Saloni Tomar
at Worley- Claim this Profile
Click to upgrade to our gold package
for the full feature experience.
Topline Score
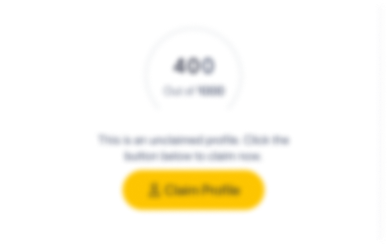
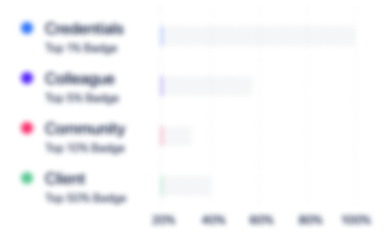
Bio


Experience
-
Worley
-
Brazil
-
Business Consulting and Services
-
700 & Above Employee
-
-
Nov 2022 - Present
-
-
-
Nov 2021 - Present
-
-
-
Umagine
-
India
-
Climate Technology Product Manufacturing
-
1 - 100 Employee
-
-
Apr 2021 - Jul 2021
As Process Engineer Hydrogen, my main task is to research moon-shot hydrogen-based solutions for a clean energy economy. Additionally, I am responsible to develop sustainable products and services with a short realisation time: my tasks range from developing system designs, communicating with internal and external stakeholders to developing business models for the projects. As Solar Design Engineer, I manage the PV installations in the north-east region of the Netherlands. My responsibilities include but are not limited to planning and designing the projects, and people management. Show less
-
-
-
Jan 2021 - Mar 2021
-
-
-
TNO
-
Netherlands
-
Research Services
-
700 & Above Employee
-
Graduate Student Intern
-
Jan 2020 - Sep 2020
My project title is "Techno-economic evaluation of bio-hydrogen production via membrane reforming and cryogenic CO2 separation." The objective was to develop a process that produces clean hydrogen to be used as a transportation fuel in fuel cell vehicles. Currently, the majority of hydrogen is produced via the conventional steam methane reforming process, resulting in high CO2 emissions. Therefore, the purpose of this research is to determine the economic potential of using the novel technologies to produce fuel-grade hydrogen, to realize a low carbon society, and promote sustainable growth for the transportation sector. The novel process designed is capable of producing fuel-grade hydrogen at 30% lower cost and 90% lower (near-zero) CO2 emissions compared to the conventional process. Future scenarios also revealed that this novel process is capable of achieving negative CO2 emissions. Show less
-
-
-
ZEF B.V. - Zero Emission Fuels
-
Netherlands
-
Industrial Machinery Manufacturing
-
1 - 100 Employee
-
Research Intern
-
Sep 2019 - Dec 2019
I designed and developed a degassing system to purify the feed water into the Alkaline Electrolyser. The purpose of the degassing system is to remove the residual CO2 in the water being fed to the alkaline (KOH) electrolyser to improve its performance. This degassing system was validated by performing lab-scale experiments. I designed and developed a degassing system to purify the feed water into the Alkaline Electrolyser. The purpose of the degassing system is to remove the residual CO2 in the water being fed to the alkaline (KOH) electrolyser to improve its performance. This degassing system was validated by performing lab-scale experiments.
-
-
-
Atul Ltd
-
India
-
Chemical Manufacturing
-
700 & Above Employee
-
Management Intern
-
Apr 2016 - Sep 2016
Due to the water crisis in Gujarat at the time, my assignment was to design a network to reuse the heat from the condensate streams to be used for the auxiliary process. The designed network was economically profitable and also environmentally sustainable. Due to the water crisis in Gujarat at the time, my assignment was to design a network to reuse the heat from the condensate streams to be used for the auxiliary process. The designed network was economically profitable and also environmentally sustainable.
-
-
-
Bharat Petroleum Corporation Limited
-
India
-
Oil and Gas
-
700 & Above Employee
-
Technical Intern
-
May 2015 - Jul 2015
My assignment was to design and improve the heat exchanger(s) placed in the crude distillation unit. The heat exchanger was designed manually referring to design handbooks. The new design was compared to the actual design of the heat exchanger(s) in operation and the updated design was improved to reduce capital and operation costs. My assignment was to design and improve the heat exchanger(s) placed in the crude distillation unit. The heat exchanger was designed manually referring to design handbooks. The new design was compared to the actual design of the heat exchanger(s) in operation and the updated design was improved to reduce capital and operation costs.
-
-
Education
-
Delft University of Technology
Master's degree, Sustainability Studies -
Mukesh Patel School Of Technology, Management and Engineering,NMIMS
MBA(Tech.), MBA in Technology Management and BTech in Chemical Engineering
Community
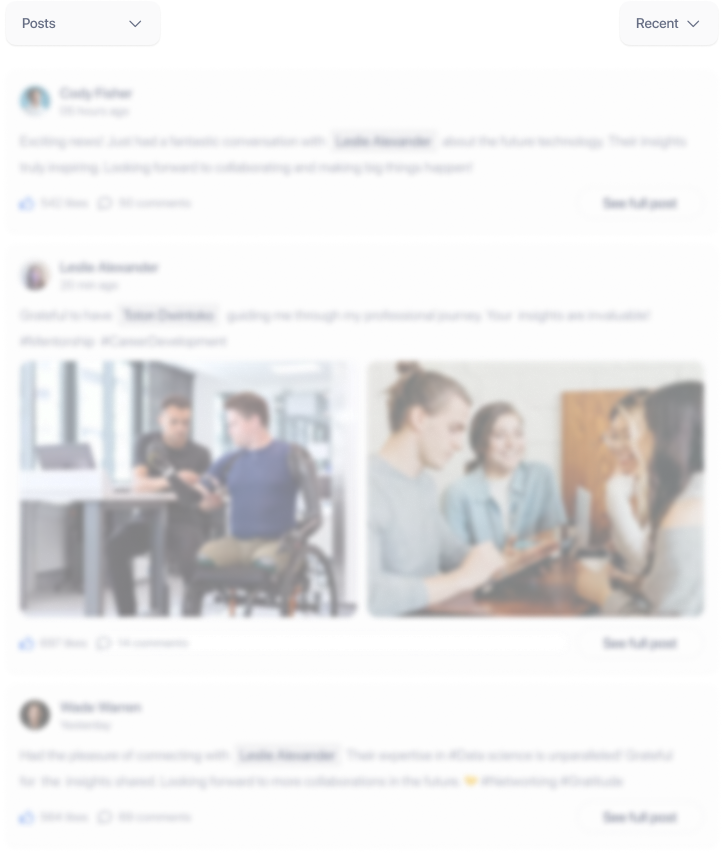