Ryan Paplow
Director Of Innovation at Structural Composites, Inc.- Claim this Profile
Click to upgrade to our gold package
for the full feature experience.
Topline Score
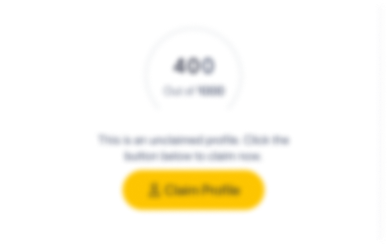
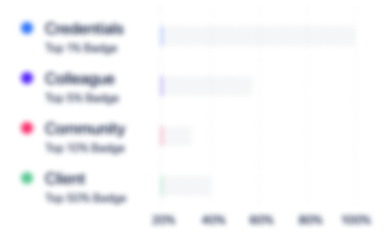
Bio


Experience
-
Structural Composites, Inc.
-
United States
-
Engineering Services
-
1 - 100 Employee
-
Director Of Innovation
-
Nov 2021 - Present
Melbourne, Florida, United States Research, develop and execute initiatives for advanced materials, processes and related technologies. Manage budgets, schedules and resources required to carry out advanced material initiatives. Mentor early workforce engineering and business resources to strengthen the bench strength of operations. Develop and execute policies and procedures for materials lab and quality assurance operations.
-
-
-
Lockheed Martin
-
United States
-
Defense and Space Manufacturing
-
700 & Above Employee
-
Staff Mechanical Engineer
-
Mar 2013 - Nov 2021
Riviera Beach, FL Established a track record of providing informed and consistent technical mentoring, leadership and subject matter expert consultancy for complex vehicle systems for design programs, white papers, and large scale proposal base-lining. Combined years of diverse experience provides optimal solutions to challenges in existing vehicle operations, troubleshooting, and new designs. Accomplishments Held vehicle design leadership positions including: Interim Chief Engineer, IPT Lead… Show more Established a track record of providing informed and consistent technical mentoring, leadership and subject matter expert consultancy for complex vehicle systems for design programs, white papers, and large scale proposal base-lining. Combined years of diverse experience provides optimal solutions to challenges in existing vehicle operations, troubleshooting, and new designs. Accomplishments Held vehicle design leadership positions including: Interim Chief Engineer, IPT Lead, Vehicle-Level-Design Consultant, and Mentor for large-scale autonomous under-water vehicles (AUVs) with advanced technologies. Development, design, testing, and consultation of advanced materials, including: Additive Composite Hybrid External Pressure Vessel, composite Variable Ballast System components, and proper usage of advanced composites on the large-scale AUV programs utilizing emerging technologies. Led a design team to develop array handling systems for manned submarines. Successfully demonstrated and a developed dynamic delivery system for long chain polymers that resulted in 40% sub-sea surface drag reduction. Led a design team for a 1.5 MW tidal turbine program to design under-sea electronic packaging. Led a team that improved Hydraulics Reliability and System Operational Availability for host vessel Integration with aggressive schedules and budget and reduced down-time from weeks to hours. Designed and executed test programs to quantify hypotheses and concepts across multiple programs that included supervision, design and execution of a water-proofness test program for the Power & Data Unit box used on the ORION space flight capsule that successfully simulated splash-down pre-recovery with thermal shock phenomenon. Received multiple company awards including 2 Special Recognition Awards, a SPOT Award, 12 Kudos awards, 2 Spotlight awards, and 2 Thanks awards. Show less
-
-
-
EDF, Inc.
-
United States
-
Aviation & Aerospace
-
1 - 100 Employee
-
Project Engineer
-
Jun 2010 - Mar 2013
Riviera Beach, FL Led technology development and test facility design initiatives for aerospace clients overseeing activities of up to five technical team members sub-contractors at a time. Performed as lead structural and flow analyst for multiple projects, controlled budgets and schedules, and mentored team members . Accomplishments Led the development of a certification test rig for corrosion susceptibility testing for the NAVAIR heavy lift helicopters. Obtained SME designation for process… Show more Led technology development and test facility design initiatives for aerospace clients overseeing activities of up to five technical team members sub-contractors at a time. Performed as lead structural and flow analyst for multiple projects, controlled budgets and schedules, and mentored team members . Accomplishments Led the development of a certification test rig for corrosion susceptibility testing for the NAVAIR heavy lift helicopters. Obtained SME designation for process systems and equipment; managed team members, budget, schedule, sub-contractors, requirements, and stakeholders; developed equipment specifications; and delivered the technical data package. Performed, led, and managed structural analysis for multiple projects including large diameter airflow straightening ducts for commercial turbofan engines, structural members in aerospace test facilities, and aircraft engine transports. Performed, led, and managed thermal flow analysis for hush house upgrades to validate the operation of the facility when the Republic of Singapore Air Force fleet upgraded to Boeing F-15SG aircraft. Detailed analysis of pressures, temperatures, bypass airflow conditions, the effects of thermal/flow equipped porous media, weather conditions, etc. Acoustic and flow data were collected at US based Boeing Hush-House facilities to correlate flow and acoustic models in order to properly project performance data for the upgraded facility. Made formal presentation at the 86th Turbine Engine Test Working Group, Arnold AFB (TETWoG). Oversaw proposal development for a $150M+ engine development facility in Brazil; a $5M+ Multi-Drive regenerative test facility in India; a $2M+, altitude chamber testing facility in Turkey; and a $3.5M+ Multi-Drive test facility for the U.S. Coast Guard. Show less
-
-
-
Lockheed Martin
-
United States
-
Defense and Space Manufacturing
-
700 & Above Employee
-
Contract Sr. Design Engineer
-
May 2008 - Apr 2010
Riviera Beach, FL Performed fluid dynamic resistance and powering studies to determine naval architecture of conceptual UAV designs. These studies included multiple power plant options for evaluation and selection including: turbine, micro-turbine gen-sets, diesel prime mover, diesel gen-sets, and hybrid power options for dive capability in the mission duration. These studies were compiled to calculate vehicle parameters such as fuel storage, battery storage, power-plant volumetric requirements, etc. Created… Show more Performed fluid dynamic resistance and powering studies to determine naval architecture of conceptual UAV designs. These studies included multiple power plant options for evaluation and selection including: turbine, micro-turbine gen-sets, diesel prime mover, diesel gen-sets, and hybrid power options for dive capability in the mission duration. These studies were compiled to calculate vehicle parameters such as fuel storage, battery storage, power-plant volumetric requirements, etc. Created 3-dimensional geometry in to create multiple detailed sub-system and design arrangements. Performed stress/strain studies on multiple components in support of Ultra-Light Structures development for use in the Littoral Combat Ship. Design included kinematic studies of Littoral Combat Ship Remote Multi-Mission Vehicle capture spine. The studies were performed with physics based models to approximate accelerations, forces and moments in various sea states derived from the Littoral Combat Ship’s sea keeping report. Authored Basis of Estimate (BoE) documents while coordinating proposals for shipboard launch & recovery systems and composite structures for the Littoral Combat Ship (LCS) program. Designed and analyzed a deep-sea, pressure compensated, oil-filled power module for an array body capable of reaching 20,000 ft below sea level. ncluded pressure compatible battery selection, sub-sea pressure compensation calculations, gasket seal calculations/selection, and management of procurement. Designed test rig, pressure vessel, electronics packaging, component placement around the test rig, buoyancy calculations for use with the Sonar Data Collection System . The test rig was designed for technology verification in the development of the MARLIN exploration vehicle. Performed forced vibration analysis to lead to a successful design of a series of brackets for vibration testing of components for implementation in the development of the MARLIN exploration vehicle. Show less
-
-
-
-
Engineer/Designer
-
Apr 1992 - Jun 2008
Misc Oversaw air-frame integration of components in the U.S. Air Force Special Operations Command’s (AFSOC) fleet of MC-130s; served as the Lead Instructor of mechanical design at a secondary educational institution; designed mechanical, structural and cryogenic systems for Pratt & Whitney aircraft test facilities; supported rocket test facilities including the design of vacuum chamber components & cryogenic supply systems; integrated hydraulics into railroad service vehicles, agricultural equipment… Show more Oversaw air-frame integration of components in the U.S. Air Force Special Operations Command’s (AFSOC) fleet of MC-130s; served as the Lead Instructor of mechanical design at a secondary educational institution; designed mechanical, structural and cryogenic systems for Pratt & Whitney aircraft test facilities; supported rocket test facilities including the design of vacuum chamber components & cryogenic supply systems; integrated hydraulics into railroad service vehicles, agricultural equipment and mining equipment. Show less
-
-
-
-
Engineer/Designer
-
Apr 1992 - Jun 2008
Misc Designed a personnel hoisting system to ANSI A10.4 standards; created conceptual design of a modular, portable coal processing bio refinery; devised a mechanism that simulated flight conditions from the control room of a test facility of the U.S. Navy's single and double rotor-wing aircraft; created patent drawings and advised in the creation of the patent documentation; designed multi-cavity, mechanically and hydraulically actuated semi-solid (thixo) injection molds.
-
-
Education
-
Old Dominion University
BS, Engineering Technology -
Northwest Iowa Community College
Associates of Science Degree, Mechanical Engineering Technology -
Sibley-Ocheyedan High
Diploma, High School
Community
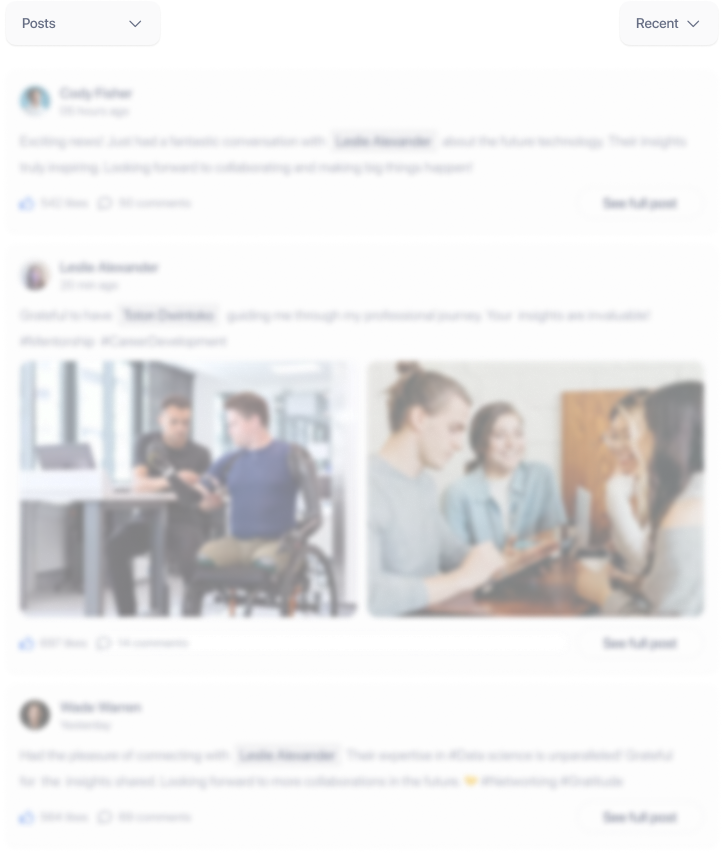