Rodolfo Angelelli
Quality Assurance at Brompton Bicycle- Claim this Profile
Click to upgrade to our gold package
for the full feature experience.
-
Português Native or bilingual proficiency
-
English Full professional proficiency
-
Italiano Limited working proficiency
Topline Score
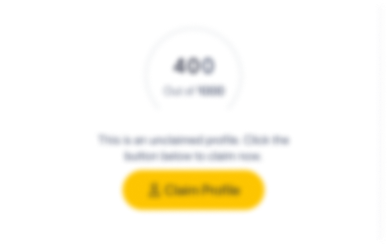
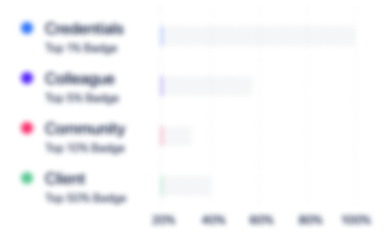
Bio


Experience
-
Brompton Bicycle
-
United Kingdom
-
Manufacturing
-
300 - 400 Employee
-
Quality Assurance
-
Aug 2020 - Present
- First Point of contact on the shop-floor for any issue related to process and quality. - CMM Programmer and Operation - 5’s Champion – Brompton Project to implement 5s at the company. - Process and Product Audit. - Customer Service Support for any issue related to product / quality. - Work Manual Review. - Assist Quality Assurance and Supplier department with samples and documentation approves. - Problems Solving analysis (8D). - Process Improvement. - Assist on product improvement (CR).
-
-
-
Hayward Tyler
-
United Kingdom
-
Industrial Machinery Manufacturing
-
100 - 200 Employee
-
Quality Engineer
-
2019 - Jul 2020
- Non-conformance management (SCAR / CAPA).- Developing and improvement a new non-conformance system.- Implementing and maintaining procedures under ISO 9001:2015.- Calibration management.- Dealing with suppliers. - Dealing customer complaints.- Supporting on management of QMS (Quality Management System).- Indirect purchase dealing.- Internal Audit.- Supplier Analysis and approval.
-
-
Quality Inspector
-
2018 - 2019
- Inspecting parts through the life cycle from small to large components.- Reviewing Quality plans for inspection requirements.- Approval of new samples for new suppliers.- Using a variety of handheld measuring equipment and CMM (QCL Software). - Raising internal and external Non-conformance (CAPA’s / SCAR’s). - Supporting manufacturing / assembly areas. - Working within the ISO 9001 requirements.
-
-
-
UK Mail
-
United Kingdom
-
Postal Services
-
400 - 500 Employee
-
Quality Logistics
-
2018 - 2018
- Dealing with customers complaints. - Updating KPI’s. - Dealing with customers complaints. - Updating KPI’s.
-
-
-
CNH Industrial
-
Machinery Manufacturing
-
700 & Above Employee
-
Quality Leader
-
2014 - 2017
- Responsible for Final Inspectors and Mechanics Team. - Development and Management of KPI’s.- Responsible for schedule duties for the operators. - Area budget management. - Continuous Improvement program using WCM philosophy and Quality Tools.- Customer Service. - Area responsible for QEHS.
-
-
Quality Analyst
-
2010 - 2014
- Quality Auditor (ISO 9001 - 14001 - OHSAS 18001).- QMS Management.- Upkeep and managing metrology equipment.- Quality Plant responsible for approval or disapproval of current and new parts.- Suppliers Audit.- Continuous improvement program using WCM philosophy and Quality Tools.- Customer Service. - Problem solving and root causes’ analysis.
-
-
-
KSB Bombas Hidraulicas S/A
-
Brazil
-
Machinery Manufacturing
-
300 - 400 Employee
-
Process Manufacturing
-
2009 - 2010
- Development of new iron casting process. - Continuous improvement on currently projects / parts. - Supporting Production Management. - Supporting Product Engineering. - Development of new iron casting process. - Continuous improvement on currently projects / parts. - Supporting Production Management. - Supporting Product Engineering.
-
-
-
EACIAL
-
Brazil
-
Industrial Machinery Manufacturing
-
1 - 100 Employee
-
CNC Programmer and Operator
-
2006 - 2009
- CNC programmer and operator machines. - Quality Control. - CNC programmer and operator machines. - Quality Control.
-
-
Education
-
Universidade Metodista de Piracicaba
Production Engineer
Community
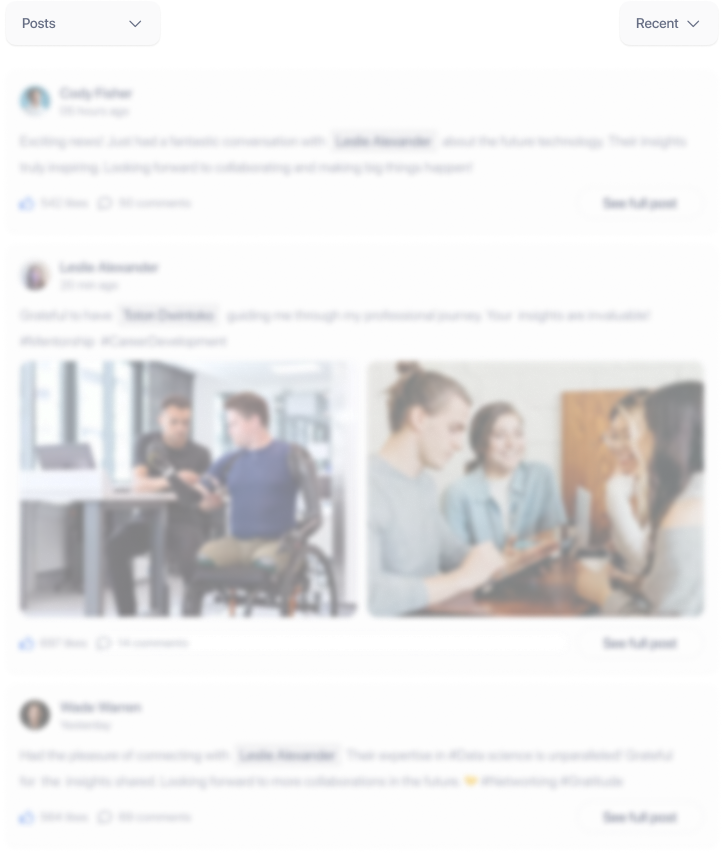