Robyn Birch
Business Analyst at Trisura Specialty Insurance Company- Claim this Profile
Click to upgrade to our gold package
for the full feature experience.
-
French Limited working proficiency
-
English Native or bilingual proficiency
Topline Score
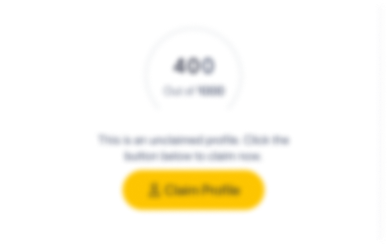
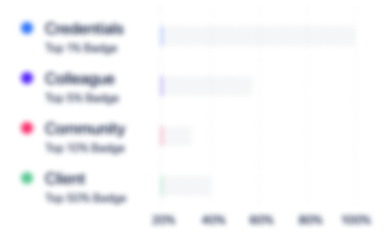
Bio


Credentials
-
Python for Everybody
University of MichiganFeb, 2021- Nov, 2024 -
SQL For Data Science
University of California, DavisJan, 2021- Nov, 2024 -
Lean Six-Sigma White Belt
Robbins International/Lean 2020Jan, 2014- Nov, 2024 -
Private Pilot
Federal Aviation AdministrationSep, 2013- Nov, 2024
Experience
-
Trisura Specialty Insurance Company
-
United States
-
Insurance
-
1 - 100 Employee
-
Business Analyst
-
Mar 2021 - Present
-
-
-
OGE Energy Corp.
-
United States
-
Utilities
-
700 & Above Employee
-
Power BI Data Analyst
-
Jul 2020 - Mar 2021
-
-
-
Schlumberger
-
United States
-
Oil and Gas
-
700 & Above Employee
-
Power Business Intelligence (Power BI) Champion
-
Apr 2019 - May 2020
Championed the introduction, integration, and use of Microsoft Power Business Intelligence (Power BI) throughout the department while concurrently serving as the Field Service Quality Engineer.▪ Designed Microsoft Power BI Dashboards to develop business cases, improve information visibility, enhance operational performance, and generate actionable steps/key strategic decisions in the best interest of the organization. Highlights Includedo Power BI Consumption and Reliability Dashboards (M&S/NPT).o Power BI Global Program Deployment Dashboards/Strategies & Gap Maps.▪ Trained a Diverse Team of Engineering Professionals (managers/staff) on the use of Microsoft Power BI while advocating its benefits.▪ Commercialized and Industrialized Microsoft Power BI Tools to Disseminate Critical Information to Executive Stakeholders in partnership with senior management.▪ Delivered Key Intelligence/Analytics Through Microsoft Power BI used to develop/prioritize annual project plans.▪ Proficient in ETL via M-Code (PowerQuery), SQL, DAX, and basic Python.
-
-
Field Service Quality Engineer
-
Apr 2018 - May 2020
Governed the planning/deployment of engineering and technical solutions using Lean Six Sigma methodologies and root cause analysis to enhance the quality and performance of stimulation and cementing assets while meeting evolving business needs.▪ Identified Key Improvement Areas in Business Workflows and Improvement Domains (technology, process, competency, behavior, and control).▪ Developed, Architected, and Provided Ongoing Real-Time Digital Support to Adaptable and Evolving Equipment Maintenance Programs while improving field personnel confidence in the Asset Care Program (ACP). Highlights Includedo Standardized Maintenance Processes/Classifications: aggregated issues, identified common themes, and eliminated redundancies across multiple business systems.o Electronic Ticketing Processes/Structures (localized help desk, SME reviews, and issue publication standards): captured laborsavings of 97.5%, from 40 hours to one hour, and achieved a 90% close rate.o Divergence/Development of Short-Term Maintenance Programs with Digital Tools (CMMS) and Expansion of Systematic Processes: captured previously unknown/invisible failure modes prior to them becoming catastrophic.▪ Designed Standards, Processes, and Solutions that Reduced Nonproductive Time (NPT), Increased Efficiency, Improved Communication Between Multidisciplinary Global Teams, and Drove Asset Performance. Highlights Includedo Asset Care Program Development: a customized equipment maintenance program to mirror business and reliability needs.o Quality Testing Processes (including standard work instructions, testing protocols, and gap maps): rapidly identified and resolved common failure points.o Equipment Rebuilding Strategies: transitioned the department from time/hour-based to fuel consumption methods to accurately define asset life cycle points, predict failures, and identify/eliminate unnecessary overhaul costs.
-
-
Mechanical Project Engineer
-
Apr 2017 - Apr 2018
Oversaw mechanical engineering projects for a variety of systems (cooling, power-end, hydraulic, and fluid-end) to capture cost savings (M&S) and improve reliability.▪ Secured $219K in Cost Savings While Improving Reliability and Increasing MTBM (mean time between maintenance) with the Redesign of an Stimulation Pump Cooling System (including 1500 assets across the globe, valued at $1MM each). Designed a retrofit kit that included design installation changes and removed high-failure components (due to poor ergonomic requirements) as a key member of the stimulation pump design team.▪ Doubled the Oil Lifespans and Reduced M&S Costs with the Design of a Custom Gear Oil Filter Cart.
-
-
Reliability Engineer
-
Jan 2015 - Apr 2017
Designed solutions, processes, and protocols to improve equipment/component reliability, enhance segment service quality, and optimize performance through standardized shop processes while serving as the liaison between field technicians, the technology center, and district level managers.▪ Decreased Rebuild Turnaround Times (TAT) by 87.5%, from 14 days to two days, by creating and mapping a 5S program, designing a toolkit, and supporting the development of standard work instructions. The project was successful and commercialized at a major maintenance shop in Saudi Arabia.▪ Created Local Standardized Quality Testing Processes to identify and resolve equipment/component failures prior to client delivery.▪ Gained the Support, Trust, and Acceptance of Cross-Functional Teams, including engineering, manufacturing, and SMO (sustaining, maintenance, and operations) to initiate major process improvements/business transformations with minimal pushback/resistance in a major economic downturn.▪ Recognized for Cultivating First-Hand Expertise in a myriad of business, manufacturing, engineering, and technical operations through professional development, research, and certifications.▪ Conducted Root Cause Analysis and Investigations to Develop Engineering Solutions using Lean Six Sigma, 5S, and RCM (reliability centered maintenance) methodologies.
-
-
-
Production Resource Group
-
United States
-
Entertainment
-
700 & Above Employee
-
Engineer/Technical Design Intern
-
May 2014 - Dec 2014
Designed and produced AutoCAD drawings for scene shop construction and CNC machines, and performed load analysis.
-
-
Project Management Intern
-
Jun 2014 - Aug 2014
Cost estimation, project scheduling, construction management of assigned projects. Supervised project activities and performed project cost/budget analysis for its duration while serving as a liaison between field teams and engineering. Coded and automated management documents through VBA in Excel.
-
-
-
Monarch Air
-
United States
-
Aviation and Aerospace Component Manufacturing
-
1 - 100 Employee
-
Aircraft Technician Apprentice
-
May 2013 - Aug 2013
Cultivated hands-on expertise in mechanical systems, including regular FAA certified safety inspections, preventive maintenance, nondestructive testing of landing gear (hydraulic systems and structural integrity of wheel assemblies), and engine assembly/installation while concurrently working in the flight school department and earning a private pilot license to gain the perspective of aeronautics from a non-engineering point of view. Cultivated hands-on expertise in mechanical systems, including regular FAA certified safety inspections, preventive maintenance, nondestructive testing of landing gear (hydraulic systems and structural integrity of wheel assemblies), and engine assembly/installation while concurrently working in the flight school department and earning a private pilot license to gain the perspective of aeronautics from a non-engineering point of view.
-
-
-
University of Oklahoma
-
United States
-
Higher Education
-
700 & Above Employee
-
Special Event Coordinator
-
May 2012 - Aug 2012
I planned and organized corporation-funded workshops and orientations for college-bound/middle school students to build foundations in engineering. I planned and organized corporation-funded workshops and orientations for college-bound/middle school students to build foundations in engineering.
-
-
-
Chase Oaks Church
-
United States
-
Religious Institutions
-
1 - 100 Employee
-
Production Team Lead
-
May 2005 - Sep 2008
Starting from a "Tech Team" of 8 members at Fellowship Bible Church North, I was one of the leaders that helped the Chase Oaks Production Team grow to over 50 members and lead a production of contemporary-style worship and sermons every week, managing multiple audio and video systems. Starting from a "Tech Team" of 8 members at Fellowship Bible Church North, I was one of the leaders that helped the Chase Oaks Production Team grow to over 50 members and lead a production of contemporary-style worship and sermons every week, managing multiple audio and video systems.
-
-
Education
-
University of Oklahoma
Bachelor of Science (BS), Aerospace, Aeronautical and Astronautical Engineering -
Université Blaise Pascal (Clermont-II) - Clermont-Ferrand
French Language and Literature
Community
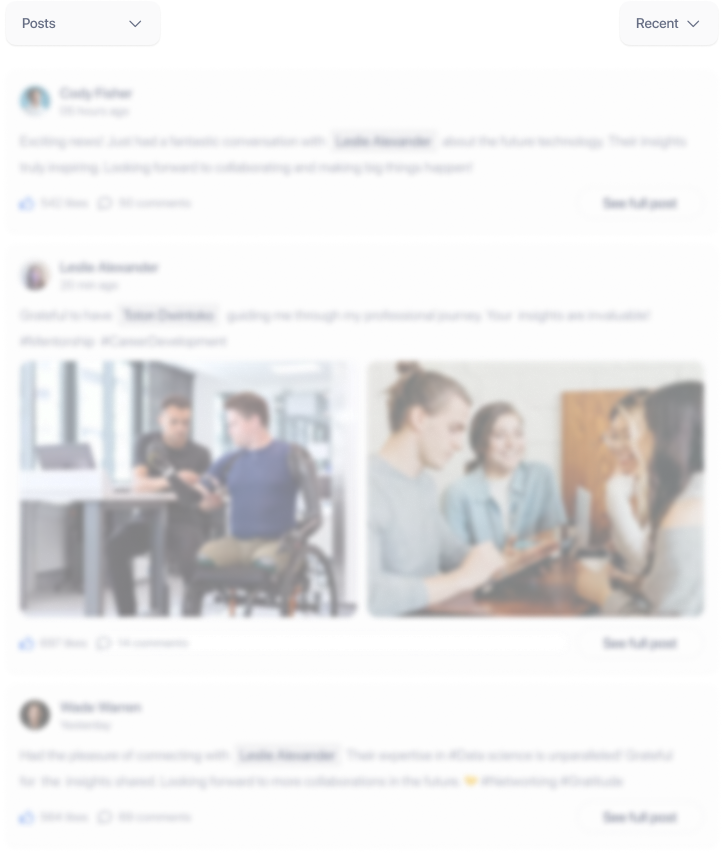