
Samarth Mehrotra
Mechanical Static Engineer, Technical Authority at Shell- Claim this Profile
Click to upgrade to our gold package
for the full feature experience.
Topline Score
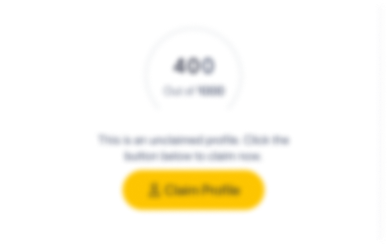
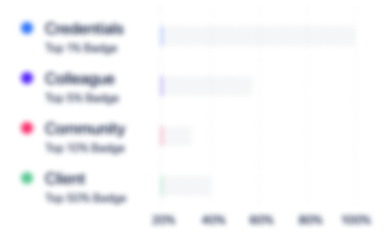
Bio


Experience
-
Shell
-
United Kingdom
-
Oil and Gas
-
700 & Above Employee
-
Mechanical Static Engineer, Technical Authority
-
Sep 2011 - Present
Selection, specification, construction and monitoring performance and integrity and reliability of mechanical static equipment, the major components of which include piping systems, valves, pressure vessels, heat exchangers and tanks for 2 offshore installations in the Central North Sea.Key highlights include•Reviewed materials corrosion and damage reports (MCDR), carried out fitness for service assessments (API 579 Level 1 and 2) and propose temporary/permanent repairs for all of the above mentioned mechanical static equipment.•Liaised regularly with inspection and materials & corrosion engineer to implement Shell Risk Based Inspection (S-RBI) to set inspection frequencies for pressure vessels and piping systems.•Participated in several root cause analysis•Implemented new hot bolting technology for 4 bolt flanges across assets to save significant costs.•Have been involved in using various NDT techniques for inspection such as manual UT, Radiography, DPI, MPI, Time of flight diffraction, Pulsed eddy current, IRIS, thermal imaging etc.•Carried out brittle fracture assessment in line with PSBR8 (EP201106207994) for selected piping and pressure vessels.•Lead Hydrocarbon leak reduction project work stream (UK wide) - Valve Maintenance Strategy•Generated maintenance reference plans (MRP) for static equipment for offshore installations•Contract Holder responsibility for 2 contracts.•Generated and implemented preventative maintenance routines for critical valves and plate pack heat exchangers.•Reviewed MOC (Management of Change) generated by asset teams and reviewed the change proposal specification generated by the engineering contractors for these MOC's.•Implemented Pipe work Vibration Strategy on the offshore assets (as per Energy institute guidelines)•Offered support to turnaround teams for scope development and challenge.•Participated in 1 major offshore incident investigation•Lead maintenance campaigns on ageing assets.
-
-
Project Engineer, Asset Delivery Team
-
Jun 2010 - Sep 2011
Managing the delivery of Pearl GTL project (largest GTL plant in the world) in the following capacities:•Managed the delivery of the asset (Air Separation Units, worth $ 1 billion) by the implementation contractor (Linde).•Monitored the project progress in terms of construction, commissioning and start-up, resolving engineering issues on a daily basis. •Interfaced with commissioning manager and discipline superintendents to raise any equipment issues observed during site walks that may jeopardize C&SU.•Interfaced with the contractor to decide way forward on technical disputes. •Coordinated interdisciplinary team of engineers to ensure complete site inspections are carried out.•Orchestrated audits for verifying the implementation of company prescribed quality standards such by the contractor •Involved with screening Project Management Lessons Learned for Pearl GTL and passing them to central Shell organization.•Involved with generating Project Close Out Report for Pearl GTL
-
-
Service Engineer, Clean Coal Technology Group
-
Jun 2009 - May 2010
Provided trouble-shooting support to the running gasification plants.Key Highlights Include:•Performed Root cause analysis (RCA) for mechanical failures occurring on site during start-up and normal operations.•Conducting fit-for purpose design calculation for pressure vessels and piping using design codes.•Proposed design solutions/trouble shooting for start-up of plants.•Developed standard equipment inspection plan and guidelines for gasification equipments.•Carried out site inspection of gasification equipments.•Analyzed plant operating and performance run data to calculate fouling factors of heat exchangers and overall heat and mass balances.•Mentoring and training Beijing SCGP operational services team to interface with clients.
-
-
Mechanical Equipment Design Engineer, Clean Coal Technology Group
-
Apr 2007 - May 2009
Developed the design of bespoke clean coal projects for Projects & Technology division of Shell InternationalKey Highlights Include:•Worked in a team to design a coal gasification plant (BDP/BDEP package) for Zerogen, Australia.•Carried out mechanical completion inspection for coal gasification plants in China.•Carried out workshop inspections of key gasification equipment (internals and pressure vessel) at vendor site.•Worked on remodeling and improvement of the main equipment design tool for coal gasification.•Developed and reviewed mechanical equipment specifications for various critical equipments like gasifier, special filters, special valves, coal burners etc used in gasification.•Developed material specification for coal gasification plants.•Developed general valve selection philosophy for coal gasification plants.•Reviewed of piping classes, plot plan layouts and heat exchanger designs for SCGP plants.
-
-
Design Engineer, Mechanical and Heat Transfer Group
-
Jul 2006 - Mar 2007
Developed design of pressure vessels and internals for hydro-processing reactors.Key Highlights Include•Design of pressure vessels and reactor internals for Hydro processing reactors. (Main deliverable s – Basic Design Engineering Packages)•Carried out vendor inspection of mock-ups for reactor internal trays
-
-
Education
-
Indian Institute of Technology (Indian School of Mines), Dhanbad
Bachelor’s Degree, Mechanical Engineering
Community
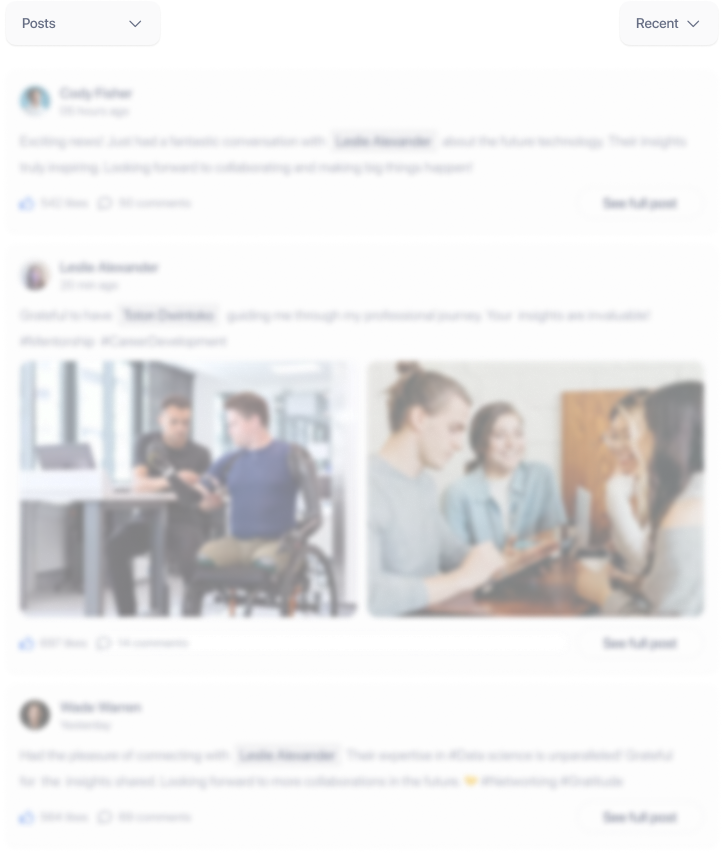