Rodrigo Díaz de la Vega
Nuclear Quality Assurance Engineer at Reuter-Stokes, a Baker Hughes business- Claim this Profile
Click to upgrade to our gold package
for the full feature experience.
-
English Native or bilingual proficiency
-
Spanish Full professional proficiency
-
Portuguese Elementary proficiency
Topline Score
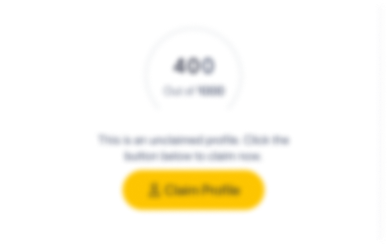
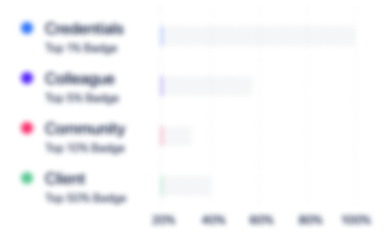
Bio


Credentials
-
Coaching Your Team in a Dynamic Workplace
LinkedInJul, 2023- Sep, 2024 -
Having Career Conversations with Your Team
LinkedInJul, 2023- Sep, 2024 -
Building Resilience
LinkedInJun, 2023- Sep, 2024 -
Change Leadership
LinkedInJun, 2023- Sep, 2024 -
Counterintuitive Leadership Strategies for a VUCA (Volatile, Uncertain, Complex, Ambiguous) Environment
LinkedInJun, 2023- Sep, 2024 -
Leading Change
LinkedInJun, 2023- Sep, 2024 -
Atomic Habits (Blinkist Summary)
LinkedInMay, 2023- Sep, 2024 -
Coaching Yourself and Your Team from Uncertainty to Action
LinkedInMay, 2023- Sep, 2024 -
Leading a Customer-Centric Culture
LinkedInMar, 2023- Sep, 2024 -
Customer Experience Leadership
LinkedInFeb, 2023- Sep, 2024 -
Yellow Belt in Lean Manufacturing
Lean Six Sigma Institute
Experience
-
Reuter-Stokes, a Baker Hughes business
-
United States
-
Measuring and Control Instrument Manufacturing
-
1 - 100 Employee
-
Nuclear Quality Assurance Engineer
-
Nov 2022 - Present
-
-
-
Thermo Fisher Scientific
-
United States
-
Biotechnology Research
-
700 & Above Employee
-
Quality Assurance Engineer III
-
Jul 2020 - Nov 2022
- Completed training for Lead Auditor certification.- Responsible for developing QVD's (Quality Verification Document).- In charge of the of the MRB (Material Review Board) process. We verify all non compliant issues (Discrepancy reports) and take action to address and resolve promptly. In charge of following up with each department to make sure no roadblocks occur. - Have constantly improved the MRB process to streamline and make sure everyone has access to the data.1.- Shifting MRB process to Microsoft Teams2.- Improved traceability for RTV material.- In charge of the CAPA/CAR process for the NFMS division, for both internal and external cases. Hold once a week meetings to update and status and follow up on actions to close cases.- Have worked extensively with customers to resolve any quality issues or concerns.- Have created work instructions to help aid and explain in finer detail the appropriate method to perform certain processes.- Have updated procedures from the Quality Assurance Manual to keep the site up to date with the latest nuclear requirements from NQA-1-2008/1a-2009, 2015 and from NRC Regulations (10 CFR Part 21).- Have been delegated the QA department authority while QA Manager is offsite. Show less
-
-
Quality Assurance Engineer III
-
May 2018 - Jun 2020
- Member of the RPS (rapid problem solving) team. Give aid and guidance to production staff when an issue arises. - Responsible for developing QVDs (Quality Verification Document).- Quality representative of the MRB (Material Review Board). We verify non-compliant issues and take action to resolve them promptly. - In charge of keeping the FPY (First Pass Yield) metrics from a Quality standpoint. - Participated in 5 kaizen events through the Thermofisher's scope called PPI (Practical Process Improvement). With these events, we've improved:* Production flow and improved document traceability by 80%.* MRB production disposition in a 48 hr. Window, from a previous 30+ days timeframe.- Team leader at kaizen event to improve MRB throughput with a new process implementation. Lead consecutive accountability actions to disposition all actual MRB products, surpassing the expectation from 2 weeks to 1 week.- Created internal C.A.R.s and followed up to get them closed before internal and external audits.*Have answered and got approved more than 15 C.A.R.s from both customer and internal audit findings. This has led to:1.- The site kept its NAIC certification.2.- Getting approved again by an external supplier on their A.S.L. (Approved suppliers list), making the site gain new customer orders.- Have worked extensively with customers to resolve any quality issues or concerns.- Have created work instructions to help aid and explain in finer detail the appropriate method to perform certain processes.- Have updated procedures from the Quality Assurance Manual to keep the site up to date with the latest nuclear requirements from NQA-1-2008/1a-2009 and NRC Regulations (10 CFR Part 21).- Keeping up to date on the nuclear regulations by attending and representing TFS at the 2018 NIAC Conference.- Have been delegated the QA department authority while QA Manager is offsite. Show less
-
-
-
Parker Hannifin
-
United States
-
Industrial Machinery Manufacturing
-
700 & Above Employee
-
Process Engineer
-
Jun 2017 - Jan 2018
• Train molding associates in the correct process procedures to manufacture complying Space parts, and assist in the production of the parts, should aid from engineering was required. • Be the liaison between program management and production staff to define the priorities of Space production. • Participate in the daily QA meeting, were it was defined if the non-conforming parts from the day were going to be reworked, reclaimed or scrapped. • Participate in the daily CAR/ATR meeting, were we worked on resolving the issues involving returned part from customer’s and CAR’s (Corrective Action Requests). • In charge of the daily LPA (Layer process audit) meeting, were we attended safety concerns from the production staff. Kept record of the findings and scheduled the audits for the upper management layers. • Involved in conference calls with SPACE customer’s (NASA) to describe the setbacks and actions taken from an engineering standpoint on the day to day issues from space parts. Show less
-
-
-
Zodiac Aerospace
-
France
-
Aviation and Aerospace Component Manufacturing
-
700 & Above Employee
-
Production Supervisor
-
Oct 2015 - Jun 2017
-Assist program management with the development of short/long term goals and objectives, providing feedback and recommendations.-Supervise production: the production process, receiving of material and inspection.- Coordinate and set daily production goals for the production staff. - Adapt the production to be able to meet the changes and still be able to meet the client's needs on time.- Regulate the production flow so it is always at full capacity. This involved monitoring the production schedule on a daily basis to guarantee the fulfillment of the production goals based on the established time frame. Take corrective actions when necessary so goals can be met on time.- Ensure that the production activities are developed according to the standards set by production, quality and safety. Implement and coordinate actions when the activities are not done by the standards.- Provide leadership through objectives, delegation of activities and communication.- Develop new BOMs and cost material for introduction of new part numbers.- Supervise and coordinate the execution of new part numbers so that they passed final inspection.- Coordinate with supporting departments (engineering, quality, process, planning, design and shipping) to meet the needs of production and reach the goals established by production.- Administrate the production's budget for raw goods and its requirements.- Report production status vs production objectives in terms of cost-benefit and delivery.- Promote the growth of my personnel, by making them acquire certifications in multiple abilities and changing their status from a single classification employee to a multiple classification employee.- Use ERP system to control overtime, unmarked clocked ins, late clock ins, etc. of in charge personnel. Show less
-
-
Manufacturing Engineer
-
May 2015 - Oct 2015
In charge of planning the production for the Global and Challenger lines within the Business Jets division.Do 6 improvements a month.Keep track and maintain the production lines leveling in 80%.Depending on the production schedule, communicate the daily goals to be reached to the production staff and help them reach it.Have communication with the client about what panels are priority so we can deliver them ASAP and improve our ODD (on dock date).
-
-
Manufacturing Technician
-
Oct 2014 - May 2015
- Develop Standard Process Worksheets for the trimming process of liners and handrails for the stairs of the Airbus models.- Filmed critical processes of trimming and bonding to have a backup of information after transfer of A380 Liners, Sidewalls and Handrails is completed.- Assisting manufacturing engineer in verifying that all the tools and equipment needed to start production for A380 Stairs were acquired.- Develop an average of 6 improvements per month since January 2015. This improvements were done on the Business Jets line and involved the following: 5's, visual management, cost reduction and ergonomics.- Develop standard worksheets and process sheets for the Falcon line in the Business Jets division.- Develop a layout proposal for the Business Jets division (this included the Falcon, Challenger and Global line). Show less
-
-
-
GE Aviation
-
United States
-
Aviation and Aerospace Component Manufacturing
-
700 & Above Employee
-
EID Intern
-
Aug 2013 - Feb 2014
- Develop a list of the materials needed for a new laboratory for the UNISON division of GE Aviation in Queretaro. - Have meetings with stakeholders to see that all the materials needed for the lab were considered and to see that the laboratory complied with both safety and environmental regulations, both from GE and from Mexico. - Make an inventory of all the parts of the engine that the UNISON team members had with them. - Create an intraweb community using GE's community portal, Support Central, so that the engineers could upload the types of errors in the drawings they have to solve and to see the effectiveness of the team. - Create and modify BOM's (Bill of Materials) in ORACLE of specific projects. Show less
-
-
-
-
Yellow Belt Trainee
-
Mar 2011 - Aug 2011
My activities while in the Socconini Consulting Group included: *NOTE: While in this Consulting Group, we worked for the manufacturing pharmaceutical company called Gerresheimer. - Make spaguetti maps of the path the operator did while working. - Make hourly reports about the scrap produced in the production lines of the machines I was assigned to. - Find opportunity areas for reducing waste, time, saving money in the lines I was assigned. - Take notes about the most common problems in the machines and make a Pareto diagram about them. In this activity, I had to see which of the scrap areas was the one that produced the most waste. - Design layouts of the machines to see were the waste areas were located. Show less
-
-
Education
-
Universidad del Valle de México
Bachelor's degree, Industrial Engineering -
Universidad Europea
Bachelor's Degree, Industrial Engineering
Community
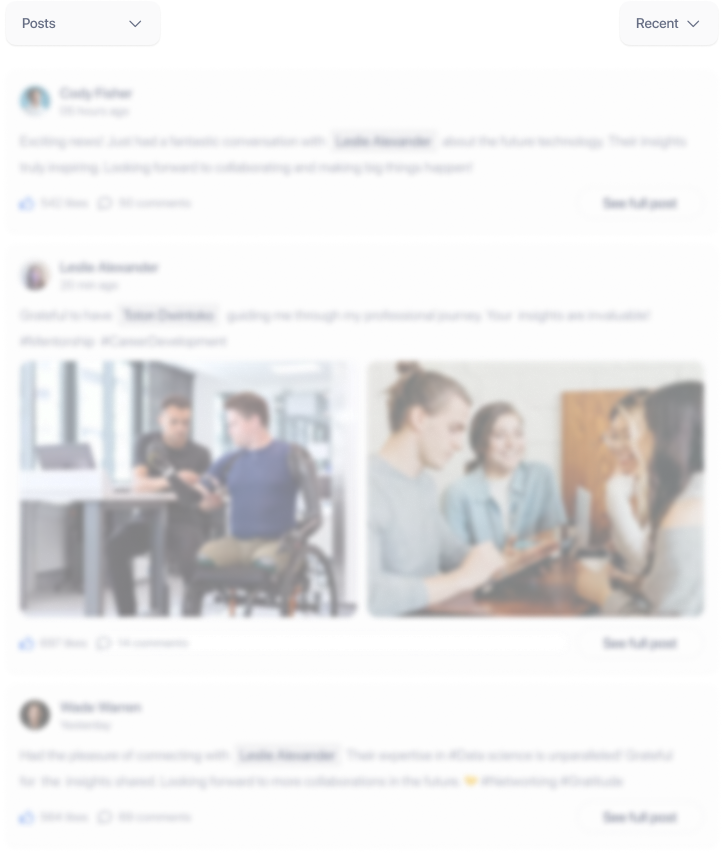