Roger Richard
Senior Director Quality at Codagenix Inc.- Claim this Profile
Click to upgrade to our gold package
for the full feature experience.
Topline Score
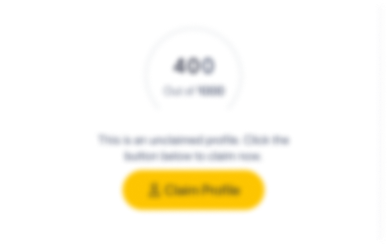
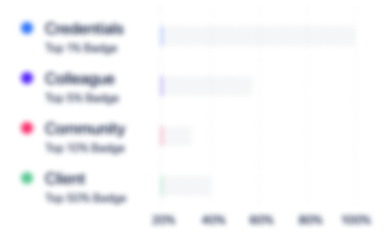
Bio


Experience
-
Codagenix Inc.
-
United States
-
Biotechnology Research
-
1 - 100 Employee
-
Senior Director Quality
-
Jan 2023 - Present
The Senior Director oversees, participates in, and manages all Quality Assurance (QA) and Quality Control (QC) activities. Responsibilities include working collaboratively across internal functions including Manufacturing, Analytical / Process Development, Regulatory Affairs, and Supply Chain to ensure QA deliverables are met. Acts as a point of contact (POC) on QA matters, internally and externally. The Senior Director oversees, participates in, and manages all Quality Assurance (QA) and Quality Control (QC) activities. Responsibilities include working collaboratively across internal functions including Manufacturing, Analytical / Process Development, Regulatory Affairs, and Supply Chain to ensure QA deliverables are met. Acts as a point of contact (POC) on QA matters, internally and externally.
-
-
-
GreenLight Biosciences
-
United States
-
Biotechnology
-
100 - 200 Employee
-
Director Of Quality Assurance
-
Jun 2020 - Mar 2022
Assembled, developed, and led the quality unit (QA & QC) responsible for implementing quality systems needed to manufacture a Phase I mRNA vaccine therapy. Duties also included QC Laboratory space planning, lab equipment purchase & qualification, and the use of an electronic documentation systems (Qualio). Served as an internal resource for instructing R & D scientists on the drug development process and the differing regulatory requirements. Supervised 3 direct reports and 10 indirect reports. • Oversaw Quality Consultant and Validation Service contractors. • Performed Approved Supplier List (ASL) vendor qualification audits. • Assisted with the design planning for pod manufacturing suites. • Participated in the selection and procurement of an electronic quality management system (Veeva). Show less
-
-
-
Cytiva
-
Biotechnology Research
-
700 & Above Employee
-
QA Site Lead
-
Apr 2020 - Jun 2020
Formerly GE Healthcare Life Sciences, I now work at Cytiva - an organization of more than 6700 people across 40 countries. With a strong background and passion for life sciences, I am helping to bring transformative health to patients through the researchers, hospitals, and pharmaceutical partners of Cytiva. Formerly GE Healthcare Life Sciences, I now work at Cytiva - an organization of more than 6700 people across 40 countries. With a strong background and passion for life sciences, I am helping to bring transformative health to patients through the researchers, hospitals, and pharmaceutical partners of Cytiva.
-
-
-
GE HealthCare
-
United States
-
Hospitals and Health Care
-
700 & Above Employee
-
QA Site Lead
-
Jun 2018 - Mar 2020
Hires, trains and directs the quality assurance staff responsible for overseeing the testing and manufacturing CGMP compliance of non-clinical and clinical (Phase 1 & 2) materials utilizing single-use technologies. Serves as a resource for related development activities such as Process Development Transfer, Cell Line Development, and Analytical Assay Development. Provides quality systems training to site personnel. Reviews records (e.g., manufacturing batch records, release & stability testing data, SOPs, Deviations, Change Requests, and Corrective and Preventative Action (CAPA) reports). • Participates in Risk Assessment and Mitigation evaluation activities. • Responsible for hosting client compliance and site qualification audits. • Provides site Quality System Overview training, CGMP Orientation and Annual Refresher training, Good Documentation Practices training, as well as Deviation Writing training. Show less
-
-
-
Dana-Farber Cancer Institute
-
United States
-
Hospitals and Health Care
-
700 & Above Employee
-
Senior QA Manager - Cell Therapy
-
Dec 2015 - Jun 2018
Responsible for the clinical QA systems used to ensure patient safety and support continued accreditation of cellular therapy transplant programs. Participated in harmonization activities between the Donor Services, Product Manufacturing, and Clinical QA groups. Utilized electronic data systems such as EPIC, StemSoft, and FormsNet for data management. Directly supervised 7 staff members who, in-turn, oversaw 14 additional staff supporting Cord Blood processing and transplant outcome (CIBMTR) reporting. • Mentored / trained staff members new to quality systems related to cell therapy regulations and standards. • Performed comprehensive gap analyses that compared existing clinical processes to the current accreditation agency standards. Created gap response plans based on prioritization of the issues discovered. • Integrated the Outcomes Reporting Team into the QA group structure in an effort to reduce staff turnover by creating a career path for entry-level staff. Result: staff turnaround reduced by 75% after 1 year. • Member of the team tasked with transitioning CAR-T and other immune effector cells from clinical trial to standard of care upon marketing approval. Responsible for implementing quality systems addressing these products. • Member of the vendor selection and implementation teams tasked with electronic data system updates. Systems include Master Control for document management and OTTR for case management and outcomes reporting. Show less
-
-
-
IDEXX
-
United States
-
Biotechnology Research
-
700 & Above Employee
-
US Reference Labs Quality Manager
-
Mar 2013 - Dec 2015
Performed status assessments and provides guidance regarding the state of quality systems for 41 veterinary diagnostics laboratories. Reviewed and implemented change control as part of a Medical Review Board (MRB) process. Provided consultation services to the BioMedical Research group working under vGCP and GLP regulations. Reviewed QC data and error trending data for process improvement opportunities. Supervised 6 staff members. • Audited reference labs from a quality management systems (QMS) perspective for process improvement purposes and creates written audit reports for laboratory and senior managers. • Project lead for the installation and implementation of the Q-Pulse quality management system. This software system moved SOP, CAPA, Training, and Equipment processes from a paper-based to electronic data system. • Participated on a team that created Smart Service viewer tools for ELISA and Symmetric Dimethyl Arginine (SDMA) testing. These tools utilized patient data as an internal quality assurance mechanism. • Participated as a voting member of the U.S., Canadian, and International Reference Labs MRB teams. • Participated as a QA representative to the Technical Management and Laboratory Implementation Teams. These teams provided oversight to section-specific laboratory operations (e.g., Chemistry, PCR, Immunology, Hematology, etc.) • Reviewed equipment qualification packages for new and recently repaired diagnostic testing analyzers. Provided release for use statements showing that the instruments are suitable for performing patient testing. • Trended validity check statistics and works with Training Team members to develop programs aimed at reversing trends in testing and processing errors. Show less
-
-
-
Sanofi
-
France
-
Pharmaceutical Manufacturing
-
700 & Above Employee
-
Principal Quality Auditor - GMP Compliance
-
Oct 2006 - Mar 2013
Ensured GLP / GMP compliance of Therapeutic Protein Laboratory Support, Cell Culture Development, Protein Purification Research, and Bioanalytical Laboratory processes to ensure compliance with regulatory requirements applicable to the manufacture of non-clinical and clinical (Phase 1 & 2) materials. Served as a resource for compliance and quality system issues. Reviewed records (e.g. manufacturing batch records, release & stability testing data, validation protocols and execution documentation, SOPs, Metrology Discrepancy Reports, Exception and Corrective and Preventative Action (CAPA) reports, environmental monitoring, and quality critical alarms). Approved & released material from quarantine for use (i.e. media, buffers, raw materials). Conducted Newcomer and Annual Refresher CGMP Training. • Performed bioreactor contamination and analytical test method investigations as assigned, suggested and implemented corrective actions, formalized findings and responses in written reports. • Assisted in the validation of electronic data management systems to include Quality Assurance Audit Database (QAAD), Product Data Management System (PDMS), and Waters Empower by reviewing procedures, protocols, and test scripts. • Reviewed QC laboratory testing data performed by high performance liquid chromatography (HPLC), gel electrophoresis, enzyme linked immunosorbent assay (ELISA), capillary isoelectric focusing (cIEF), Vesivirus 2117 RT-PCR, as well as other standardized testing methods. • Authored SOPs in response to process improvement initiatives (e.g., material transfer process, nonconforming material evaluation & disposition, status labeling). • Assisted the GLP Compliance team by conducting off-site vendor audits. Routinely performs in-house GMP Compliance process audits. Show less
-
-
-
Genzyme - Clinical Specialty Laboratory
-
Framingham, MA
-
Staff Scientist 1
-
Aug 2004 - Sep 2006
Supervised sample and data accessioning activities related to the receipt of clinical trial and post-market monitoring samples from human sources. Performed cell count and sample manipulation activities (i.e., viral media inoculation). Reviewed sample labels and documentation for compliance with local and regulatory requirements; investigated and resolved issues affecting sample acceptance for testing. Wrote SOPs and performed quality assurance functions as needed. Supervised 5 staff members. • Provided input regarding sample collection, shipping (U.S. & International), processing, informed consent, blinding of patient and clinical trial participants, and accessioning activities as part of a team designing new clinical trials. • Assisted process improvement activities aimed at preparing the laboratory for CLIA licensure. Drafted the laboratory’s Quality Plan, Sample Manual, HIPAA Policy, and Corrective Action & Process Improvement procedures. CLIA Approval obtained. • Assisted in executing computer system validation protocols related to system upgrades. Procedures ensure continued regulatory (Part 11) compliance of the facility’s BLAZE Laboratory Information Management System. Show less
-
-
-
Beth Israel Deaconess Medical Center
-
United States
-
Hospitals and Health Care
-
700 & Above Employee
-
Transfusion Medicine Compliance Officer
-
May 2000 - Oct 2004
Evaluated and interpreted new regulatory guidance and accreditation standards for their impact on current policy. Advised medical directors on actions needed to ensure that the donor collections, biologic product manufacture, and transfusion related activities complied with FDA and other accrediting agency mandates. • In-house consultant to the Department of Pathology. Ensured regulatory compliance in preparation for JCAHO and CAP accreditation. All accreditations maintained. • Served as the primary facility contact for interacting with FDA and accreditation agency staff performing compliance inspections. Assisted in establishing corrective actions and preparing response packages as needed. Wrote / revised quality plans, standard operating procedures, and validation protocols as needed. • In-house advisor to the Division of Transfusion Medicine. Ensured regulatory compliance in two blood banks, a Blood Donor Center & Component Manufacturing area, a stem cell laboratory, a Transfusion & Pheresis ward, and an HLA testing laboratory. AABB, ASHI, and FACT accreditations obtained / maintained. • Coordinated process improvement activities including label control, process validation (product transfer by pneumatic tube & computer system data merges), and document change control for 317 procedures. • Managed the Error & Accident reporting program. Monitored, tracked & trended deviations. Corresponded with the FDA (reportable errors) or other agencies as needed. • Supervised the Product Withdrawal & Recall and Hepatitis C Virus Lookback programs. Investigated product and patient dispositions, corresponding with physicians and suppliers as needed. • Developed and conducted annual GMP refresher training courses for manufacturing and testing staff members. Developed and provided Quality Systems and Inspection Readiness training to Pathology Residents. Show less
-
-
-
American Red Cross - Biomedical Services
-
Dedham, MA
-
Associate Director, Quality Management
-
Nov 2001 - Mar 2002
Supervised deviation tracking & reporting, donor management activities (demographics, deferral, lookback), product collection criteria (Nurse of the Day), and product recall & customer notification activities. Supervised a staff of 20. • Authored the operating procedure for and implemented the use of electronic reporting methods to inform the U.S. Food & Drug Administration of blood product deviations. • Audited records for accuracy, completeness, and assessment of process improvement actions to prevent future deviations from established protocol. Show less
-
-
-
American Red Cross - Biomedical Services
-
Dedham, MA
-
Production Laboratory Manager
-
Oct 1998 - May 2000
Directed the daily operations of a GMP blood component manufacturing laboratory that processed 1100 – 1300 computer-tracked products daily. Supervised a staff of 40 unionized employees. Ensured that blood products were manufactured in accordance with cGMP standards. Reviewed and audited quality control and quality assurance data as part of product release procedures. Participated in Material Review Boards to determine the acceptability and disposition of non-conforming products. Coordinated training, implementation, and validation planning for the introduction of new processes into existing operations: • Trained in Radiation Safety procedures. Assisted in monitoring employee exposure during irradiation of blood product components. • Converted operations from manufacturing non-leukoreduced products to ensuring that all of the red cell units produced were leukoreduced. • Implemented the processing of double red cell units collected by apheresis methods. Show less
-
-
-
-
Instructional Program Writer & Instructor
-
Jun 1997 - Oct 1998
Created distance-learning courses (chemistry) used for continuing education and promotion examination study by all Air Force Medical Laboratory Technicians. Instructed basic laboratory procedures to newcomers as well as management and advanced techniques to mid-career technicians.
-
-
Laboratory Supervisor
-
Jun 1993 - Jun 1997
Assisted in moving laboratory operations into a new facility including the installation, validation, and training for six new analyzers and information systems. Supervised a staff of 8. Responsible for blood program operations to include transfusion services, donor center activities, and blood product manufacture and testing.• Helped lead the blood bank to licensure by the Food and Drug Administration, the only Class C Air Force laboratory to hold a blood product manufacturing license. • Trained and supervised laboratory staff performing the ship-out of slides, tissues, and blood samples using international courier services. Established written procedures for accomplishing customs and biohazardous shipping declaration forms. Result: Decreased delayed shipments; analyte turn-around time cut from 5 weeks to 3 weeks.• Gained project management experience by assisting in the implementation and management of the Blood Transshipment Center and Frozen Blood Depot in support of medical readiness capabilities. Responsible for tracking the arrival, storage location, blood type, and expiration date of 1,800 frozen blood units.• Created in-house training programs for newly arriving personnel saving $700 per person in training costs. • Authored laboratory operating instructions and equipment validation plans for computerized product labeling systems. These documents were then used as templates for other military laboratories in the Pacific Rim. Show less
-
-
Section Supervisor
-
Jan 1990 - Jun 1993
Supervised operations in the Hematology, Chemistry, and Microbiology sections of the laboratory. Administered the quality control programs in support of 50,000 patient procedures per month. • Prepared an average of 300 urine samples per month for shipping to a reference laboratory using special procedures designed to ensure that legal chain of custody was maintained. Result: Legal challenges in court upheld, samples and results of testing approved for use.• Technical writing experience gained while serving temporarily as the Strategic Missile Wing Historian. Show less
-
-
Air Force Recruiter
-
Jan 1986 - Dec 1989
Utilized public speaking engagements and other marketing tools to successfully recruit more than 100 individuals into positions in the Air Force.
-
-
Medical Research Technician
-
Feb 1981 - Dec 1985
Performed medical research procedures to establish safety guidelines and exposure limits for aircraft maintenance personnel when working with jet fuels and chemicals. Analytical methods included HPLC and gas chromatography. Maintained tissue culture cell lines and rodent colonies as well as performed surgical procedures and vivisections on laboratory animals.
-
-
Laboratory Technician
-
Nov 1978 - Jan 1981
Provided general laboratory services in support of outpatient and emergency room treatment and care.
-
-
Education
-
Massachusetts College of Pharmacy
Master of Science, Drug Regulatory Affairs & Health Policy -
Park University
Bachelor of Science, Social Psychology -
Community College of the Air Force
Associate Degree, Applied Science (Laboratory Technology)
Community
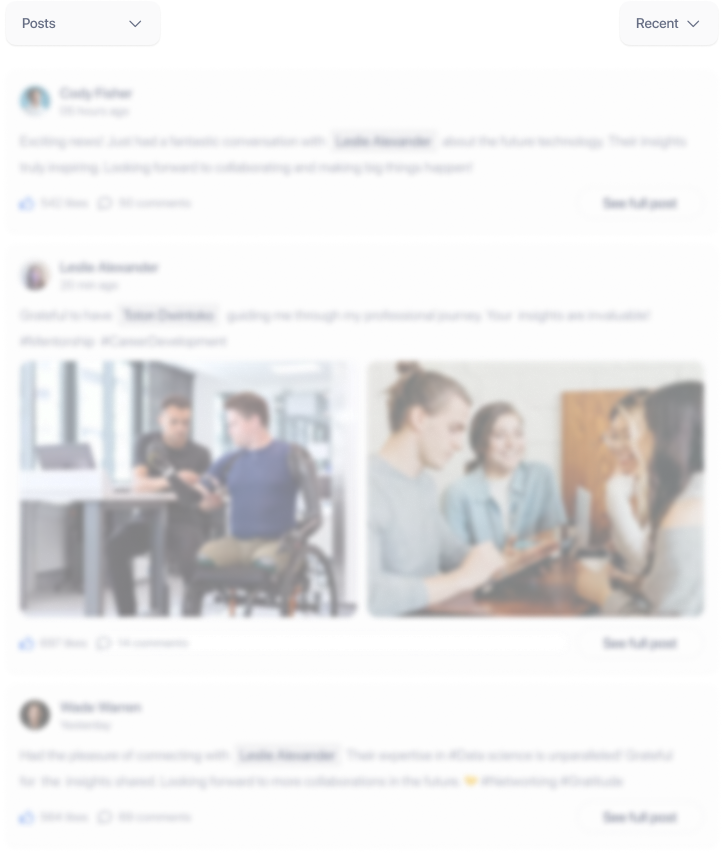