
Rutuja Raut
Manufacturing Process Engineer at NeoTherma Oncology- Claim this Profile
Click to upgrade to our gold package
for the full feature experience.
-
English -
-
Hindi -
Topline Score
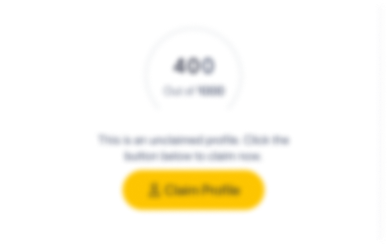
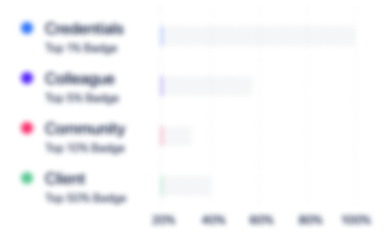
Bio

Jeff Scott
I was Rutuja's immediate supervisor at Solidoodle. Rutuja has a strong background in both Mechanical Engineering and Industrial Engineering which allowed her to hit the ground running and to make an immediate impact upon her arrival. During her tenure at Solidoodle Rutuja conducted time studies of all production areas, updated and developed station to station work instructions and assisted me in developing and implementing tool control per station within the facility. These efforts resulted in labor savings and in a reduction of steps that allowed us to divert the labor saved to accommodate increased production coming into the company through orders. Rutuja also developed a matrix and time study whereby we were able to plan and predict the printed parts needed without over producing or under producing those parts. Prior to her engagement in the area the shop floor had traditionally encountered overages and shortages that would slow or stop the line for hours at a time resulting in production delays and missed shipping schedules weekly. Rutuja’s efforts allowed us to plan the correct parts for the correct models being assembled and allowed the time lost to be regained in the form of production and completed shipping schedules. Rutuja was also responsible for our quality control and quality management area. Upon her arrival at Solidoodle our printed part output was seeing high reject rates. Rutuja assisted in the coordination of a preventive maintenance program with our repair team that tracked our PM and enabled us to reduce the reject rate to just over three percent resulting in both time and materials savings. Additionally, Rutuja coordinated the repair and retune program for customers returning their units for repair, retune or service. Rutuja oversaw the reduction of the backlog of repairs and retunes from three months to a turnaround of seventy two hours while coordinating with Customer Service to provide timely information on the return of their unit. I would recommend Rutuja for any position where an organization’s needs are similar to those listed above. She is highly adaptable and works very well with all departments and with all team members.

Frank J. Freda
Rutuja was a key addition to our management team and she was instrumental in improving our production efficiency. Rutuja performed time studies, put quality assurance testing procedures in place and completely overhauled our repair process. Her efforts directly improved the quality of our products and reduced the number of hardware issues our customers experienced. Additionally, Rutuja was a great influence on others and helped to make the production floor an efficient and fun place to work. I would welcome the opportunity to work with Rutuja again and highly recommend her.

Jeff Scott
I was Rutuja's immediate supervisor at Solidoodle. Rutuja has a strong background in both Mechanical Engineering and Industrial Engineering which allowed her to hit the ground running and to make an immediate impact upon her arrival. During her tenure at Solidoodle Rutuja conducted time studies of all production areas, updated and developed station to station work instructions and assisted me in developing and implementing tool control per station within the facility. These efforts resulted in labor savings and in a reduction of steps that allowed us to divert the labor saved to accommodate increased production coming into the company through orders. Rutuja also developed a matrix and time study whereby we were able to plan and predict the printed parts needed without over producing or under producing those parts. Prior to her engagement in the area the shop floor had traditionally encountered overages and shortages that would slow or stop the line for hours at a time resulting in production delays and missed shipping schedules weekly. Rutuja’s efforts allowed us to plan the correct parts for the correct models being assembled and allowed the time lost to be regained in the form of production and completed shipping schedules. Rutuja was also responsible for our quality control and quality management area. Upon her arrival at Solidoodle our printed part output was seeing high reject rates. Rutuja assisted in the coordination of a preventive maintenance program with our repair team that tracked our PM and enabled us to reduce the reject rate to just over three percent resulting in both time and materials savings. Additionally, Rutuja coordinated the repair and retune program for customers returning their units for repair, retune or service. Rutuja oversaw the reduction of the backlog of repairs and retunes from three months to a turnaround of seventy two hours while coordinating with Customer Service to provide timely information on the return of their unit. I would recommend Rutuja for any position where an organization’s needs are similar to those listed above. She is highly adaptable and works very well with all departments and with all team members.

Frank J. Freda
Rutuja was a key addition to our management team and she was instrumental in improving our production efficiency. Rutuja performed time studies, put quality assurance testing procedures in place and completely overhauled our repair process. Her efforts directly improved the quality of our products and reduced the number of hardware issues our customers experienced. Additionally, Rutuja was a great influence on others and helped to make the production floor an efficient and fun place to work. I would welcome the opportunity to work with Rutuja again and highly recommend her.

Jeff Scott
I was Rutuja's immediate supervisor at Solidoodle. Rutuja has a strong background in both Mechanical Engineering and Industrial Engineering which allowed her to hit the ground running and to make an immediate impact upon her arrival. During her tenure at Solidoodle Rutuja conducted time studies of all production areas, updated and developed station to station work instructions and assisted me in developing and implementing tool control per station within the facility. These efforts resulted in labor savings and in a reduction of steps that allowed us to divert the labor saved to accommodate increased production coming into the company through orders. Rutuja also developed a matrix and time study whereby we were able to plan and predict the printed parts needed without over producing or under producing those parts. Prior to her engagement in the area the shop floor had traditionally encountered overages and shortages that would slow or stop the line for hours at a time resulting in production delays and missed shipping schedules weekly. Rutuja’s efforts allowed us to plan the correct parts for the correct models being assembled and allowed the time lost to be regained in the form of production and completed shipping schedules. Rutuja was also responsible for our quality control and quality management area. Upon her arrival at Solidoodle our printed part output was seeing high reject rates. Rutuja assisted in the coordination of a preventive maintenance program with our repair team that tracked our PM and enabled us to reduce the reject rate to just over three percent resulting in both time and materials savings. Additionally, Rutuja coordinated the repair and retune program for customers returning their units for repair, retune or service. Rutuja oversaw the reduction of the backlog of repairs and retunes from three months to a turnaround of seventy two hours while coordinating with Customer Service to provide timely information on the return of their unit. I would recommend Rutuja for any position where an organization’s needs are similar to those listed above. She is highly adaptable and works very well with all departments and with all team members.

Frank J. Freda
Rutuja was a key addition to our management team and she was instrumental in improving our production efficiency. Rutuja performed time studies, put quality assurance testing procedures in place and completely overhauled our repair process. Her efforts directly improved the quality of our products and reduced the number of hardware issues our customers experienced. Additionally, Rutuja was a great influence on others and helped to make the production floor an efficient and fun place to work. I would welcome the opportunity to work with Rutuja again and highly recommend her.

Jeff Scott
I was Rutuja's immediate supervisor at Solidoodle. Rutuja has a strong background in both Mechanical Engineering and Industrial Engineering which allowed her to hit the ground running and to make an immediate impact upon her arrival. During her tenure at Solidoodle Rutuja conducted time studies of all production areas, updated and developed station to station work instructions and assisted me in developing and implementing tool control per station within the facility. These efforts resulted in labor savings and in a reduction of steps that allowed us to divert the labor saved to accommodate increased production coming into the company through orders. Rutuja also developed a matrix and time study whereby we were able to plan and predict the printed parts needed without over producing or under producing those parts. Prior to her engagement in the area the shop floor had traditionally encountered overages and shortages that would slow or stop the line for hours at a time resulting in production delays and missed shipping schedules weekly. Rutuja’s efforts allowed us to plan the correct parts for the correct models being assembled and allowed the time lost to be regained in the form of production and completed shipping schedules. Rutuja was also responsible for our quality control and quality management area. Upon her arrival at Solidoodle our printed part output was seeing high reject rates. Rutuja assisted in the coordination of a preventive maintenance program with our repair team that tracked our PM and enabled us to reduce the reject rate to just over three percent resulting in both time and materials savings. Additionally, Rutuja coordinated the repair and retune program for customers returning their units for repair, retune or service. Rutuja oversaw the reduction of the backlog of repairs and retunes from three months to a turnaround of seventy two hours while coordinating with Customer Service to provide timely information on the return of their unit. I would recommend Rutuja for any position where an organization’s needs are similar to those listed above. She is highly adaptable and works very well with all departments and with all team members.

Frank J. Freda
Rutuja was a key addition to our management team and she was instrumental in improving our production efficiency. Rutuja performed time studies, put quality assurance testing procedures in place and completely overhauled our repair process. Her efforts directly improved the quality of our products and reduced the number of hardware issues our customers experienced. Additionally, Rutuja was a great influence on others and helped to make the production floor an efficient and fun place to work. I would welcome the opportunity to work with Rutuja again and highly recommend her.

Credentials
-
Power BI Essential Training
LinkedInOct, 2020- Oct, 2024 -
Six Sigma Yellow Belt
Harley-Davidson Motor CompanyMay, 2017- Oct, 2024
Experience
-
NeoTherma Oncology
-
Biotechnology Research
-
1 - 100 Employee
-
Manufacturing Process Engineer
-
Dec 2019 - Present
• Lead inventory management and prototype manufacturing of Class II medical device. • Develop work instructions, Factory Acceptance Tests (FAT), Site Acceptance Tests (SAT) for Quality Measurement Systems. • Perform iterations of prototype assembly to assess product performance, functionality, and manufacturability. • Develop Instructions for Use (IFU) and training manuals for clinicians and MRI technical team for use of the medical device.• Create training plan and provide onsite product training for FDA approved clinical trials and animal studies.• Lead site equipment installations and execute device setup plans at multiple medical research facilities. • Assess and acquire vendors for outsourcing machined parts required for the device and system racks.
-
-
-
Harley-Davidson Motor Company
-
United States
-
Motor Vehicle Manufacturing
-
700 & Above Employee
-
Manufacturing Engineer
-
Jan 2017 - May 2019
• Lead process engineer for wheels and powertrain assembly.• Evaluate & manage labor requirements for changing throughput and schedule fulfilment by using the EASE Line Balancing.• Develop standard work procedures, execute job safety risk assessment; evaluate ergonomic job measurement system, designprocess flow and floor layout, authorize process change notices and product deviation notices.• Track and improve performance metrics such as safety, quality, delivery, cost, sustainability of different areas in the plant in compliance to ISO/TS 16949 and ISO 9001 using APQP, MSA, SPC and other CI tools and techniques.• Lead model year launch for new product introductions (NPIs), BOM changes and manage cross-departmental projects.• Develop PM schedules and TPM to improve overall equipment effectiveness of assembly equipment. Provide technical supportand troubleshoot manufacturing equipment for daily production activities.• Develop control plans after conducting PFMEA Analysis for assembly processes of on-going production and new product launch.• Lead CI activities using the core tools, designing tools and fixtures to eliminate non-conformance identified in internal and external system audits, final vehicle audits and field warranties to improve manufacturing efficiency and first pass yield while reducingbottlenecks.
-
-
Continuous Improvement Engineer
-
Aug 2016 - Dec 2016
• Performed Yamazumi for analyzing assembly processes at workstations throughout the assembly line to identify and eliminate TIMWOOD wastes along with non-value added work and engage operators in following standard work.• Conducted weekly 5S, Layered Process and Work Station Audits to identify issues in daily production activities and provide solutions for counter measures. • Performed Ergo Kaizen event to identify ergonomic risks as per standards of the plant throughout the fabrication department and developed solutions for design changes of racks and carts. • Coordinator of the Red Tag Area for the plant. • Identified and implemented continuous improvement initiatives on production lines to overcome frequent down time and quality issues.
-
-
-
-
Quality Assurance/ Process Improvement Manager
-
Mar 2014 - Jan 2015
• Documented production procedures to ensure accurate assembly processes and timely updates.• Implemented 5S system at each workstation, set boundary samples for assemblies and directed standard production practices that led to increase in overall product quality and labor efficiency throughout the assembly lines. Managed and trained a workforce of 15-20 operators.• Made quality inspection checklist to reduce defects throughout the production lines.• Performed time and motion studies to identify non-value added activities and by using lean manufacturing techniques reduced waste by 75 % and end-to-end production time by 45%.• Performed drop tests and fault analysis on the products, implemented safety designs that contributed to improved end product quality and reduced hardware issues by 95%.• Observed statistical analysis for repairs, created quality assurance testing procedures and preventive maintenance methods for improving productivity. Provided ongoing production support and troubleshooting. Collaborated with engineering, customer service and procurement teams to deliver quality products.• Re engineered production layouts that increased efficiency of the product flow and reduced material travel time and achieved 15% improvement in overall productivity. Implemented necessary material handling systems.• Established a tool inventory control, developed guidelines and procedures for accurate tool usage to reduce overhead cost by 10%.
-
-
-
New York City Industries for the Blind, Inc.
-
United States
-
Civic and Social Organizations
-
Process Engineer Intern
-
Sep 2013 - Dec 2013
• Gathered and analyzed data to develop a detailed catalog of the products’ Bill of Materials (BOMs) with its manufacturing process, machines used for each operation, demands and cycle times, logistics associated with shipments of the raw material and finished goods.• Optimized the factory floor by performing detailed study of the layout and product flow process to identify operational delays and causes of bottleneck and by applying Value Stream Mapping and ABC analysis techniques. The recommended new layout brought down the material travel time by 40%, cycle time of operation by 60% and reduced the work in progress by 35% overall.• Ergonomically redesigned the work space without compromising the comfort of the visually impaired workers. Performed physical simulations to test the solutions.• Studied the demands for previous years to observe the trend of each product and with the help of available data, developed a forecast and the safety stock for minimum inventory; determined and reorganized the inventory to optimize the storage space.• Categorized the products for efficient simultaneous production without increasing the need of resources as of previous processes. Suggested technical solutions for keeping a track of machine down times and improve production efficiency.
-
-
-
D-Shape
-
Italy
-
Environmental Services
-
1 - 100 Employee
-
Industrial Engineer Intern
-
Oct 2012 - Jun 2013
• Worked on the Facility Planning and design of the 3D printer and printing manufacturing plant which consisted of looking out for new locations, inventory management techniques, facility systems and the material handling systems. • Designed various factory floor plans by studying different possible assembly lines for the plant. Project scheduling was done using MS Project. • Worked on the Facility Planning and design of the 3D printer and printing manufacturing plant which consisted of looking out for new locations, inventory management techniques, facility systems and the material handling systems. • Designed various factory floor plans by studying different possible assembly lines for the plant. Project scheduling was done using MS Project.
-
-
Education
-
NYU Tandon School of Engineering
Master's degree, Industrial Engineering -
Harrisburg University of Science and Technology
Master’s Degree, Project Management -
Pune University
Bachelor of Engineering (B.E.), Mechanical Engineering
Community
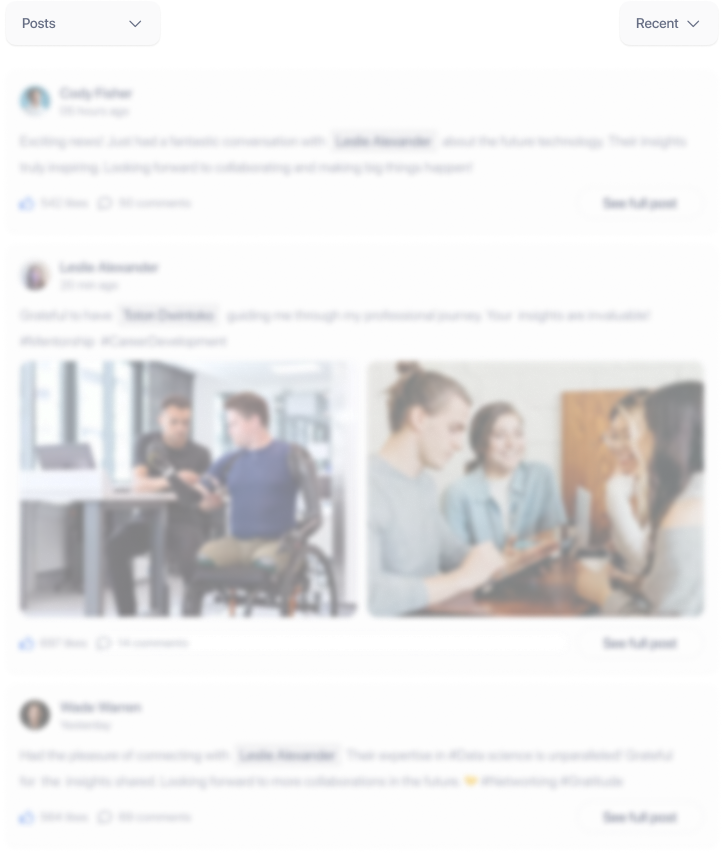