Russell Tacken
Lead WHS Manager at Staughton Group at Staughton Group- Claim this Profile
Click to upgrade to our gold package
for the full feature experience.
Topline Score
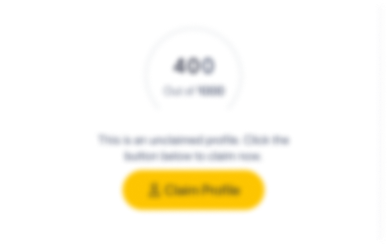
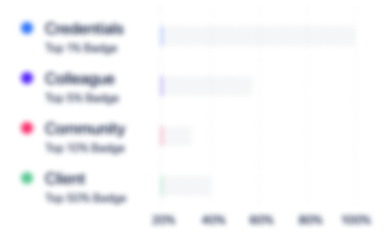
Bio
0
/5.0 / Based on 0 ratingsFilter reviews by:
Experience
-
Staughton Group
-
Australia
-
Food Production
-
1 - 100 Employee
-
Lead WHS Manager at Staughton Group
-
Sep 2020 - Present
-
-
-
Sole Trader_
-
Writing and Editing
-
100 - 200 Employee
-
Health Safety Environment Consultant
-
Mar 2019 - Sep 2020
-
-
-
Green's General Foods
-
Australia
-
Food and Beverage Manufacturing
-
1 - 100 Employee
-
Health, Safety & Environment Manager
-
Sep 2017 - Mar 2019
Responsible for the safety and environment systems, training and workers compensation of corporate office, manufacturing, research and development and logistics operations. Responsible for the safety and environment systems, training and workers compensation of corporate office, manufacturing, research and development and logistics operations.
-
-
-
GrainCorp
-
Australia
-
Food Production
-
700 & Above Employee
-
National Safety Health & Environment Operations Manager
-
Nov 2015 - Mar 2017
Responsible for the development and implementation of the S.H.E system and risk management solutions to meet the grain, road and rail logistics and export operations from Mackay in Qld to Portland in Victoria. Responsible for . Responsible for the development and implementation of the S.H.E system and risk management solutions to meet the grain, road and rail logistics and export operations from Mackay in Qld to Portland in Victoria. Responsible for .
-
-
-
Teys Australia
-
Australia
-
Food Production
-
500 - 600 Employee
-
Workplace Health & Safety Manager
-
Jan 2014 - Nov 2015
Responsible for the safety and environment systems and training, for beef processing, value added, logistics and rendering operations. Responsible for the safety and environment systems and training, for beef processing, value added, logistics and rendering operations.
-
-
-
Essential Energy
-
Australia
-
Utilities
-
700 & Above Employee
-
Regional Safety & Environment Auditor
-
Jan 2011 - Dec 2013
Responsibilities• Implemented and audited the Safety and Environmental Management System (SEMS) for multiple sites across the NSW southern region and Melbourne office. Identified and executed SEMS improvements.• Developed all HSE audit procedures and plans for multiple sites (southern, central and far west NSW and VIC). • Conduced audits on Essential Energy’s procedures and processes of business units and contractors to ensure compliance and to maintain certification to AS/NZS 4801 and AS/NZS ISO 14001.• Mentored and coached the Southern Region Management team and employees in safety and environmental compliance and management, as well as guiding them through transformational change. • Prepared a wide range of reports, including reports for the Board of Directors.• Developed and maintained the SEMS documentation, and coordinated the implementation of policies and procedures across the Essential Energy footprint.• Maintained safety and environment performance standards and accreditation to Australian standards.Achievements• Developed and executed the Essential Energy Waste Management plan.• Coached and mentored the Southern Region Management team and employees to achieve a 15% improvement in environmental management and 12% improvement in health and safety.• Developed, authored and implemented Essential Energy's internal HSE audit program to ensure compliance with procedures and processes, and to meet the requirements and maintain certification of AS/NZS ISO14001 Environment Systems and AS/NZS4801 OHS Systems. • Obtained accreditation to meet AS/NZS14001 Environment Systems for Far West Essential Water.
-
-
National SHE Policy & Compliance Manager
-
Feb 2009 - Dec 2010
-
-
Safety Environment Audit & Investigation Coordinator
-
Sep 2006 - Jan 2009
-
-
-
Bartter Enterprises
-
United States
-
Wholesale
-
1 - 100 Employee
-
Regional OHS Coordinator
-
Dec 2005 - Sep 2006
• Developed Regional Safety Plan which was rolled out nationally. (Bartters).• Developed OHS consultation to educate and mentor OHS Representatives conducting internal audits of procedures. (Bartters).• Implemented manual task risk assessment program to quantify manual handling risks.• Implemented manual handling strategic plan, training program and risk management program for employees and leaders. • Developed Regional Safety Plan which was rolled out nationally. (Bartters).• Developed OHS consultation to educate and mentor OHS Representatives conducting internal audits of procedures. (Bartters).• Implemented manual task risk assessment program to quantify manual handling risks.• Implemented manual handling strategic plan, training program and risk management program for employees and leaders.
-
-
-
-
Safety and Environment Coordinator
-
Jul 2003 - Nov 2005
-
-
-
Private Consultant
-
Financial Services
-
1 - 100 Employee
-
Specialist Safety and Environmental Management Systems Consultant
-
Jul 2001 - Jun 2003
-
-
-
SunRice
-
Pakistan
-
Food & Beverages
-
1 - 100 Employee
-
Safety Health & Environment Manager Northern Region
-
Jan 1998 - Jun 2001
• Developed and successfully implemented a sustainable system of risk management while employed as the Safety Health and Environment Manager – Ricegrowers’ Northern Region, achieving a 63% reduction in lost time incidents over 12 months.• Developed strategy guide to improve leadership and safety management of line managers. A total of 23 of 49 strategies implemented over 12 months at Ricegrowers’ resulted in the reduction of lost time injuries by 20%, companywide. Achieved an unprecedented reduction in the LTIFR by 48% and 63% at the two rice mills under my direct responsibility for OHS systems implementation.• Developed and implemented Safety Leadership program for Managers and Supervisors in the following subjects:- Managers/Supervisors/Employees Commitment and Responsibility.- Regular safety inspections to reduce the instance of unsafe conditions.- Safety behaviour monitoring to reduce the instance of unsafe acts.- Risk management methodology based on AS 4360 Risk Management.- Hazard register to record and track all hazards, risk assessments and compliance with closure.• Review and restructuring of OHS committees.• Hazardous substance management by implementing the “Chemwatch” system.• Contractor induction and contractor controls.• Set quarterly internal audit program to measure Line management targets and compliance based on positive performance measures.
-
-
-
Royal Australian Air Force
-
Armed Forces
-
700 & Above Employee
-
Airfield Defence Guard
-
Mar 1978 - Jun 1997
• Responsible for the operational readiness training for all RAAF personnel in the North Queensland operational area.• Attained the highest non-commissioned rank in the RAAF.• Squadron Occupational Health & Safety Coordinator. • Responsible for the operational readiness training for all RAAF personnel in the North Queensland operational area.• Attained the highest non-commissioned rank in the RAAF.• Squadron Occupational Health & Safety Coordinator.
-
-
Education
-
UNSW Australia
Environmental Science, Environmental Management
Community
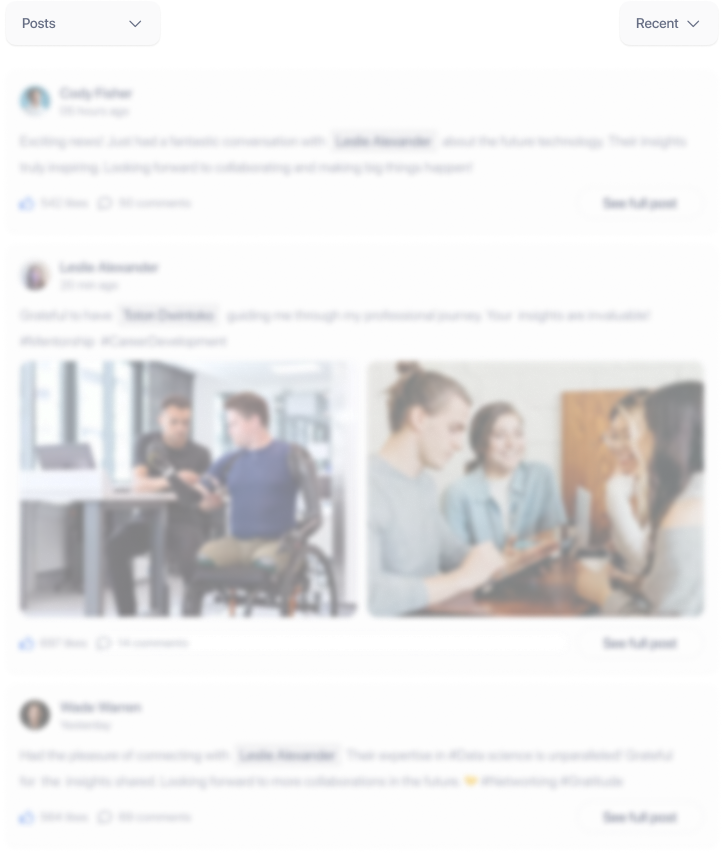