Russell Ellis
Proposal Manager at SCI Technology, Inc.- Claim this Profile
Click to upgrade to our gold package
for the full feature experience.
Topline Score
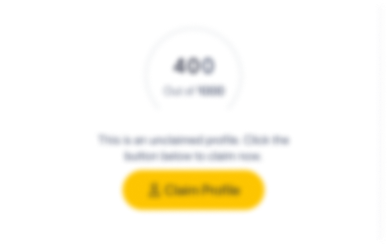
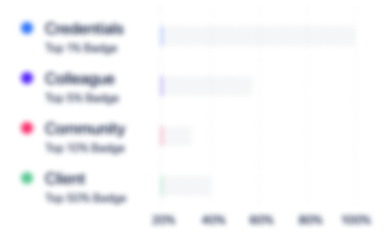
Bio

Benjamin Preston, PMP, MBA
Russell is a team player and is very knowledgeable in the cost analysis field. He has years of experience, is easy to work with, and adds tremendous value to the team.

C V Key
Russell is very work oriented

Benjamin Preston, PMP, MBA
Russell is a team player and is very knowledgeable in the cost analysis field. He has years of experience, is easy to work with, and adds tremendous value to the team.

C V Key
Russell is very work oriented

Benjamin Preston, PMP, MBA
Russell is a team player and is very knowledgeable in the cost analysis field. He has years of experience, is easy to work with, and adds tremendous value to the team.

C V Key
Russell is very work oriented

Benjamin Preston, PMP, MBA
Russell is a team player and is very knowledgeable in the cost analysis field. He has years of experience, is easy to work with, and adds tremendous value to the team.

C V Key
Russell is very work oriented

Experience
-
SCI Technology, Inc.
-
United States
-
Defense and Space Manufacturing
-
1 - 100 Employee
-
Proposal Manager
-
May 2019 - Present
-
-
-
Yulista Aviation, Inc.
-
United States
-
Defense and Space Manufacturing
-
100 - 200 Employee
-
Cost Analyst
-
Nov 2008 - May 2019
Responsibilities are to interface with internal customers (Program Managers, Project Leads, Production, and Engineering) and Government Tech. lead for Aerospace/Aviation/Defense projects. Duties include analyze project cost incurred, prepare/analyze budgets, track PR’s and PO’s. Develop and maintain funding status monitoring and reporting spreadsheets, CDRLs. Prepare data as requested by PM and customer in timely matter. Identify potential problems from CPR and cost data. Support in the preparation of new business activities and on-going PMR reporting. Review ROMs, OEPs, and other documents verifying FAR and CAS procedures are followed.
-
-
-
-
Owner
-
Jul 1988 - May 2019
Raise registered and non-registered Gelbvieh and Balancer Cattle. Raise registered and non-registered Gelbvieh and Balancer Cattle.
-
-
-
-
CMS/Cost Analyst
-
Jul 2004 - Oct 2008
Responsibilities included working with Suppliers to ensure accurate orders; maintenance of inventory levels and liabilities to ensure procuring at EOQ; communicate daily with Suppliers, program mgr., and finance to achieve max. inventory turns; reporting for quarterly QBR meetings; L/T analysis, Out Source and drive escalations to support Supply Chain. Work closely with contract customers with NPI’s, validations of BOM, tracking PPV. Certified in use of BaaN computer software. Responsibilities included working with Suppliers to ensure accurate orders; maintenance of inventory levels and liabilities to ensure procuring at EOQ; communicate daily with Suppliers, program mgr., and finance to achieve max. inventory turns; reporting for quarterly QBR meetings; L/T analysis, Out Source and drive escalations to support Supply Chain. Work closely with contract customers with NPI’s, validations of BOM, tracking PPV. Certified in use of BaaN computer software.
-
-
-
Southern Energy Homes
-
United States
-
Wholesale
-
1 - 100 Employee
-
Assistant Controller
-
Jun 2000 - Jul 2004
Establish and maintain the product specifications, bill-of-materials, production processes and cost in a P.C. network system (J.D. Edwards’s software). Developed a new configuration of product layout in the computer system. Develop various methods and tools to control inventory. Assist in developing systems of assurance in financial reporting for auditing compliance, productivity improvements, expense savings and quality improvements. Produce cost and performance reports. Assist the Controller with month-end closing
-
-
-
-
Purchasing Dir,/Plant Mgr./Cost & Eng.
-
Nov 1978 - Apr 2000
Established and maintained the product specifications, bill-of-materials, production processes and cost. Produced reports using Activity-based costing (ABC) and direct labor methods. Outsourced machinery and raw materials. As Director negotiated and purchased all raw materials and maintenance products. Operated with very low J-I-T inventory. Developed numerous productivity improvements, expense savings, quality improvements, and a broad range of efficient and reliable suppliers. Controlled materials for GSA contracts to meet both customer and supplier schedules.Established and maintained product cost for goods manufactured. Set and monitored quality control standards, efficiency, labor cost, product development, generated quotes, material yields, feasibility studies, component testing, and inventory controls.Administered the manufacturing of various types of furniture. Scheduled and supervised all phases of manufacturing, during a 100% increase in production. Established a 5% reduction in direct labor. This facility had as many as 170 associates employed.
-
-
Education
-
Athens State University
Bachelor of Science (BS), Accounting and Business/Management -
George C Wallace State Community College-Hanceville
Associate's degree, Business Administration, Management and Operations -
Meek High School
-
Meek High School
-
Meek High School
Community
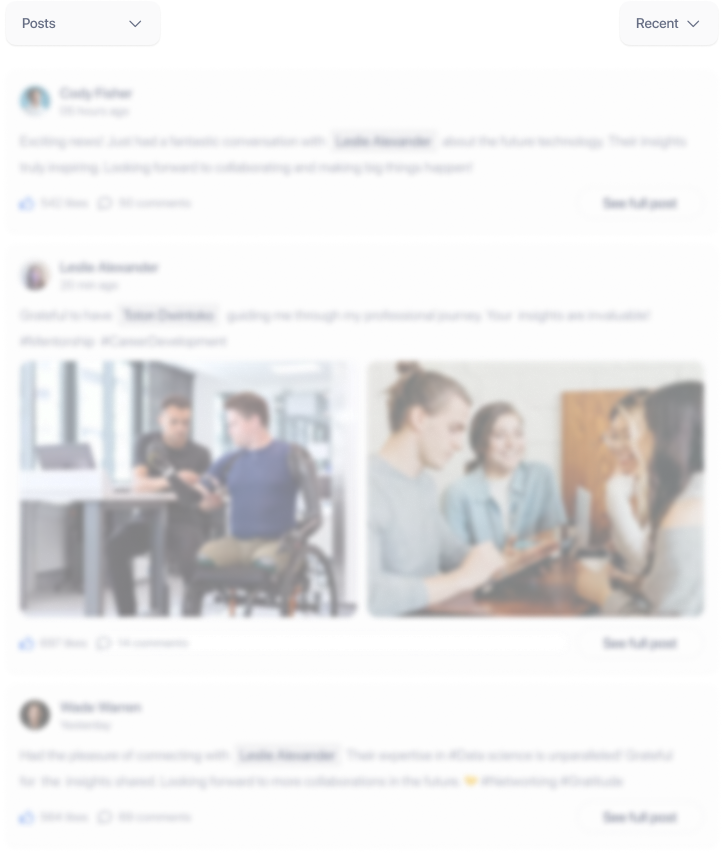