Ron Wertz
Quality Control Specialist at Volvo Car USA- Claim this Profile
Click to upgrade to our gold package
for the full feature experience.
-
French Professional working proficiency
Topline Score
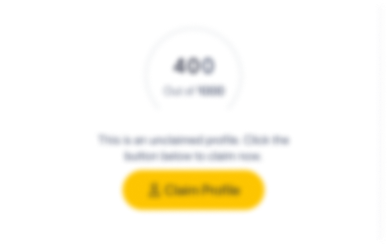
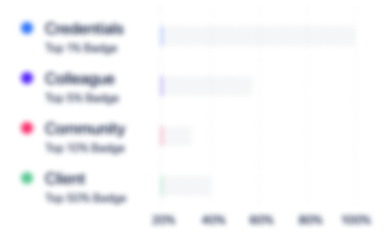
Bio


Credentials
-
Lean Six Sigma White Belt Certification
VolvoDec, 2018- Nov, 2024 -
Six Sigma Black Belt Certification – Level I
Mercedes-Benz Vans, LLC (Charleston, SC)Oct, 2018- Nov, 2024 -
Teaching License-Standard
TeachMay, 2012- Nov, 2024
Experience
-
Volvo Car USA
-
United States
-
Motor Vehicle Manufacturing
-
300 - 400 Employee
-
Quality Control Specialist
-
Oct 2019 - Present
• Develop prioritization plans for the delivery of products, services, and data • Execute compliance tasks and make corrections and modifications • Consul with management and ensure effective production methods were employed • Performs root cause analysis on the nonconformance to identify the cause and prevent reoccurrence. Inspect products for quality and adherence to build specifications. • Collect and interprets data to adhere to applicable regulations, policies, and procedures for health, safety, and environmental compliance. Train and mentor peers • Develop, modify and document actions to assure problem resolution • Review and validates product non-conformance and disposition type, quality procedures, and engineering requirements. • Performs analyses to identify and evaluate the quality of products, operations, and processes to Quality Management System requirements, per company’s procedure, contract requirement, or government regulations. Show less
-
-
-
Volvo Cars Charleston Plant
-
United States
-
Motor Vehicle Manufacturing
-
300 - 400 Employee
-
Assembler
-
Jan 2019 - Oct 2019
-
-
-
Mercedes-Benz USA
-
United States
-
Motor Vehicle Manufacturing
-
700 & Above Employee
-
Paint Technician
-
Oct 2018 - Jan 2019
• Retrieved and provided material, work pieces, tools, work documents, device parts, auxiliary materials, etc. according to the specified min/max stock. Arranged for disposal/treatment. • Prepared the workplace for manual activities ensuring that the area is clean, organized and up to 5S standards • Prepared cars and car bodies for paint process • Masked/unmask parts and car bodies and areas to be coated • Sprayed wax for cavity preservation • Performed visual inspection for completeness and proper execution of standard and record defects into the quality reporting system • Sealed interior and exterior seams • Sprayed or layed out PVC protection and sika, taking into account the required surface quality on the visible parts of the shell • Fixed minor issues with paint tools/equipment (such as through filter cleaning, changing of nozzles) • Monitored and controlled coating/painting processes • Set order sequence • Analyzed end-of-process items, and adjust the coating process accordingly • Monitored production flow and buffer levels • Coordinated with upstream/downstream areas • Proposed corrective measures for bottleneck situations, and coordinate with the foreman if necessary • Accumulated manufacturing data and evaluate • Analyzed system errors, if necessary by the use of diagnostic systems. Identify vulnerabilities in advance • Developed and implement corrective measures • Carried out spot repairs (partial surface repair/coating) • Adhering to painting standards, inspect, detect, classify, determine corrective measures and fix localized damage and defects outside of the normal painting process • Acted as the final coatings/paint quality point, and conduct repair work so the product will be released to the customer • Refinished seam seals for finished painted vehicles • Participated in the Continuous Improvement Program Show less
-
-
-
Colleton County High School
-
United States
-
Education Administration Programs
-
1 - 100 Employee
-
Teacher
-
Jun 2015 - Oct 2018
-
-
-
Jasper County High School
-
United States
-
1 - 100 Employee
-
Teacher
-
Aug 2014 - Jun 2015
-
-
-
Montgomery County Public Schools
-
United States
-
Primary and Secondary Education
-
700 & Above Employee
-
Learning and Academic Disabilities Paraeducator
-
Oct 2013 - Jun 2014
-
-
-
Howard Community College
-
United States
-
Higher Education
-
700 & Above Employee
-
Adjunct Professor
-
Aug 2011 - May 2014
-
-
-
Lycée Romain Rolland
-
Paris Area, France
-
Assistant d’Anglais
-
Sep 2007 - Apr 2008
-
-
-
WestPoint Stevens
-
Textile Manufacturing
-
1 - 100 Employee
-
Team Leader
-
Apr 2002 - Apr 2004
Part of a hardworking team and had the opportunity to learn and grow alongside a group of supportive and respectful individuals. Provided with opportunities to learn new skills, become a leader, and advance in career goals. Practiced Lean manufacturing and embraced new perspectives that improved the way we did things. Tasked with running a 100-yard fabrication machine, drove gas and electric forklifts as well as A-frame tuggers, and inspected rolls of cloth for color and texture tolerances. Part of a hardworking team and had the opportunity to learn and grow alongside a group of supportive and respectful individuals. Provided with opportunities to learn new skills, become a leader, and advance in career goals. Practiced Lean manufacturing and embraced new perspectives that improved the way we did things. Tasked with running a 100-yard fabrication machine, drove gas and electric forklifts as well as A-frame tuggers, and inspected rolls of cloth for color and texture tolerances.
-
-
-
Li'l Cricket Food Stores, Inc.
-
United States
-
1 - 100 Employee
-
Manager
-
Jan 2000 - Apr 2002
Emphasized duties like liaising with loyal customers, contacted suppliers, negotiated pricing and contract terms and conditions, budgeting. Implemented safety policies, conducting risk, issues and opportunities management, recruited staff, and maintained inventories. Integrated internal partners, customer, product and in-service strategies into source selection, negotiation and contracting strategies. Managed supply and demand, schedules, supplier quality, delivery and financial performance, Initiating and executing supplier improvement activities and integrates results. Show less
-
-
-
Bass Hotels and Resorts
-
Charleston, South Carolina Area
-
Call Center Agent
-
Jan 2000 - Dec 2000
Obtained client information by answering telephone calls; interviewed clients; verified information. Determined eligibility by comparing client information to requirements. Established and followed policies; confirmed pricing. Informed clients by explaining procedures; answered questions; provided information. Maintained communication equipment by reporting problems. Maintained and improved quality results by adhering to standards and guidelines; recommended improved procedures. Updated job knowledge by studying new product descriptions; participated in educational opportunities. Accomplished sales and organization mission by completed related results as needed. Show less
-
-
-
BI-LO
-
Retail Groceries
-
700 & Above Employee
-
Manager
-
Dec 1998 - May 2000
Front End Supervisors coordinated and trainned Front End Clerks. Supervised employees, provided customer service, monitored sales, enforced company policy and regulations, solved crises, and assigning other duties as needed. Front End Supervisors coordinated and trainned Front End Clerks. Supervised employees, provided customer service, monitored sales, enforced company policy and regulations, solved crises, and assigning other duties as needed.
-
-
Education
-
Charleston Southern University
Bachelor's degree, Secondary Education and Teaching
Community
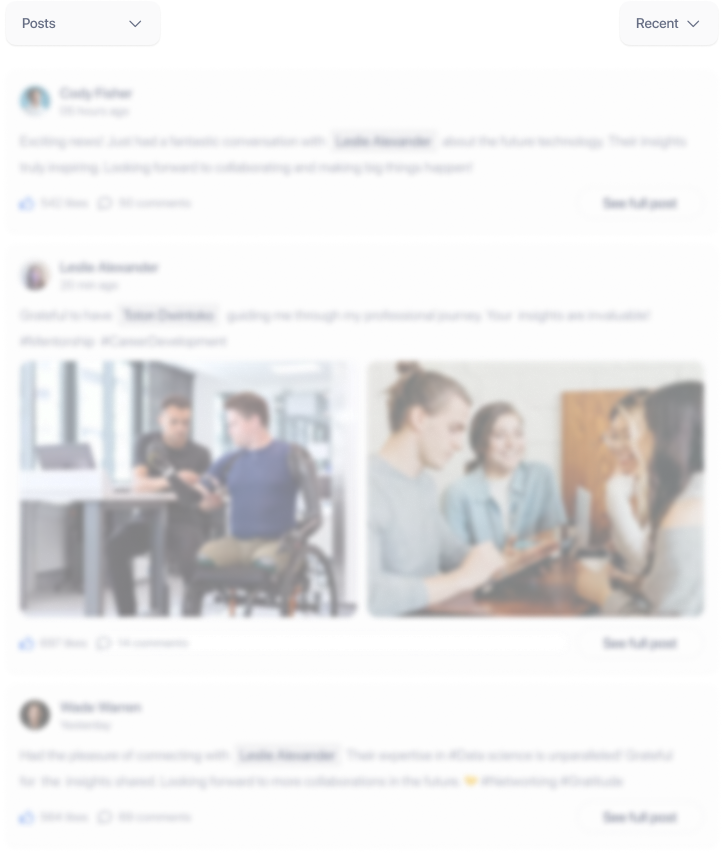