Ronnie Rostamian
Director of Quality Assurance, Health, Safety & Environment at Omron Delta Tau Data systems- Claim this Profile
Click to upgrade to our gold package
for the full feature experience.
-
English Professional working proficiency
-
Armenian Native or bilingual proficiency
-
Persian Native or bilingual proficiency
Topline Score
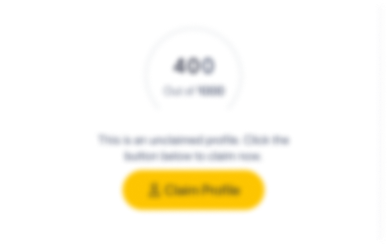
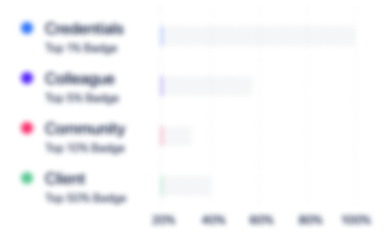
Bio

LinkedIn User
I worked directly with Ronnie for one year in Pars Telecom. He is a brilliant colleague with active engineering mind and systematic approach. He is a very supporting colleague with a team work mind set.

Amit Agnihotri
I have known Ronnie for over 4 years now. I have taken several classes with him and we accomplished various projects together. He is a true professional and is dedicated and responsible toward any tasks that are assigned to him. He is a great team player. Once a task is assigned to him, I know that it will be completed in an accurate and concise manner. In most cases he would volunteer to lead the team. I wish him the best.

LinkedIn User
I worked directly with Ronnie for one year in Pars Telecom. He is a brilliant colleague with active engineering mind and systematic approach. He is a very supporting colleague with a team work mind set.

Amit Agnihotri
I have known Ronnie for over 4 years now. I have taken several classes with him and we accomplished various projects together. He is a true professional and is dedicated and responsible toward any tasks that are assigned to him. He is a great team player. Once a task is assigned to him, I know that it will be completed in an accurate and concise manner. In most cases he would volunteer to lead the team. I wish him the best.

LinkedIn User
I worked directly with Ronnie for one year in Pars Telecom. He is a brilliant colleague with active engineering mind and systematic approach. He is a very supporting colleague with a team work mind set.

Amit Agnihotri
I have known Ronnie for over 4 years now. I have taken several classes with him and we accomplished various projects together. He is a true professional and is dedicated and responsible toward any tasks that are assigned to him. He is a great team player. Once a task is assigned to him, I know that it will be completed in an accurate and concise manner. In most cases he would volunteer to lead the team. I wish him the best.

LinkedIn User
I worked directly with Ronnie for one year in Pars Telecom. He is a brilliant colleague with active engineering mind and systematic approach. He is a very supporting colleague with a team work mind set.

Amit Agnihotri
I have known Ronnie for over 4 years now. I have taken several classes with him and we accomplished various projects together. He is a true professional and is dedicated and responsible toward any tasks that are assigned to him. He is a great team player. Once a task is assigned to him, I know that it will be completed in an accurate and concise manner. In most cases he would volunteer to lead the team. I wish him the best.

Credentials
-
Six Sigma Green Belt
CSUNMay, 2009- Oct, 2024 -
Surface Mount Solder Join Standard
IPC -A-600Sep, 2008- Oct, 2024 -
QMS ISO 9001 Auditor
-Mar, 2007- Oct, 2024 -
ASQ Certified Manager of Quality/Organizational Excellence
ASQ - World HeadquartersMar, 2018- Oct, 2024
Experience
-
Omron Delta Tau
-
United States
-
Electrical/Electronic Manufacturing
-
1 - 100 Employee
-
Director of Quality Assurance, Health, Safety & Environment
-
Nov 2015 - Present
Ensures that company and customer quality requirements are met on assigned products, programs, areas and functions. Develops various quality reports for upper management and communicates progress and activities. Monitor company process and performance KPI, company goals and objectives, process and products yield. Generate corporate required reports, and manage the action items and activities. Acts as the main contact for external quality and/or customer quality audits. Interfaces and interact with customers, suppliers, and regulatory agencies for compliance and problem resolution. Manages audits of Supplier systems, products, and processes to identify need for improvement. Establishes and implements quality awareness programs and develops systems to track and report results. Manage and coordinate company management and quality system activities including continuous improvement kaizen efforts. Manage and maintain ISO-9001 and ISO14001 certification via overseeing internal audit, supplier audit and registrar requirements. Participate in decisions, recommendations pertaining to non-conforming materials and products at MRB with supplier or manufacturing issues. Manage corrective action and preventive action CAPA process and review and approve CAPA results. Manage and review QMS and EMS procedures and instructions. Review QA and EHS Team objectives and results regularly to evaluate success of department and product quality. Provide leadership, guidance and training to team to promote individual and departmental growth in a high performance environment. Manage and monitor IQC, IPQC and OQC activities and procedures. Hire, train and manage quality assurance and quality control and environmental staff. Show less
-
-
-
EnerSys
-
United States
-
Appliances, Electrical, and Electronics Manufacturing
-
700 & Above Employee
-
Manufacturing Quality Manager/ Sr. Quality Engineer
-
Apr 2013 - Nov 2015
Engage QC/QA/Test, Manufacturing and Engineering Staff daily to identify and correct process deficiencies. Maintain surveillance pertaining to Company QMS Processes to ensure compliance to company QMS, ISO 13485 and AS9100. Supervises/Train and coach the quality receiving, in-process and final inspection team in maintaining an effective quality workforce. Ensures staff coverage across the entire manufacturing floor and across all shifts. Carries out supervisory responsibilities in accordance with the organization's policies and applicable laws, including interviewing, hiring, terminating and training employees; planning, assigning, and directing work. Proactive in engaging manufacturing staff and prioritizes the completion of quality inspection tasks to meet production deadlines. Implements new inspection skill sets based on new product requirements. Improves inspection test equipment usage and reliability. Monitor and maintain department Key Performance Indicators (KPI) and report periodically. Deploy and manage inspection continuous improvement activities. Support medical product line quality engineering activities such as disposition and review discrepancies. Coordinates product testing, analysis and reporting of results (internal/external) to ensure compliance to customer specification. Analyze process data and identify tangible actions to drive improvement. Supports corrective and preventive action (CAPA), Problem Reporting activities related to audits, customer feedback and complaint investigations. Initiate and submit non-conformance report to Material Review Board (MRB). Sets up and manages test regimes to determine product quality. Writes test protocols, coordinates and executes testing and test reports for product qualifications. Develops, implements test and inspection techniques, documents inspection plans. Reviews and audits documentation to ensure accuracy and performs other duties and responsibilities, as required. Show less
-
-
-
Delta Tau Data Systems inc.
-
Chatsworth, CA
-
Quality Assurance Manager / R&D Project Coordinator
-
Jan 2007 - Apr 2013
Quality Assurance manager for design and manufacturing electronic company with high precision motion controller and amplifier products. Establish, maintain, analyze and improve the ISO 9001-2008 Quality Management System, related to all organizational quality processes. Responsible for company’s Quality Manual, Policies and maintenance of all Procedures and Working Instructions. Conduct and coordinate quality audits including internal, customer, supplier and registrar. Plan, improve and monitor quality of processes and products by implementing data collection (dashboard) and Data Analysis and goal oriented process controls. Review data throughout the company to determine possible failure trends, workmanship issues, supplier issues and process improvement needs. Monitor and control receiving inspection and in process inspection throughout the company. Control and eliminate process and product nonconformities by implementing and applying MRB (Material Review Board) and CAPA (Corrective Action Preventive Action) methods. Coordinator, planner and leader of CCB (Configuration Control Board) process. Fulfill customer contractual quality requirements and implement into processes such as First Article Inspection Reports and Source Inspection. Work directly with customer quality organizations in order to resolve issues and product improvement. Schedule, control and manage R&D projects and development processes. Collaborate with design engineers to better understand the process need, follow through and completion of design projects. Conduct and instruct quality and process related trainings for employees on annual and as needed basis as well as maintaining training matrix and records of all related trainings. Show less
-
-
-
-
Production Planning Supervisor
-
2005 - 2006
Production Planning supervisor for design and manufacturing company with high quality wood furniture and kitchen cabinet products. Organized, planed, scheduled and coordinated production projects and orders. Developed production capabilities and efficiency assessment by implementing production planning tools. Prepared the infrastructure of production planning for HYPSIS ERP software implementation. Improved the organization work flow by establishing Process Flow diagrams. Implemented Coding System to improve process and material flow. Analyzed and prepared manufacturing operation processes for various work orders. Show less
-
-
-
-
Quality Assurance Engineer
-
2004 - 2005
Quality Assurance engineer for Service Company with high speed broadband internet and internet phone card products. Implemented the Quality Management System (ISO 9001 standard). Created and implemented quality manual, procedures and working instructions for different departments. Implemented and improved the quality validation process. Worked on Syscon Solution as a team member to adopt Enterprise Resource Planning (ERP) software for Small and Medium Enterprises (SME). Analyzed and Prepared Company for ERP software and system implementation and prepared the documentations needed for software instructions. Show less
-
-
-
-
Project Control Engineer
-
2003 - 2004
Project control engineer for design and manufacturing company with high quantity automotive transmission products. Established WBS (Work Breakdown Structure) and LRM (Linear Responsibility Matrix) for manufacturing projects. Estimated time, resources and budget requirements for projects. Performed Time Study and Capacity Analysis and prepared Feasibility Study and Cost Analysis reports. Controlled the development projects and prepared weekly and monthly progress reports for management using Gantt and S-Curve charts via MS Project and Excel. Worked in a team to prepare PPAP (Production Part Approval Process) package and FMEA (Failure Mode and Effect Analysis) reports for projects. Created executive report and presentation for each project and presented project milestones and bottlenecks to upper management. Show less
-
-
Education
-
California State University, Northridge
MS, Engineering Management -
IUST
BS, Industrial Engineer
Community
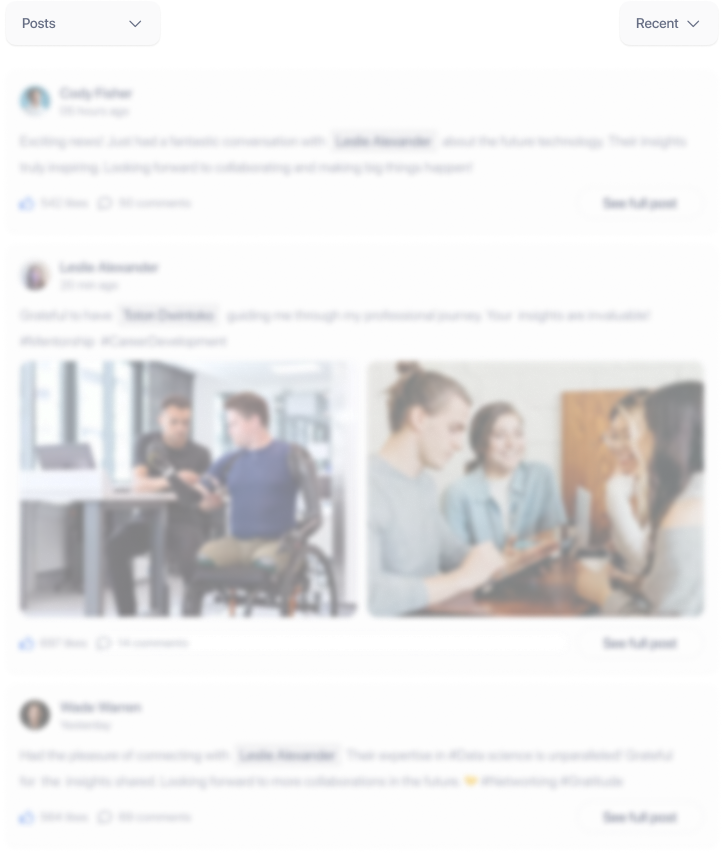