Salih C.
After Sales Services Specialist at Mitsubishi Heavy Industries Air-Conditioning Europe- Claim this Profile
Click to upgrade to our gold package
for the full feature experience.
-
İngilizce Full professional proficiency
-
Rusça Limited working proficiency
-
Türkçe Native or bilingual proficiency
Topline Score
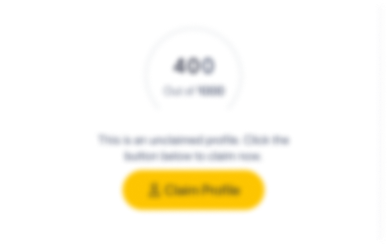
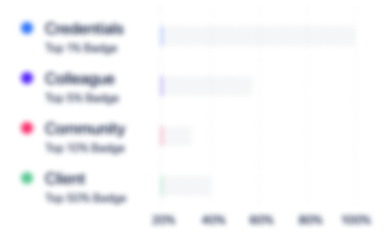
Bio


Experience
-
Mitsubishi Heavy Industries Air-Conditioning Europe
-
United Kingdom
-
Machinery Manufacturing
-
1 - 100 Employee
-
After Sales Services Specialist
-
May 2022 - Present
• Providing technical support to distributors/customers in Europe; responding to technical enquiries which are related to all MHI air conditioning and refrigeration products. • Visiting the site for commissioning/troubleshooting, • Organising seminars for distributors/customers, creating technical or nontechnical training presentations and preparing technical support and information documents, creating new service tools (e.g. e-learning activity) • Supporting MTH/MACO factories for aftersales activities; reporting to MTH/MACO about spare part and epidemic failure KPI analysis. • Supporting spare part activities for the operation team to improve the spare part deliveries. • Collecting market information/surveying for new products, benchmarking, and analysing competitors' new products. Show less
-
-
-
-
Director
-
Dec 2020 - Mar 2022
Sales, service, maintenance and repair of split AC units, VRF units, cold rooms and refrigerated display cabinets. Sales, service, maintenance and repair of split AC units, VRF units, cold rooms and refrigerated display cabinets.
-
-
-
-
After Sales Services Manager
-
Aug 2016 - Jul 2020
• Management of after sales services team in accordance with the company's targets and strategies; starting from the authorisation stage of service partner, performance evalution, executing and following of working processes. • To keep in touch with after sales service dept. of Hisense / Hitachi Company. • To complete the VRF, AHU and DX projects at the desired date and quality. • To execute the authorized service partner operations and services according to the determined date, quality and cost criteria and keeping update relevant reports. • To define deficiencies detected in after sales organization and initiating necessary corrective and preventive activities and adding technological developments. Determining need of service training, training organization and giving trainings. • Management of technical and field support process of service partners. • Follow-up of services taking from the other companies in case of need. • Providing technical documentation from Hisense / Hitachi and sharing critical issues with other departments, providing technical support to the sales department. • Service partner and customer visits when necessary. • Giving the service fee payment instructions and invoice approvals, follow-up payments and contracts with service partners. • Making site visits and the creation of action plans and eliminating the shortcomings seen as a result of these visits. • Determination of critical spare parts that can be asked by service partners according to failure analysis, pricing, tracking of minimum stock levels, providing spare parts service partners or customers. Show less
-
-
-
-
Technical Chief of After Sales Services
-
Feb 2013 - Mar 2016
• Managing and satisfying the technical service needs and negotiating with Italy company center in order to find a solution considering customer complaints and epidemic defects or quality problems for all products. Reporting all service KPI data to Italy center. Releasing and sharing quality reports with all plants in order to sustain product quality. • Evaluating technical / behavioral capacity and capability of the service partners in order to take action and improve service partners by field visits and analyzing KPI data. Eliminating the inadequacies that is observed during the visit of service partners. • Executing of quality improvement activities in order to find production line or defect diagnosis mistakes by service technicians by means of collecting defective samples of component and exchanged products from the field. • Preparing trainings to improve new or old product knowledge of service partners. • Planning and executing specific technical trainings corresponding to training needs on the basis of service KPIs and for the new service partners. (the basic or advanced level product training, lab. exercises, presentations of all product range, assessments and reporting & documentation) • Management of technical documentation (exploded views, spare part lists, technical bulletins) • Evaluating and reporting safety incident issues arising from products (Fire, water flooding etc.) • Developing educational learning solutions, presentation materials and techniques to improve knowledge of service solution of service partners. • Answering product complaints or technical / nontechnical support requests of service partners. • Assisting the area managers, sales and marketing departments, call center, spare part warehouse on technical issues. • Training cost budgeting and reporting. • Following Turkish Consumer Law and similar legal regulations. • Management of air conditioner & SDA (Small domestic appliances) Turkey service project. (Best Practice-2014) Show less
-
-
-
Vestel
-
Türkiye
-
Appliances, Electrical, and Electronics Manufacturing
-
1 - 100 Employee
-
After Sales Services Quality&Training Responsible
-
Mar 2012 - Feb 2013
• Planning and determining training requirements of the products which I was in charge of white goods. • Preparing the training & technical documentation, presenting the theoretical and practical training plan of the service organization and executing the regional training face to face, providing training in a live broadcast in the company. • Evaluating and reporting of the trainings. I was also responsible for building consistency by standardizing training materials which is previously prepared and keep going to enhance them. • Planning and executing specific technical trainings taking into account customer complaints and epidemic defects or quality problems such as part defect diagnosis and controls, lab. exercises. • Defining and implementing technical training strategies for all internal and external customers. • Making assessments and reporting & documentation at the end of trainings. Coordinating relations with service suppliers for services offered to training participants. Show less
-
-
-
-
Air conditioner & Heatpump R&D Project Leader
-
Jun 2011 - Mar 2012
• Managing and carrying out product (Airconditioner & Heatpump) improvement activities negotiating with Germany Company center by evaluating customer feedbacks and defect analysis. • Performing benchmarking and product cost reduction activities. • Controlling optimization of the production processes with cost saving projects. • Assisting the production, after sale services, quality and sales departments. • Following relevant test standards, pursuing product certification process and executing appropriate test activities depending on these results. • Confirming product capabilities, test control apparatus, equipment by studying feasibility and test methods in production and development of methods, procedures in order to test products. • Analysing field failures & making root cause clarification, addressing the failure to the related department. Carrying out negotiations including of supplier based on defected parts and ppm evaluation. • Developing / improving specifications of products with Chinese colleagues. Creating processes and work instructions specific for production. • Preparing documentation for the releasing of parts, components in the production. Preparing a test / trial concept, carrying out project planning and coordinating the final technical release in SAP. • Coordinating / confirming improvement projects relating with parts and components (in-house and externally procured) and releasing the finished products (manufacturing release). Show less
-
-
-
Kaplanlar Refrigeration INC
-
Türkiye
-
Retail Groceries
-
100 - 200 Employee
-
Technical Manager
-
Mar 2009 - Jan 2011
• Dealing with the customers and executing subcontractors in order to lead cooling projects for big supermarket chains and food production centers… • Coordinating the resource and capacity planning, taking in account the overall project roadmap for products and components. • Designing & developing mechanical and electromechanical products for the control systems by studying customer requirements and researching understanding industry trends. • Engineering project calculation; including piping, utilities, accessories, selecting devices, to decide production or procurement etc. Analysing and taking physical information (buildings, material flow, layout/flowchart etc.) by oversee construction site (domestic or international). • Identifying total hardware/software items and supply costs for a such system, to assist the sales department in selecting the most suitable and economical system. • Managing the technical support which is provided to all internal and external customers across the full product portfolio. Providing engineering information to customers by answering technical questions and requests corresponding with products, components and/or systems. Show less
-
-
-
-
Chief Engineer of Projects
-
Mar 2007 - Mar 2009
• Dealing with the customers in order to lead cooling projects for big supermarket chains and food production centers… • Providing engineering information to customers by answering technical questions and requests corresponding with products, components and/or systems for the most suitable and economical cooling project. • Experienced in customized machine sales (specific cooler and cooling system designs), technical sales and technical support with project management, • Designing refrigeration projects, cost calculation and proposal preparation. • Following up the production, oversee the construction site to ensure proper project plans and resources (people, facility, supplies etc.) efficiently in order to provide the uninterrupted supply of goods. Then, carrying out project plan. • Designing test methods to ensure finished product and system capabilities. Confirming production, assembly, and installing components. Show less
-
-
Education
-
Dokuz Eylul University
Mechanical Engineering, Termodynamics -
Dokuz Eylul University
MSc.Thermodynamics and Energy
Community
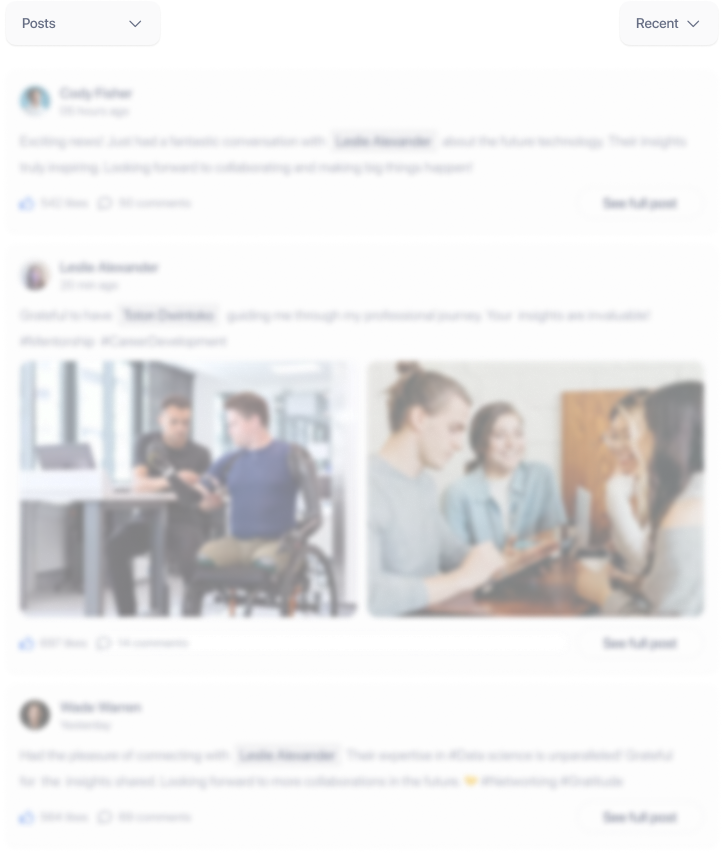