Ronald de Hoog
Manager Logistiek en Productie a.i. at QbiQ Wall Systems- Claim this Profile
Click to upgrade to our gold package
for the full feature experience.
-
Engels Full professional proficiency
-
Nederlands Native or bilingual proficiency
Topline Score
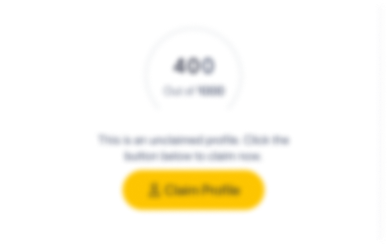
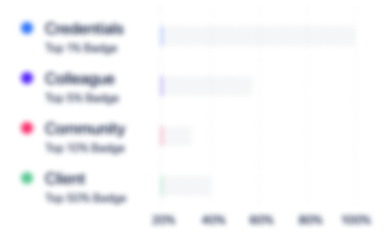
Bio


Credentials
-
Lean Green Belt
ICM opleidingen & trainingenFeb, 2017- Nov, 2024 -
VCA VOL
ARBO centrumApr, 2023- Nov, 2024
Experience
-
QbiQ Wall Systems
-
Netherlands
-
Wholesale Building Materials
-
1 - 100 Employee
-
Manager Logistiek en Productie a.i.
-
Apr 2023 - Present
-
-
-
UC Group_SC
-
Transportation, Logistics, Supply Chain and Storage
-
1 - 100 Employee
-
Interim Supply Chain / Logistics manager
-
Sep 2022 - Present
-
-
-
Royal FloraHolland
-
Netherlands
-
Transportation, Logistics, Supply Chain and Storage
-
700 & Above Employee
-
Operationeel Manager Logistiek
-
Jan 2023 - Apr 2023
-
-
-
PACCOR
-
Germany
-
Packaging and Containers Manufacturing
-
300 - 400 Employee
-
Supply Chain Manager
-
Nov 2019 - Aug 2022
Responsible for the overall supply chain activities of Paccor Netherlands B.V. including the short- and long-term Production planning, Procurement and stock management of raw materials, semi-finished products, packaging materials and traded goods, Logistics, transport and warehousing at both the Standdaarbuiten and Nijkerk location as well as all outsourced 3PL activities. In addition, responsible for further professionalizing the various operational processes (towards Operational Excellence), monitoring and steering on KPIs (OTIF, DIO), defining and achieving strategic objectives, chairing the S&OP, delivering various management reports for the local management team as well as Paccor Group Management. Achievements: * Relocation of the 2 production facilities in Nijkerk to Standdaarbuiten and all warehouse and storage activities in a fully operating environment; * Key player and driver of a Logistics outsource project (3PL) from tender phase to contract phase as a result of redesigning all logistics flows and functions of the various warehouses, with the aim of removing the logistical complexity and related costs. - * Key player and driver to implement a S&OP process , resulting in, among other things, better demand forecast accuracy, more accurate production- and personnel planning , stabilized machine utilization throughout the year, lower and accurate stocks of raw, semi- and finished goods, increased visibility and control of operating costs, increased OTIF * Reduction of stocks of finished products and traded goods (€4.5 million to €3.6 million, DIO reduction of 55 > 45 days) * Building a brand new and performing Supply Chain Team from scratch in a fully operating and changing organization Show less
-
-
-
ASSA ABLOY Opening Solutions
-
Wholesale Building Materials
-
700 & Above Employee
-
Operations Manager Nederland
-
Sep 2017 - Oct 2019
Responsible for all Production and Assembly activities, Logistics, Services and Repair and the VAS activities at a 3PL. Thereby ensuring the achievement of the qualitative and quantitative objectives (KPIs) within the set preconditions, coaching and training of the department heads and Operations planner, ensuring safety, hygiene and cleanliness in and around the various departments. Achievements: * Organizing and realizing relocation of the production and assembly lines, stocks and all related logistics activities from the former location in Apeldoorn to the current location in Raamsdonksveer. * Key pleyer for transforming the production and assembly department into a Late Configuration Hub (Strategic project) * Redesigning warehouse, including the installation of two Kardex Remstar cabinets, and the production and assembly area for maximum efficiency and flow based on the Lean methodology. * Introducing a weekly planning for production and assembly in combination with fixed sales lead times on all product groups with the aim of more clarity and transparency for the entire organization and customer ("Do what we promise"). The result is an increase in OFR from an average of 33% to 93% in a period of 4 months. * Organizing and realizing the transfer of non-value-adding assembly activities to 3PL Show less
-
-
-
-
Logistics Operations Manager
-
Jul 2015 - Sep 2017
Responsible for the entire logistics operation Benelux including the departments In-Outbound, Printshop (VAS), Logistics Administration, Rental and Services and Facilities. In addition, responsible for further professionalizing the various operational processes (towards Operational Excellence), monitoring and steering on KPIs, achieving the strategic objectives, the daily capacity planning and production planning, training and guidance of the team leaders, ensuring safety, hygiene and order and cleanliness in and around the various departments.Achievements:* Increasing the productivity and quality of the Printshop department through process optimizations according to Lean methodology, including standard work instructions, creating standard workplaces, implementing quality controls and various small adjustments wms process. As a result, On Time percentage increased from 43% to 96% and averaged number of prints per person per hour from 26 to 53 with an increased workload. * Redesigning the Outbound department based on Lean methodology, including creating more flow on consolidation, packaging and shipping, which has resulted in a higher throughput of collected orders. This also resulted in improved safety by eliminating traffic bottlenecks in the supply and discharge routes. Also standardization workplaces by means of 5S methodology. * Creating a disciplined, structured and motivated team on both In-Outbound and the Printshop from a very undisciplined and unmotivated group of employees. * Tender process and realization replacement of all internal means of transport* Drawing up and implementing a Warehouse Traffic Plan, including signage in and around the warehouse, lines, traffic rules internal transport and house rules for staff and visitors. Show less
-
-
Warehouse Manager
-
Feb 2014 - Jul 2015
Responsible for the departments Inbound, Outbound and Printshop (VAS), further professionalizing the various operational processes (towards Operational Excellence). In addition, responsible for all facility matters, cycle counts, daily capacity planning, training and guidance of the team leaders, ensuring safety, hygiene and order and cleanliness within the warehouse.
-
-
-
Bowltech International BV
-
Made, The Netherlands
-
Logistics Manager
-
Dec 2012 - Feb 2014
Responsible for the logistics operation including the Logistics department (warehouse, stock management, returns, export and transport) and a shared responsibility over the Customer Service department. In addition, responsible for the further professionalization of all logistics and operational processes within Bowltech International B.V. Achievements: * Integrating the various stand-alone SAP administrations (Master Distributorships) into a single SAP administration including merging the various customer service departments into one department. * Restructuring the warehouse to achieve the most efficient operational process possible from inbound to outbound, including the implementation of location codes and the use of scanners * Determining and implementing KPIs, which in a time frame of 1.5 months has already led to an increase in the on-time percentage from 84% to 92%. Show less
-
-
-
-
Logistics Manager
-
Sep 2010 - Dec 2012
Responsible for the entire logistics operation within the EMEA region (warehouse, import, export, inventory management, purchasing, returns and transport) with a shared responsibility for the Customer Service department and the Warranty and Exchange department. In addition to the Department in Rotterdam, Customer Service also included the Customer Service departments of the office in France, England, Germany and Italy.Achievements:* Key role in implementing JD Edwards within the Rotterdam branch and the European sales offices. * Establishing, developing and maintaining long-term relationships with Logistics service providers, including UPS and Dachser.* Initiating several successful projects within the Rotterdam location. As an example, a reduction in the time required for entry (from an average of 4 days to 1 -2 days) by making good agreements with the suppliers about the way and loading of the containers and the packaging of the orders. Also in the warehouse a higher efficiency was realized by following the 5S method. Show less
-
-
Logistics Specialist
-
Jan 2007 - Sep 2010
Responsible for creating purchase orders through a professional prediction module, monitoring and updating the outstanding purchase orders, placing orders with the various suppliers on time, monitoring deliveries, optimizing the total stock level, managing item master data, arranging international and national transports by truck (especially for turnkey bowling projects the so-called modernizations), aircraft or boat, the preparation and processing of the entry into storage, the financial processing of the entry into storage, the preparation of the necessary documents for customs formalities. Show less
-
-
Warranty administration
-
Jul 2006 - Jan 2007
Responsible for the correct and timely administrative handling of warranty claims and shortages with regard to completed installation projects or projects that were still installed at that time as well as arranging the returns and the administrative handling thereof. Also responsible for scheduling, coordinating Cycle Counts. as well as the processing in the ERP system (Navision).
-
-
Education
-
Hogeschool voor Economische Studies Rotterdam (HES)
Bachelor's degree, Logistiek en Supply Chain Management, specialisatie Inkoop -
NCOI University of Applied Sciences
Professional master, Logistics, Materials, and Supply Chain Management -
Havo / De Ring van Putten
Community
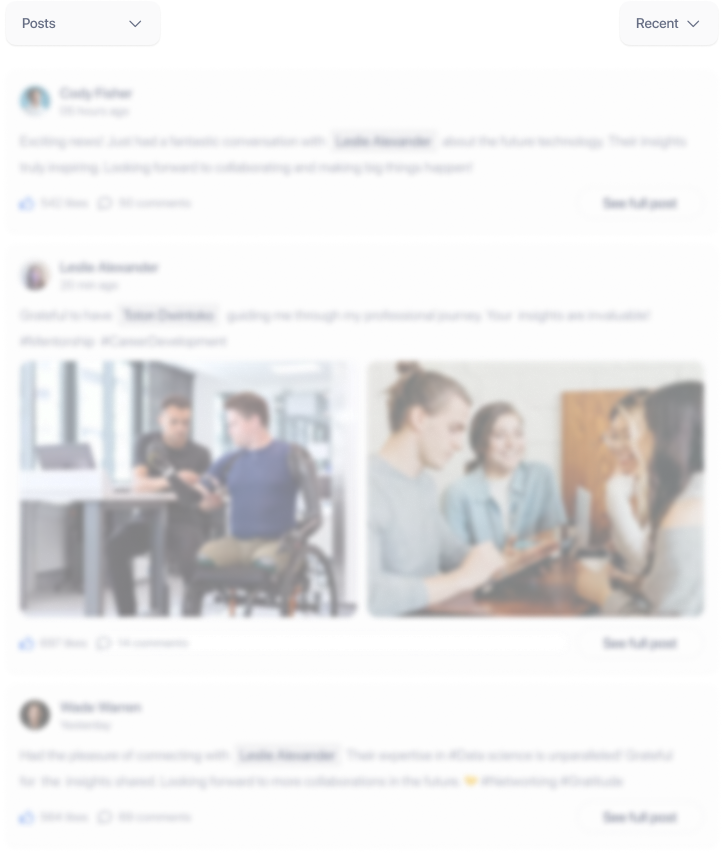