Sarabjit Singh
Chief Operating Officer at MAHLE ANAND Filter Systems Private Limited- Claim this Profile
Click to upgrade to our gold package
for the full feature experience.
Topline Score
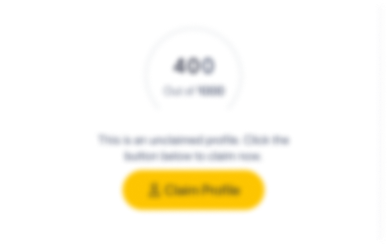
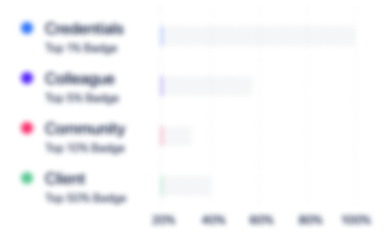
Bio

Sincere, well knowledgeable person. Lively nature.

I have worked closely with Sarabjit. He is always willing to learn and take up new challenges. He will always like to experiment with new ideas and find out best alternative. He will give his best to see the results through. It was always pleasure working with him.

Sincere, well knowledgeable person. Lively nature.

I have worked closely with Sarabjit. He is always willing to learn and take up new challenges. He will always like to experiment with new ideas and find out best alternative. He will give his best to see the results through. It was always pleasure working with him.

Sincere, well knowledgeable person. Lively nature.

I have worked closely with Sarabjit. He is always willing to learn and take up new challenges. He will always like to experiment with new ideas and find out best alternative. He will give his best to see the results through. It was always pleasure working with him.

Sincere, well knowledgeable person. Lively nature.

I have worked closely with Sarabjit. He is always willing to learn and take up new challenges. He will always like to experiment with new ideas and find out best alternative. He will give his best to see the results through. It was always pleasure working with him.

Experience
-
MAHLE ANAND Filter Systems Private Limited
-
India
-
Motor Vehicle Manufacturing
-
300 - 400 Employee
-
Chief Operating Officer
-
Apr 2021 - Present
-
-
-
Anchemco ANAND
-
India
-
Automotive
-
1 - 100 Employee
-
Chief Operating Officer
-
Sep 2020 - Mar 2021
-
-
-
-
COO-PCBU
-
Jan 2017 - Aug 2020
Gabriel India Ltd., leading manufacturer of Shock absorbers for the Automobile manufacturers with turnover more than 15 Bio INR/Annum Business Development Multi location operation management Improvement of the profitability by negotiating selling price and taking decision of make or buy. Deriving of the organization goal & target alignment with the Organizational KPI by use of X matrix, KRA setting and appraisal process. Systematic introduction of the process approach
-
-
COO-PCBU
-
Jan 2017 - Aug 2020
-
-
-
Takata
-
United States
-
Motor Vehicle Manufacturing
-
700 & Above Employee
-
Chief Operating Officer
-
Dec 2013 - Dec 2016
Successful handling of transition of responsibility and management of the operation of Takata India. Deriving of the organization goal & target alignment with the global KPI by use of X matrix, KRA setting and appraisal process. Systematic & procedural introduction of the process of monitoring of the achievement of the department objective with respect to the goal setting. Course correction & support in case of non-achievement Daily operation review and management of operation in Chennai & Neemrana. Development of the team and continuous interaction to realize the smooth operation without any surprise Inventory reduction and minimization of the variance. Financial accuracy and strict control, on the premium freights Capex and Expense budget planning for the operation and with target of saving of 10% from the budget by projects. Maximize utilization of the equipment and facility. Reduced financial load 100 % delivery for Honda san from the inception & 100% for Nissan in FY 16. No failure in delivery for all the other customer 100 % event management for the new projects. Successful event management for the Honda san, Nissan san, Maruti Suzuki san, Daimler san & other customers Project management & Greenfield setup for the Neemrana plant. Selection of the utility equipment, cost finalization and legal compliance for the new setup. Recruitment and selection of the team of optimum size. Rapport building with the customer. Meeting customer on periodic basis to understand the requirement and proactively eliminate issues Established Cost of poor quality control. Improvement & control on scrap & premium freights New initiative of Supplier partnership, supplier up gradation. Introduction of best practice of Human capital Identification of the key talent for the organization. Developing & motivating key talent for achieving the organizational requirements Compliance to all legal & statutory requirements.
-
-
-
-
Program coordinator
-
Dec 2012 - Dec 2013
• Program coordination of Global projects• Lead Indian Team in Japan and start exchange program.
-
-
-
Takata
-
United States
-
Motor Vehicle Manufacturing
-
700 & Above Employee
-
Plant Manager
-
Jul 2009 - Dec 2012
• Team selection and team building • Preparation of Plant CAPEX budget and Expense Budget • Organizational Goal adherence and to meet the stakeholder expectations• Shop floor management• Managing profit and loss for the plant and adherence to the budget• Contingency Planning for the manpower, machinery and other resource• Inventory control and management for the plant• Adherence to the statutory,legal requirement & QMS(TS16949)Project Head for the Greenfield project• Selection of contractors & manufacturers • Tendering and awarding of contract to the contractors• Project monitoring and course correction based on the progress.• Finalization of the machine specification• Capex generation • Machine inspection• Installation of the machine• Layout design and finalization• Tooling Management
-
-
-
Gabriel India Limited
-
Motor Vehicle Manufacturing
-
700 & Above Employee
-
Sr. Manager-process TSG & Manufacturing
-
Feb 2003 - Jul 2009
Technical Services, Process Management & Improvement Head• TPM & TPS coordinator for the plant• Lean Coach for the plant• Management of Asset Budget and maximum utilization of resources• Functioning of the plant as per the QMS (TS16949) • Implementation of MOST and improvement in MOP Team member for the Greenfield project• Selection of machine manufacturers • Machine Specification & RFQ finalization • Project monitoring and course correction based on the progress.• Capex management • Machine inspection• Installation of the machine• Layout design and finalization• Tooling ManagementProduction Management• Manpower & Capacity planning• Resource allocation• Interaction with customer for quality & delivery • Interaction with other functions for synchronized working• Initiation of improvements and team management
-
-
-
-
Line Incharge (Engineer-Production)
-
Nov 2001 - Feb 2003
• Production management for the machine area. • Assistant to MR (Management Representative) for TS 16949.• Initiation and monitoring kaizen activities across the plant.• Verification of process capability by using SPC as a tool.• Implementation of mistake proofing by doing Poka Yoke.• Conducting MSA for various measuring instrument.• Layout management of m/c area.• Internal Auditor for the TS 16949
-
-
-
-
TPM engineer
-
Oct 1999 - Nov 2001
• Coordination of TPM activities across the plant.• Coordination with CII and Yamaguchi San for the implementation of TPM• Coordination of cost reduction activities.• Implementation of activities to reduce set up time (Kobetsu Kaizen).• Implementation of the concept of autonomous maintenance.(Jishu Hozen)• Implementation of kaizen activities across the plant.
-
-
Education
-
Management Development Institute
MBA, operation & Strategy -
Gulbarga University
Bachelor of Engineering (BE), Mechanical Engineering -
Faith Academy
Senior Secondary, Science
Community
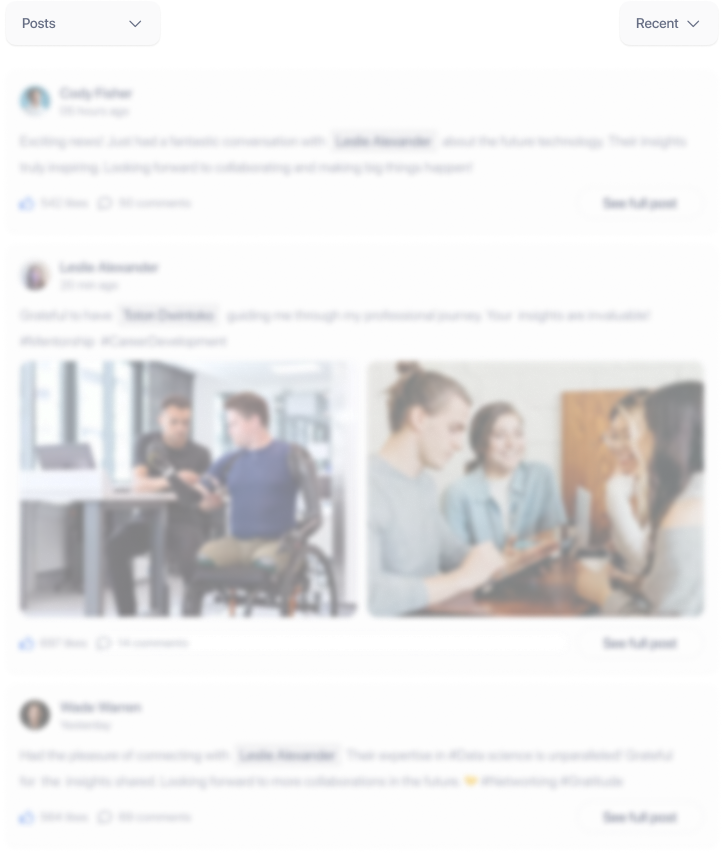