Ronan Ali, PMP, PMI-RMP
Project Controls Manager at RECON Engineering & Construction- Claim this Profile
Click to upgrade to our gold package
for the full feature experience.
-
Arabic -
-
English -
-
Chinese Elementary proficiency
Topline Score
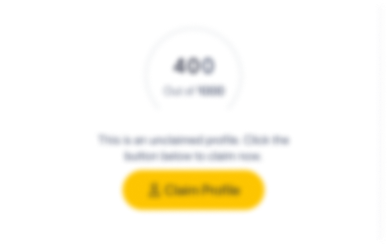
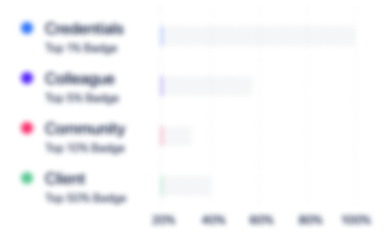
Bio

Amro Kandil
Ronan is an asset for any organization for her leadership and functional skills, her contribution was noticed and teamwork was appreciated.

Khaireddin Salama Alomoush
She is discipline in work, delivering on time, can handle multitask . She is good in follow up & follow through ,, usually meeting the deadline.

Amro Kandil
Ronan is an asset for any organization for her leadership and functional skills, her contribution was noticed and teamwork was appreciated.

Khaireddin Salama Alomoush
She is discipline in work, delivering on time, can handle multitask . She is good in follow up & follow through ,, usually meeting the deadline.

Amro Kandil
Ronan is an asset for any organization for her leadership and functional skills, her contribution was noticed and teamwork was appreciated.

Khaireddin Salama Alomoush
She is discipline in work, delivering on time, can handle multitask . She is good in follow up & follow through ,, usually meeting the deadline.

Amro Kandil
Ronan is an asset for any organization for her leadership and functional skills, her contribution was noticed and teamwork was appreciated.

Khaireddin Salama Alomoush
She is discipline in work, delivering on time, can handle multitask . She is good in follow up & follow through ,, usually meeting the deadline.

Credentials
-
Certificate of Appreciation
Black & VeatchAug, 2013- Sep, 2024 -
Best Participation : Making Quality Heard
Black & VeatchFeb, 2013- Sep, 2024 -
Certificate of Achievement
Black & VeatchSep, 2012- Sep, 2024 -
OSHA Ten Hours Training General Industry
Missouri S&TDec, 2011- Sep, 2024 -
PMI Risk Management Professional (PMI-RMP)®
Project Management InstituteJun, 2022- Sep, 2024 -
Project Management Professional (PMP)
Project Management InstituteDec, 2020- Sep, 2024 -
Two Hours OSHA Refreshment Course
-Mar, 2013- Sep, 2024 -
OSHA Ten Hours Construction Industry
Black & VeatchNov, 2012- Sep, 2024
Experience
-
RECON Engineering & Construction
-
Construction
-
1 - 100 Employee
-
Project Controls Manager
-
Feb 2020 - Present
-
-
-
KATERRA
-
United States
-
Construction
-
700 & Above Employee
-
Project Controls Engineer
-
Apr 2019 - Feb 2020
As a project controls engineer, Ronan was in charge of the integration vision of Katerra’s cost, risk management and schedule. Ronan’s first responsibility was to reestimate all the inflight jobs at Katerra a total of 25 projects. The vision is to integrate cost/ schedule and risk management. Ronan performed over target baseline estimate for all the projects. Initiated respective production and unit rates for all major commodities. This effort allowed Katerra to have resource loaded schedules. In addition, to seamless integration of all Katerra’s system, which allows for better forecasting for all the projects. Shortly after Ronan joined Katerra X organization. Katerra X is in charge of delivering Katerra products to the market. Ronan worked on the K3 and the corridor products. In her time with Katerra X, Ronan Ronan lead the implementation of AWP “Advance work packaging”. Ronan managed to aid in the processes of setting up all the EWPs “Engineering Work Packages”, PWPs “Procurement Work Packages” or as Katerra calls them FID “Field installation drawings” and the IWP “Installation Work Packages”. Ronan generated content for the EWPs in Revit 2020. Ronan helped Katerra bridge the gap to understand what is needed to be included in an IWP. In addition, Ronan generated IWP content in Execl to help Katerra X visualizing what goes into an IWP. Show less
-
-
-
Black & Veatch
-
United States
-
Engineering Services
-
700 & Above Employee
-
Project Controls - Lead Cost
-
May 2015 - Apr 2019
Direct operations in both Scheduling & Planning and Cost Engineering with a focus on industry technology and project management.COST ENGINEERING• Assembled necessary data utilizing Earned Value Management System to compose accurate monthly and quarterly cost reports.• Generated financial forecasting and cash flow for project completion.• Ensured proper and regular maintenance of the Change Management Program. Including Risk and Opportunity log, Backcharge log, Vendor Issues log.• Bridged communications with the Home Office Engineering team and the Filed Project Controls to develop the Bill of Quantities for obtaining accurate Control Budgets.• Devised and upheld subcontractor Field Project Measurement System.SCHEDULING/PLANNING• Collaborated with internal teams to schedule fragnet preparation and resource loading, conduct critical path analysis, and accomplish successful project planning.• Oversaw monthly schedule updates and progress reporting.• Prepared and maintained Plan/Earn/Spent reporting.Cost Engineer on OCE: Develop and maintain the cost report, cash flow, cost spreads and the BOQ. Alongside assisting with the change management process and internal reporting tools"Project Dashboard" Show less
-
-
Project Controls Senior Associate
-
Apr 2013 - May 2015
The Project Controls Sr Associate position is combination of Scheduling/Planning & Cost Engineering. This position primarily focused on seeking responsibility in the areas of scheduling, costing, and concepts related to the industry technology and project management.Cost Engineering:• Assists with the development of monthly/quarterly reports.• Assists in cash flow and in forecasting cost at complete.• Maintains the project Change Management Program.• Maintains project cost report under supervision.• Assists in invoicing to ownerScheduling/Planning:• Assists in schedule fragnet preparation and resource loading.• Assists in critical path analysis.• Prepares and maintains PES reporting. Show less
-
-
Project Quality Manager
-
Aug 2012 - Apr 2013
The Project Quality Manager is responsible for implementing quality procedures and best practices to fulfill the quality mission and support the successful execution of assigned Division’s projects as described in the Division’s Quality Management System (QMS) and/or the Nuclear Quality Assurance Program. Project Quality Manager will ensure implementation of the Division QMS through day-to-day and oversight activities and maintain the quality program for assigned projects. Technical:Understands principles, practices, techniques and theories of quality processes, including a thorough knowledge of ISO 9001:2008.Proficient in techniques relating to quality assurance and quality control programs and procedures.Possesses a basic knowledge of engineering, design, procurement, construction and project management principles, practices and methods.Ability to understand and follow instructions; makes sound judgments based on quality and project requirements; ; interacts effectively with B&V professionals as well as client, supplier, and contractor representatives. Intermediate knowledge of Microsoft Office computer tools.include:• Corrective action programs.• Quality process training.• Audits and assessment experience.• Root Cause Analyses.• Trend Analysis.• Supplier qualification programs and commercial grade dedication.Non-technical:Demonstrates intermediate: Process management, conflict management, total work systems, written communications, composure, managerial courage and decision quality. Show less
-
-
-
Bluefield Process Safety
-
United States
-
Chemical Manufacturing
-
1 - 100 Employee
-
Safety Consultant
-
Jan 2012 - Apr 2012
Bluefield Process serves the chemical, petrochemical, refinery, oil, and gas industries in their efforts to make their processes and facilities safer. Bluefield Process Safety vision is simple: make the world a safer place. Ronan as an intern with Bluefield Process safety was introduced to the following: • Facilitation of HazOp studies and other Process Hazard Analysis studies • Risk Assessment within the facility and the process • Risk Tolerance Criteria determination and application • Facilitation of Levels of Protection Analysis • Safety Instrumented Systems • Safety Requirement Specifications • Pre-Startup Safety Reviews • Regulatory Compliance assistance • LOPA analysis • Facilitates Facility Siting for six PSM cover processes at Sigma Aldrich CO, St. Louis, MO, USA. • Co-Facilitates HazOp and LOPA analysis for multiple units at Afton Chemicals Co., St. Louis, MO, USA. • Hazardous Processes analysis at Calvert City, KY, USA Show less
-
-
-
Procter & Gamble
-
United States
-
Manufacturing
-
700 & Above Employee
-
Material Planner & CFR analyst
-
Jul 2008 - Apr 2009
Ronan Joined Procter & Gamble as a summer trainee, Ronan had observed the following during her training period with Procter & Gamble: - WPI- Work process improvement strategies. - Overview about all the departments of the plant illustrating the policies, processes and requirements. - Site Integrating planning and QA/QC processes, including two weeks of on-hand SAP training. - Material Supply Management polices, and WH/ Global Material Development Supply organization processes. - Ronan was challenged with a project to integrate all SNO departments and to facilitate the integration among all five different departments; Ronan was giving three month to make it happen. In three weeks Ronan delivered her final product and tested it, it was the DDS stands for "Daily Direction Setting." Ronan was hired as full time employee there after. During her time as a professional employee, Ronan continues to deliver above and beyond the expectations and overachieve in her personal goals: - Deliver with excellence the PtQ (Produce to Quantity) campaign as a trainee. - Lead the safety training to 100% completion among the SNO users. - Manage and own the DDS- Daily direction setting- meeting in which all the SNO departments meet to discuss key measures. (Process improvement) – Saves Money - Leading a team from the plant, the general Office and the MDO to apply the CFR tool – Case Fill Rate – which measures costumers’ satisfaction and owned the system as a plant user. (Process improvement) – Saves Money Show less
-
-
Education
-
Villanova University
Master's degree, Project Management -
University of Missouri-Rolla
Master of Science (M.S.), Engineering/Industrial Management -
University of Missouri-Rolla
Certificate, Quality Engineering -
King AbdulAziz University
Bachelor of Science (BS), Chemistry
Community
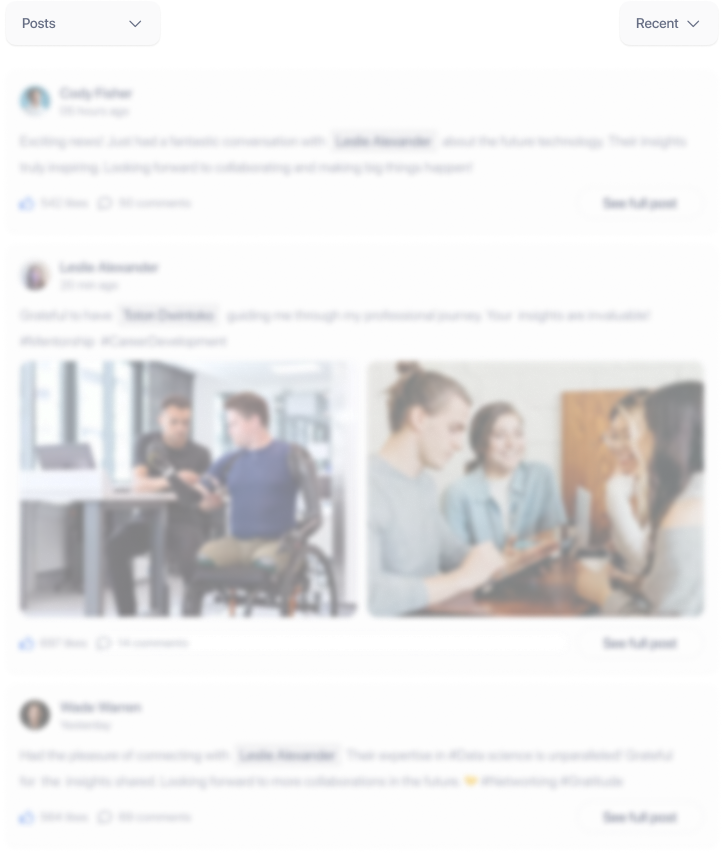