Ron McCollum
Vice President, Corporate Quality Assurance at Keystone Powdered Metal Company- Claim this Profile
Click to upgrade to our gold package
for the full feature experience.
Topline Score
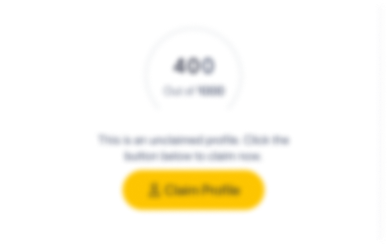
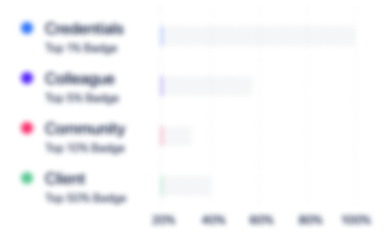
Bio


Credentials
-
ASQ Supplier Auditing & Nonconformances
ASQ - World HeadquartersOct, 2012- Nov, 2024 -
ASQ Certified Quality Improvement Associate
ASQ - World HeadquartersDec, 2007- Nov, 2024 -
ISO 9001 Lead Auditor - Quality Certification
Avery Dennison Label and Packaging MaterialsJun, 2004- Nov, 2024 -
Six Sigma Greenbelt Certification
Avery Dennison Label and Packaging MaterialsMay, 2001- Nov, 2024 -
OSHA: The Complete Compliance Workshop
US DEPARTMENT OF LABOR OSHAMay, 1999- Nov, 2024 -
Basic/Advanced Ergonomics
The University of ToledoJan, 1997- Nov, 2024
Experience
-
Keystone Powdered Metal Company
-
United States
-
Motor Vehicle Manufacturing
-
1 - 100 Employee
-
Vice President, Corporate Quality Assurance
-
Aug 2023 - Present
-
-
-
Ultium Cells LLC
-
United States
-
Manufacturing
-
300 - 400 Employee
-
Quality Systems Manager
-
Apr 2023 - Aug 2023
Initial focus on co-development of Ultium Cells, LLC company-wide Quality Management System. Preparations made for multi-site deployment and successful IATF 16949 certification.
-
-
Launch Team, Operations Leader, Electrode/Cell Assembly
-
Jul 2022 - Apr 2023
• Ultium Cells is a joint venture between GM and LG Energy Solutions that mass-produces Ultium battery cells for all GM electric vehicles (ie; GMC Hummer EV, Cadillac LYRIQ. Chevy Silverado EV and others).• Recently led both Cell Assembly, Electrode Operations, and OEM Teams from launch to production phase. Drove execution in areas of Leadership Development, Employee Training, and Continuous Improvement.
-
-
-
Axium Packaging, LLC
-
New Albany, Ohio, United States
-
Senior Manager, Quality Assurance
-
Mar 2021 - May 2022
• Managed company-wide quality assurance program, while serving in direct customer-facing role for key customer accounts (Procter & Gamble, Johnson & Johnson, L Brands and others). • Decreased rework by 35% resulting in a company savings of approx. $250,000 in annual production costs by working collaboratively to decrease customer claims and drive sustainable corrective actions. • Implemented Lean Management directives, which cut overall operating cost by 15%, while focusing on other continuous improvement and cost-saving initiatives. Show less
-
-
-
Avery Dennison Label and Packaging Materials
-
United States
-
Manufacturing
-
700 & Above Employee
-
Divisional Quality Systems Leader
-
Dec 2016 - Jun 2020
Successfully led Divisional Quality Team in ISO transition from 9001:2008 to 2015 standard by overhauling the Quality Manual, Divisional Documents and Internal Quality Audit content. • Effectively directed the Internal Quality Audit Team resulting in sustained compliance to the ISO 9001:2015 standard for duration of time as Divisional Quality System Leader. Responsibility spanned across a 25-person audit team with oversight of multiple divisions comprised of 18 manufacturing locations including 500+ employees stationed at divisional headquarters.• As Divisional Quality System Leader and owner of Divisional Document Control. led a cross functional team focused on improving overall employee training participation. Priority was placed on system alerts, procedural revisions and streamlining the overall process. The project resulted in a 38% increase in the employee training qualification rate. Show less
-
-
Divisional Quality Consultant
-
Sep 2013 - Nov 2016
Effectively and efficiently managed Midwest/West Coast territories acting as technical resource for key customer accounts. This included oversight of international distribution centers in Asia Pacific and S.A.• Consistently exceeded Divisional Quality metrics as they related to customer satisfaction survey, claim resolution and corrective action timeliness and effectiveness.• As Divisional Lead ISO Quality Auditor, I successfully led Internal Audits in the Midwest, West Coast and Canadian facilities with all meeting or exceeding ISO 9001 standards. Show less
-
-
Quality Assurance Specialist, Medical Devise
-
Apr 2012 - Sep 2013
Promoted to Quality Assurance Specialist within Avery Dennison’s Medical Solutions Division. Initial accomplishments include enhancing medical device inspections and establishing procedures to better manage medical device retains.• Drove improvements in the area of Supplier Management by assuming responsibility of medical suppliers (NCR/SCAR/CAPA). Additional process improvements made in the areas of customer claim resolution, loss reduction and management of material review board (MRB).• Acquired good working knowledge of ISO 13485 and FDA Regulations, GDP, and cGMP. Show less
-
-
Quality Systems Specialist
-
Sep 2010 - Sep 2012
• Effectively managed site quality systems as they related to Customer Response, Supplier Management and Operations Support. Most notable achievements include implemented the Customer Response Team. As site CAR Coordinator I maintaining one of the Division’s best CAL timing percentages for coating or finishing combined. Additionally, I have a history of driving results with suppliers in the areas of claim and credit resolution. • Key contributor in the effort to expand the Divisional Internal Audit Program by training and mentoring numerous auditors. As Lead Auditor, I established myself quickly by getting favorable results and improvements out of site management. This was achieved by ensuring sites implemented long term sustainable corrective actions.• Collectively revised site Quality Participation Program. Results included a noticeable shift in the quality culture as employees became actively involved through audits and inspections. • Collaborated with Divisional team as pilot site in development of the Global Supplier Scorecard (data collection phase).• Actively managed site lab calibration services by setting frequencies and coordinating calibration schedule. Also managed specialized lab equipment and tests as required for customer and supplier investigations. This included the management and testing of production samples, traceability and historical process data. Show less
-
-
Senior Quality Analyst
-
Apr 2004 - Sep 2010
• Participated on numerous Divisional and site Kaizen Teams with the most notable event and accomplishment being the reduction of customer corrective action response time from an average of 45days to under 10days Division wide. • Partnered with key suppliers to develop solutions that met customer specifications and requirements. Worked closely with product managers to establish visual standards and spec revisions utilized to meet “fit for use” criteria.
-
-
Operations Team Leader
-
Apr 2003 - Apr 2004
Promoted to Team Leader position with 15 direct reports. Responsibilities included management and reporting of site business metrics. Also managed preventative maintenance and production activities including staffing and conflict resolution.
-
-
Operations Specialist
-
May 1995 - Apr 2003
• Developed specialized knowledge of pressure sensitive products and specifications over a span of nine years in operations. Acquired a deep skill base for troubleshooting film/film and film/paper products with respect to web handling, film conditioning, corona treatment and adhesive coating. • Facilitated site wrinkle reduction efforts by collectively establishing wrinkle audit forms utilized to proactively detect pre-wrinkles and troughs in the coating process. • Collectively developed and managed Behavioral-Based Safety process for Cleveland Films Facility. Was later appointed as divisional leader to implement the behavioral based safety process program across NA manufacturing locations.• Performed preventative maintenance for all assets establishing a good working knowledge of machine alignment, load cell calibration and die set-up. Show less
-
-
-
Lincoln Electric
-
United States
-
Machinery Manufacturing
-
700 & Above Employee
-
Production Control Specialist
-
May 1994 - May 1995
-
-
-
Kenco Group
-
United States
-
Truck Transportation
-
700 & Above Employee
-
Quality Assurance
-
Apr 1991 - Apr 1994
-
-
-
Magnetic Springs Water Company
-
United States
-
Food & Beverages
-
1 - 100 Employee
-
Quality Control
-
Mar 1989 - Apr 1991
-
-
Community
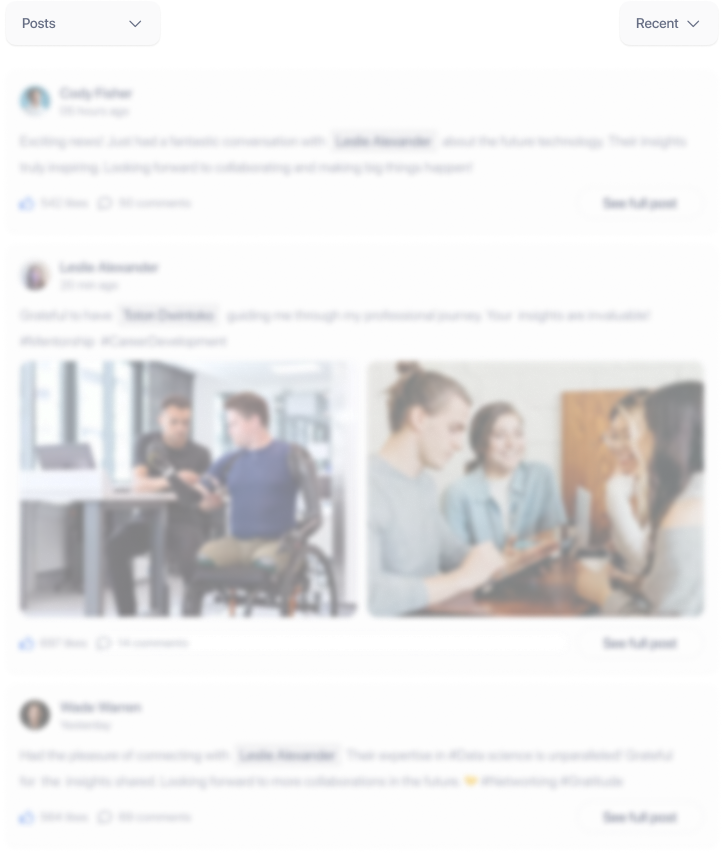