Randall Sheckler
Director Of Quality at Aero Components LLC- Claim this Profile
Click to upgrade to our gold package
for the full feature experience.
Topline Score
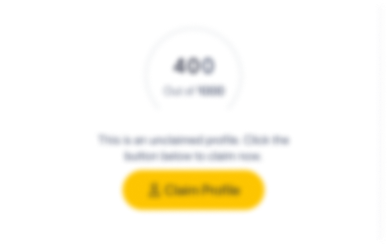
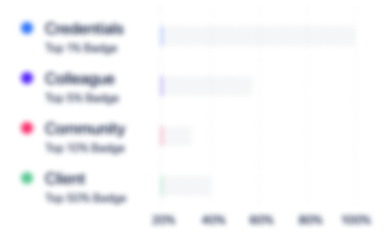
Bio

Lauren B.
Randy is an extremely sharp and charismatic leader with the ability to command the attention of a group unlike any I have ever seen. His extreme work ethic and precise attention to detail made him an invaluable asset to our Product team at Stance. Randy was always a complete pleasure to work with and could be counted on to make unique and substantive contributions to any meeting he was included in. He has the ability to clearly articulate the issue at hand and offer solutions that are driven by data and company goals. Any organization would be lucky to have Randy on board.

Lauren B.
Randy is an extremely sharp and charismatic leader with the ability to command the attention of a group unlike any I have ever seen. His extreme work ethic and precise attention to detail made him an invaluable asset to our Product team at Stance. Randy was always a complete pleasure to work with and could be counted on to make unique and substantive contributions to any meeting he was included in. He has the ability to clearly articulate the issue at hand and offer solutions that are driven by data and company goals. Any organization would be lucky to have Randy on board.

Lauren B.
Randy is an extremely sharp and charismatic leader with the ability to command the attention of a group unlike any I have ever seen. His extreme work ethic and precise attention to detail made him an invaluable asset to our Product team at Stance. Randy was always a complete pleasure to work with and could be counted on to make unique and substantive contributions to any meeting he was included in. He has the ability to clearly articulate the issue at hand and offer solutions that are driven by data and company goals. Any organization would be lucky to have Randy on board.

Lauren B.
Randy is an extremely sharp and charismatic leader with the ability to command the attention of a group unlike any I have ever seen. His extreme work ethic and precise attention to detail made him an invaluable asset to our Product team at Stance. Randy was always a complete pleasure to work with and could be counted on to make unique and substantive contributions to any meeting he was included in. He has the ability to clearly articulate the issue at hand and offer solutions that are driven by data and company goals. Any organization would be lucky to have Randy on board.

Credentials
-
Diversity, Inclusion, and Belonging
National Association of State Boards of Accountancy (Registry ID: 140940)Sep, 2021- Nov, 2024 -
Excel Supply Chain Analysis: Solving Inventory Problems
LinkedInMar, 2021- Nov, 2024 -
Strategic Thinking
Project Management InstituteJul, 2020- Nov, 2024 -
Lean Foundations
National Association of State Boards of Education (NASBE)May, 2020- Nov, 2024 -
Learning Minitab
LinkedInMay, 2020- Nov, 2024 -
Six Sigma Green Belt (CSSGB)
Project Management InstituteMay, 2020- Nov, 2024 -
Lean Management Certification
Expert Ratings - Global CertificationsSep, 2016- Nov, 2024 -
CPR, AED and Basic First Aid
American Safety & Health InstituteMay, 2016- Nov, 2024 -
Preventing Workplace Harassment for Mandated Managers
emTRAiN Training VerificationDec, 2015- Nov, 2024 -
Certification - Infrared/Thermal Testing (ASNT-NDT3-IR)
Infrared Training CenterFeb, 2014- Nov, 2024
Experience
-
Aero Components LLC
-
United States
-
Aviation and Aerospace Component Manufacturing
-
1 - 100 Employee
-
Director Of Quality
-
Apr 2022 - Present
Establish and deploy a highly effective and comprehensive Quality Management System (QMS) that is certified to NADCAP, AS9100, and OEM-specific quality management systems. • Prepare, obtain, and maintain critical certifications such as NADCAP, AS9100, and all special process certifications for Boeing, Northrop Grumman, and other OEMs. • Guarantee compliance with external customer requirements with a focus on a zero-defects mindset. • Ensure communication with external stakeholders on… Show more Establish and deploy a highly effective and comprehensive Quality Management System (QMS) that is certified to NADCAP, AS9100, and OEM-specific quality management systems. • Prepare, obtain, and maintain critical certifications such as NADCAP, AS9100, and all special process certifications for Boeing, Northrop Grumman, and other OEMs. • Guarantee compliance with external customer requirements with a focus on a zero-defects mindset. • Ensure communication with external stakeholders on all Quality issues that may impact the Site's reputation. • Define training in the management of quality subjects (methods and tools) such as 6S, Lean, 5 Why’s, Fishbone, DMAIC, etc. • Develop continuous improvement plans (CI) based on quantitative data acquisition from the quality metrics (company-wide). • Conduct annual management review meetings (AS9100) with a comprehensive report card for all departments. • Calculate and report cost of poor quality (COPQ) to management quarterly. • Drive root cause and corrective action (RCCA) at every level of the organization with our advanced quality improvement database (QID). Show less Establish and deploy a highly effective and comprehensive Quality Management System (QMS) that is certified to NADCAP, AS9100, and OEM-specific quality management systems. • Prepare, obtain, and maintain critical certifications such as NADCAP, AS9100, and all special process certifications for Boeing, Northrop Grumman, and other OEMs. • Guarantee compliance with external customer requirements with a focus on a zero-defects mindset. • Ensure communication with external stakeholders on… Show more Establish and deploy a highly effective and comprehensive Quality Management System (QMS) that is certified to NADCAP, AS9100, and OEM-specific quality management systems. • Prepare, obtain, and maintain critical certifications such as NADCAP, AS9100, and all special process certifications for Boeing, Northrop Grumman, and other OEMs. • Guarantee compliance with external customer requirements with a focus on a zero-defects mindset. • Ensure communication with external stakeholders on all Quality issues that may impact the Site's reputation. • Define training in the management of quality subjects (methods and tools) such as 6S, Lean, 5 Why’s, Fishbone, DMAIC, etc. • Develop continuous improvement plans (CI) based on quantitative data acquisition from the quality metrics (company-wide). • Conduct annual management review meetings (AS9100) with a comprehensive report card for all departments. • Calculate and report cost of poor quality (COPQ) to management quarterly. • Drive root cause and corrective action (RCCA) at every level of the organization with our advanced quality improvement database (QID). Show less
-
-
-
Planet Innovation
-
Australia
-
Design
-
300 - 400 Employee
-
Vice President Operations
-
Aug 2020 - Jan 2022
Negotiate manufacturing agreements with domestic and international clients. Determine department and division progress toward stated goals and objectives through evaluating costs and forecast data. Maintain effective liaison with commercial clients and received positive client feedback. Facilitate a team of Product Managers in building lucrative client relationships. Execute company’s growth strategy to attain competitive advantages, while promoting planet innovation’s presence within the… Show more Negotiate manufacturing agreements with domestic and international clients. Determine department and division progress toward stated goals and objectives through evaluating costs and forecast data. Maintain effective liaison with commercial clients and received positive client feedback. Facilitate a team of Product Managers in building lucrative client relationships. Execute company’s growth strategy to attain competitive advantages, while promoting planet innovation’s presence within the designated region. • Achieved manufacturing outcomes for complex and high-volume biomedical products through strategic production planning and implementation. Saved the company more than $1 million. • Played an integral role in new business development through implementing strategic measures. Negotiated and closed over $5 million in new manufacturing contracts. • Led the successful establishment of product service and prototype manufacturing capability, including hiring and managing technical staff. • Built positive client feedback through implementing best practices and ensuring workflow compliance with Planet Innovation’s Quality systems. Show less Negotiate manufacturing agreements with domestic and international clients. Determine department and division progress toward stated goals and objectives through evaluating costs and forecast data. Maintain effective liaison with commercial clients and received positive client feedback. Facilitate a team of Product Managers in building lucrative client relationships. Execute company’s growth strategy to attain competitive advantages, while promoting planet innovation’s presence within the… Show more Negotiate manufacturing agreements with domestic and international clients. Determine department and division progress toward stated goals and objectives through evaluating costs and forecast data. Maintain effective liaison with commercial clients and received positive client feedback. Facilitate a team of Product Managers in building lucrative client relationships. Execute company’s growth strategy to attain competitive advantages, while promoting planet innovation’s presence within the designated region. • Achieved manufacturing outcomes for complex and high-volume biomedical products through strategic production planning and implementation. Saved the company more than $1 million. • Played an integral role in new business development through implementing strategic measures. Negotiated and closed over $5 million in new manufacturing contracts. • Led the successful establishment of product service and prototype manufacturing capability, including hiring and managing technical staff. • Built positive client feedback through implementing best practices and ensuring workflow compliance with Planet Innovation’s Quality systems. Show less
-
-
-
Stance
-
United States
-
Apparel & Fashion
-
100 - 200 Employee
-
Director of Global Quality Assurance, Testing, Compliance and Product Education
-
May 2014 - Apr 2020
Stance Inc. 05/2014 – 04/2020 Director: Global Quality Assurance, Testing and Compliance Delivered strategic direction to USA and Asia quality assurance teams tasked with preventing mistakes and defects in manufactured products. Implemented a scalable world-class quality assurance infrastructure and testing laboratory in line with AATCC, ASTM, MSC, JIS, and ISO practices and procedures. Led the seamless implementation of core innovations and technologies, such as… Show more Stance Inc. 05/2014 – 04/2020 Director: Global Quality Assurance, Testing and Compliance Delivered strategic direction to USA and Asia quality assurance teams tasked with preventing mistakes and defects in manufactured products. Implemented a scalable world-class quality assurance infrastructure and testing laboratory in line with AATCC, ASTM, MSC, JIS, and ISO practices and procedures. Led the seamless implementation of core innovations and technologies, such as FEEL360™, ButterBlend™, INFIKNIT™, and the patented Wholester™. • Elevated stance to a premium brand position through establishing product development and quality platform. • Served as a key player in growing stance from $33M to 150M. • Reduced critical defects from 10% to 0.6% within 12 months through building effective quality assurance, control, defect, and compliance manuals. • Drove strategic product improvement through leading the implementation of cost of quality and strategic plans. • Facilitated leadership team in securing over $50M in first and second-round funding. • Achieved consistent compliance to approved quality levels (AQL) through creating standards and a robust five-point inspection system for fit, form, and functions. • Increased AOV (average order value) by 5-8% at retail through implementing a global product education curriculum for over 23 stores. • Drove critical defects down from 10% to .6% within four years, while reducing cost by $1M. • Supported the integration of core innovation features and benefits through executing training techniques. • Achieved 100K+ views with greater than 70% engagement in 24 hours through facilitating digital training and articulating product features and benefits on social platforms. • Drove more than $230,000.00 annual savings in education and training costs through utilizing digital education series. • Produced episodic product marketing videos providing insights on “sales scenarios” used in retail, distribution, and wholesale. Show less Stance Inc. 05/2014 – 04/2020 Director: Global Quality Assurance, Testing and Compliance Delivered strategic direction to USA and Asia quality assurance teams tasked with preventing mistakes and defects in manufactured products. Implemented a scalable world-class quality assurance infrastructure and testing laboratory in line with AATCC, ASTM, MSC, JIS, and ISO practices and procedures. Led the seamless implementation of core innovations and technologies, such as… Show more Stance Inc. 05/2014 – 04/2020 Director: Global Quality Assurance, Testing and Compliance Delivered strategic direction to USA and Asia quality assurance teams tasked with preventing mistakes and defects in manufactured products. Implemented a scalable world-class quality assurance infrastructure and testing laboratory in line with AATCC, ASTM, MSC, JIS, and ISO practices and procedures. Led the seamless implementation of core innovations and technologies, such as FEEL360™, ButterBlend™, INFIKNIT™, and the patented Wholester™. • Elevated stance to a premium brand position through establishing product development and quality platform. • Served as a key player in growing stance from $33M to 150M. • Reduced critical defects from 10% to 0.6% within 12 months through building effective quality assurance, control, defect, and compliance manuals. • Drove strategic product improvement through leading the implementation of cost of quality and strategic plans. • Facilitated leadership team in securing over $50M in first and second-round funding. • Achieved consistent compliance to approved quality levels (AQL) through creating standards and a robust five-point inspection system for fit, form, and functions. • Increased AOV (average order value) by 5-8% at retail through implementing a global product education curriculum for over 23 stores. • Drove critical defects down from 10% to .6% within four years, while reducing cost by $1M. • Supported the integration of core innovation features and benefits through executing training techniques. • Achieved 100K+ views with greater than 70% engagement in 24 hours through facilitating digital training and articulating product features and benefits on social platforms. • Drove more than $230,000.00 annual savings in education and training costs through utilizing digital education series. • Produced episodic product marketing videos providing insights on “sales scenarios” used in retail, distribution, and wholesale. Show less
-
-
-
Sentinel® Offender Services
-
United States
-
Public Safety
-
100 - 200 Employee
-
VP Operations
-
Jun 2013 - Jan 2014
Oversaw the management of high-value budget worth over$10M for training, warehouse management, equipment services, and monitoring. • Elevated business growth to over $15M through promoting focused products and increasing global distribution. • Suggested engineering solutions to multiple technical design flaws on focused products (Radio Frequency and Global Positioning Systems) that drove over $500K in savings. • Drove operational excellence through implementing operating unit’s… Show more Oversaw the management of high-value budget worth over$10M for training, warehouse management, equipment services, and monitoring. • Elevated business growth to over $15M through promoting focused products and increasing global distribution. • Suggested engineering solutions to multiple technical design flaws on focused products (Radio Frequency and Global Positioning Systems) that drove over $500K in savings. • Drove operational excellence through implementing operating unit’s policies and procedures, enforcing compliance, and mitigating risks. • Produced cost savings up to $1M through streamlining critical operations and improving supply chains. Show less Oversaw the management of high-value budget worth over$10M for training, warehouse management, equipment services, and monitoring. • Elevated business growth to over $15M through promoting focused products and increasing global distribution. • Suggested engineering solutions to multiple technical design flaws on focused products (Radio Frequency and Global Positioning Systems) that drove over $500K in savings. • Drove operational excellence through implementing operating unit’s… Show more Oversaw the management of high-value budget worth over$10M for training, warehouse management, equipment services, and monitoring. • Elevated business growth to over $15M through promoting focused products and increasing global distribution. • Suggested engineering solutions to multiple technical design flaws on focused products (Radio Frequency and Global Positioning Systems) that drove over $500K in savings. • Drove operational excellence through implementing operating unit’s policies and procedures, enforcing compliance, and mitigating risks. • Produced cost savings up to $1M through streamlining critical operations and improving supply chains. Show less
-
-
-
Caliber Electronics Inc.
-
San Clemente, California
-
Founder and Chief Quality Officer (Business was acquired)
-
Jan 1994 - Jun 2013
Led the successful establishment of the company from planning to successful market execution. Supported defect-free production of focused components through building strategic long-term partnerships with six overseas factories. Implemented ISO90001 certification and re-certification within three overseas factories to meet customer and regulatory requirements. • Increased profitability by over 10-15% through negotiating favorable contract terms and conditions. • Reduced costs and… Show more Led the successful establishment of the company from planning to successful market execution. Supported defect-free production of focused components through building strategic long-term partnerships with six overseas factories. Implemented ISO90001 certification and re-certification within three overseas factories to meet customer and regulatory requirements. • Increased profitability by over 10-15% through negotiating favorable contract terms and conditions. • Reduced costs and improved operational efficiency and productivity through implementing MRP, JIT, and other lean manufacturing techniques and systems. • Conceptualized and produced the tightest tolerance frequency controlled timing devices on the market. Additional experience as Director of Quality Assurance and Training, Quality Assurance Manager, and Engineer / Associate Scientist within diversified organizations. Show less Led the successful establishment of the company from planning to successful market execution. Supported defect-free production of focused components through building strategic long-term partnerships with six overseas factories. Implemented ISO90001 certification and re-certification within three overseas factories to meet customer and regulatory requirements. • Increased profitability by over 10-15% through negotiating favorable contract terms and conditions. • Reduced costs and… Show more Led the successful establishment of the company from planning to successful market execution. Supported defect-free production of focused components through building strategic long-term partnerships with six overseas factories. Implemented ISO90001 certification and re-certification within three overseas factories to meet customer and regulatory requirements. • Increased profitability by over 10-15% through negotiating favorable contract terms and conditions. • Reduced costs and improved operational efficiency and productivity through implementing MRP, JIT, and other lean manufacturing techniques and systems. • Conceptualized and produced the tightest tolerance frequency controlled timing devices on the market. Additional experience as Director of Quality Assurance and Training, Quality Assurance Manager, and Engineer / Associate Scientist within diversified organizations. Show less
-
-
-
ILSI
-
United States
-
Appliances, Electrical, and Electronics Manufacturing
-
1 - 100 Employee
-
Director of Quality Assurance and Corporate Training
-
Jan 1992 - Jan 1994
6 direct reports and 65 indirect reports • Authored the company’s first Corporate Quality Control Manual. Streamlined manufacturing and created strategic international supplier relationships that propelled sales from $3 million to $12 million in 2 years • Trained and educated over 60 employees on defect prevention, SPC, root cause analysis technical sales and requirements identification resulting in improved KPI’s in all departments. Responsible for administering all corporate… Show more 6 direct reports and 65 indirect reports • Authored the company’s first Corporate Quality Control Manual. Streamlined manufacturing and created strategic international supplier relationships that propelled sales from $3 million to $12 million in 2 years • Trained and educated over 60 employees on defect prevention, SPC, root cause analysis technical sales and requirements identification resulting in improved KPI’s in all departments. Responsible for administering all corporate presentations to large original equipment manufacturers Show less 6 direct reports and 65 indirect reports • Authored the company’s first Corporate Quality Control Manual. Streamlined manufacturing and created strategic international supplier relationships that propelled sales from $3 million to $12 million in 2 years • Trained and educated over 60 employees on defect prevention, SPC, root cause analysis technical sales and requirements identification resulting in improved KPI’s in all departments. Responsible for administering all corporate… Show more 6 direct reports and 65 indirect reports • Authored the company’s first Corporate Quality Control Manual. Streamlined manufacturing and created strategic international supplier relationships that propelled sales from $3 million to $12 million in 2 years • Trained and educated over 60 employees on defect prevention, SPC, root cause analysis technical sales and requirements identification resulting in improved KPI’s in all departments. Responsible for administering all corporate presentations to large original equipment manufacturers Show less
-
-
-
Dickson Testing Company
-
South Gate, CA
-
Quality Assurance Manager
-
Jan 1990 - Jan 1992
3 direct reports and 10 indirect reports • Managed complete Quality Assurance Department • Conducted/hosted quality audits with Bell Helicopter, Rolls Royce Aircraft Engines, GE Aircraft Engines, Allied and McDonnell Douglas in accordance with strict Military and Aerospace specifications • Responsible for all documented standard operating procedures in stress rupture, chemical analysis, heat treating, machining and order entry • Developed KPI’s for all critical processes 3 direct reports and 10 indirect reports • Managed complete Quality Assurance Department • Conducted/hosted quality audits with Bell Helicopter, Rolls Royce Aircraft Engines, GE Aircraft Engines, Allied and McDonnell Douglas in accordance with strict Military and Aerospace specifications • Responsible for all documented standard operating procedures in stress rupture, chemical analysis, heat treating, machining and order entry • Developed KPI’s for all critical processes
-
-
-
McDonnell Douglas Aircraft
-
Long Beach, California
-
Engineer / Associate Scientist
-
Dec 1987 - Jan 1989
• Created critical engineering drawings for over wing life support, emergency oxygen panels and flotation slide fixtures • Lead Engineer for critical engineering drawing review (Certified FAGAN Inspector) • Certified Statistical Process Control (SPC) Analyst • Continued Education: • Certified FAGAN Facilitator for drawing review team. • Certified SPC Analyst. • Created critical engineering drawings for over wing life support, emergency oxygen panels and flotation slide fixtures • Lead Engineer for critical engineering drawing review (Certified FAGAN Inspector) • Certified Statistical Process Control (SPC) Analyst • Continued Education: • Certified FAGAN Facilitator for drawing review team. • Certified SPC Analyst.
-
-
Education
-
California State Polytechnic University-Pomona
BS, Mechanical Engineering -
Catawba Valley Community College
Hosiery -
Philip Crosby and Associates / The Quality College
Facilitator Certification Training, Quality Management, Control and Improvement -
McDonnell Douglas Aircraft
Certified Fagan Inspector, Engineering Document Inspection
Community
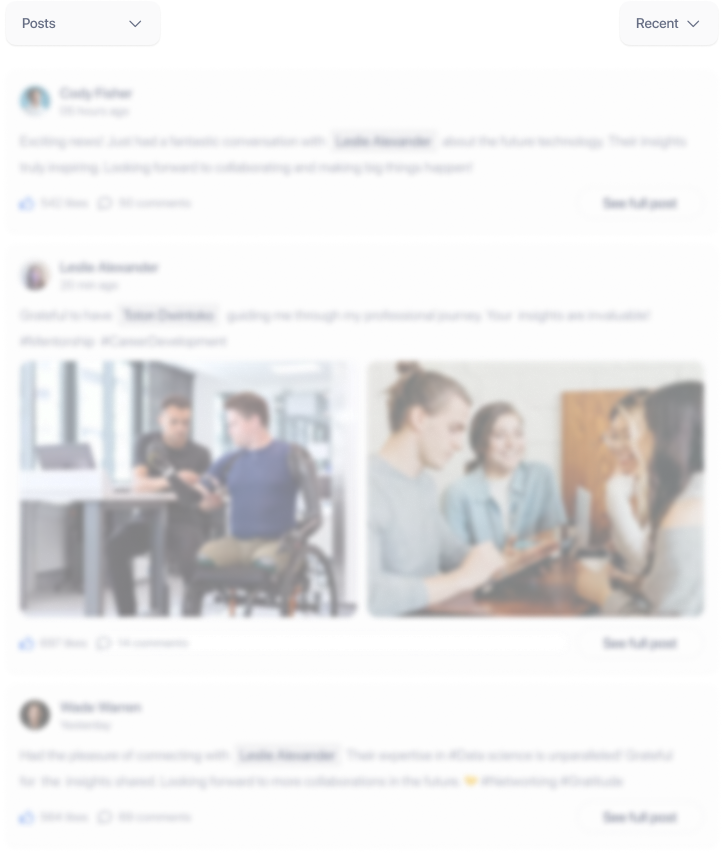