
Salima Remtulla
Manager, Quality Systems at Revelle Aesthetics, Inc.- Claim this Profile
Click to upgrade to our gold package
for the full feature experience.
-
Gujarati -
-
Swahili -
-
Hindi -
Topline Score
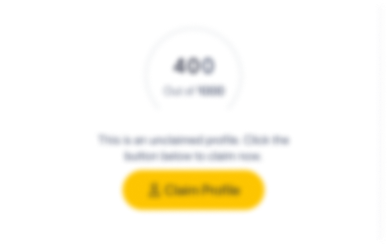
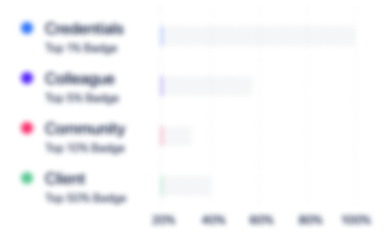
Bio

Harry Hari
Salima worked in my team in Milpitas. She did an excellent job leading the teams in successful CAPA closures. Salima also supported establishing the quality management system with associated procedures which included training for all levels of the organization. Salima is friendly and approachable. Her proactive approach to quality will be an asset to any organization.

Paul O'Connor
Salima is an excellent Quality resource to support and ensure that all aspects of Production and Operations are performed and meet all of the necessary quality/regulatory requirements. Salima consistently worked with engineering in providing suggestions and solutions to move forward rather than be a static road block. Salima is both proactive and positively reactive and constantly finds and implements process improvements.

Harry Hari
Salima worked in my team in Milpitas. She did an excellent job leading the teams in successful CAPA closures. Salima also supported establishing the quality management system with associated procedures which included training for all levels of the organization. Salima is friendly and approachable. Her proactive approach to quality will be an asset to any organization.

Paul O'Connor
Salima is an excellent Quality resource to support and ensure that all aspects of Production and Operations are performed and meet all of the necessary quality/regulatory requirements. Salima consistently worked with engineering in providing suggestions and solutions to move forward rather than be a static road block. Salima is both proactive and positively reactive and constantly finds and implements process improvements.

Harry Hari
Salima worked in my team in Milpitas. She did an excellent job leading the teams in successful CAPA closures. Salima also supported establishing the quality management system with associated procedures which included training for all levels of the organization. Salima is friendly and approachable. Her proactive approach to quality will be an asset to any organization.

Paul O'Connor
Salima is an excellent Quality resource to support and ensure that all aspects of Production and Operations are performed and meet all of the necessary quality/regulatory requirements. Salima consistently worked with engineering in providing suggestions and solutions to move forward rather than be a static road block. Salima is both proactive and positively reactive and constantly finds and implements process improvements.

Harry Hari
Salima worked in my team in Milpitas. She did an excellent job leading the teams in successful CAPA closures. Salima also supported establishing the quality management system with associated procedures which included training for all levels of the organization. Salima is friendly and approachable. Her proactive approach to quality will be an asset to any organization.

Paul O'Connor
Salima is an excellent Quality resource to support and ensure that all aspects of Production and Operations are performed and meet all of the necessary quality/regulatory requirements. Salima consistently worked with engineering in providing suggestions and solutions to move forward rather than be a static road block. Salima is both proactive and positively reactive and constantly finds and implements process improvements.
0
/5.0 / Based on 0 ratingsFilter reviews by:
Experience
-
Revelle Aesthetics, Inc.
-
United States
-
Medical Device
-
1 - 100 Employee
-
Manager, Quality Systems
-
May 2020 - Present
• Upgrading and maintaining company’s Quality System to meet ISO 13485:2016 and the MDSAP requirements. In process of hosting Stage 1 audits by the Auditing Organization.• Supporting R &D, Manufacturing, and other areas to assure high quality products are developed for Clinicals and for Commercialization. • Responsible for various areas of QMS; from Training and Document Control to Calibration/Preventive Maintenance, from Supplier Management and Qualification to Internal/External audits and Complaint management.• Developing validation test protocols and reports for various areas such as Sterilization, Biocompatibility, and Medical Electrical Equipment (IEC 60601 compliant).• Revamping risk management process to ensure it is compliant with ISO 14971 and creating procedures for Usability/Human Factors engineering in compliance with ISO 62366-1.• As the Management Representative – lead Management Reviews; liaise with external auditors on matters relating to registration, certification, audits, etc.• Researched and evaluated various electronic QMS platforms to meet the company needs and improve efficiency while supporting company growth.• Periodically analyzing and reporting trends on key metrics to evaluate effectiveness and suitability of company’s QMS thereby identifying and continuously addressing areas for improvement.
-
-
-
Moximed
-
United States
-
Medical Equipment Manufacturing
-
1 - 100 Employee
-
Manager, Quality Assurance
-
Dec 2017 - Dec 2020
• Maintained and continuously improved Moximed’s Quality Management System to comply with applicable FDA regulations and international ISO standards. Transitioned the company’s QMS to ISO 13485:2016.• Managed all aspects of internal quality from incoming inspections to NCMRs and MRB to addressing day-to-day manufacturing challenges to assure product quality.• Supported, and where appropriate drove, product development and project improvement activities not limited to managing risk analysis, product/process validation including product sterilization and dose audits. • As a Management Representative, led the Management Review meetings. Managed Quality Objectives and on a periodic basis reported these and other Key Performance Indictor (KPIs) to the leadership team.• Revamped CAPA process (as a six-sigma project), ensured level of investigation and root cause analysis was commensurate based on risk. • Per schedule, coordinated and hosted external ISO audits and conducted supplier quality audits based on risk-approach. • As appropriate, assisted with inputs to periodic Post-Market Surveillance Status (PMS) Reports and device specific information for the Clinical Evaluation Reports (CER). Supported activities related to Technical Files (for CE Marked Product) to demonstrate continual compliance with European requirements and renew the product certificate.
-
-
-
NeoPhotonics
-
United States
-
Telecommunications
-
200 - 300 Employee
-
Sr. Manager, Quality
-
Jan 2011 - May 2017
• Supervised and guided team of 3-10 people (at different times) within the Quality department.• In 2012 – integrated two different companies’ Quality Systems (with separate registrars) into one US based QMS certified under one ISO 9001 registrar. Created such a robust QMS that between 2015 – 2017, the ISO auditor found no major non-conformances during the annual surveillance / triennial audits.• Managed Internal Audit program which included generating yearly schedules, selecting, and training auditors and qualifying them to become independent internal auditors. Ensured all internal audits were completed within specified time. • Accountable for entire CAPA program. From hosting CAPA meetings, monitoring daily progress to driving root cause analysis and resolving discrepancies. Reduced # of aging CAPAs down to 80% compliance.• Managed Document Control department: resolved ECO related issues (both from CMs and other global sites) to ensure smooth document control operation. • As Management Representative, led the bi-annual Management Reviews; liaised with external auditors; and where necessary, implemented changes to drive Quality System improvements. • Coached individuals on Quality Policy & procedures, promoted awareness of project-specific quality and performance standards and ensured they were adequately documented, communicated, and understood. • Drove continuous improvement projects in various areas: Product Design, Failure Mode and Effects Analysis (FMEAs), Customer Complaints, etc. • In conjunction with HR, identified relevant training needs and developed (first) Training Requirements Matrix for all departments. Developed procedures, respective training materials and where necessary provided training to individuals.• Where appropriate managed the financial objectives, prepared annual operating budgets, controlled expenditures, analyzed and reconciled budget conflicts.
-
-
-
Flextronics
-
United States
-
Staff Quality Engineer
-
Jan 2007 - Nov 2010
(From Jan 2009 - Nov2010) - Managed the Corrective and Preventive Actions (CAPA) and handled Customer Complaints for the Bay Area location. - Participated in ISO Certification, surveillance audits and various Customer audits. - Wrote procedures, prepared technical documents, generated variety of reports, etc.(From Jan 2007 - Jan 2009)- Responsible for establishing the quality systems, especially the design control procedures, in conformance with the FDA QSR and ISO 13485 regulatory standards. - Managed the design quality department, provided guidance and served as a lead/coach/trainer for design engineers in the implementation of design controls, GMP and risk management activities according to ISO 14971.
-
-
-
Adiana
-
Medical Equipment Manufacturing
-
1 - 100 Employee
-
Quality Engineer
-
Apr 2004 - Jan 2007
• Developed detailed procedures and validation test protocols based on product specifications and risk analysis in collaboration with the development team.• Performed validation studies on the Tray Sealer, device Shelf Life/Aging and generated appropriate final reports.• Worked in the manufacturing floor to identify appropriate monitoring and control mechanisms based on product risk analysis. • Managed inconsistencies related to LHRs, DHF, labelling and device traceability and accuracy of records. • Participated in design reviews, team meetings, and assisted in design control projects and quality plans in accordance with internal procedures.• Improved training non-compliance from 50% to 5% in three months.• Assisted in PMA modular activities of compiling and reviewing device history and technical sections i.e., biocompatibility, engineering bench testing, etc.
-
-
-
Nektar Therapeutics
-
Biotechnology
-
300 - 400 Employee
-
Device Process Engineer II
-
Oct 2002 - Nov 2003
• Served as a communication liaison between inter-departmental and cross-functional teams to ensure design development activities and project goals were achieved within proposed timeframes.• Responsible for supplier audit of the contracted design firm in the UK with the aim to ensure they met internal requirement while maintaining their established procedures and applicable FDA standards. Generated audit reports to identify gaps in their system and help address the gaps before transferring of design and technical documents.• Scheduled, organized, and tracked open actions from Design Reviews and Risk Management activities. • Supported compliance related activities to ensure full traceability of materials used in manufacturing of the device (such as Design intent, component history, raw materials C of A, C of C, labeling and DMRs).• Actively managed various Design History File (DHF) and other technical documentation for the engineering team.
-
-
-
MDMI Technologies
-
Canada
-
Medical Equipment Manufacturing
-
Development and Manufacturing Engineer
-
1999 - 2001
Started as an R&D engineer supporting the design of PTCA catheters and other medical products for women's health but later transitioned into production to improve the manufacturing processes. Part of my job duty also included conducting market research on competitive products, liase with vendors, perform cost analysis, assist in device packaging design, product sterilization and clinical trial activities. Started as an R&D engineer supporting the design of PTCA catheters and other medical products for women's health but later transitioned into production to improve the manufacturing processes. Part of my job duty also included conducting market research on competitive products, liase with vendors, perform cost analysis, assist in device packaging design, product sterilization and clinical trial activities.
-
-
Education
-
California State University-San Bernardino
Lean Six Sigma Green (LSSGB) and Lean Six Sigma Black Belt (LSSBB) -
The University of British Columbia
B.A.Sc., Bio-Resource Engineering -
University of Alberta
B.Sc., Mathematics
Community
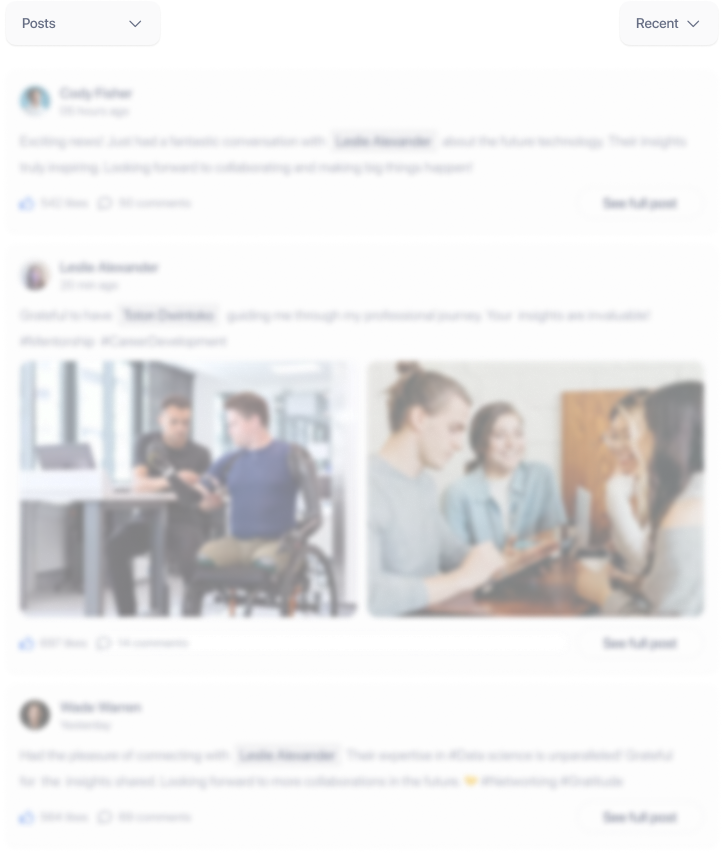