Roman D'Alessandro
Technical Director at Fairfield Processing Corporation- Claim this Profile
Click to upgrade to our gold package
for the full feature experience.
Topline Score
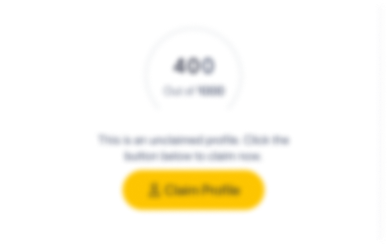
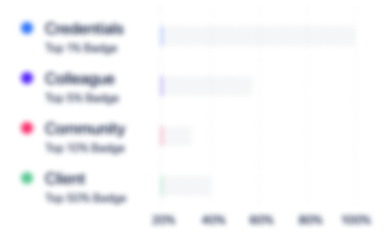
Bio

Ann K. Driscoll
I've had the pleasure of working closely with Roman during our time together at Fairfield. He is an outstanding professional with a strong work ethic and a remarkable ability to solve complex problems and drive innovation. His dedication and contributions have been instrumental in our team's success, and he will be greatly missed. Beyond Roman’s professional expertise, he is also a fantastic colleague and a pleasure to work with. He brings positivity and teamwork to every project. I have no doubt that Roman will excel in his future endeavors, and I look forward to seeing all the great achievements ahead. Wishing him the very best in his new chapter!

Manfredi Julie
Roman is a true master of his art. As technical director, he guided our team to achieve the high standards and quality we promised our customers. His attention to detail and tenacity for the truth is second to none. Professional, Focused, driven, respectful and most of kind and compassionate. It was an absolute pleasure working with Roman.

Ann K. Driscoll
I've had the pleasure of working closely with Roman during our time together at Fairfield. He is an outstanding professional with a strong work ethic and a remarkable ability to solve complex problems and drive innovation. His dedication and contributions have been instrumental in our team's success, and he will be greatly missed. Beyond Roman’s professional expertise, he is also a fantastic colleague and a pleasure to work with. He brings positivity and teamwork to every project. I have no doubt that Roman will excel in his future endeavors, and I look forward to seeing all the great achievements ahead. Wishing him the very best in his new chapter!

Manfredi Julie
Roman is a true master of his art. As technical director, he guided our team to achieve the high standards and quality we promised our customers. His attention to detail and tenacity for the truth is second to none. Professional, Focused, driven, respectful and most of kind and compassionate. It was an absolute pleasure working with Roman.

Ann K. Driscoll
I've had the pleasure of working closely with Roman during our time together at Fairfield. He is an outstanding professional with a strong work ethic and a remarkable ability to solve complex problems and drive innovation. His dedication and contributions have been instrumental in our team's success, and he will be greatly missed. Beyond Roman’s professional expertise, he is also a fantastic colleague and a pleasure to work with. He brings positivity and teamwork to every project. I have no doubt that Roman will excel in his future endeavors, and I look forward to seeing all the great achievements ahead. Wishing him the very best in his new chapter!

Manfredi Julie
Roman is a true master of his art. As technical director, he guided our team to achieve the high standards and quality we promised our customers. His attention to detail and tenacity for the truth is second to none. Professional, Focused, driven, respectful and most of kind and compassionate. It was an absolute pleasure working with Roman.

Ann K. Driscoll
I've had the pleasure of working closely with Roman during our time together at Fairfield. He is an outstanding professional with a strong work ethic and a remarkable ability to solve complex problems and drive innovation. His dedication and contributions have been instrumental in our team's success, and he will be greatly missed. Beyond Roman’s professional expertise, he is also a fantastic colleague and a pleasure to work with. He brings positivity and teamwork to every project. I have no doubt that Roman will excel in his future endeavors, and I look forward to seeing all the great achievements ahead. Wishing him the very best in his new chapter!

Manfredi Julie
Roman is a true master of his art. As technical director, he guided our team to achieve the high standards and quality we promised our customers. His attention to detail and tenacity for the truth is second to none. Professional, Focused, driven, respectful and most of kind and compassionate. It was an absolute pleasure working with Roman.

Experience
-
Fairfield Processing Corporation
-
United States
-
Manufacturing
-
1 - 100 Employee
-
Technical Director
-
Jun 2020 - Present
Experienced champion of lean principles to lead product development & improvement teams to create revenue. Experienced champion of lean principles to lead product development & improvement teams to create revenue.
-
-
-
Inline Plastics
-
United States
-
Packaging and Containers Manufacturing
-
200 - 300 Employee
-
Manager New Product Design
-
Oct 2015 - Jun 2020
All aspects of new product development, from Client facing meetings, design, prototyping, 1 UP sampling, production tools for release to Production. NPI process refinement for optimum speed and accuracy. Cross functional leadership to align corporate assets toward our goal of being the most responsive and creative supplier in the plastic food packaging market. Lean Six Sigma Black Belt level achieved. Blue Ocean Strategy Team member. Patent #D850,249 awarded as Inventor. All aspects of new product development, from Client facing meetings, design, prototyping, 1 UP sampling, production tools for release to Production. NPI process refinement for optimum speed and accuracy. Cross functional leadership to align corporate assets toward our goal of being the most responsive and creative supplier in the plastic food packaging market. Lean Six Sigma Black Belt level achieved. Blue Ocean Strategy Team member. Patent #D850,249 awarded as Inventor.
-
-
-
Waring, a Division of Conair
-
Torrington, Connecticut
-
Senior Project Engineer
-
Jun 2014 - Sep 2015
Senior Engineering role with responsibilities for new product development and commercialization at home and in Asia for this global brand. Senior Engineering role with responsibilities for new product development and commercialization at home and in Asia for this global brand.
-
-
-
Fisnar
-
United States
-
Industrial Automation
-
1 - 100 Employee
-
Engineering Manager
-
Jan 2011 - Jun 2014
Industrial robot & liquid dispensing equipment manufacturer. We are the dispensing equipment division of Ellsworth Adhesives. We operate globally, with service & stocking locations throughout the Americas, Europe, and Asia. Responsible for all Engineering Operations related to dispenser and robot systems to deliver design intent, performance requirements, design for test (DFT), design for manufacturability (DFM), prototype development and validation, efficient transfer to Production, in-process testing and final testing protocols. Show less
-
-
-
Berry Global, Inc.
-
United States
-
Plastics Manufacturing
-
700 & Above Employee
-
Manager of New Product Development
-
Nov 2002 - May 2010
Rigid closed top food and beverage container manufacturer. Expertise in Injection Stretch Blow Molding, Injection Blow Molding, Extrusion Blow Molding, decorating & automated handling systems. Materials include PET, HDPE, MDPE, LDPE, PP, Clarified PP, Barex, Copolyester, bio-based PET, & both active and passive barriers whether they be additive or applied. Led three Senior Development Engineers executing over 80 projects representing $60MM annually in new revenue. Drove the refinement of the quote process to satisfy the explosive demand, which grew 250% to over 850 product development quotes annually. Conducted over 100 Customer presentations to demonstrate how our value propositions could enrich their market positions. Delivered 94% of both team and personally driven projects on time, within budget. Re-engineered development processes to support sales force growth of 50% and number of mfg locations that increased 30%. Earned promotion to Manager of this $400MM category in Mar 09 after Berry bought Captive Plastics. Show less
-
-
-
Inverness Corporation
-
Northern New Jersey
-
Quality Manager & Sr. Industrial Engineer
-
Aug 1995 - Oct 2003
Medical device manufacturer. Co-developed automation project plans that demonstrated design intent, qualified tooling designs, cost justification analysis, development of machinery and staffing requirements. Both were concurrently completed on time, in budget. Process yields met or exceeded corporate quality expectations. Team Member in offshore technology transfer for medical device manufacturing. Extensive cost structure development and ROI Analysis. Transferred 166 finished goods assemblies successfully. Achieved performance yields within 0.5% of expectations. Developed and implemented comprehensive Engineering Change Control process for compliance to GMP and FDA requirements. Designed & rebuilt processes for compliance to GMP & FDA guidelines. Authored 35% of the Corporate Quality Manual and 70% of the Work Instructions. Trained and led a staff of two Engineers and nine Inspectors supporting 250 employees on two shifts, covering ten different manufacturing lines. Conducted extensive Failure Analysis and Corrective Action implementation for electrolysis and hot waxing hair removal systems. Technologies included metal foil heat stamping, ultra sonic welding, cable stripping/termination, cable harness assembly, welding, machining, gold and palladium plating with manual assembly. Redesigned 34 manual and automated tooling press heads to eliminate manufacturing related defects. Developed and implemented Statistical Process Control program for in-house component machining systems. Trained QA staff on metrology techniques. Initiated failure analysis leading to corrective action implementation, which improved yields from 71% to 99.4%. Project duration: 4.5 months. Show less
-
-
-
US Army
-
United States
-
Armed Forces
-
700 & Above Employee
-
94th Army Reserve Command
-
Sep 1986 - Sep 1995
-
-
10th Special Forces Group
-
Aug 1983 - Sep 1986
-
-
Education
-
Harvard University
CSS, Business Administration -
University of Massachusetts Lowell
BSIE, Industrial Engineering
Community
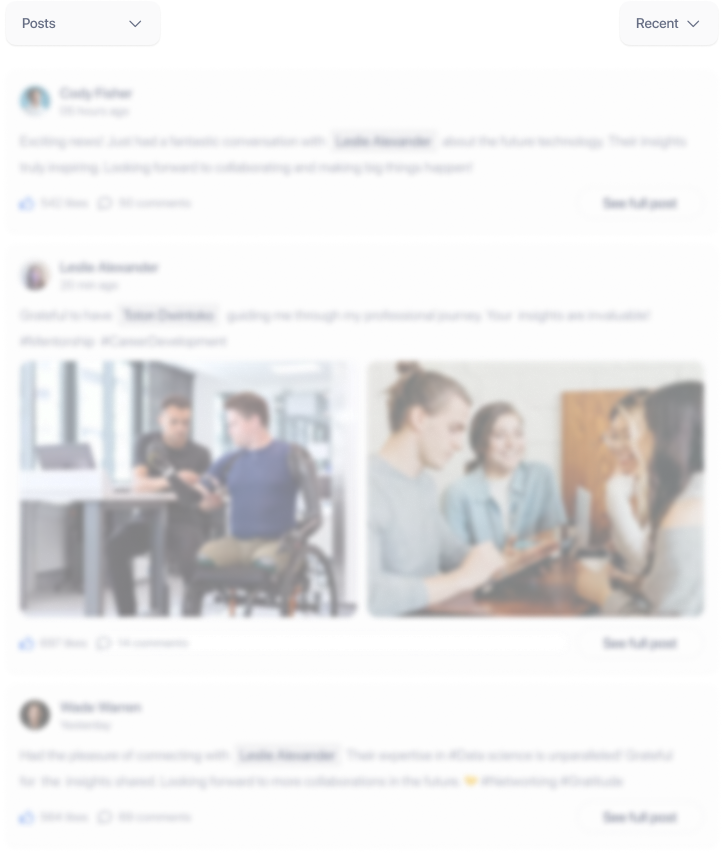