Robert Dolman, CAPM
Data Analyst at American Tissue Corp- Claim this Profile
Click to upgrade to our gold package
for the full feature experience.
Topline Score
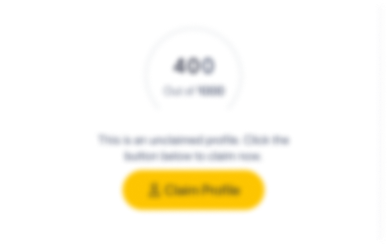
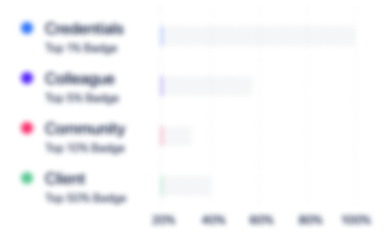
Bio


Credentials
-
Certified Associate in Project Management (CAPM)
Project Management InstituteApr, 2021- Oct, 2024
Experience
-
American Tissue Corp
-
United States
-
Manufacturing
-
1 - 100 Employee
-
Data Analyst
-
Aug 2021 - Present
-
-
Data Analyst
-
Aug 2021 - Present
Provide the Plant Manager and manufacturing teams with production data analysis and reports to support plant activities to achieve Key Performance Indicators (KPI) and manufacturing goals.Analyze production data to identify trends and anomalies, prepare summary findings, reports and presentations, alert appropriate departments on findings.Perform production modeling activities on current and future SKU’s to determine optimal line loading, production rates, operating efficiency, total efficiency and capacity utilization for optimum monthly production scheduling and future year production forecast.Update Production reporting using VBA and SQL queries.Creating and formulating automated reports as needed for all departments.Create advanced tracking reports for Operation Efficiency, Metric Tonnage, Time Efficiency, Total Efficiency and COGM.Monthly, Quarterly and Yearly computing, and tracking of KPI goals.Perform detailed analysis to identify process improvement activities in the manufacturing process.Perform cost savings analysis to determine payback and rate of return for cost justification on potential CAPEX projects.Complete various month-end production related reports and distribute internally, to HQ teams, and outside departments. Show less
-
-
-
Armacell
-
Luxembourg
-
Building Materials
-
700 & Above Employee
-
Plant Production Supervisor
-
Jan 2020 - Mar 2021
● Manage safety, quality, delivery, cost and morale to achieve positive results and KPI. ● Manage department priorities, schedules, all production associates time and attendance. Analyzes data while investigating issues around quality and correction planning. ● Demonstrated experience coaching, developing and leading a team of 55+ direct reports. ● Manages departmental performance measures, goals, controls and provides regular feedback to production managers. ● WCM Environmental Pillar leader, responsible for reducing the environmental impact of the Plant. Show less
-
-
-
-
Co-Owner
-
May 2017 - Mar 2020
● Maintain and manage operations of $500,000 private equity venture. ● Managed residential renovation projects from start to finish. ● Analyze real estate markets for investment opportunities. ● Prepare investment packets and presentations for investors. ● Approach and develop new investors. ● Manage operations and coordinate with lenders. ● Maintain and manage operations of $500,000 private equity venture. ● Managed residential renovation projects from start to finish. ● Analyze real estate markets for investment opportunities. ● Prepare investment packets and presentations for investors. ● Approach and develop new investors. ● Manage operations and coordinate with lenders.
-
-
-
ECS Federal
-
United States
-
Industrial Machinery Manufacturing
-
1 - 100 Employee
-
Fundamental Maintainance Skills Training Instructor
-
Nov 2017 - Jun 2018
● Delivered 8-day training courses on basic electronics troubleshooting to a class of 12 to 24 students for the purpose of maintaining US Postal mail sorting equipment. ● Developed curriculum to reduce class length from 10-days to 8-days. ● Trained over 200 US Postal employees without a single failure. ● Utilized training equipment, supplies, facility and fiscal resources to implement and deliver approved training programs in the classroom and lab. ● Managed training activities to ensure course objectives are met and maintained all lab equipment. ● Evaluated students’ performance and provided feedback throughout training. Show less
-
-
-
-
Production Control Manager
-
Aug 2012 - Apr 2017
● Analyzed customer demand information, forecasts, orders, machine, labor and material availability to develop a flexible yet efficient master schedule that supported company goals and budget. ● Coordinated with Sales, Engineering, and Production to meet master schedule. ● Led a team of Supervisors that increased on-time delivery, inventory turns, and gross margins year over year. ● Planned, scheduled, coordinated, and approved the release of production orders to manufacturing based on material and capacity availability. ● Provided input to management and/or interfaced with customers when rescheduling was required due to design changes, labor and material shortages, backlogs and other potential schedule interruptions ● Instrumental in developing ERP reports and worksheets that supported production planning, capacity planning, and operational management. ● Implemented continuous improvement methods to reduce cycle times and inventory. ● Presented the status of key initiatives to upper management monthly. Show less
-
-
-
Cannon Spring Company
-
United States
-
Accounting
-
Operations/Quality Management Consultant
-
Jun 2011 - Aug 2012
● Implemented the 5S method to develop an organizational culture of continuous improvement. ● Mentored staff through the implementation of ISO 9001: 2008. ● Analyzed effectiveness of the Quality Management System for management. ● Performed safety and technical training. ● Wrote and implemented ISO processes, procedures, and work instructions throughout the company. ● Project Manager for the new company website. ● Implemented the 5S method to develop an organizational culture of continuous improvement. ● Mentored staff through the implementation of ISO 9001: 2008. ● Analyzed effectiveness of the Quality Management System for management. ● Performed safety and technical training. ● Wrote and implemented ISO processes, procedures, and work instructions throughout the company. ● Project Manager for the new company website.
-
-
-
-
Lead Coiler
-
Jul 2007 - Nov 2010
● Worked with management and engineering to establish a new spring manufacturing line for the Vehicle Component Manufacturing division. ● Instrumental in training new hires to support the move of Betts Spring manufacturing plant from San Leandro, CA to Fresno, CA. ● Developed and prepared technical manuals and work instructions for spring manufacturing equipment. ● Set-up and manufactured all prototype designs. ● Worked with management and engineering to establish a new spring manufacturing line for the Vehicle Component Manufacturing division. ● Instrumental in training new hires to support the move of Betts Spring manufacturing plant from San Leandro, CA to Fresno, CA. ● Developed and prepared technical manuals and work instructions for spring manufacturing equipment. ● Set-up and manufactured all prototype designs.
-
-
-
Warhall Designs
-
Construction
-
1 - 100 Employee
-
Production Manager
-
2005 - 2007
● Managed shop labor and supplies to ensure on-time delivery. ● Performed all CAD and CAM programming for Intermac granite mill. ● Coordinated with installation teams to ensure customer satisfaction. ● Managed shop labor and supplies to ensure on-time delivery. ● Performed all CAD and CAM programming for Intermac granite mill. ● Coordinated with installation teams to ensure customer satisfaction.
-
-
Education
-
Southern Nazarene University
Bachelor's Degree, Organizational Leadership -
US Navy Nuclear Field Electronics Technician "A" School
Industrial Electronics Technology/Technician -
Southern Nazarene University
Bachelor of Science - BS, Organizational Leadership
Community
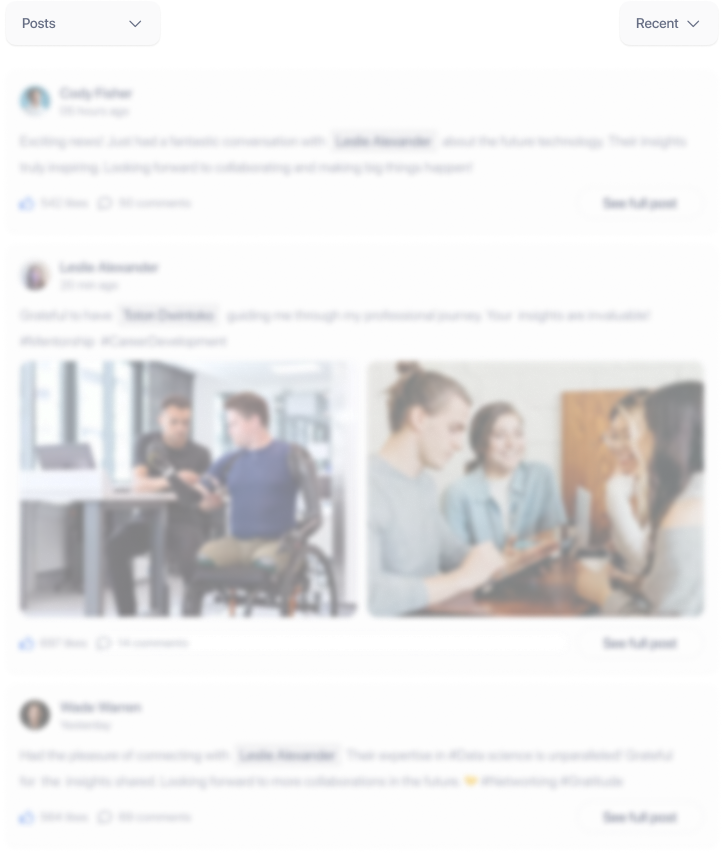