Ron Wieder
Supervisor at Blue Ridge Pressure Casting, Inc.- Claim this Profile
Click to upgrade to our gold package
for the full feature experience.
Topline Score
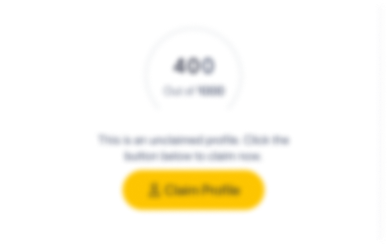
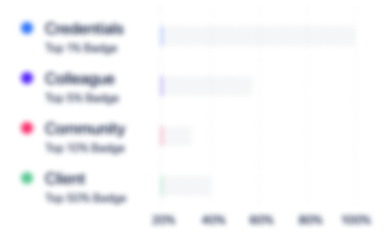
Bio


Experience
-
Blue Ridge Pressure Casting, Inc.
-
Machinery Manufacturing
-
1 - 100 Employee
-
Supervisor
-
May 2023 - Present
-
-
-
SIMOS Insourcing Solutions
-
United States
-
Business Consulting and Services
-
400 - 500 Employee
-
Operations Supervisor
-
Aug 2016 - Present
-
-
Operations Manager
-
Mar 2017 - May 2023
-
-
-
Continental
-
Germany
-
Motor Vehicle Manufacturing
-
700 & Above Employee
-
Materials Analyst
-
Aug 2015 - Aug 2016
Responsible for planning scheduling and monitoring of tasks for the logistics department on 2nd shift customer and shipping requirements, create material transfers ,material consolidations help to determine efficient utilization of manpower to meet customer demands both internal and external. Focus on KPI’s for delivery performance, Inventory levels and storage utilization, Post Goods issued daily into SAP. Support Safety, Quality and Lean process. Work closely with first shift Shipping Supervisor to ensure we are achieving our daily shipping goals. Manage Ozark Back orders Show less
-
-
-
VOLVO GROUP TRUCKS OPERATIONS (MACK TRUCKS INC.)
-
Macungie Pa
-
Materials Coordinator
-
Jan 2015 - Jul 2015
• Generation of orders for pick/pack delivery to main production lines • System monitoring to ensure order completion determined by the daily production schedule • Data collection using Access database software to monitor and track shift efficiencies • Assisting warehouse lead in coordination of freight shipments for timely delivery to main production lines • Critical communication to warehouse lead regarding ordering system issues to avoid production line stoppage • Communication with production supervision and warehouse lead ensuring delivery of critical schedule changes completed and ordering system is closely maintained Show less
-
-
-
DSC Logistics
-
United States
-
Transportation, Logistics, Supply Chain and Storage
-
700 & Above Employee
-
Quality Assurance Team Lead
-
Jan 2014 - Dec 2014
• Evaluate product holds and add and remove hold codes within WMS as directed and needed for daily operations • Segregate product as needed for various types of holds until product is evaluated for return or release • Strong knowledge of Microsoft Excel • Conduct audits of locations after employee picking to ensure proper counts of product • Perform employee performance observations and conduct on the job as well as formal coaching sessions to discuss the employees performance • Monitor the progress of daily inbound and outbound loads while communicating any issues to other LM’s • Daily use of WMS in both a user and manager capacity • Communicate with customer daily on various issues from product holds, to transportation updates • Communicate all issues, to include safety, productivity and volumes to other LM’s • Ensure that employees adhere to DSC’s Best Practices while promoting DSC’s culture of safety • Foster a participative and goal-driven work environment characterized by teamwork, partnership and accountability for achieving goals Show less
-
-
-
Cordell Transportation Company LLC
-
United States
-
Transportation/Trucking/Railroad
-
1 - 100 Employee
-
Director of Operations
-
Mar 2012 - Dec 2013
• Managed Detroit Terminal and assisted with the main terminal operations central dispatch out of Dayton Ohio to encompass a fleet of 150 trucks 250 drivers 22 office support personnel. • Maintained safety as well as driver compliance, truck utilization, fuel consumption and on time delivery • Maintained metrics, KPI’s daily, weekly and monthly • Conduct audits of locations after employee picking to ensure proper counts of product • Participated in customer contact both internally and externally • Worked with managers to hire and retain drivers, engineer route design and maintain driver fast certification for drivers going into Canada Show less
-
-
-
-
Account Manager
-
May 2010 - Feb 2012
Responsible for Yard Management and Shuttle operations to include 500 inbound and outbound Carriers on a daily basis, 40 to 60 private shuttles per day to and from cold and dry storage. Managed 3 Supervisors, 9 dispatchers, 11 Clerks, and 40 drivers. While maintaining a Safe work environment and giving world class service to our partner in the business, tracked daily on time percentage Manage overtime and equipment cost. Communicate daily with the customer as issue arise Manage KPI's daily weekly and monthly. Show less
-
-
-
Penske Logistics
-
United States
-
Truck Transportation
-
700 & Above Employee
-
Project Leader
-
Aug 2008 - May 2009
Lead successful launch of GMSPO Philadelphia within 45 day time constraints while maintaining customer satisfaction. Coordinated efficient equipment allocations across our network Tractors, Trailers, and Office equipment for new start-up. Within a five state area Trained All Operations staff in Philadelphia, Office and Dock associates Set up Transportation claims data base and negotiated settlements Trained site Manager on KPI'S, AS 400 and financial, Safety, and Productivity reportingMaintained P.O Log Monitored daily metric reporting to both internal and external customers.Route optimization for network. Show less
-
-
Logistics Center Manager
-
Apr 2007 - Aug 2008
Full P&L responsibility, Safety Quality, and ProductivityManaged a 12 million dollar per year account to include 70 UAW drivers, 30 UAW dock workers, and 9 administration staff.Operated in 3 states with 9 outer domicile locations.Successfully moved buildings without interruption or negative impact to the customer or the operation.Successfully shut down the operation without interruption to the customerRedeployed Equipment to support new business in Philadelphia. Daily Metric reportingCustomer ServiceResponsible for route designs and bidding of routes bi-annually Claims Management and negotiated Quartly settlementsKPI'S daily, weekly, and Monthly Show less
-
-
Logistics Center Supervisor
-
Jun 2006 - Mar 2007
Managed 40 outbound routes 25 inbound shuttles for the dedicated delivery for General Motors SPO for a total of 544 daily deliveries Eliminated waste by staggering the outbound teams shift times, increased productivity, and controlled cost. Maintained Quality and Safety. Lead and develop 2 dock leads. Supervise 16 UAW dock associates Maintain Safety regulatory items, trained all drivers on Hazmat awareness, Developed a safety cabinet for all regulatory items, train dispatchers on a continuous basis, Implemented cost savings ideas (redesign s for continuous improvement, maintain data base for all routes and associated dealerships) Show less
-
-
-
-
Plant Manager
-
Mar 2005 - Jun 2006
Manage day-to-day operations of $16 million per year facility. Responsible for Insuring health and safety of facility and maintaining high standards of Productivity while incorporating lean concepts and driving down cost in Materials and labor. Full P&L responsibilty Accountable for 9 production lines building frame chassis for the RV industry. Responsible for materials management including ordering of all steel and Fabricated, and non-fabricated parts. While reducing cost and scrap. Oversee and monitor Powder Coat Paint Application Department, which powder coated 6,000 frames per month on average. GENERAL MOTORS SERVICE PARTS OPERATIONS Drayton Plains, MI Show less
-
-
-
General Motors
-
United States
-
Motor Vehicle Manufacturing
-
700 & Above Employee
-
Operations Manager
-
Mar 2003 - Feb 2005
Lead and developed team of 8 salaried first-line supervisors Encompassing 160 hourly employees and 6 production departments.Monitored and oversaw process for selection of new salaried employees. Monitored performance of team in meeting and exceeding facility metric goals in Receiving and Raw Materials Departments while driving down cost. Maintained inventory integrity and accuracy; resulted in plant finishing Annual Physical Inventory first (amongst division) in 2001, 2002 and 2004. This Reduced man-hours for indirect activity.Maintained and exceeded metric standards in Safety, Quality, and Housekeeping Through continuous improvement.Met weekly 100% schedule requirements, including overtime scheduling to meet Customer demands.Proactively worked with suppliers to speed shipments in avoidance of parts Becoming backordered; success rate evident in achievement of metric goals.Developed/ implemented metric measurements to gauge priority completion.Participated in and oversaw daily Quality Wall Show less
-
-
Operations Manager
-
Mar 2001 - Mar 2003
Shipping and Service Warehouse DepartmentsLead/ developed team of 6 salaried first-line supervisors and 90 UAW hourly Employees.Monitored performance of team in meeting and exceeding metric goals in parts Picking productivity and replenishment for Parts Distribution Centers.Planned, executed and directed the Annual Physical Inventory of over 26,000 part numbers for years
-
-
-
General Motors
-
United States
-
Motor Vehicle Manufacturing
-
700 & Above Employee
-
first line Supervisor
-
Jan 1995 - Jan 2001
Ran Various production and warehousing departments while maintaining safety, Quality, and Productivity, managed 25 to 40 UAW associates within these departments within the parts distribution center Ran Various production and warehousing departments while maintaining safety, Quality, and Productivity, managed 25 to 40 UAW associates within these departments within the parts distribution center
-
-
Education
-
Baker College
Community
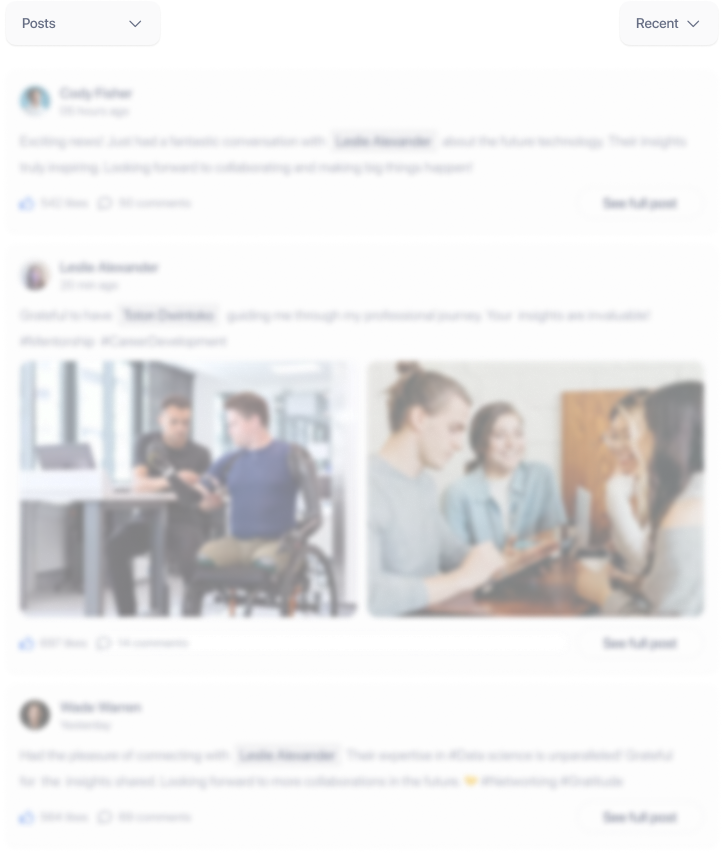