Robert Kapel
Chief Operating Officer at Apotheek A15- Claim this Profile
Click to upgrade to our gold package
for the full feature experience.
-
English Full professional proficiency
-
Dutch Native or bilingual proficiency
-
German Elementary proficiency
Topline Score
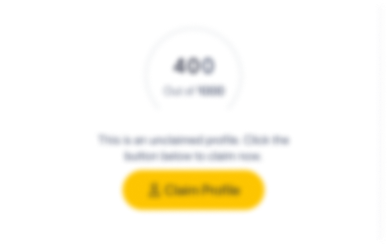
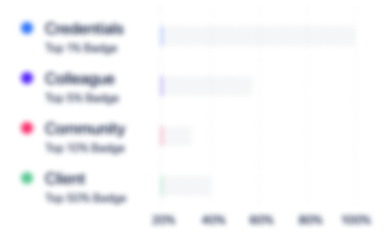
Bio

Arjan Kok
Robert had been my manager for a couple of years and I would never hesitate to work for him again. I have seen him successfully heading Operations where he created harmony amongst team managers by creating trust, being approachable, emphatic, honest and with a sense of humor. Robert is the type of manager who gets results by empowering, supporting and inspiring his reports to get the best out of themselves. True people manager.

Olivier Larue
In May 2010 Kapel Robert attended and successfully completed the Ydatum / Merck advanced MPS Lean seminar in Oss, Holland. During the course, Kapel Robert demonstrated an advanced understanding of the principles and techniques behind lean, as well as strong leadership.

Arjan Kok
Robert had been my manager for a couple of years and I would never hesitate to work for him again. I have seen him successfully heading Operations where he created harmony amongst team managers by creating trust, being approachable, emphatic, honest and with a sense of humor. Robert is the type of manager who gets results by empowering, supporting and inspiring his reports to get the best out of themselves. True people manager.

Olivier Larue
In May 2010 Kapel Robert attended and successfully completed the Ydatum / Merck advanced MPS Lean seminar in Oss, Holland. During the course, Kapel Robert demonstrated an advanced understanding of the principles and techniques behind lean, as well as strong leadership.

Arjan Kok
Robert had been my manager for a couple of years and I would never hesitate to work for him again. I have seen him successfully heading Operations where he created harmony amongst team managers by creating trust, being approachable, emphatic, honest and with a sense of humor. Robert is the type of manager who gets results by empowering, supporting and inspiring his reports to get the best out of themselves. True people manager.

Olivier Larue
In May 2010 Kapel Robert attended and successfully completed the Ydatum / Merck advanced MPS Lean seminar in Oss, Holland. During the course, Kapel Robert demonstrated an advanced understanding of the principles and techniques behind lean, as well as strong leadership.

Arjan Kok
Robert had been my manager for a couple of years and I would never hesitate to work for him again. I have seen him successfully heading Operations where he created harmony amongst team managers by creating trust, being approachable, emphatic, honest and with a sense of humor. Robert is the type of manager who gets results by empowering, supporting and inspiring his reports to get the best out of themselves. True people manager.

Olivier Larue
In May 2010 Kapel Robert attended and successfully completed the Ydatum / Merck advanced MPS Lean seminar in Oss, Holland. During the course, Kapel Robert demonstrated an advanced understanding of the principles and techniques behind lean, as well as strong leadership.

Experience
-
Apotheek A15
-
Netherlands
-
Pharmaceutical Manufacturing
-
1 - 100 Employee
-
Chief Operating Officer
-
Apr 2020 - Present
Responsible for: -Production -Quality Control -Operational Support -Procurement -Business Excellence (continuous improvement, LSS) -Facility Management Apotheek A15 is a state-of-the-art GMP manufacturing / QC unit in Gorinchem. Apotheek A15 is a collaboration between Erasmus MC, UMC Groningen, Radboud UMC and UMC Utrecht. Responsible for: -Production -Quality Control -Operational Support -Procurement -Business Excellence (continuous improvement, LSS) -Facility Management Apotheek A15 is a state-of-the-art GMP manufacturing / QC unit in Gorinchem. Apotheek A15 is a collaboration between Erasmus MC, UMC Groningen, Radboud UMC and UMC Utrecht.
-
-
-
ProQR Therapeutics
-
Netherlands
-
Biotechnology Research
-
100 - 200 Employee
-
VP Operations
-
Nov 2015 - Apr 2020
Responsible for Operations, originally consisting of:-Quality Assurance (QA Manager, QP and QA Specialists)-Human Resources (general HR, L&D and Recruitment)-Facility / Lab Management-Safety (EHS, BSO, CSO, BHV)-Information Technology / Information Management-Intellectual Property-Legal (company lawyers)HR, IP and Legal were split off from Operations in 2018. Compliance focus of Operations increased, including e.g. information security and privacy, management reporting, ERMReporting to CEO. Member of Leadership Team. Show less
-
-
Senior Director Quality Release
-
Nov 2014 - Oct 2015
Responsible for all batch release related activities (DS, DP / IMP), quality management, incl. support/guidance in QMS development, performing internal and external audits, providing (internal) trainings.As member of 'Happy Unit' involved in definition and implementation of 'Habits of Happiness'.Qualified Person.
-
-
-
Rescop
-
Netherlands
-
IT Services and IT Consulting
-
1 - 100 Employee
-
Corporate Director Quality & Process Management
-
Feb 2014 - Oct 2014
Responsible for set up and development of new branch of consultancy services within Rescop B.V., regarding 'Quality & Process Management'. March 2014 – August 2014: interim Director Business Development & Operations NL. Responsible for operational management of NL Organization (approx. 25 consultants, via 3 team leads). Assignments (50% of time): March 2014 – April 2014: QMS gap assessment at Bilthoven Biologicals. April 2014 – July 2014: batch release en deviation management at Sharp Packaging Solutions. June 2014 – October 2014: support set up of QMS, perform audits and back-up QP role at ProQR. Provided several trainings (e.g. quality management, deviation and CAPA handling, continuous improvement) in time period March - October 2014. Show less
-
-
-
Merck
-
United States
-
Pharmaceutical Manufacturing
-
700 & Above Employee
-
Associate Director Quality Assurance (QA Manager)
-
May 2011 - Jan 2014
Manager of Quality Assurance department (14 FTE). May 2011 (i.e. directly after reorganisation) started with 'brand new team', without the experienced QA Officers of the former department. First focus was ‘installation’ (a.o. management of work, installation of meeting/consultation structure, knowledge and team building). Step by step extended to a more strategic role/approach.Responsible for 'Quality Management' (owner subsystem 8 'Quality Management') within Pharmaceutical Operations. Member of steering committees for all medium and large (investment) projects. Chairman of change control board.From October 2012 to May 2013 additional function as Pharmaceutical Specialist Level 3, to manage backlog in batch record and deviation / CAPA handling and to manage the Pharmaceutical Specialist team. Received gratification for achieving all goals. Show less
-
-
Project manager MPS (Merck Production System) Team - Org Design
-
Jan 2010 - May 2011
Project responsibility for the complete design of the new Pharmaceutical Operations organization in Oss (approx. 1000 FTE). This design was based on an in depth analysis of all key processes within the Pharmaceutical Operations organization, and application of relevant lean principles. Responsible for e.g. correct analysis of relevant data, design of new org structure, set up of job descriptions, adaptation of the QMS.At the same time sub system owner 'environmental control' (responsible for compliance in this area) and involved in implementation of visual management (to support management tier processes). Show less
-
-
Head Production Quality Team MBU Parenterals, Sr Production Pharmacist
-
Apr 2004 - Jan 2010
Responsible for set up of Quality Team within steriles production department (2 FTE in 2004, 7,2 FTE in 2010).As a Production Pharmacist, responsible for batch (record) handling within production, for both bulk production and packaging activities. In line, responsible for deviation and CAPA handling, change management, validation (master planning), guiding inspectors (internal and external), introduction of new products / processes and supporting continuous improvement. Besides roles and responsibilities ´Production Pharmacist´, in the course of time increasing focus on people management, quality management and continuous improvement. Responsible for both existing facility (CO) and new facility (CP), that was built in this period. For CP heavily involved in set up of (quality) systems, transfer of first product (Esmeron) and first successful IGZ inspection. Show less
-
-
-
Organon
-
United States
-
Pharmaceutical Manufacturing
-
700 & Above Employee
-
Trainee Qualified Person
-
Dec 2001 - Apr 2004
Trained as Qualified Person. Involved in several (improvement) projects in various departments (e.g. production, regulatory, clinical). Trained as Qualified Person. Involved in several (improvement) projects in various departments (e.g. production, regulatory, clinical).
-
-
Education
-
Utrecht University
Pharm. D., Pharmacy
Community
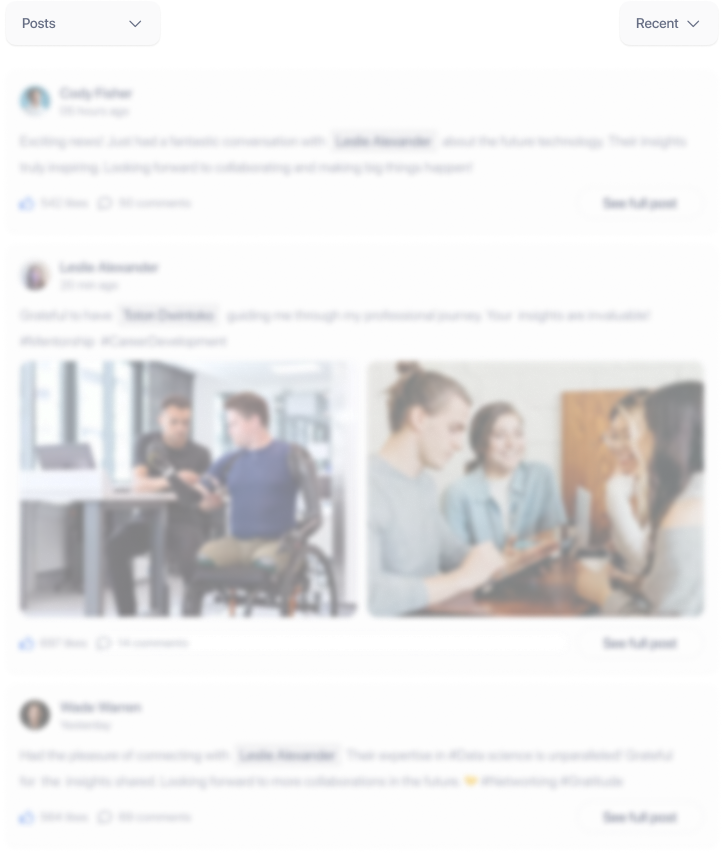