
Ronnel Lorenzo
Field Service Technician at Mid Atlantic Industrial Equipment- Claim this Profile
Click to upgrade to our gold package
for the full feature experience.
Topline Score
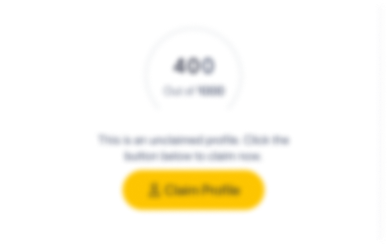
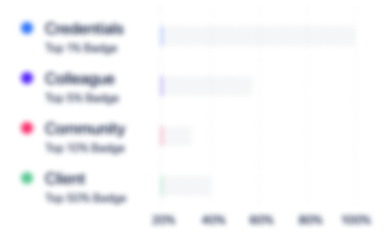
Bio


Credentials
-
Boosting Your Team's Productivity
LinkedInMar, 2021- Oct, 2024 -
Project Leadership
LinkedInMar, 2021- Oct, 2024 -
Quality Management Foundations
LinkedInMar, 2021- Oct, 2024 -
Transitioning from Manager to Leader
LinkedInMar, 2021- Oct, 2024 -
How to Make Strategic Thinking a Habit
LinkedInFeb, 2021- Oct, 2024 -
Managing Logistics
LinkedInFeb, 2021- Oct, 2024 -
Managing for Results
LinkedInFeb, 2021- Oct, 2024 -
Six Sigma Green Belt (CSSGB)
International Six Sigma Institute™Nov, 2020- Oct, 2024 -
Commercial Driver License (CDL)
Troops Into Transportation & The CDL SchoolsDec, 2019- Oct, 2024
Experience
-
Mid Atlantic Industrial Equipment
-
United States
-
Machinery Manufacturing
-
1 - 100 Employee
-
Field Service Technician
-
Aug 2021 - Present
-
-
-
Frozen Food Development
-
United Kingdom
-
Food and Beverage Manufacturing
-
Plant Maintenance Manager
-
Apr 2021 - Aug 2021
-
-
-
Royal Arc
-
United States
-
Professional Training and Coaching
-
1 - 100 Employee
-
Field Service Manager - North East Region
-
Jan 2021 - Apr 2021
• Promote the company’s image, appearance, and reputation to new and existing customers.• Ensure assigned area meets or exceeds customer and company requirements to establish and grow customer relationships.• Assist with planning and scheduling of field service activities and projects.• Support operation manager to achieve ongoing service revenue growth, profitability, productivity, and quality.• Accountable for service equipment installations, preventative maintenance, equipment upgrades and updates, and sales support for new systems.• Prioritize operational issues and implement creative solutions to solve problems as they arise.• Manage regular maintenance for service vehicles, trailers, and lifting equipment.• Assist management and administration of general business operations.• Involved in creating and implementing a strategy focused on achieving financial and customer satisfaction results.• Communicate technical issues to management, technical support and quality assurance to ensure situation is addressed properly.• Assist with the assembly and preparation of orders and all warehouse operations.• Responsible for expense control within the assigned area to comply with targets and goals set.• Ensure compliance with State/Local/Federal regulations and guidelines.
-
-
Site Supervisor
-
Jan 2020 - Jan 2021
• Inspect overhead industrial cranes and hoists to verify safety and compliance with manufacture, OSHA, and ANSI standards.• Conduct all applicable safety training to include monthly, semiannual, and annual training.• Conduct preventive and complex repairs, perform scheduled inspections, and load testing on overhead cranes and hoist equipment.• Ensure compliance with appropriate safety policies and procedures, on and off work site.• Provide a high level of communication with both Customer and Corporate Office.• Maintain Timesheets, data and record management.• Troubleshoot mechanical & electrical component malfunctions, complete necessary repairs and maintenance.• Oversee installations and replacements of electrical controls, circuits, relays, transformer, main line, fuses, and festoon to ensure proper operation and ensure compliance with EM 385-1-1.• Work closely with leads, specialists and other supervisors to develop specific objectives, strategies, and action plans.• Ensure vehicles, lifts, and trailers are maintained to the best possible standard.• Responsible for maintaining and accuracy of OSHA 300 Log
-
-
-
Ring Container Technologies
-
United States
-
Plastics Manufacturing
-
300 - 400 Employee
-
Electro Mechanical Technician
-
Mar 2019 - Nov 2019
• Perform routine preventative maintenance of machinery and equipment to ensure smooth business and production operations.• Troubleshoots and repairs manufacturing equipment: motor controls, AC/DC drives and controls, dryer systems, extruders, temperature instrumentation, packaging machines electronic scales.• Assemble, install, or repair wiring, electrical and electronic components, pipe systems and plumbing, machinery, and equipment.• Replace and test electrical circuits, equipment and appliances using hand tools and testing instruments.• Able to work with single phase, 3 phase, 110V, 240V, 480V, and 24V control systems. • Wire machinery using various circuits and phases, blueprints, charts or wiring diagrams.• Ensure accurate parts assignments and equipment histories are maintained.• Complete and document all necessary reports and maintenance work orders under EAM• Assist in training operators/mechanics on repairs, adjustments and standard operating procedures.• Assist supervisor and quality assurance personnel to maintain continuous improvement on quality product and safe environment.
-
-
-
Sonoco
-
United States
-
Packaging and Containers Manufacturing
-
700 & Above Employee
-
Electro Mechanical Technician
-
Jan 2018 - Mar 2019
• Conducting preventive maintenance on extrusion system, printers, pneumatic and hydraulic systems, vacuum generators and conveyor systems. • Troubleshooting mechanical & electrical systems continuously staying proactive on preventive solutions for maintenance tasks and procedures to eliminate downtime and delays in production. • Documenting performed work and root causes for historical data and future analysis on C-Works (CMMS). • Maintaining a safe work environment ensuring all safety standards are meet. Fabricating guards and systems to improve and provided a safer environment. • Assisting shift lead and supervisors to maintain quality production that meet the customers and Sonoco standards. • Completed CAT II industrial Electrical Certificate September 2018
-
-
-
-
Mechanical Technician
-
Apr 2017 - Jan 2018
• Maintained press and kiln equipment, hydraulics, pneumatic systems, high vacuum machines and conveyor systems. • Diagnose mechanical & electrical systems to provide immediate solutions and proper corrections, minimizing cost and preventing delays in production. • Ensure safety standards are meet by performing all safety procedures including lockout-tagout. • Assist shift supervisors and quality assurance personnel to produce quality materials that meet Dal-Tile and Mohawk standards.
-
-
-
US Army
-
United States
-
Law Enforcement
-
1 - 100 Employee
-
Fleet Maintenance Manager
-
Aug 2012 - Dec 2014
• Enhanced the organization’s maintenance standard operating procedures to ensure equipment operational readiness rates no lower than 95%.• Supervised and trained 27 personnel performing maintenance support and service. • Responsible for completing daily reports for equipment to subordinates to availability rates and repair parts tracking. • Provided personal and professional counseling to subordinates to enhance career development. • Implemented quality assurance schedule to ensure flow with operation schedule.• Oversaw assigned equipment and tool sets $1.7 million. • Performed scheduled and unscheduled maintenance of 23 track and 58 wheeled vehicles and support equipment valued at $324 million. • Assigned as the Maintenance Supervisor for supported units under the headquarters and a forward support company. • Provided technical guidance, troubleshooting, quality control and assurance, forklift operations, customer service, and quick repair turnaround times. • Considered the lead liaison between the Military command and local supervisors. Responsible for the retail facility servicing over 584 personnel; accountable for over $1.2 million in U.S. Army property.
-
-
Maintenance Supervisor
-
Aug 2004 - Aug 2012
• Managed automotive repair, support services, and equipment operation readiness for unit cavalry scout, consisting of 8 heavy wheeled vehicles, 4k and 10k forklift, and 1 mine & IED roller valued at $25 million. • Provided technical advice to higher-level staff on automotive issues. Determined trend analysis and recommended solutions to correct substandard conditions. Advised commander on policy and procedure establishment and enforcement of performance, training, discipline, daily conduct of assigned personnel. • Supervised and trained 23 personnel performing maintenance on vehicle fleet. Responsible for readiness for accountability of over $3 million worth of equipment. • Provided technical guidance, troubleshooting, quality control and assurance, customer service, and quick repair turnaround times for 2,000 pieces of supported equipment. • Perform Hazard Analysis and Risk Assessments.• Maintained daily reports for equipment availability rates and repair parts tracking. Analyzed and interpreted information from support activities and recommended solutions when issues existed. • Maintained a strong emphasis on command inspection program and training rotations away from home station. • Worked with local police and army, trained and assisted with movement, maintenance, leadership and setting up SOP’s (Standard Operating Procedures).
-
-
Education
-
Villanova University
Certificate, Agile Contract Management -
Motorcycle Mechanic Institute
Certification, Harley Davidson -
Central Texas College
General Study -
Guam High School DODEA
Community
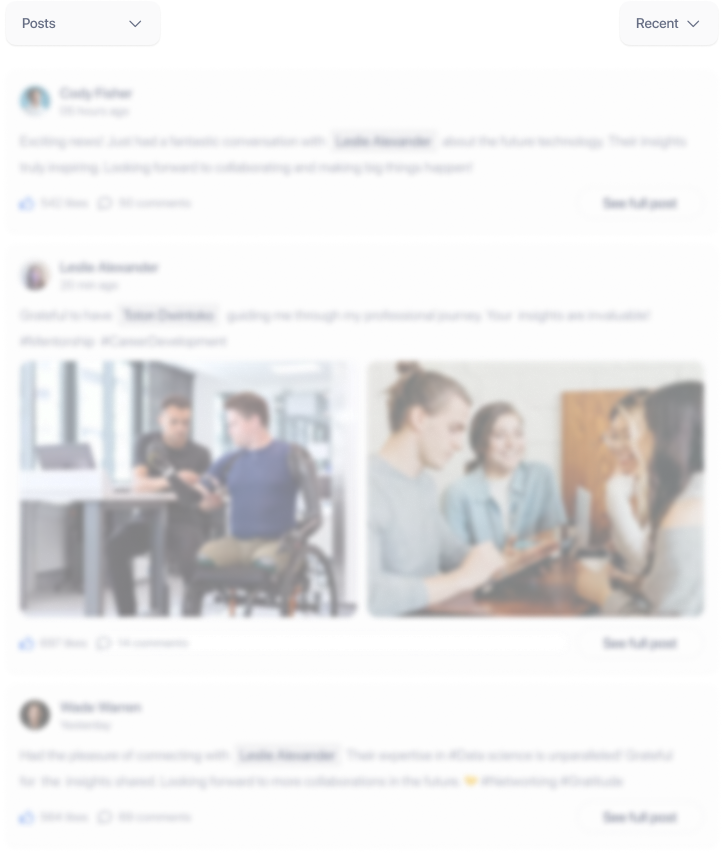