Sabine Moosmann
Qualitätsmanagerin at BBC Cellpack Technology- Claim this Profile
Click to upgrade to our gold package
for the full feature experience.
-
Deutsch -
-
Englisch -
Topline Score
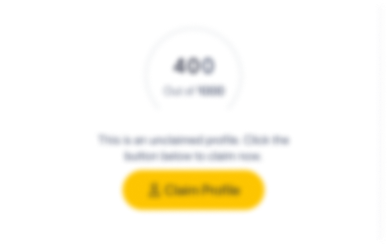
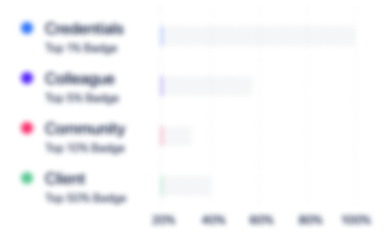
Bio


Experience
-
BBC Cellpack Technology
-
Switzerland
-
Medical Device
-
1 - 100 Employee
-
Qualitätsmanagerin
-
Feb 2021 - Present
-
-
-
-
Senior Compliance Specialist
-
Oct 2019 - Feb 2021
• Responsible for compliance according to the compliance requirements of all local, national, international and company regulations, guidelines and procedures for the local implementation of the quality system • Ensure that quality measures are carried out, all internal and external audit deviations are examined, the root cause analysis of failures is carried out, action plans are completed and appropriate effectiveness checks are carried out independently according to the agreed timetables• Contribute to improvement measures resulting from non-conformities, internal audits, quality board topics and other system indicators• Collaborate with other site compliance engineers / specialists to ensure uniform systems. • Representation of DePuy Synthes in the development of tools to prepare the sites for external audits and to continuously evaluate the site's ability to audit • Implement harmonized J & J and MD compliance standards and work instructions • Generation of data necessary for the Dashboard Reviews as well as the support of the site when using the EtQ Audit module• Creation, provision, implementation and maintenance of the internal audit program• Ensures that appropriate audit reports are prepared, verifies and approves the feedback, communicates relevant issues, as well as appropriate monitoring and trend analysis. • Training of quality system auditors and assistants to ensure that there is an appropriate control mechanism and that it is continuously optimized and adapted to the regulatory environment• Front room / Back room support during external audits
-
-
-
Johnson & Johnson
-
United States
-
Hospitals and Health Care
-
700 & Above Employee
-
Senior Compliance Specialist
-
Sep 2016 - Oct 2019
• Responsible for compliance according to the compliance requirements of all local, national, international and company regulations, guidelines and procedures for the local implementation of the quality system • Ensure that quality measures are carried out, all internal and external audit deviations are examined, the root cause analysis of failures is carried out, action plans are completed and appropriate effectiveness checks are carried out independently according to the agreed timetables• Contribute to improvement measures resulting from non-conformities, internal audits, quality board topics and other system indicators• Collaborate with other site compliance engineers / specialists to ensure uniform systems. • Representation of DePuy Synthes in the development of tools to prepare the sites for external audits and to continuously evaluate the site's ability to audit • Implement harmonized J & J and MD compliance standards and work instructions • Generation of data necessary for the Dashboard Reviews as well as the support of the site when using the EtQ Audit module• Creation, provision, implementation and maintenance of the internal audit program• Ensures that appropriate audit reports are prepared, verifies and approves the feedback, communicates relevant issues, as well as appropriate monitoring and trend analysis. • Training of quality system auditors and assistants to ensure that there is an appropriate control mechanism and that it is continuously optimized and adapted to the regulatory environment• Front room / Back room support during external audits
-
-
-
-
Head Quality Assurance at maxon motor medical ag
-
2014 - 2016
• Head of Quality Assurance department with four employees and succession teams• Securance and development of quality within the medical business unit (BU) according to ISO 13485, ISO 9001• Member of the BU leadership team• Assessment of customer complaints• Auditing of ISO 13485• Supplier support including supplier qualification• Expansion of specific professional knowhow• Planning and securing ISO certification and customer audits• Responsible for training schedule and implementation• Formulation and implementation of idea management• Risk management
-
-
-
-
Head of Quality Management at LEONI Studer Hard AG, Däniken
-
2009 - 2016
• Integration and maintenance of quality management systems at LEONI Studer Hard AG• Responsible for the continued development of a quality system with emphasis on a system that is efficient, process-oriented and economic, bearing in mind the cost / benefits according to 21 CFR 820 / ISO 13485, ISO 9001• Professional and personal leadership of direct reports• Scheduling and implementation of periodic quality training• Responsible for scheduling and implementing non conformities, detection and deviation reporting systems up to and including completion (CAPA)• Ensure the necessary requirements are met to obtain cost optimal quality objectives• Responsible for the review of the implementation of quality policy• Preparation and planning of the quality objectives, policies and management report. Reporting to the Executive Committee and Board• Run and monitor (actuality check) of all relevant company standards• Technical support for the product manager, the production manager and the project manager for elimination of damage and/or process optimization• Responsible for the clearing within the capacity as delegate to the technical director of pharmaceutical products• Responsible for the coordination of quality checks with the departments as well as further development of the instructions, changes, deviation reporting and test equipment monitoring according to 21 CFR 820 / ISO 13485•Planning and coordination of the action plan for the periodic review of the quality system as well as for external audits (customers and suppliers regulatory). • Planning and implementation of internal audits according to 21 CFR 820 / ISO 13485 and coordination of the action plan. Motivation and integration of the relevant areas for a resolution on system enhancements
-
-
-
-
European Quality Manager at Synergy Health AG
-
2013 - 2014
• Coordination of global documentation for local quality management systems at the following sites: France, Netherlands, Germany and Switzerland• Auditing at the two German sites • Coordination of global documentation for local quality management systems at the following sites: France, Netherlands, Germany and Switzerland• Auditing at the two German sites
-
-
-
-
Head of filling and packaging
-
2006 - 2009
• Responsible for GMP-compatible filling and packaging of the Spirig Pharma AG product range • Direct management of 17 employees, including their advancement, evaluation and assessment • Planning the filling and packaging processes• Work preparation for equipment and employees• Preparation of work shifts, holidays and work schedules• Monitoring production documentation• Preparation of master batch records and specifications• Responsible for complaints including contact with the supplier• Evaluation of new technologies within packaging
-
-
-
-
Validation / Planning Manager of pharmaceutical production
-
2000 - 2006
• Create and perform all validation activities within pharmaceutical production• Create associated documents• Monitoring and creation of GMP documentation• Coordinating the departments involved• Create and execute projects• Creation of the medium-term sales volumes (3 year planning) into the master plan. Productivity considerations and activation of project work on new investments or changes in production process• Check correspondence of stocks between SAP and Master plan• Determine and check the production/sales/stock quantities• Creation of monthly sales report / production planningAdditional tasks:• Creation and implementation of GMP compliant documentation and employee training• ISO 9001 / 2000 company certification with all associated procedures and processes in accordance with the ISO standards• Creation, introduction and training of staff within the change control system• Implementation of internal and external audits• Monitoring the compliance measures resulting from the audit pending tasks• System support and organization of the company quality management system• Creation of internal policies to meet regulatory requirements• Deputy Director of the company ambulance
-
-
-
-
CAPA Manager, Validation Manager and Planning- and Validation Manager of pharmaceutical Production
-
2000 - 2006
CAPA Manager • Introduction and maintenance of the system responsible for processing, evaluation, documentation and reporting of deviations "Exceptions".• Enhancement, development and improvement of CAPA management• Issuing internal policies and procedures for the analysis of Exceptions • Internal department for all questions and definitions of exceptions, for the regulation of the evaluation and the establishment of measures• Monitoring the investigations of concerning substantive and scheduling of objectives and taking any necessary measures• Lead the management review meeting, suggest performance indicators and measures based on the CAPA evaluation• Point of contact for the Group office relating to CAPA Management, Investigation Board and Management Review BoardValidation Manager• Coordination of all validation activities within the company• Creating, updating and sustaining the validation master plan according to ISO 13485 9001 and 21CFR, GMP• Monitoring and control of the validation plans and reports • Create or participate in writing validation/qualification plans and reports• Checking the change control system• Project management: creating, organisation, performance and implementation
-
-
-
-
Lab assistant in the field of galenics development
-
1998 - 2000
• Creation of master production records (MPR)• Creation of the valuation pages with quantity calculations (BPRs) • Order and dispensing of active ingredients and auxiliary substances including empty capsules• Manufacturing of pharmaceutical composite• Sampling and organisation for the introduction of patterns in the quality control laboratory• Inventory management of raw materials in stock by monitoring of shelf live (Expiration-and, test date)• Monitoring compliance with the safeguards for employees and products• Creating laboratory standards (SOPs)• Participation in the evaluation of new technologies and machines and their qualification• Substitute the Equipment responsibility• Delegate in the management of the logbooks, which included the weekly or monthly control of the logbooks, the storage of old logbooks and creating new logbooks
-
-
-
Novartis
-
Switzerland
-
Pharmaceutical Manufacturing
-
700 & Above Employee
-
Associate validation galenics forms at Ciba Geigy / Novartis
-
1986 - 1998
• Scheduling, organisation, and reporting of cleaning and process validation• Preparation of cleaning SOP• Preparation of the validation plan• Organization and support of the staff in the validation skills• Instruction and monitoring of staff in the context of validation implementation• Evaluation and preparation of validation reports• Data and problem analyses• Implementation of data and problem analyses relating to the preparation and evaluation of validation, as well as on operational improvements and equipment procurement• Performance of Qualification IQ,OQ,PQ• Implementation and documentation of qualifications
-
-
Education
-
Ciba Geigy Schweizerhalle
Chemikantin, - -
Ciba Geigy Schweizerhalle
Chemikantin, 5.4
Community
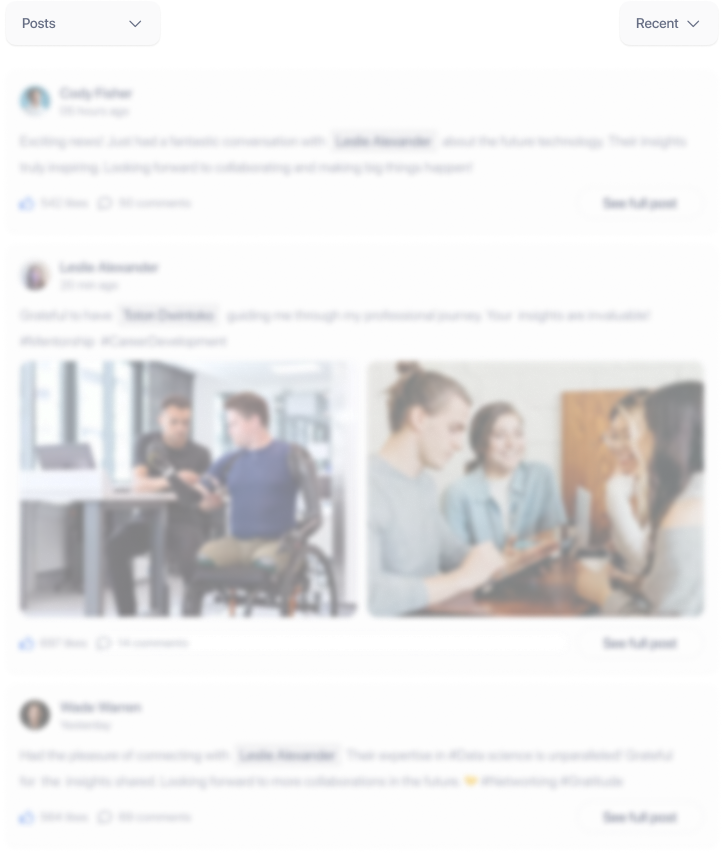