluate and Troubleshoot suspect customer product for conformance to requirements, coordinates with internal and external customers to drive resolution and delivery of parts- Internal ISO9000/AS9100 and Nadcap Auditor.
-
-
-
Innatech
-
United States
-
Plastics Manufacturing
-
1 - 100 Employee
-
Quality Engineer
-
Oct 2004 - Jan 2009
- Develop and coordinate all new cell layouts- Lead continuous improvement activities to reduce internal and external scrap- Establish and monitor GMP (Good Manufacturing Practices) to ensure strict compliance to sanitary and safety standards. - Lead continuous improvement activities to improve product throughput- Lead and coordinate implementation of SMED (Single Minute Exchange of Die) methodology- Manage customer concerns through problem solving activities- Manage APQP activities and PPAP submissions- ISO9000/TS16949 Internal auditor
-
-
-
Stant
-
United States
-
Motor Vehicle Manufacturing
-
300 - 400 Employee
-
Quality Manager
-
Jul 2004 - Oct 2004
- Manage customer concerns through facilitating problem solving activities- Coordinate incoming and outgoing quality audits ISO9000/TS16949 coordinator- Coordinator and evaluate supplier PPAP submission- Quote cost to meet customer specifications- Comply and submit of customer PPAP- Manage various supplier base activities
-
-
Quality Engineer
-
Sep 2000 - Jul 2004
- Lead Lean/Six Sigma effort to improve process set-up, throughput, elimination of process with est. $150,000 in savings- Advanced product development for international and domestic customers - Supplier advanced product quality planning development - Active role in new program cell layout and design- Active role in product development - Review subcontractors PPAP supplier development- Advanced product quality planning coordinator on new product launches- Customer PPAP submissions- Six Sigma Project leader- Lead problem solving teams- Internal ISO9000/TS16949 Auditor
-
-
-
Findlay Industries
-
Motor Vehicle Manufacturing
-
1 - 100 Employee
-
Quality Engineer
-
Jul 1991 - Sep 2000
- Liaison between General Motors and Findlay Industries - Maintain and control all statistical process control data- Develop and maintain all Advance Product Quality Planning control plans, process flows, and PFMEA- Directed problem solving and corrective action- Maintained all customer measurable- Submitted production part approval process presentation team- Directed problem solving and corrective action- Maintain, tracked, and performed gage calibration- Review subcontractors’ PPAP submission
-
-
Education
-
Sinclair Community College
Associate’s Degree, Industrial Quality Engineering
Community
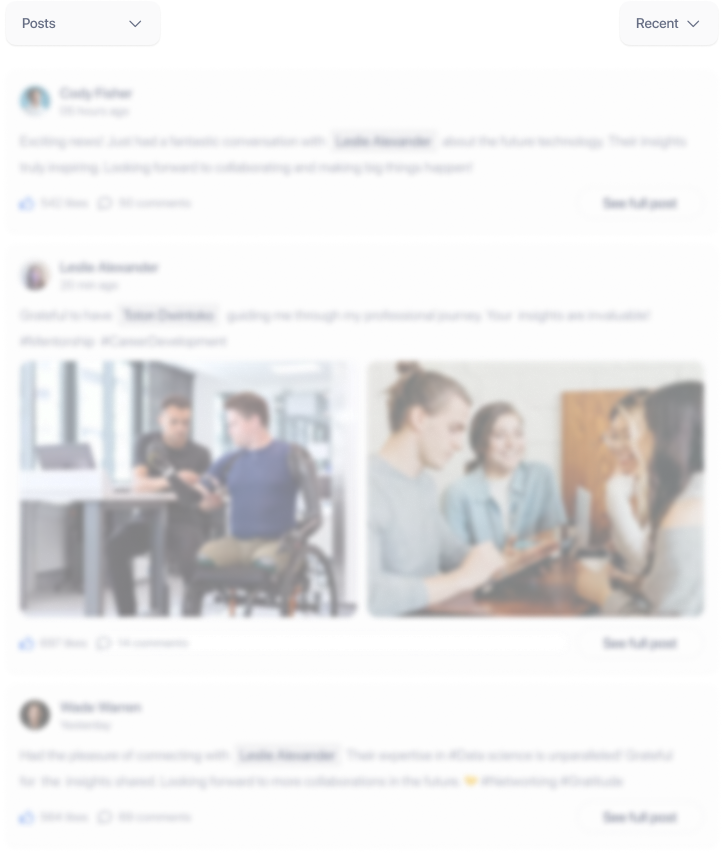