Scott Allen
Quality Assurance at TruVision Health- Claim this Profile
Click to upgrade to our gold package
for the full feature experience.
Topline Score
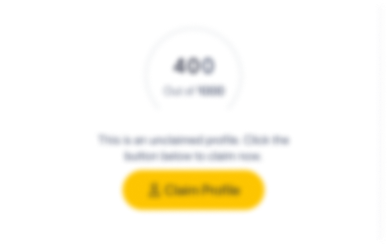
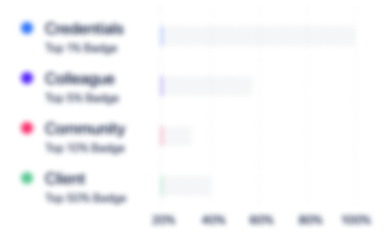
Bio

Brian Andersen
Scott is one of the most capable people I know. He can do any task he is put to with efficiency. He enjoys people and loves getting the job done right the first time on time. He would be an asset to any organization.

Brian J. Smith
Having worked with Scott in many capacities and over many years, I can easily say that he is one of the most brilliant minds I've engaged with. From project and product management, leadership, QA, systems integration and more, Scott provides a level of comfort, when he's on your team, that you just know things are going to be the best they can be. Professional, current, growth mindset describe Scott. He's the first pick when choosing teams!

Brian Andersen
Scott is one of the most capable people I know. He can do any task he is put to with efficiency. He enjoys people and loves getting the job done right the first time on time. He would be an asset to any organization.

Brian J. Smith
Having worked with Scott in many capacities and over many years, I can easily say that he is one of the most brilliant minds I've engaged with. From project and product management, leadership, QA, systems integration and more, Scott provides a level of comfort, when he's on your team, that you just know things are going to be the best they can be. Professional, current, growth mindset describe Scott. He's the first pick when choosing teams!

Brian Andersen
Scott is one of the most capable people I know. He can do any task he is put to with efficiency. He enjoys people and loves getting the job done right the first time on time. He would be an asset to any organization.

Brian J. Smith
Having worked with Scott in many capacities and over many years, I can easily say that he is one of the most brilliant minds I've engaged with. From project and product management, leadership, QA, systems integration and more, Scott provides a level of comfort, when he's on your team, that you just know things are going to be the best they can be. Professional, current, growth mindset describe Scott. He's the first pick when choosing teams!

Brian Andersen
Scott is one of the most capable people I know. He can do any task he is put to with efficiency. He enjoys people and loves getting the job done right the first time on time. He would be an asset to any organization.

Brian J. Smith
Having worked with Scott in many capacities and over many years, I can easily say that he is one of the most brilliant minds I've engaged with. From project and product management, leadership, QA, systems integration and more, Scott provides a level of comfort, when he's on your team, that you just know things are going to be the best they can be. Professional, current, growth mindset describe Scott. He's the first pick when choosing teams!

Credentials
-
Lean Six Sigma White Belt Certification
Management and Strategy InstituteMar, 2019- Oct, 2024
Experience
-
TruVision Health
-
United States
-
Wellness and Fitness Services
-
1 - 100 Employee
-
Quality Assurance
-
Aug 2021 - Present
-
-
-
iTOVi
-
United States
-
Wellness and Fitness Services
-
1 - 100 Employee
-
Regulatory and Quality Assurance Manager
-
May 2019 - Jul 2021
-
-
-
Nu Skin Enterprises
-
United States
-
Executive Offices
-
1 - 100 Employee
-
Director, Packaging Development
-
May 2018 - Mar 2019
• Collaborate with Marketing, R&D, and Regulatory Affairs to design and produce new products.• Propose and oversee cost savings projects reducing COGS.• Locate and qualify contract manufacturers.• Support design transfer to manufacturing.• Design and implement efficient supply chain for high and low volume products.
-
-
Director, Quality Management Systems
-
Mar 2012 - May 2018
• Design, configure and validate eQMS System to meet specific organizational needs.• Manage team to gather requirements and configure system.• Develop and execute manual and automated test scripts for system validation.• Develop and publish documentation for user training and conducted training.• Manage Document Control, Complaints Handing and Product inspections teams.• Lead FDA site inspections, and other third-party audits of the quality system.• Improve quality processes for Non-Conformance Reports, inspection, returns, document management and others.• Advise colleagues in regional offices on design of local quality systems.
-
-
Manager, Global Quality Management Systems
-
Aug 2009 - Mar 2012
• Direct supervisor of Document Control functions including SOPs, specifications, training records, and related systems.• Collaborate with process owners to ensure the documentation matches current practice.• Continuous improvement of the Nu Skin quality systems.• Manage internal audit process.• Developed and deployed database to manage SOPs.• Maintained training database.• Scripted daily reports in MS Excel from SAP, MS Access and oracle databases.
-
-
Quality Engineer
-
Aug 2006 - Aug 2009
• Develop, improve and implement inspection methodologies for new and existing products.• Audit suppliers to ensure conformance to cGMP and Nu Skin standards.• Collaborate with cross functional teams to evaluate root cause and implement solutions to resolve issues.
-
-
Packaging/Production Engineer
-
Aug 2005 - Aug 2006
• Collaborate with a cross functional development team to create new products and maintain vitality in existing products.• Manage specifications and costs for a range of products.• Develop, source and test packaging for new product initiatives.
-
-
-
Alberto Culver
-
Personal Care Product Manufacturing
-
100 - 200 Employee
-
Project Engineer
-
Jul 2002 - Aug 2005
• Source, purchase and install equipment to increase plant capacity, capability and efficiency.• Coordinate production of new products, working with suppliers, customer and internal functions to ensure project success.• Monitor and work with Operations to improve production line efficiencies. • Source, purchase and install equipment to increase plant capacity, capability and efficiency.• Coordinate production of new products, working with suppliers, customer and internal functions to ensure project success.• Monitor and work with Operations to improve production line efficiencies.
-
-
-
-
Machinist
-
Jan 1997 - May 2002
• Operate engine lathe, milling machine and other machine tools to repair or fabricate new parts used in chemistry labs.• Design and build, and make to print work. • Operate engine lathe, milling machine and other machine tools to repair or fabricate new parts used in chemistry labs.• Design and build, and make to print work.
-
-
-
-
Foundry Man
-
Sep 1991 - Jun 1994
• Mold making, rubber two piece molds in plaster shell, ceramic investment molds on wax• Bronze casting, divestment and finishing including welding, grinding polishing• Design and build facility support equipment • Mold making, rubber two piece molds in plaster shell, ceramic investment molds on wax• Bronze casting, divestment and finishing including welding, grinding polishing• Design and build facility support equipment
-
-
Education
-
Brigham Young University
Bachelor of Science - BS, Manufacturing Engineering Technology
Community
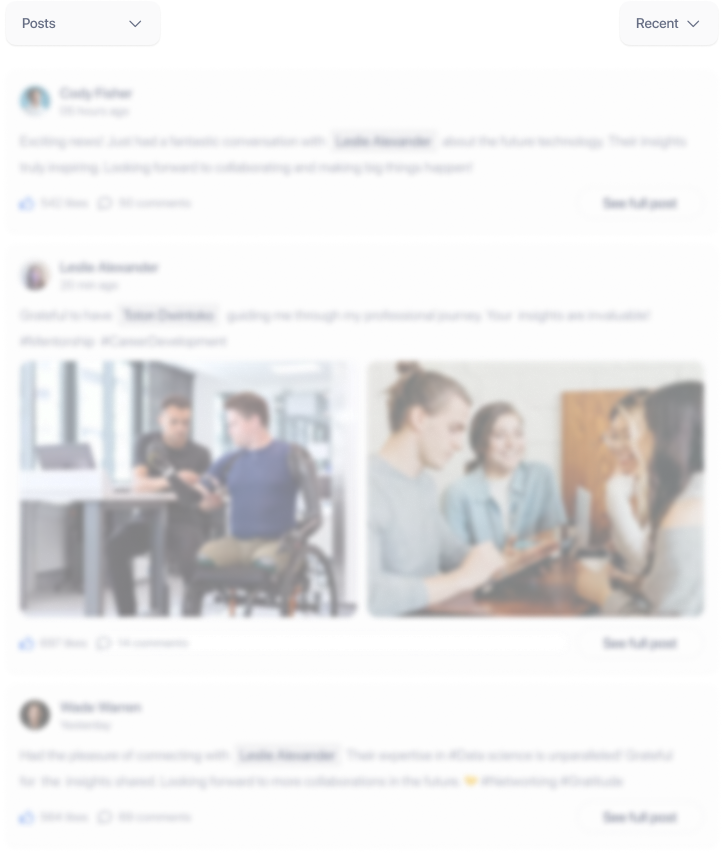