Sam Scott
Manager, Supply Chain Management at Raytheon Technologies- Claim this Profile
Click to upgrade to our gold package
for the full feature experience.
Topline Score
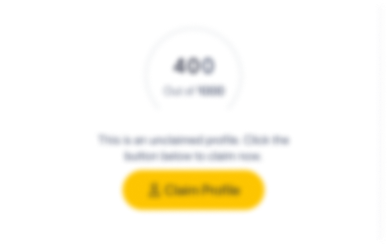
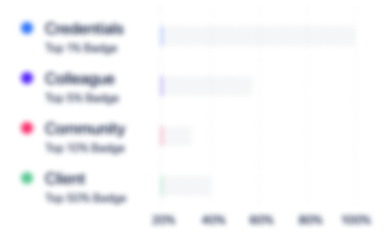
Bio


Credentials
-
EIT Certified
-Oct, 2012- Oct, 2024
Experience
-
Raytheon Technologies
-
United States
-
Aviation and Aerospace Component Manufacturing
-
700 & Above Employee
-
Manager, Supply Chain Management
-
Jun 2021 - Present
-
-
Subcontract Program Manager
-
Jun 2020 - Jun 2021
My second role in the Leadership Development Program was a Subcontract Program Manager (SPM), primarily supporting the TPY Contracts and Logistics program (CLS), a strategic capture program, and the KSA TPY program – all within Raytheon Missiles and Defense.With an SPM, the Supply Chain function leads the management of the subcontract team from strategic development through tactical execution to produce major assemblies. As an SPM supporting three different programs, I was able to lead and support front end activities such as Best Value Source Selection, SOW development, RFP issuance and negotiation, and supplier assessments, while also managing program execution tasks such as contractual requirements (SDRL) completion, risk and opportunity management, and establishing daily and weekly process management activities. These activities helped the CLS program pilot a new outsourcing process to significantly reduce (approx. 68%) repairs lead times and negotiate 11% savings for a proof-of-concept structure build to support new business capture.
-
-
Material Program Manager
-
Jan 2019 - Jun 2020
My first role in Raytheon’s Supply Chain Leadership Development Program was a Material Program Manager (MPM), primarily supporting the Next Generation Jammer program within Raytheon Intelligence and Space.As an MPM, I acted as the primary supply chain resource for the Power & Cooling and Product Support Integrated Product Teams (approximate combined total value $42M). My responsibilities were to create and maintain the material strategy, including financial reporting, supplier startup for first time builds, and managing other tactical Supply Chain activities such as directed procurements, Return to Vendor, Sole Source Justification, and supplier database approvals. My greatest accomplishments included reduction of late to MRP material through requirements burndown, expediting demand creation and PO placement for unique procurements for Product Support, and financial reporting despite constantly changing MRP requirements.Additionally, I also served as the MPM supporting NGJ High Band, an Internal Research and Development program. This provided me the opportunity to work in a smaller team with significantly more autonomy but also harsher time constraints. I was able to expedite material procurement navigating various strategic supplier agreements to successfully support sample CCA builds within three months.
-
-
-
CHC Helicopter
-
United States
-
Airlines and Aviation
-
700 & Above Employee
-
Fleet Strategy Intern
-
Jun 2018 - Aug 2018
Working with the Strategy Committee, I created the Aircraft Requisition Form that can forecast regional P&L impacts of new aircraft leases or lease extensions. After developing the formula for Total Lease Cost, I built the form in Excel, which was connected to CHC’s data warehouses using SQL for live data from each specific aircraft and contract. This not only allows for more precise cost estimation but also enables revenue forecasting based on historical contract structures. The Form also standardizes the Regional Sales teams’ aircraft requests, which increases awareness of total lease cost, incorporates Supply Chain and Fleet Management into decision-making, and expedites the approval process. I also developed the Capital Allocation Playbook, which will be used to inform CHC’s operating regions of the Strategy Committee’s outputs and ongoing Fleet updates. This was accomplished by attending the Strategy Committee’s workshops and interpreting results into various distributable methods, including a brochure cheat sheet.
-
-
-
4FRONT Engineered Solutions
-
United States
-
Industrial Machinery Manufacturing
-
200 - 300 Employee
-
Product Design Engineer
-
Jun 2013 - Aug 2017
My responsibilities were most basically to improve any and all facets of the performance and production of loading dock equipment.However, my greatest accomplishment in doing this was creating the product release procedure for new products and defining the Lead Engineer’s role as a project manager as opposed to simply being a product designer.For example, I was the lead engineer for the release of a new brand of dock leveler. This new line of products, which consisted of mechanical, air, and hydraulic powered levelers, required not just new mechanism designs, but also incorporation into existing production capabilities and implementation into our ERP system. New product design and release required extensive communication and collaboration with all functions of the business, including senior management in Operations, Manufacturing, Quality, and Sales.I also designed a telescoping support strut to detect truck-restraint jams at dock loading and unloading. Technically, this was accomplished by modifying the existing strut casting to a new weldment mechanism with an integrated proximity switch while maintaining safety standards required by the restraint. Practically, this was accomplished by working extensively with Customer Service, Quality, and end users to accurately define and eventually solve this unique problem created by a specific set of building, product, and truck combinations.Other various responsibilities and accomplishments include: collaborating with Operations to create and restructure production organization in JDE, visiting client sites to provide technical support, representing the Engineering department at weekly Quality meetings and daily Tactical Operations meetings, internally auditing the Quality Control and Customer Service departments for ISO Compliance certification, assisting Sales with custom branded product renderings, and providing engineering assistance to our aftermarket product specialist.
-
-
Product Design Engineer Intern
-
Sep 2012 - May 2013
Similar to my current position, product improvement is primarily accomplished through geometrical design, material selection, and drawing modification.I developed a standardized lip plate maintenance bar by consolidating three distinct designs into one universal design for different high capacity dock levelers, and I created reinforced mounting mechanisms for hydraulic power units.
-
-
-
Southern Methodist University
-
United States
-
Higher Education
-
700 & Above Employee
-
Undergraduate Researcher
-
Jul 2011 - Sep 2012
Working alongside an Assistant Professor in the Physics department, I used data from the Babar Experiment at SLAC in the search for dark matter's equivalent of a photon, a dark photon. This is accomplished primarily through coding in Python using data stored in ROOT files. Working alongside an Assistant Professor in the Physics department, I used data from the Babar Experiment at SLAC in the search for dark matter's equivalent of a photon, a dark photon. This is accomplished primarily through coding in Python using data stored in ROOT files.
-
-
-
SMU Guildhall
-
United States
-
Higher Education
-
100 - 200 Employee
-
Counselor
-
Jun 2010 - Jul 2010
Counselors are in charge of a group (sizes ranging from 6 to 10) of 6-12 year olds. Participating in activities from fitness and crafts to intramurals and swimming, I assure safety and provide a fun atmosphere in a recreational setting. This required certification in CPR and First Aid. Counselors are in charge of a group (sizes ranging from 6 to 10) of 6-12 year olds. Participating in activities from fitness and crafts to intramurals and swimming, I assure safety and provide a fun atmosphere in a recreational setting. This required certification in CPR and First Aid.
-
-
Education
-
Southern Methodist University
Bachelor of Science, Mechanical Engineering -
The University of Texas at Dallas
Master of Business Administration - MBA
Community
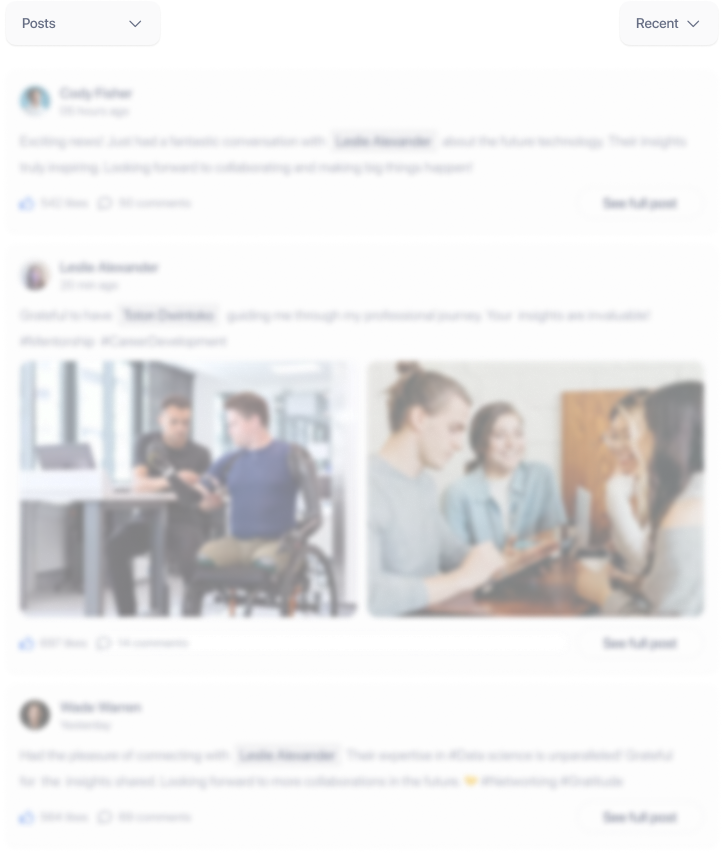