Rose Maria Andrade
Senior Operations Director at Fabfoods- Claim this Profile
Click to upgrade to our gold package
for the full feature experience.
-
Spanish Full professional proficiency
-
English Native or bilingual proficiency
-
Portuguese Native or bilingual proficiency
Topline Score
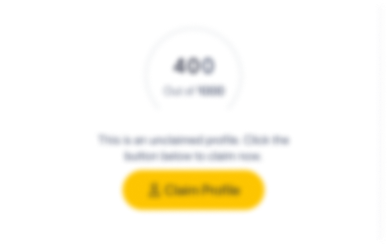
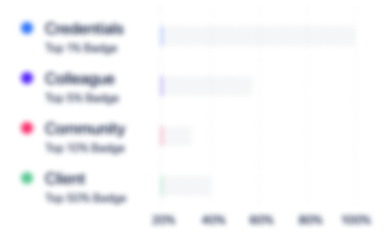
Bio

Aline Araujo Ferreira
Rose Andrade , uma líder que gera inspiração na sua equipe! Tive o prazer de trabalhar com a Rose, e me desenvolver com seus feedbacks e apoio. Muito experiente com gestão de pessoas e sempre auxilia no crescimento de sua equipe ! Eternamente grata por ter feito parte de sua equipe de trabalho ! Sucesso sempre ! Grande profissional 👏🏻

Kerginaldo Melo
Rose is a extremely dedicated and results- focused professional, who knows the importance of people in the results and leads by example

Aline Araujo Ferreira
Rose Andrade , uma líder que gera inspiração na sua equipe! Tive o prazer de trabalhar com a Rose, e me desenvolver com seus feedbacks e apoio. Muito experiente com gestão de pessoas e sempre auxilia no crescimento de sua equipe ! Eternamente grata por ter feito parte de sua equipe de trabalho ! Sucesso sempre ! Grande profissional 👏🏻

Kerginaldo Melo
Rose is a extremely dedicated and results- focused professional, who knows the importance of people in the results and leads by example

Aline Araujo Ferreira
Rose Andrade , uma líder que gera inspiração na sua equipe! Tive o prazer de trabalhar com a Rose, e me desenvolver com seus feedbacks e apoio. Muito experiente com gestão de pessoas e sempre auxilia no crescimento de sua equipe ! Eternamente grata por ter feito parte de sua equipe de trabalho ! Sucesso sempre ! Grande profissional 👏🏻

Kerginaldo Melo
Rose is a extremely dedicated and results- focused professional, who knows the importance of people in the results and leads by example

Aline Araujo Ferreira
Rose Andrade , uma líder que gera inspiração na sua equipe! Tive o prazer de trabalhar com a Rose, e me desenvolver com seus feedbacks e apoio. Muito experiente com gestão de pessoas e sempre auxilia no crescimento de sua equipe ! Eternamente grata por ter feito parte de sua equipe de trabalho ! Sucesso sempre ! Grande profissional 👏🏻

Kerginaldo Melo
Rose is a extremely dedicated and results- focused professional, who knows the importance of people in the results and leads by example
0
/5.0 / Based on 0 ratingsFilter reviews by:
Experience
-
Fabfoods
-
South Africa
-
1 - 100 Employee
-
Senior Operations Director
-
Jun 2022 - Present
-
-
-
DSM
-
Indonesia
-
Facilities Services
-
1 - 100 Employee
-
Senior Plant Operations Manager
-
Feb 2008 - Nov 2018
Responsible for the operation of a large and high complexity production site include 3 chemistry productions plant and two final product plant and the internal logistic, include production management plan, project implementation, cost controls, management of HSE and quality systems and organizational changes and manager engineer projects to adequate the site up to global standard.Improvements the levels of customer service by define management and process system to manager delays, customer dissatisfaction, communication problems between sales and manufacturing, creating KPIs to measure performance and identify the principal causes of problems and create action plan to solve the inefficiency.implement of quality tools, training, adequacy of procedures for high level of customer satisfaction;Improving efficiency of delivery on time, right first time, cost, Improve the warehouse management and control by implement methodologies such as lean manufacture for Warehouse, visual management, housekeeping and define KPIsmanager improvement project and behavioral program in quality, SHE ( safety health and environmental) by use methodology such as Six Sigma, SafeStart, stop and some internal initiative to involving all teammates Improvement of 20% in the production volume in less then 3 months by performance route cause analyze of performance killers and involving the right team;Manage global strategy projects for cost reduction, continuous improvements, productivity increase, process optimization. Attained targets defined at global, region and site level. Show less
-
-
Warehouses Operational manager - Brazil
-
Jul 2017 - Feb 2018
• Responsible for the operation of 9 distribution centers, include implementation of all SOP, cost controls, management systems, process redefinition, training, and organizational changes to bring up all nine DCs to DSM standard.• Improvements the levels of customer service by define management and process system to manager delays, customer dissatisfaction, communication problems between sales and manufacturing, creating KPIs to measure performance and identify the principal causes of problems and create action plan to solve the inefficiency.• Deployment of quality tools, training of staff, adequacy of procedures for high level of customer satisfaction;• Improving efficiency of delivery on time, right cost, and quality by implement methodologies such as lean manufacture for Wearhouse, visual management, housekeeping and define KPIs to manager and control.• Deployment and training the teams in methodologies such as Six Sigma, 6'S, HACCP, IN65 and FAMIQs, SHE, Security and process safety.• Implanting the internal systems and culture of Safety, health and environment and increase the mindset of the team• Managed global strategy projects for cost reduction, environment improvement, productivity increase, process optimization. Attained targets defined at global level, developed partnerships with universities and started working with the lean manufacture for Wearhouse method. Show less
-
-
SHE (Safety, Health and Environment) and Security Manager for manufacture sites and DC - Brazil
-
Mar 2013 - Apr 2017
Position 2013 - 2017: SHE and Security ManagerReporting to: Operations VP Brazil Staff: 12 directs and 1000 indirectTeam leader of Tortuga integration with DSM leading the groups responsible to implement operational and process safety and security procedures to comply with DSM industrial standards and requirements.Implemented framework to assess, control and monitor by use a systematic audit program, definition of projects procedures and training to be comply with DSM requirements and twelve Life save rules and comply with international rules (OSHA, GHS etc.).Improved the levels of SHE (safety, health and environment) and Security a reduction by more than 90% of reportable events (OSHA). And implementation of 100% of actions planned.creation and implementation of preventive culture through training as SafeStart, STOP program, recognition program NEMO card, internal and cross-audits, team development, maintenance program and managerial tools and methodology .. Show less
-
-
Site Operations Manager
-
Feb 2008 - Apr 2013
Reporting to: DirectorStaff: 100 people- Responsible for production, maintenance, production planning and Receiving and Warehouse areas.- Improvements the levels of customer service above the expected time by 30%, eliminating delays, customer dissatisfaction, communication problems between sales and manufacturing, creating KPIs to measure performance and identify the principal causes of problems and create plan action to solve the inefficiency.- Deployment of quality tools, training of staff, adequacy of procedures for obtaining certifications such as ISO 9001, IN65, HACCP, GMP and FAMIQs systems.- Improving efficiency of equipment in 20%, reduction about 30% of no scheduled equipment stop and increasing the useful life of the machines through methodology as TPM (Total Productivity Maintenance), preventive and predictive maintenance.- Deployment and training the teams in methodologies such as Six Sigma, 6'S, TPM, HACCP, IN65 and FAMIQs.- Implanting the internal systems and culture of Safety, health and environment system and achievement the results proposed by the company zero incidents and accidents ( more than 3 years with no accidents and incidents). Show less
-
-
-
Libbs Farmacêutica Ltda
-
1 - 100 Employee
-
Production and Total Quality Manager
-
Feb 2005 - Mar 2006
Reporting to: Industrial Manager Staff: 98 people - Improved finished product inventory levels, thereby eliminating product shortages with the implementation of production planning and scheduling in the area, and improving productivity through the implementation of methodologies like Set Up and Housekeeping. - Improved the work environment by implementing self-managed teams. Reduced significantly rework and losses with the creation of more than 60 general standard procedures, GMP and onsite training for trams. - Started to implement TPM (Total Productive Maintenance) with the objective of increasing productivity and reducing the large number of overtime hours in the factory, with a 12% improvement in productivity (reallocation of 240 h/m/month) and increase in production. - Coordinated the pilot project to reduce set-up with 40% gain in the first phase, using the SMED method (Single Minute Exchange of Dies). Show less
-
-
-
Sanofi
-
France
-
Pharmaceutical Manufacturing
-
700 & Above Employee
-
Manufacturing Excellence Manager
-
Dec 1998 - Mar 2003
Reporting to: Manufacturing Director Brazil and Excellence Director Latin America Staff: up to 08 people - Managed global strategy projects for cost reduction, environment improvement, productivity increase, process optimization, and time cycle reduction. Attained targets defined at global level, developed partnerships with universities and started working with the Six Sigma method. - Developed and implemented an Operational Training Program in the Suzano factory aimed at preventing (material and product) losses due to lack of knowledge of processes and equipment. The program included practical and theoretical training of the production process, trainings on Security GMPs and environment, in addition to changes in processes and systems. - Coordinated studies of key products/processes aimed at reducing costs and increasing time to respond to customers. Reduced by 50% cycle times, improved by 1% the yield of three key products (15% of total production), and reduced set up times by 30%. This project was used as a reference in plants in other countries. - Administrated improvement actions of the 5S Program, quantifying and qualifying results, conducting and receiving auditors. Created leaders for training on all phases and dissemination of procedures for production lines. - Conducted work seeking to improve the organizational climate and managed leaders through the “Great Place to Work” initiative in Brazil. Show less
-
-
-
-
Production Manager
-
Aug 1989 - Dec 1998
Reporting to: Manufacturing Director Staff: 200 people, including Supervisors, Engineers, Quality and Operators - Led a project to transfer all injectable products from sites in Argentina, Venezuela and Mexico to the facilities of the plant in São Paulo, when Rhodia and Hoechst merged, forming Aventis Pharma. Participated in the process to build a new injectables factory in Suzano. - Led a project to transfer the manufacturing of liquids and ointments from Rhodia’s former factory in São Paulo to Aventis Pharma’s plant in Suzano, which included coordinating changes in technologies and processes, controlling the schedule to prevent failures in market supply, in addition to managing cultural and behavioral conflicts. - Developed and managed a security system to reduce accident rates, which enhanced staff awareness regarding security and thus led to a significant reduction in accidents with or without leaves of absence. Show less
-
-
Education
-
London School of Business and Finance LSBF
Executive education management Development program, Business, marketing and planning strategy, effective managment techniques, managerial finance -
Business School Sao Paulo - BSP
Master of Business Administration (M.B.A.), Business Administration and Management, General -
Universidade Bandeirante de São Paulo
Bachelor of Applied Science (B.A.Sc.), Pharmaceutical Sciences -
Universidade de São Paulo
Pos Graduation, Industrial Engineering -
Universidade Paulista
Bachelor of Business Administration (B.B.A.)
Community
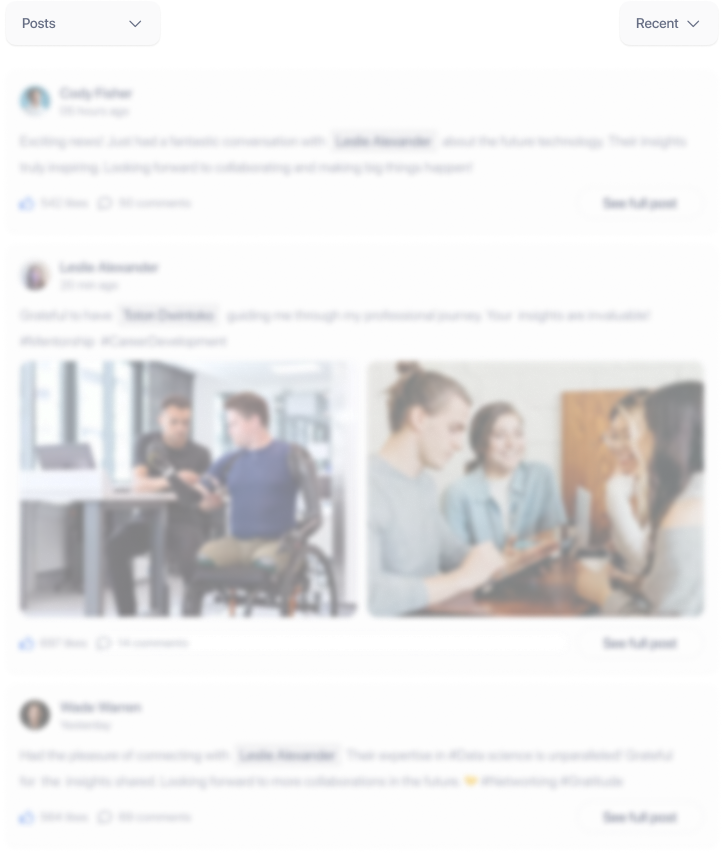