Scott Paliani
Site Leader at Fathom Digital Manufacturing- Claim this Profile
Click to upgrade to our gold package
for the full feature experience.
Topline Score
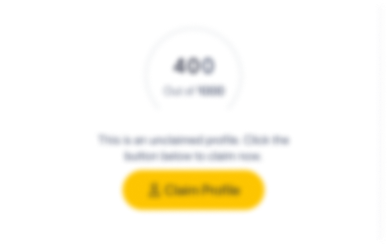
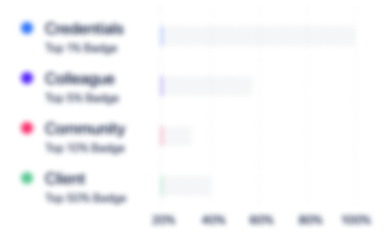
Bio

Stephen Evans
Scott has consistently proven himself to be a fantastic mentor and an exceptional leader. He continuously showed a high level of commitment to investing in the professional development of myself and others on his team. His efforts to continuously improve all of the areas of his responsibility was a driving force for positive change within the organization.

Mohamed Eldery, PhD, MBA
Scott is a gifted quality leader with a rare combination of patience, spunk, and research skills. His strong leadership and ability to manage complicated challenges are not disputable. Scott was always there to support, coach, and direct the team in critical operation and quality aspects. Scott knows his way well around people, he is good with the customers, suppliers and internal clients he does whatever it takes to help colleagues and gets things done. I really enjoyed working with Scott.

Stephen Evans
Scott has consistently proven himself to be a fantastic mentor and an exceptional leader. He continuously showed a high level of commitment to investing in the professional development of myself and others on his team. His efforts to continuously improve all of the areas of his responsibility was a driving force for positive change within the organization.

Mohamed Eldery, PhD, MBA
Scott is a gifted quality leader with a rare combination of patience, spunk, and research skills. His strong leadership and ability to manage complicated challenges are not disputable. Scott was always there to support, coach, and direct the team in critical operation and quality aspects. Scott knows his way well around people, he is good with the customers, suppliers and internal clients he does whatever it takes to help colleagues and gets things done. I really enjoyed working with Scott.

Stephen Evans
Scott has consistently proven himself to be a fantastic mentor and an exceptional leader. He continuously showed a high level of commitment to investing in the professional development of myself and others on his team. His efforts to continuously improve all of the areas of his responsibility was a driving force for positive change within the organization.

Mohamed Eldery, PhD, MBA
Scott is a gifted quality leader with a rare combination of patience, spunk, and research skills. His strong leadership and ability to manage complicated challenges are not disputable. Scott was always there to support, coach, and direct the team in critical operation and quality aspects. Scott knows his way well around people, he is good with the customers, suppliers and internal clients he does whatever it takes to help colleagues and gets things done. I really enjoyed working with Scott.

Stephen Evans
Scott has consistently proven himself to be a fantastic mentor and an exceptional leader. He continuously showed a high level of commitment to investing in the professional development of myself and others on his team. His efforts to continuously improve all of the areas of his responsibility was a driving force for positive change within the organization.

Mohamed Eldery, PhD, MBA
Scott is a gifted quality leader with a rare combination of patience, spunk, and research skills. His strong leadership and ability to manage complicated challenges are not disputable. Scott was always there to support, coach, and direct the team in critical operation and quality aspects. Scott knows his way well around people, he is good with the customers, suppliers and internal clients he does whatever it takes to help colleagues and gets things done. I really enjoyed working with Scott.

Credentials
-
Six Sigma Green Belt (CSSGB)
Honeywell -
Six Sigma Lean Expert Certifiction
Honeywell
Experience
-
Fathom Digital Manufacturing
-
United States
-
Industrial Machinery Manufacturing
-
100 - 200 Employee
-
Site Leader
-
Jan 2023 - Present
-
-
-
Eberle Design, Inc.
-
United States
-
Appliances, Electrical, and Electronics Manufacturing
-
1 - 100 Employee
-
Vice President Operations
-
May 2021 - Nov 2022
Planned, directed, coordinated, and oversaw operations activities in the organization including quality, manufacturing, manufacturing engineering, planning, procurement, logistics, facilities/maintenance, and repair/recertification. 150+ employees, $40M+in revenue, manufacturer of traffic safety products. • Established, implemented, and communicated the strategic direction for the operations function. • Collaborated with EDI executive leadership to develop and meet company… Show more Planned, directed, coordinated, and oversaw operations activities in the organization including quality, manufacturing, manufacturing engineering, planning, procurement, logistics, facilities/maintenance, and repair/recertification. 150+ employees, $40M+in revenue, manufacturer of traffic safety products. • Established, implemented, and communicated the strategic direction for the operations function. • Collaborated with EDI executive leadership to develop and meet company goals/objectives while providing guidance on operations projects and systems. • Established, communicated, and implemented operations policies, procedures, and standards to ensure effective and consistent support and execution. • Developed, implemented, and measured Key Performance Indicators for safety, quality, delivery, inventory, and productivity. • Developed and implemented a lean manufacturing cell transformation process (5S, visual management, waste elimination, one piece flow, and standard work). • Implemented a Sales, Inventory, Operations, and Planning (SIOP) process to drive customer forecast/demand into ERP while ensuring factory capacity and supplier orders are aligned. • Coached and mentored my direct reports, front line supervisors, and team leads through one on ones and daily factory Gemba walks. Show less Planned, directed, coordinated, and oversaw operations activities in the organization including quality, manufacturing, manufacturing engineering, planning, procurement, logistics, facilities/maintenance, and repair/recertification. 150+ employees, $40M+in revenue, manufacturer of traffic safety products. • Established, implemented, and communicated the strategic direction for the operations function. • Collaborated with EDI executive leadership to develop and meet company… Show more Planned, directed, coordinated, and oversaw operations activities in the organization including quality, manufacturing, manufacturing engineering, planning, procurement, logistics, facilities/maintenance, and repair/recertification. 150+ employees, $40M+in revenue, manufacturer of traffic safety products. • Established, implemented, and communicated the strategic direction for the operations function. • Collaborated with EDI executive leadership to develop and meet company goals/objectives while providing guidance on operations projects and systems. • Established, communicated, and implemented operations policies, procedures, and standards to ensure effective and consistent support and execution. • Developed, implemented, and measured Key Performance Indicators for safety, quality, delivery, inventory, and productivity. • Developed and implemented a lean manufacturing cell transformation process (5S, visual management, waste elimination, one piece flow, and standard work). • Implemented a Sales, Inventory, Operations, and Planning (SIOP) process to drive customer forecast/demand into ERP while ensuring factory capacity and supplier orders are aligned. • Coached and mentored my direct reports, front line supervisors, and team leads through one on ones and daily factory Gemba walks. Show less
-
-
-
Honeywell
-
United States
-
Appliances, Electrical, and Electronics Manufacturing
-
700 & Above Employee
-
Director Of Quality Contract Manufacturing Operations
-
Nov 2017 - Jul 2020
Oversaw and directed the global quality assurance functions, activities, and teams for CMOC to ensure that all quality and regulatory requirements were met. Multi-site leader (6 OEM and R&O sites) that drove continuous improvement for all aspects of CMOC quality performance. • Managed the overall relationship and drove quality improvements with the contract manufacturer’s quality, operations, and business teams. • Developed and implemented quality improvement projects to improve quality… Show more Oversaw and directed the global quality assurance functions, activities, and teams for CMOC to ensure that all quality and regulatory requirements were met. Multi-site leader (6 OEM and R&O sites) that drove continuous improvement for all aspects of CMOC quality performance. • Managed the overall relationship and drove quality improvements with the contract manufacturer’s quality, operations, and business teams. • Developed and implemented quality improvement projects to improve quality metrics and customer satisfaction. • Monitored progress of CMOC Quality metrics and communicated to CMOC organization and HON Aerospace senior leadership. • Ensured the Quality Management System, regulatory requirements, and site processes and procedures were implemented and sustained while training team members as required. • Communicated with external customers, regulatory agencies (FAA, EASA, DCMA), and internal customers on quality issues, quality improvement plans, and audits. • Provided Quality support/oversight for CMOC suppliers on supplier quality issues and supplier transitions. • Developed and mentored Site Quality Leaders, site QEs, and inspectors through one on ones and skip levels. • Reduced CMOC PPM 30% from Q1’18 to Q2’20. • Established a Management Operating System between HON and Celestica (contract manufacturer) to drive improved collaboration, communication, and escalation path. MOS included daily escalation path, weekly Quality Management Board, and monthly Management Operating Review. • Established CMOC QE do different plan that focused on proactive activities including escape triage/containment, root cause investigation rigor, verification of builds and RFMEAs on high risk parts, additional testing on high risk parts, Gage R&R, enhanced shop floor/layered audits, and improved supplier interaction/communication.
-
-
Site Leader Phoenix Service Center
-
Apr 2014 - Oct 2017
Led the operational planning of the site with accountability for its successful operation. Managed, directed and coordinated day-to-day operations to provide a safe and efficient facility performing R&O of avionics components. Security clearance. 50+ employees, $35M in revenue. • Drove performance targets including health, safety, quality, delivery, inventory/cost, productivity, and employee satisfaction. • Matured and improved all elements of the Honeywell Operating System and leveraged… Show more Led the operational planning of the site with accountability for its successful operation. Managed, directed and coordinated day-to-day operations to provide a safe and efficient facility performing R&O of avionics components. Security clearance. 50+ employees, $35M in revenue. • Drove performance targets including health, safety, quality, delivery, inventory/cost, productivity, and employee satisfaction. • Matured and improved all elements of the Honeywell Operating System and leveraged to drive daily execution, problem solving, and a culture of continuous improvement. • Led site strategic planning, capital planning, and materials management; responsible for the site budget. • Developed strong partnerships with external customers and internal businesses/support functions. • Developed and mentored front-line supervisors and partnered with cross functional teams (HR, finance, HSE, operations, materials, quality, and engineering) to achieve business objectives through talent management/staff development. • Led PSC site to achieve HOS Silver Certification in 2015. • Reduced PSC customer escapes from 11 in 2014 to 1 in 2016, 0 YTD in 2017. • Decreased PSC customer past due by 91% from 2014 to 2017, PASC by 80% from 2016 to 2017. • Reduced PSC backlog by 43% from 2014 to 2017, PASC by 41% from 2016 to 2017. • Increased PSC customer delivery from 63% to 95% from 2014 to 2016, PASC from 44% to 93% from 2016 to 2017. • Improved PSC site Positive Employee Relations score 10% (68% to 78%) from 2014 to 2016. • Raised PSC site productivity from -19% in 2014 to +15% in 2016.
-
-
Operations Manager/Value Stream Leader
-
Dec 2009 - Apr 2014
Led day-to-day operations for the Pneumatic Controls value stream with 150+ employees, $250M in revenue. Analyzed and improved processes to drive improvements in safety, quality, delivery, productivity and efficiency. • Drove performance targets including safety, quality, delivery, inventory/cost, productivity, and employee satisfaction. • Assembled and aligned resources required to meet performance targets in production output, material control, and new product introduction. • Coached… Show more Led day-to-day operations for the Pneumatic Controls value stream with 150+ employees, $250M in revenue. Analyzed and improved processes to drive improvements in safety, quality, delivery, productivity and efficiency. • Drove performance targets including safety, quality, delivery, inventory/cost, productivity, and employee satisfaction. • Assembled and aligned resources required to meet performance targets in production output, material control, and new product introduction. • Coached and mentored peers, direct reports, functional reports, and shop floor team leads. • Developed/implemented Honeywell Operating System manufacturing systems and processes to continually improve. • Developed lean manufacturing cell transformation model (5S, waste elimination, Point of Use storage, one piece flow, set up reduction, and work simplification); all cells in my value stream were transformed based upon this model. • Led and supported site HOS deployment from phase 1 through Bronze Certification. • Reduced customer past due in my value stream from ~$5M to ~$1M. • Increased customer OTTR in my value stream from ~60% to ~90%.
-
-
Site Quality Manager
-
Jul 2007 - Dec 2009
Led the site quality engineering (customer quality, supplier quality, and product quality) and manufacturing engineering functions and ensured compliance with customer requirements, regulatory agencies, government regulations and engineering specifications. • Led team in meeting performance targets including safety, customer PPM, customer disruptions, internal scrap/rework and defects, supplier PPM, and employee satisfaction. • Ensured compliance of Quality Management System policies and… Show more Led the site quality engineering (customer quality, supplier quality, and product quality) and manufacturing engineering functions and ensured compliance with customer requirements, regulatory agencies, government regulations and engineering specifications. • Led team in meeting performance targets including safety, customer PPM, customer disruptions, internal scrap/rework and defects, supplier PPM, and employee satisfaction. • Ensured compliance of Quality Management System policies and procedures including the coordination and deployment of standardized Aero Quality Management System (QMS) and Audit management; met ISO and AS9100 standards. • Led the development of quality improvement projects to decrease customer escapes and communicated with customers on product and process issues; quality focal for customer relationship management and customer complaints. • Generated, monitored, and reported site-specific quality metrics to product center and site leadership. • Oversaw site ISC engineering support budget including reviewing and approving internal funding. • Coached and mentored peers, direct reports, and functional reports. • Managed capital budget, including coordinating projects, appropriation requests, and spend for approved projects. • Integrated site manufacturing engineering into the site quality organization. • Decreased Tempe site PPM from 1419 in Q3’07 to 787 in Q4’08.
-
-
Manufacturing Engineering Manager
-
Jul 2005 - Jul 2007
Led the manufacturing engineering organization to drive quality, cost and cycle time improvements within the factory and supply base utilizing lean and Six Sigma tools. • Led team in meeting performance targets including warm start cycle time, rolled throughput yield, overall equipment effectiveness, cost, and employee satisfaction. • Managed capital budget, including coordinating projects, appropriation requests, and spend for approved projects. • Directed site ISC engineering support… Show more Led the manufacturing engineering organization to drive quality, cost and cycle time improvements within the factory and supply base utilizing lean and Six Sigma tools. • Led team in meeting performance targets including warm start cycle time, rolled throughput yield, overall equipment effectiveness, cost, and employee satisfaction. • Managed capital budget, including coordinating projects, appropriation requests, and spend for approved projects. • Directed site ISC engineering support budget including reviewing and approving internal funding for production support activities, value engineering, and supplier support. • Supported site Honeywell Operating System implementation and sustainment, driving standard work and manufacturing process control. • Served as the interface with engineering on product design and new product introductions focusing on process capability and design to cost. • Coached and mentored leadership rotation employees and direct reports. • Implemented an operating system to track and control both Capital and ISC engineering support budget/spend. • Worked onsite at supplier Eaton Phelps performing quality/delivery recovery activities.
-
-
Logistics Manager
-
Jun 2003 - Jun 2005
Led the site Logistics organization including receiving, receiving inspection, storeroom, government stores, and shipping. Responsible for ensuring compliance with inventory management, traffic, and Import/Export regulations. -Created and implemented a Logistics labor grade progression plan for hourly employees. -Created a dock closing process to meet independent auditor requirements for month/quarter end. -Drove creation and implementation of dock to floor process that reduced stores… Show more Led the site Logistics organization including receiving, receiving inspection, storeroom, government stores, and shipping. Responsible for ensuring compliance with inventory management, traffic, and Import/Export regulations. -Created and implemented a Logistics labor grade progression plan for hourly employees. -Created a dock closing process to meet independent auditor requirements for month/quarter end. -Drove creation and implementation of dock to floor process that reduced stores hardware by 46% on common parts and reduced Logistics cycle time by one day.
-
-
ISC Supervisor Assembly/Test
-
Nov 1999 - May 2003
Responsible for leading, developing, and mentoring high performance cell teams that complete assembly, test, final product preparation, and inspection of aerospace components. Responsible for the ongoing development and cross-training of employees. Functional responsibilities include Hourly Operators (Mechanics, Test Technicians, and Inspectors), Manufacturing Engineering, Product Quality, and Production Control. -Reduced cell cycle time by an average of 46%. -Increased on-time delivery… Show more Responsible for leading, developing, and mentoring high performance cell teams that complete assembly, test, final product preparation, and inspection of aerospace components. Responsible for the ongoing development and cross-training of employees. Functional responsibilities include Hourly Operators (Mechanics, Test Technicians, and Inspectors), Manufacturing Engineering, Product Quality, and Production Control. -Reduced cell cycle time by an average of 46%. -Increased on-time delivery to customer by an average of 28%. -Reduced quality escapes to the customer by an average of 60%. -Participated in the development and implementation of an operations capacity model.
-
-
Education
-
Arizona State University
MBA -
Arizona State University
Bachelor of Science - BS, Management
Community
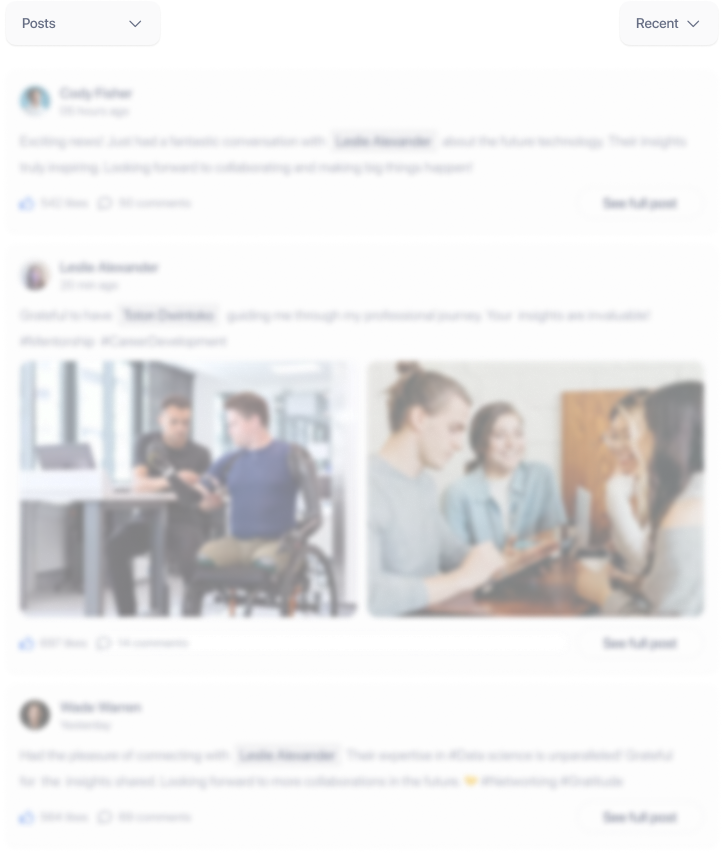