Robinson Balestero
CEO at R3 Professional- Claim this Profile
Click to upgrade to our gold package
for the full feature experience.
-
English Full professional proficiency
-
Spanish Full professional proficiency
-
French Limited working proficiency
-
Portuguese Native or bilingual proficiency
Topline Score
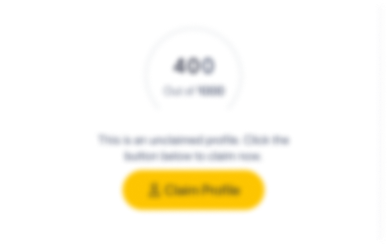
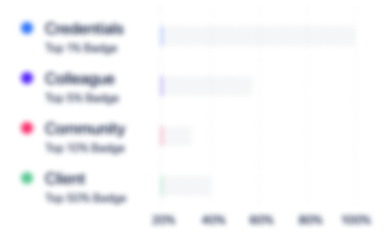
Bio

Carlos Farinha
Robinson is a good definition of a very nice guy. Truly competent and a very good person whose always focused on his tasks and goals related to his challenges during his career. He is a very commited professional with the fully comprehension of his responsabilities and duties and it is a pleasure to recommend him.

Juliano Nogueira
we worked together at Flextronics Instituto de Tecnologia, and he has showed us a high performance on logistic and purchase international process. Also, good behavior and ethic.

Carlos Farinha
Robinson is a good definition of a very nice guy. Truly competent and a very good person whose always focused on his tasks and goals related to his challenges during his career. He is a very commited professional with the fully comprehension of his responsabilities and duties and it is a pleasure to recommend him.

Juliano Nogueira
we worked together at Flextronics Instituto de Tecnologia, and he has showed us a high performance on logistic and purchase international process. Also, good behavior and ethic.

Carlos Farinha
Robinson is a good definition of a very nice guy. Truly competent and a very good person whose always focused on his tasks and goals related to his challenges during his career. He is a very commited professional with the fully comprehension of his responsabilities and duties and it is a pleasure to recommend him.

Juliano Nogueira
we worked together at Flextronics Instituto de Tecnologia, and he has showed us a high performance on logistic and purchase international process. Also, good behavior and ethic.

Carlos Farinha
Robinson is a good definition of a very nice guy. Truly competent and a very good person whose always focused on his tasks and goals related to his challenges during his career. He is a very commited professional with the fully comprehension of his responsabilities and duties and it is a pleasure to recommend him.

Juliano Nogueira
we worked together at Flextronics Instituto de Tecnologia, and he has showed us a high performance on logistic and purchase international process. Also, good behavior and ethic.

Experience
-
R3 Professional
-
Brazil
-
Cosmetics
-
1 - 100 Employee
-
CEO
-
Jun 2021 - Present
Membro do conselho Gestão de portfólio Desenvolvimento de novos produtos Gestão comercial e customer care Supply chain management Gestão e planejamento financeiro Gestão da estratégia de social media Planejamento estratégico Responsável por P&L (lucros e perdas) Membro do conselho Gestão de portfólio Desenvolvimento de novos produtos Gestão comercial e customer care Supply chain management Gestão e planejamento financeiro Gestão da estratégia de social media Planejamento estratégico Responsável por P&L (lucros e perdas)
-
-
-
OnFrontiers
-
United States
-
IT System Custom Software Development
-
1 - 100 Employee
-
Supply Chain Expert
-
Oct 2020 - May 2021
Consulting services for supply chain issues and challenges worldwide. Consulting services for supply chain issues and challenges worldwide.
-
-
-
-
Takeoff Specialist
-
Aug 2020 - May 2021
Takeoff services to enable building painting projects estimating. Use of PlanSwift. Takeoff services to enable building painting projects estimating. Use of PlanSwift.
-
-
-
CSBIM - Consultoria e Soluções em BIM
-
Brazil
-
Civil Engineering
-
Head of Operations
-
Jul 2020 - May 2021
Board member. Deployment of governance best practices. Lean concept launch. People managment best practices introduction. Management of software licenses retail. New business development. Board member. Deployment of governance best practices. Lean concept launch. People managment best practices introduction. Management of software licenses retail. New business development.
-
-
-
-
Head Of Operations
-
May 2019 - May 2021
e-Commerce start-up for elite products on home decor. e-commerce platforms design. Logistics and supply chain structuration. Financial management. Sales & Operations Planning. Social media exposure & management. e-Commerce start-up for elite products on home decor. e-commerce platforms design. Logistics and supply chain structuration. Financial management. Sales & Operations Planning. Social media exposure & management.
-
-
-
fw distribuidora
-
Brazil
-
Motor Vehicle Manufacturing
-
200 - 300 Employee
-
Operations & Finance Superintendent
-
Oct 2018 - Apr 2019
-
-
Supply Chain & Tech Projects Manager
-
Jan 2018 - Sep 2018
Led restructuration project from a family company into a highly professionalized organization:1- Supply Chain:a. Strategic sourcing in China.b. Procurement: Material planning methods implementation.i. 172 suppliers, BRL 455 MM/yr spend.ii. 25k SKUs, coverage 12 to 6 wk, reducing cash flowiii. Average terms 30 to 45 days, 50% of cash opportunityiv. Supplier OTIF 72% to 86%v. Missing parts: -17% inventory disruption.vi. Inventory turns: 2,4 to 1,3. BRL 45 MM obsolete.vii. Price evolution to manage nego, reducing price increasesviii. Supplier day recognizing best one in each category.c. Logisticsi. Goods receipt: Dock to stock lead timeii. Order fulfillment1. Automatic volumes planning2. Picking with data collector3. Conveyor system in warehouseiii. Inventory1. Cycle count and inventory planning2. Root cause analysis.iv. BPR (Business Process Reengineering): analysis and redesign of logistics flows and BP and VSM (Value Stream Mapping).v. Transportation: redesign of inbound and outbound and renego. ~200 providers to 150. BRL 15MM/yr spend to 14MM (-6,7%), 16% organic growth in sales.vi. Overseas and customs clearance for Asia products.2- IT & Telecom: contracts renegotiation. Infrastructure remodeling. Printing and datacenter outsourcing. ERP implementation project (Sankhya). Innovation in sales app, e-commerce platform, CRM and TMS.3- General management:a. Management efficiency tools deployment. Continuous improvement initiatives.b. Led culture change and change management.c. Market assessment and business intelligence. Strategic view on sourcing.d. Head of corporate governance project. Board member.e. Introduction of cost reduction program, with budget and forecastf. Strategic planning for short, medium and long term.g. Stakeholders satisfaction and HPC (High Performance Culture) advancement.h. Branches audit and management Show less
-
-
-
Schneider Electric
-
Appliances, Electrical, and Electronics Manufacturing
-
1 - 100 Employee
-
Regional Sourcing Manager for South America, Global Supply Chain
-
May 2017 - Jan 2018
Strategic sourcing management for indirect purchasing (non production purchases) for South America on industrial means, professional services, real estate, IT and telecom.
-
-
Regional Commodity Manager, Logistics Purchasing for South America, Global Supply Chain
-
Sep 2015 - May 2017
Logistics purchasing for South AmericaSupplier development and sourcing for Full Truck (FTL) and Less than Truck (LTL) for inbound, outbound, and Lead Transport Provider (LTP).3PL development for warehouses and regional customs broker. Insurance coverage.MSA with SLA and contract analysis.RFP/RFQ bids via Ariba, e-Reverse Auctions to maximize savings.Supplier reduction and concentration programs and Supplier Base Optimization.Spend on South America of 21 MM EUR. Yearly savings at 1.6 MM EUR. Main negotiations:1. Change of major outbound supplier for Brazil. Yearly savings of 7.5% by changing 3PL logistics operator by transportation company. Implementation plan with 9 waves to keep SLA at 98,5% and avoid services disruption.2. Forklifts. Savings at 27% with e-Reverse Auction in 2 months negotiations.3. Main DC (São Paulo) services to obtain licenses for operations. Savings of 66% with competitiveness strategy.4. 3PL DC and outbound operations in Recife, PE. Bid and negotiations over 3 months. Expected savings at 15%.5. Merging of 2 DCs at Bogotá, Colombia.6. Outbound flows in Colombia. 41% savings in 3 months negotiations.7. Airfreight outbound nationwide in Brazil. 38% savings in 3 months negotiations.8. Sensitive equipment delivery. All offer above baseline. Managed e-RA and attained 9% savings.9. Outbound of big extra dimensions cargo. Several spot nego due to project profile with several savings range.10. Strategy of changing road transport for long distances to multi modal (road and cabotage) to reduce costs.11. Should-cost methodology on "commodities" like freight to drive competitiveness12. TCO (Total Cost of Ownership) to attain better results in P&L impact.13. Tech savings by optimizing resources and improving processes.Regular Business Reviews with suppliers to manage service level and KPIs. Quarterly BRs with stakeholders to fine tune goals. Show less
-
-
-
FIT - Instituto de Tecnologia
-
Brazil
-
IT Services and IT Consulting
-
400 - 500 Employee
-
Senior Supply Chain Consultant
-
Apr 2015 - Sep 2015
FIT Flextronics Institute of Technology: prototype builds and automation/innovation for electronic industries and CMs (Contract Manufacturers). Projects run over R&D incentive law in Brazil. BPTW for 5 years. Materials Management Consultant for Motorola smartphone prototypes Materials Planning Procurement: international vendors (most in Asia) Support for deployment of ERP Baan Materials process mapping and revision POs over BOM Interfacing customer materials area Supplier management Clear To Build (CTB) Material support for NPI and dogfooding E&O (Excess & Obsolete) analysis and management Show less
-
-
-
Alstom Transport
-
United Kingdom
-
Automotive
-
700 & Above Employee
-
Supply Chain Director
-
Jan 2013 - Sep 2014
LOGISTICS: inbound, outbound, handling, cycle counts, WMS, biometric access, BOM reliability, C-Class under/over consumption, webEDI supplier communication, milk run. KPIs: Accuracy 32% to 98%. OTIF 32% to 90%. Internal OTIF 85% to 96%. Missing parts: 3,5% to 0,9%. Freight -13%. METHODS LOGISTICS: Pull, push flows, Kanban, JIT, contractualized log specs, ERP parameters, line feeding racks (productivity + ergonomics), reverse logistics, recycling +25%. Continuous improvement, best practices, benchmarking, lean, VSM, Process Mapping, Kaizen, QRQC, 5S, 5 why's, Fishbone, etc. PROCUREMENT: Stock projection, budget, MRP parameters, ERP focus. Material planning: QCD, inventory and OTIF levels, suppliers capacity audits, postponement. Automatic release. MRP over BOM and exemptions treated. Takt time 4,5 to 2 days. Sourcing strategy (int'l, national), supplier development and performance, budgeted negotiation, contract fulfillment. Outsourcing strategy. EUR 900MM annual revenues, EUR 680MM budget, 230 suppliers. Procurement Centers: synergy: buyer + mat planner + quality. KPIs: inventory coverage 12 to 7 weeks; hard inventory Delta -3%; RM and missing parts 2,6% to 0,4%; obsolete -85%; budget -7%; 12% suppliers renewal; 23 critical backup suppliers. IMPORT/EXPORT: equipment imports, ex-tarifário, drawback, process simplification, Linha Azul, international cross-dock platforms, cash flow focus, SAP interface. Customs 15 to 4 days, -47% freight. Saved EUR 15MM drawback penalties. PLANNING (Industrial, Project, Production): strategic planning, S&OP, demand fluctuations forecast, workload simulations, bottlenecks management, demand forecasting, retro planning projections. FUP engineering releases. WOs management (routes, control, closure). Missing root cause. MPS production schedule. WOs per cycle time. KPIs: MPS accuracy 0% to 80%. OTD 0% to 70%. Inter company OTIF 41% to 78%. SL (Service Level) 0% to 87%. Show less
-
-
-
SCHWING Equipamentos Industriais Ltda.
-
Brazil
-
Machinery Manufacturing
-
1 - 100 Employee
-
Senior Supply Chain Manager
-
Jan 2012 - Dec 2012
PROCUREMENT: Budget $60MM/yr. Portfolio renegotiation saved +3%/yr. Improved production needs follow-up. Postponement. Key suppliers development. Sourcing of Brazilian suppliers to qualify for FINAME (~2.5%/yr). Set metrics to check suppliers performance. Cost reduction and outsourcing strategy. S&OP, demand fluctuation. LOGISTICS: inbound, outbound, operations and inventory. Start-up of new branches with warehouse. Audited stock-taking. Reduced 17% inventory ($26.5MM to 22MM). Increased accuracy from 94 to 98% by (a) updating SKU records, (b) accurate checking at receiving, (c) improvement in counting process, (d) monthly cycle counting, (e) clearing obsolete parts, (f) implementation of JIT with key suppliers, (g) postponement, (h) warehouse integration, and (i) addressing of stock positions. Decreased inventory turnover in 20%. Deployed total logistics cost reduction. Increased order fulfillment in 25% by consolidating parts into kits. Deployed Kanban, JIT (Just In Time) and VMI (Vendor Management Inventory) to reduce inventory level and increase supplying punctuality. Increased follow-up level. Deployed process improvement in storing material and orders processing. PRODUCTION PLANNING: Enhanced sync of production with customer orders. Created mapping for missing parts. Scheduling of production slots. Order cost management. Turned MRP more accurate and timely. SAP automatic TAKT calculation. Discontinued parallel controls reducing human error and rework inefficiency. Focused SAP transactions. Deployed lean practices (5S, Kaizen, Kanban, Poka-Yoke). IMPORT/EXPORT: Savings: (a) $0.5MM/yr demurrage (negotiations and dynamic unloading). (b) $21MM/yr cash flow. (c) $1MM/yr storage, (d) $2.5MM/yr freight. Bonded warehouse, exchange rate strategy, fiscal benefits strategies (drawback), etc. GENERAL: Start-ups, ERP SAP/R3 materials management tools. Reduced headcount in 15%, increased efficiency in 12%. Budget fulfillment, Make To Order and Make To Stock. Show less
-
-
-
Multi Holding
-
Brazil
-
Education Administration Programs
-
1 - 100 Employee
-
Supply Chain Director
-
Aug 2009 - Dec 2011
PLANNING: Lead S&OP process. Demand fluctuation forecast. Ability to Project forecast and buget, as well as to assess the breakeven point for purchase packages. Expert in taxation analysis on the supply chain. INBOUND LOGISTICS: Management of inbound processes: goods receipt, storage, stock control (raw material, WIP, finished products, goods for resale), inventory accounting, Operations Logistics: Production control and scheduling supported by ERP and MRP. WebEDI interface with customers. Production metrics management. Inventory management (ABC analysis). Audited inventory accounting to close yearly financial statements. OUTBOUND LOGISTICS: Management of outbound processes: picking, packing, invoicing, shipping, transportation, export operations. Reverse logistics. PURCHASING/PROCUREMENT: supplier development national and internationally (especially China), strategic sourcing, costs management, new products viability analysis, supplier performance analysis, postponement, import operations with focus on cost reduction and taxation strategy to take advantage of any fiscal benefits available for each operation format, competitiveness through strategic outsourcing. SUPPLY CHAIN MACRO MANAGEMENT: Management of several KPIs (accuracy, cycle time, lead time, stock average cost, inventory turns, productivity, etc.) as well as financial metrics (P&L, budget, EBITDA, revenue, etc.) and managing accounting. Daily follow-up on indicators, reviewing goals. Strong strategic focus, strategic planning process, defining mission, vision and values. Participation on business plan reviews and analysis. Adopting best practices and continuous improvement (Kaizen). Close management on supply chain costs and results. Project overseeing (analysis on viability, investments, risks, ROI, IRR, payback, breakeven, etc.) Specialist in people management. Flexibility, versatility and diplomacy. Show less
-
-
-
Autocam Corporation
-
India
-
Motor Vehicle Manufacturing
-
1 - 100 Employee
-
Supply Chain Manager
-
Feb 2001 - Jul 2009
Oversight and management of all supply chain operations in 3 plants in Brazil. Member of Global Supply Chain Committee based in Grand Rapids, MI, USA. Constant contact with supply chain teams worldwide to make sure overall guidelines are followed. Regional purchasing for South America operations. Steel commodities large negotiations. LOGISTICS: inbound and outbound, inventory control and demand management (ABC analysis) inventory strategies, shipping and receiving oversight, transport management, taxation on the supply chain; SOURCING/PROCUREMENT: Domestic suppliers development, as well as in Europe, US, Asia and China. Deep knowledge of the automotive supply chain requirements. Sourcing of commodities such as special steel league bars, tubes, aluminum and stainless steel rods, generic raw material, components, (machined and forged blanks, pre-machined parts, etc.), tooling, and several new and used machines, such as CNC multispindle lathes and wide variety of machine tool. Oversight suppliers’ evaluation. Strategic sourcing. Directed supplier base in Brazil and internationally, Directed main negotiations, especially contracts and agreements at millions of dollars. SUPPLY CHAIN: Directed program for analyzing high quality, constant cost reduction due to productivity or else, budget management. Daily follow-up on purchasing schedules. Directed procurement development for attaining savings target, cost reduction and profit. Development of policies for supplying, the metrics for evaluating supplier, the strategies for minimizing risks and maximizing results. Show less
-
-
-
-
International Business Manager
-
Oct 1996 - Feb 2001
Setting up of a complete export department Exports management Exchange and payment control Customs clearing New business development abroad Setting up of a complete export department Exports management Exchange and payment control Customs clearing New business development abroad
-
-
-
ESTRELA DO VALE
-
Brazil
-
Truck Transportation
-
1 - 100 Employee
-
Finance and Administration Manager
-
Sep 1995 - Oct 1996
Financial strategies Company restructuration Costs management HR, IT, inventory and logistics management Financial strategies Company restructuration Costs management HR, IT, inventory and logistics management
-
-
-
-
Import Export Supervisor
-
May 1991 - Sep 1995
Setting up of a complete export department Exports management Exchange and payment control (includes L/C [Letter of Credit]) Customs clearing New business development abroad. Setting up of a complete export department Exports management Exchange and payment control (includes L/C [Letter of Credit]) Customs clearing New business development abroad.
-
-
-
IBM
-
IT Services and IT Consulting
-
1 - 100 Employee
-
Senior Assembly Technician
-
Aug 1990 - May 1991
Assembling and testing of mainframes. Assembling and testing of mainframes.
-
-
Education
-
Fundação Getulio Vargas
MBA Executive, Logistics, Materials, and Supply Chain Management -
Babson F.W. Olin Graduate School of Business
MBA Executive, Entrepreneurship -
Universidade Paulista
BA, International Bussiness
Community
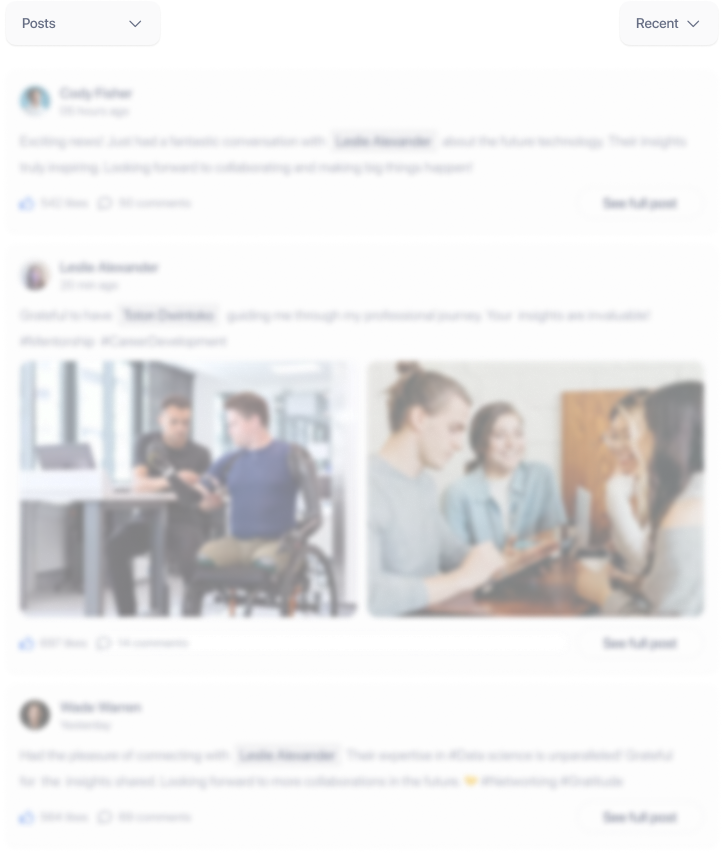