Roy E. Townsend Jr, LSSGB
Operations Process & Continuous Improvement Engineer at Sugar Foods Corporation- Claim this Profile
Click to upgrade to our gold package
for the full feature experience.
Topline Score
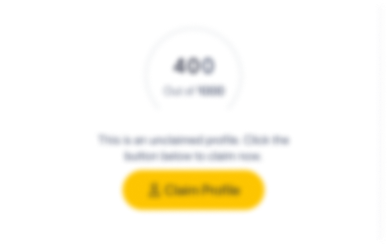
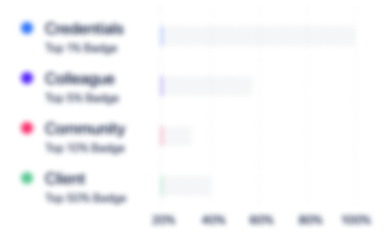
Bio


Credentials
-
HACCP (Food Safety) Auditor
Safe Food AllianceOct, 2020- Nov, 2024 -
Six Sigma - Green Belt
MOSES CONE HEALTH SYSTEMJan, 2015- Nov, 2024
Experience
-
Sugar Foods Corporation
-
Food and Beverage Manufacturing
-
300 - 400 Employee
-
Operations Process & Continuous Improvement Engineer
-
Nov 2022 - Present
Implement practices for improvements in personnel safety, food safety, and food quality. Works with Quality and Operations teams to maintain product consistency and product quality. Analyze and identify opportunities to reduce process variation, improve process capabilities and optimize process performance. Develop innovative solutions to support new products, processes, and capabilities. Assume subject matter expert status for manufacturing processes (manufacturing, packaging, filling etc.). Perform equipment/process capability analysis and testing. Lead trials to improve processes, procedures, and reliability. Support systems including PLC’s, in-line measurement, packaging, and automation. Provide weekly, period, and 'Year to Date' reliability and variability downtime analysis support with action plan to the operations team. Apply knowledge of industrial engineering principles and practices in broad areas of assignments and related fields. Champion new initiatives directed toward continuous improvements and waste reduction efforts. Conduct equipment utilization and capacity studies and provide recommendations and action plan and deliverables. Provides leadership in the implementation of CFM/Lean Manufacturing techniques. Lead efforts to reduce equipment setup time. Apply ergonomic techniques to improve working conditions in manufacturing.
-
-
-
Middleby Outdoor
-
United States
-
Manufacturing
-
100 - 200 Employee
-
Planning Manager
-
Oct 2021 - Aug 2022
-
-
-
Luxottica
-
Italy
-
Luxury Goods & Jewelry
-
700 & Above Employee
-
Manager, Planning (AFA)
-
Jan 2021 - Oct 2021
Part of the distribution planning team of a 1st level distribution center with the objective to manage the allocation run and simulation function for the military channel of trade for AFA (Apparel, Footwear, and Accessories), and support the analysis and the optimization of the service level. Part of the distribution planning team of a 1st level distribution center with the objective to manage the allocation run and simulation function for the military channel of trade for AFA (Apparel, Footwear, and Accessories), and support the analysis and the optimization of the service level.
-
-
-
The Home Depot
-
United States
-
Retail
-
700 & Above Employee
-
Senior Operations Business Analyst
-
Jan 2019 - May 2020
January 2019 – May 2020 Senior Operations Business Analyst – Labor Engineering • Allocate labor hours to individual departments within a Home Depot store using historical data, and calculated rates that are obtained through labor study and the rates of historical drivers. • Create SQL queries to obtain historical data from select tables within the Home Depot’s database. • Currently implementing a new labor model in the Deliveries department that will allocate hours unto Home Depot stores based on the complexities of a delivery, instead of simply using an average to assign hours • Assists stores and field support by providing data when needed. • Saved The Home Depot $2,000,000 by completing a waste time study, and eliminating steps in the overall waste disposal process in the Massachusetts stores. • Directly responsible for the allocation of $500,000,000 worth of labor throughout 2,000 Home Depot stores.
-
-
-
DGS
-
United States
-
Airlines and Aviation
-
700 & Above Employee
-
Systems Engineer
-
Feb 2018 - Jan 2019
• Provide staffing, scheduling and shifts to the world’s largest wheelchair operation in the Atlanta airport using a staffing program and historical data.• Analyze and collect data through Delta platforms to keep up with wheelchair agent behaviors, delay patterns, injuries, agent performance, and productivity throughout the operation.• Serve as a liaison between both Delta Global Staffing directors and Delta directors; providing support through providing data.• Head up the Ergonomics team. Currently in the midst of a project where the goal is to reduce agent injuries by 15%. In the process flow building stage.• Involved in start up of wheelchair contract, so currently building reports, standards of procedures, and guidelines for the operation.
-
-
Performance Resource Analyst
-
Feb 2017 - Feb 2018
• Provide staffing analyses specific to airports and contracts.• Performance analyses in support of certain DGS continuous improvement processes.• Provide flight schedule analysis and presented to business leaders and station managers.• Visit different airports/stations to locate continuous improvement opportunities, and implement processes that improve the overall flow and process of the airport operation.• Identified both ergonomic and safety issues within one of the airport operations, and recommended procedures to solve those issues. Recommended ear equipment to decrease risk of hearing loss in operation and identified ergonomic issues with the checked in bag process.
-
-
-
Shaw Industries
-
United States
-
Textile Manufacturing
-
700 & Above Employee
-
Process Engineer
-
Jan 2016 - Jan 2017
• Waste Champion within the plant. Lead initiatives and projects throughout the plant to drive down overall waste in the plant.• Manage support staff (Financial Systems clerk, Waste clerk).• Set budget for plant; while also setting standards & projections for carpet styles within plant.• Update guidelines used for product costing and accounting.• Prepare business cases and capital projects recaps; calculate savings and return on investment within plant.
-
-
Process Improvement Engineer
-
Jan 2015 - Jan 2016
• Set budget for plant; while also setting standards & projections for carpet styles within plant.• Initiated and completed a Six Sigma Black Belt project to increase productivity in the Yarn Mill. Altered change over procedures that has saved the plant a total of $270,000.• Lead Kaizen events to increase productivity, increase safety throughout warehouse and plant, and reduce waste.• Manage the Six Sigma projects of Green/Black Belts and assists within the plant on various improvement efforts. Maintain a constant stream of Six Sigma Projects in the plant.• Waste Champion within the plant.
-
-
Operations Management Trainee - Industrial Engineer
-
Aug 2014 - Jan 2015
• Conducted comprehensive study of widths on kuster and coater across style groups by working with associates in each department. This work followed removal of two yarn ends in tufting and ensured that product specifications and customer expectations were met for all styles.• Conducted a 5S event on Tufting floor to reduce associate motion throughout plant.• Under the direction of the Senior Process Engineer, created style reference sheet for Plant 23 capturing reference critical product specifications. Gathered information using G-Link, Color Map, Data Analysis, and HQMS.• Developed understanding of budget, POVA, and standards by working with Process Improvement Manager.
-
-
Education
-
North Carolina Agricultural and Technical State University
Bachelor of Science (B.S.), Industrial Engineering
Community
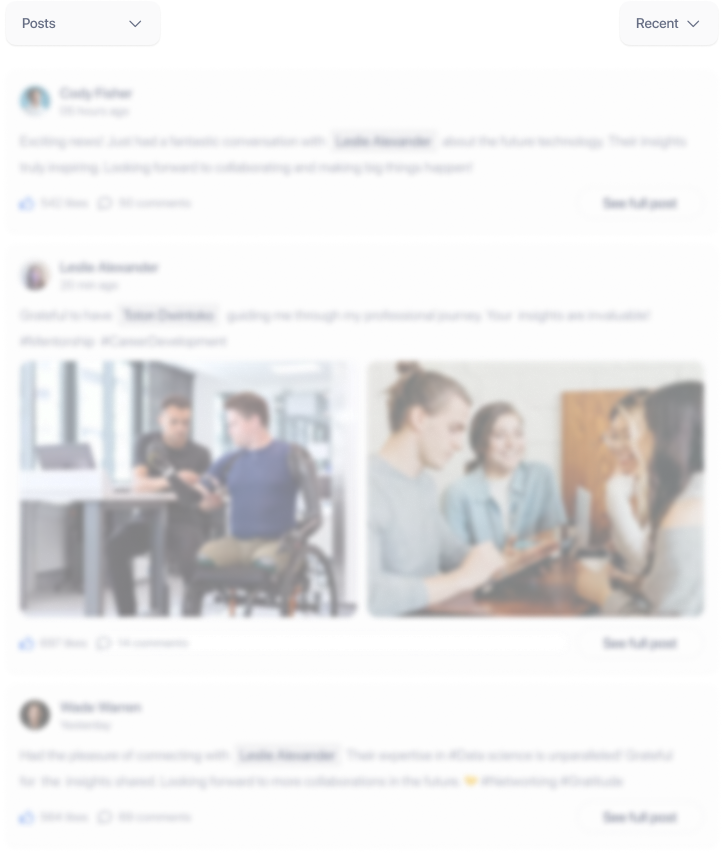