Ronald Fisher
Senior Facilities Engineer at Barrday Inc.- Claim this Profile
Click to upgrade to our gold package
for the full feature experience.
Topline Score
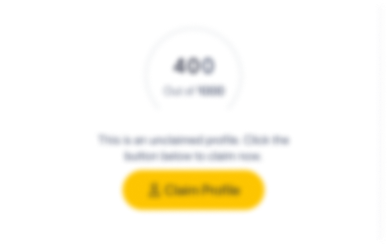
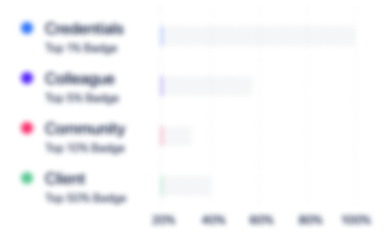
Bio


Experience
-
Barrday Inc.
-
United States
-
Manufacturing
-
1 - 100 Employee
-
Senior Facilities Engineer
-
Aug 2020 - Present
-
-
Process Engineer
-
May 2016 - Aug 2020
• Support manufacturing and facility maintenance including: o Working directly with the manufacturing team to implement new and support existing equipment o Participate in the development of new equipment specifications and procurement of parts and equipment o Accountability for Fluid Dynamic processes including air flow, facility air makeup and balancing ovens. o Maintenance of oxidizers, tenter frames, tower coaters, IR and natural gas ovens… Show more • Support manufacturing and facility maintenance including: o Working directly with the manufacturing team to implement new and support existing equipment o Participate in the development of new equipment specifications and procurement of parts and equipment o Accountability for Fluid Dynamic processes including air flow, facility air makeup and balancing ovens. o Maintenance of oxidizers, tenter frames, tower coaters, IR and natural gas ovens and general facilities o Ensuring proper preventative maintenance procedures are established and performed o Generation of working mechanical and electrical drawings with part specifications o Maintenance and expansion of contractor relationships o Providing operator training and hands on/standby support as needed • Provide support for multiple prepreg manufacturing lines focusing on: o Daily process monitoring o Maintenance of processing parameters o Achieving lot to lot consistency o Identifying and implementing opportunities for change-over time reduction o Creation and maintenance of standard operating procedures for equipment and processing tools o Capital budget and equipment project planning and timelines • Work with EH&S to maintain compliance with regulatory requirements • Work with Quality on Document Control and Contract Review to ensure proper setup and utilization • Perform ergonomic and hazard review on equipment • Assist facility in establishing lean manufacturing principles
-
-
-
Intel Corporation
-
United States
-
Semiconductor Manufacturing
-
700 & Above Employee
-
Process/Equipment Engineer
-
Mar 2015 - Feb 2016
Responsible for engineering support spanning Lithography track equipment ownership, project management, process monitoring and troubleshooting, yield improvement and day to day support of manufacturing activities. •Selected from Fab17 Mass for a business need to support the AZFSM LITHO BARC track area •Successfully owned 5 Litho BARC tracks including 2 Lithius tracks and 3 ACT 12 tracks on an unfamiliar site running a new cutting edge technology after only 2-3 weeks of hands on… Show more Responsible for engineering support spanning Lithography track equipment ownership, project management, process monitoring and troubleshooting, yield improvement and day to day support of manufacturing activities. •Selected from Fab17 Mass for a business need to support the AZFSM LITHO BARC track area •Successfully owned 5 Litho BARC tracks including 2 Lithius tracks and 3 ACT 12 tracks on an unfamiliar site running a new cutting edge technology after only 2-3 weeks of hands on training. •Utilized data mining and statistical analysis software such as SPC, KLARITY, SQL, and DART to maintain and improve product yield. •Recognized for safety improvement of COHE LOTO updates to SPEC. -Noticed the area SPEC procedures had many safety issues that needed correction and used extensive knowledge from Fab17 training for cross site training opportunity. -Had meetings with Corporate EHS to align on corporate and OSHA standards and expectations -Implemented updated SPEC procedures and trained 2 other area tool owners to proliferate these changes for all ACT12 track tool set SPECs.
-
-
Process/Equipment Engineer
-
Aug 2011 - Mar 2015
Responsible for engineering support activities which include Lithography TEL track equipment ownership, project work, process monitoring and troubleshooting, continuous improvement, and day to day support of manufacturing activities. •Used model based problem solving and design of experiments to troubleshoot and rebuild Tokyo Electron Limited adhesion module ovens that were failing across the Lithography track fleet. -The ability to repair these modules in-house resulted in a… Show more Responsible for engineering support activities which include Lithography TEL track equipment ownership, project work, process monitoring and troubleshooting, continuous improvement, and day to day support of manufacturing activities. •Used model based problem solving and design of experiments to troubleshoot and rebuild Tokyo Electron Limited adhesion module ovens that were failing across the Lithography track fleet. -The ability to repair these modules in-house resulted in a "per-module" savings of $35,000 and a total cost avoidance of over $400,000 in addition to the extensive downtime of critical production equipment and costly need to rework product •Developed and implemented a modification to Chilling Hot Plate module lid exhaust system to enable critical exhaust flow stability which reduced in-lot critical dimension variability by 50%. •Selected by management to lead a team of Equipment Techs to decontaminate and de-install three Tokyo Electron Limited (TEL) Act 8 tools for resale in order to both free up expensive fab space for future projects and to capitalize on an opportunity to sell equipment that was not being utilized. -Completed training in several proprietary decontamination and de-installation systems and used this knowledge to develop and execute project plan. -Ran the process as a LEAN boot-camp to develop a standardized process. -Project was completed before schedule enabling factory to receive a capital recovery through resale of $675,000. •Seized the opportunity to recover over $700,000 in spare parts from another Intel site by facilitating a spare part harvest project which included the organization of the recovery of TEL Clean Track parts. •Eight year member of the Intel Fab17 Emergency Response Team; responsibilities included life safety, incident stabilization, hazard mitigation and protection of property and environment
-
-
Equipment Specialist
-
Jul 2000 - Jul 2011
Responsible for maintaining and troubleshooting Litho TEL ACT8, ACT12 and SOG equipment • TEL Level 4 Up-skill Certified on the ACT 8 and ACT 12 TEL tracks • Worked an engineering rotation for two months which included being responsible for and owning 16 TEL ACT8 tracks, monitoring Best Tool Matching Process Control Systems, writing repair/troubleshooting game-plans, and tracking and containing any quality events in the area. • Recognized for troubleshooting and repair of extensive… Show more Responsible for maintaining and troubleshooting Litho TEL ACT8, ACT12 and SOG equipment • TEL Level 4 Up-skill Certified on the ACT 8 and ACT 12 TEL tracks • Worked an engineering rotation for two months which included being responsible for and owning 16 TEL ACT8 tracks, monitoring Best Tool Matching Process Control Systems, writing repair/troubleshooting game-plans, and tracking and containing any quality events in the area. • Recognized for troubleshooting and repair of extensive and challenging tool issues. • Attended TEL Level 2/3 training at the TEL site in Austin, TX. • Responsible for safely and efficiently troubleshooting TEL track issues to resolution while utilizing EEW certification and LOTO safety procedures. • Partnered with Engineering to resolve advanced issues on the equipment. • Led senior technicians and engineers from different Intel sites in a Virtual Fab audit to investigate current preventative maintenance (PM) procedures in order to explore new possibilities to improve safety, quality and tool availability.
-
-
Education
-
New England Institute of Technology
Associate of Science (AS), Electrical and Electronics Engineering -
Oxford High School
Community
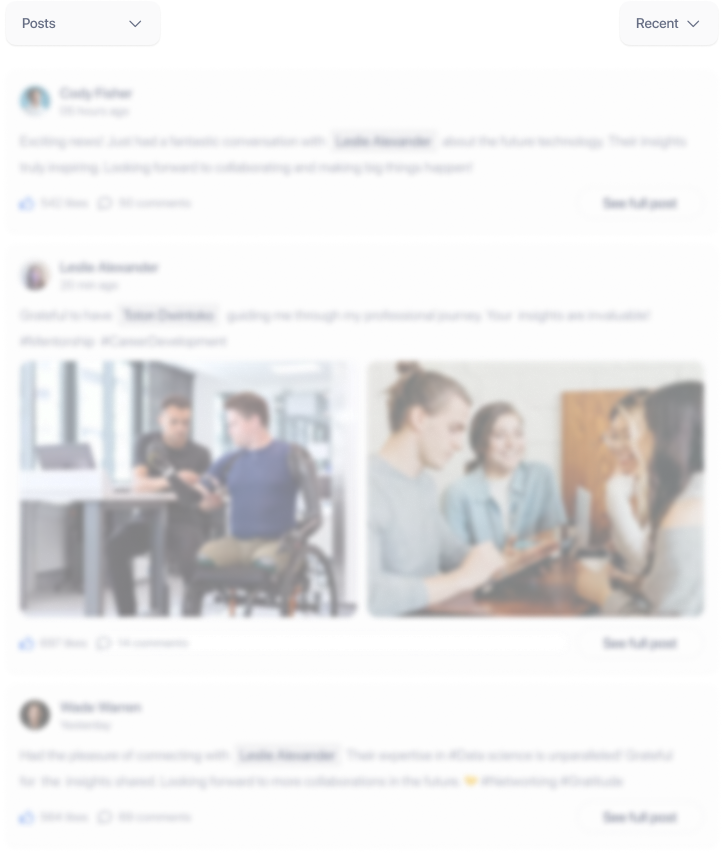