Sahan Hansitha
Operations Engineer - Component Manufacturing Unit at David Pieris Motor Company (Pvt) Ltd- Claim this Profile
Click to upgrade to our gold package
for the full feature experience.
Topline Score
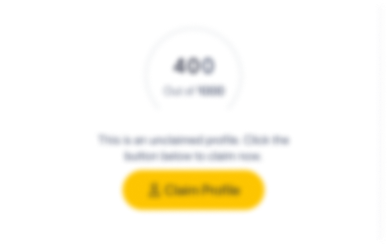
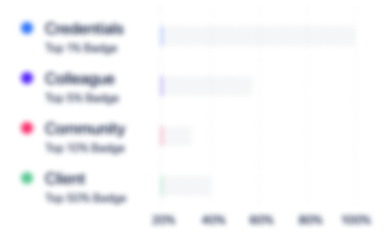
Bio


Credentials
-
Associate Member
Institute Of Engineers Sri LankaApr, 2021- Nov, 2024 -
Six Sigma Tools for Define and Measure
CourseraJun, 2020- Nov, 2024 -
Six Sigma Principles
CourseraMay, 2020- Nov, 2024 -
Artificial Intelligence Foundations: Neural Networks
LinkedInJan, 2020- Nov, 2024 -
Learning Microsoft Power BI Desktop
LinkedInJan, 2020- Nov, 2024 -
Microsoft PowerApps Essential Training: Beyond the Basics
LinkedInJan, 2020- Nov, 2024 -
Six Sigma Foundations
LinkedInJan, 2020- Nov, 2024
Experience
-
David Pieris Motor Company (Pvt) Ltd
-
Sri Lanka
-
Motor Vehicle Manufacturing
-
100 - 200 Employee
-
Operations Engineer - Component Manufacturing Unit
-
Dec 2021 - Present
-
-
Management Trainee - Component Manufacturing Unit
-
Dec 2020 - Dec 2021
-
-
-
Fonterra
-
New Zealand
-
Food and Beverage Manufacturing
-
700 & Above Employee
-
Manufacturing Engineering Intern
-
Dec 2019 - Jun 2020
During my 2nd training period in fonterra, I was assigned to work with the plants' digitization project. This plants' digitization project is conducted under the Integrated Work System (IWS) project. In the IWS concept there are 12 capability pillars linked to losses and there is a standard called Daily Management System (DMS). IWS pillars are created by DMSs. In Fonterra Brands Lanka (PVT) Ltd, there are 7 critical DMSs are tracking everyday. From those 7 DMSs Defect Handling (DH), Centerlines (CL) and Clean - Inspection - Lubrication (CIL) are the most critical DMSs. Under the plants' digitization project, I had to develop the computerized systems for most critical DMSs. Highlight works of plants' digitization project • Successfully designed and developed the computerized defect handling systems for liquid & culture plant, powder plant and site engineering section • Initiated the computerized centerlines management system for the liquid and culture plant • Initiated the computerized clean - inspection - lubrication (CIL) management system for the liquid and culture plant Other highlight works of IWS project • Restored all the IWS pillar boards • Designed and implemented the training boards for the autonomous maintenance pillar • Participated the training programs under autonomous maintenance pillar and preventive maintenance pillar Show less
-
-
-
Fonterra
-
New Zealand
-
Food and Beverage Manufacturing
-
700 & Above Employee
-
Engineering Inplant Trainee
-
Mar 2019 - Jun 2019
During the training period in fonterra, I was assigned to work with the liquid and culture plant. With that experience I could have very good knowledge about the whole manufacturing process, quality standards, performance measures and maintenance activities in liquid & culture plant. During my training period, I mainly focused on following works/projects. Introduced the concept of "Automated Defect Handling System". Under that, designed and developed the automated defect handling system for the manual defect handling process in liquid and culture plant. Used the Microsoft PowerApps tool (App development tool in Microsoft) to develop the system. Highlights • Totally eliminated the paper usage for the defect handling procedure in liquid & culture plant • Improved the efficiency of the defect handling procedure • Increased the transparency of the defect handling procedure • Created the dashboard for performance measurements of defect handling procedure Worked with the plant sustainability project in the liquid and culture plant. Mainly focused about steam saving and water saving in the plant. Highlights • Found new water and steam saving point in the plant • Calculated the saving steam and water amounts on all points • Developed the action plans for plant sustainability project Prepared the standard documents for the continuous improvement (kaizen) projects which were done in the liquid and culture plant. These documents were created according to the "A3" standard documentation procedure. Made improvements on the "standard ordering procedure" of the company. Show less
-
-
-
Sri Lanka Railways
-
Transportation/Trucking/Railroad
-
100 - 200 Employee
-
Engineering Inplant Trainee
-
Oct 2017 - Jan 2018
During the training period in Sri Lanka Railways, I was assigned to work with chief mechanical engineering workshops, Ratmalana Highlight areas, • Tool engineering • Manufacturing operations (lathe, milling,forming, grinding, etc) • Welding • Industrial safety During the training period in Sri Lanka Railways, I was assigned to work with chief mechanical engineering workshops, Ratmalana Highlight areas, • Tool engineering • Manufacturing operations (lathe, milling,forming, grinding, etc) • Welding • Industrial safety
-
-
Education
-
University of Peradeniya
B.Sc.Eng (Hons), Specializing in Production Engineering -
C.W.W Kannangara Central Collage, Mathugama
Mathematics
Community
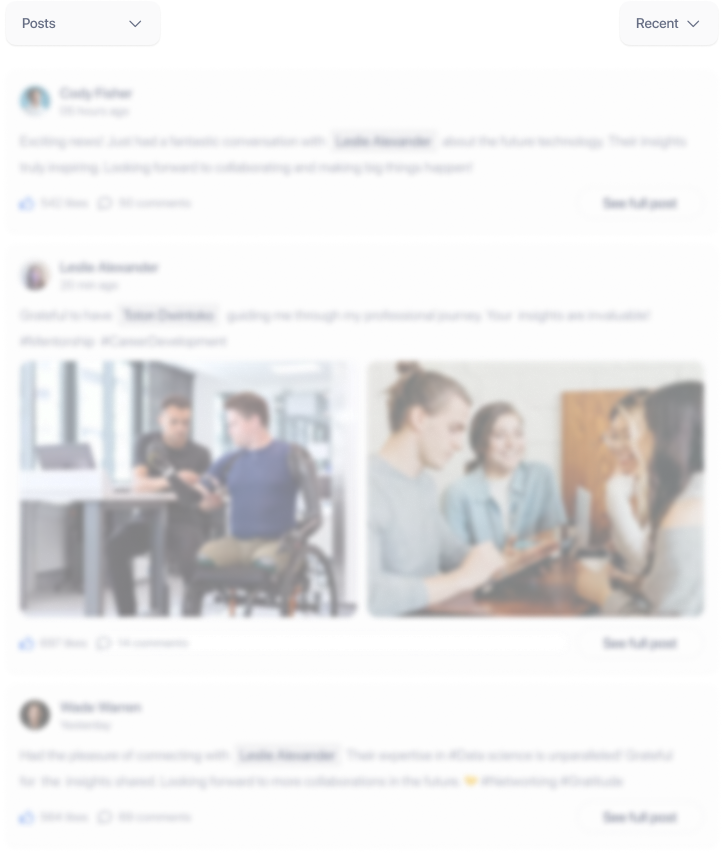