Robert Ross
Senior R&D Program Manager at Metronom Health- Claim this Profile
Click to upgrade to our gold package
for the full feature experience.
Topline Score
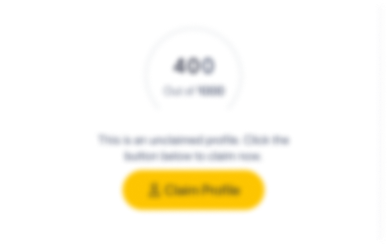
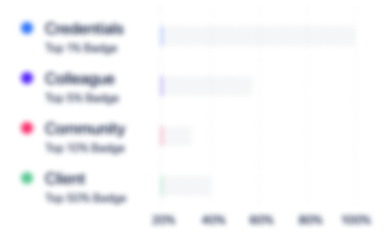
Bio


Experience
-
Metronom Health
-
United States
-
Medical Equipment Manufacturing
-
1 - 100 Employee
-
Senior R&D Program Manager
-
Apr 2020 - Present
Reported to the Senior VP of R&D and Manufacturing. Led a multidisciplinary multinational team in the development of an implantable Continuous Glucose Monitor (CGM) from bench-top concept to clinical trial readiness. Orchestrated all activities in a fast-paced start-up with over 100 resources with levels from operators, technicians, engineers, PHD’s and directors. Product required management of engineering disciplines including, Mechanical Design, Molding, Process Development and Manufacturing, Electronic Component Development, Firmware, Software, Development of IOS apps, Chemistry and Optics. Responsibilities: -Assist management with resource planning, utilization, and justification of R&D business resources. -Manage highly complex projects, or a combination of projects, or a project portfolio. -Provides project management support for research and development. -Manages projects and/or assists project managers identify resource requirements, cost and time schedules. -Develop an implementation plan, conduct risk assessments, and develop and implement contingency plans to allow for and accommodate unforeseen events and changes in strategy. -Interface with other disciplines, customers, internal clients, project staff and internal and external experts as required. -Prepare and present written and oral reports and other presentations to internal and external audiences. -Interact with senior level management to reach agreement regarding significant program strategies. -Accountable for the successful completion of project tasks on time and within budget. -Accountable for managing resources (direct and matrix) assigned to project regarding project tasks. -Identify potential problem areas and implement corrective actions as needed. -Provides leadership for project management and training of project managers. Show less
-
-
-
Medtronic
-
United States
-
Medical Equipment Manufacturing
-
700 & Above Employee
-
Engineering Program Manager
-
Jul 2017 - Apr 2020
Led a multinational team to develop and commercialize a Peripheral Vascular Occlusion Implantable device. Responsible for the overall operations aspects including value stream selection, planning, execution and successful implementation of activities in the development and introduction of new products. Key voice of Operations in Core Teams, leads a cross functional team, responsible for ensuring the voice of operations is properly captured, and all team commitments and project contract metrics are met and communicated in a timely manner. • Lead cross functional teams including Design, Manufacturing, Supply Chain, Off-shore facilities and Quality functions through the product development process to ensure successful completion of development projects and business goals. • Responsibility for all Operations activities in product development planning and execution • Responsible for developing, communicating, and documenting project strategies and plans including operations budget and detailed schedule creation and maintenance • Overall value stream development and process responsibility from technology through market release. • Responsible to drive the Design Transfer activities • Ensure Operations aspects of Quality System Compliance, Design History File, and Regulatory Submissions • Coordinate Development builds • Lead the manufacturing and supply chain schedule risk burn down • Champion manufacturing strategy and sourcing strategy for program • Lead decision making for facility locations, make-buy decisions, business continuity. • Define and meet operations objectives: Labor, Burden, Material, Cycle Time, Capacity, First Run Yield, • Cumulative Yield, Process Ppk, etc • Ensure Design for Reliability and Manufacturing (DRM) • Facilitate launch build planning, capacity planning and execution and Commercialization Readiness activities • Champion Product Costing efforts • Indirect People Management, Coaching & Development Show less
-
-
-
Edwards Lifesciences
-
United States
-
Medical Equipment Manufacturing
-
700 & Above Employee
-
Principal Engineer
-
Mar 2013 - Jul 2017
Manufacturing Engineering Lead (2015-Present)Lead/guide the development of pilot line capabilities, equipment and processes to manufacture a catheter based delivery system required to deliver a mitral valvular implant.Responsibilities include:-Support R&D design; provide DFM guidance-Line and Station Layout-Fixture/Equipment Development/Implementation-Process Development (DOEs)/Improvement-Define/develop SOP-Validations: IQ, TFIQ, OQ, PQ Protocols and Reports-Develop/Manage project plans and timelines-Track tasks in a cross-functional organization-Manage Build Schedule and Clinical Inventory-Provide Guidance to team membersSustaining Engineering/Project Leader (2014-2015)Led the conversion of over 230 product models produced in Critical Care sold in France representing $1.2MM/month in revenue.Responsibilities include:-Develop Project Plans/Define Scope.-Project management of cross-functional teams. Manage Quality, Manufacturing, Regulatory, and R&D resources from Irvine, Dominican Republic, and Puerto Rico-Develop and drive project timeline-Track tasks, Present/communicate to Sr. Management-Design Control compliance-Lead/complete Commercial Design Review activities-Develop/validate new product configurationsProcess Development Engineering Lead (2013-2014)Lead process development and validation of new in-vivo continuous glucose monitoring device.Responsibilities include:-Cleanroom design/construction/validation-Equipment transfer, process development, DOEs and validation.-IQOQPQ Protocols/Reports-Vendor Management-Product development-Fixture design/development/implementation Show less
-
-
Staff Engineer
-
Jan 2011 - Mar 2013
Design Transfer Lead (2012-2013)Lead transfer and pre-commercial activities for a disposable pressure monitor device as part of a new continuous glucose measurement device.Responsibilities include:-Support R&D design; provide DFM guidance-Line and Station Layout-Fixture/Equipment Development/Implementation-Process Development (DOEs)/Improvement-Define/develop SOP-Validations: IQ, TFIQ, OQ, PQ Protocols and Reports-Develop/Manage project plans and timelines-Track tasks in a cross-functional organization-Manage Build Schedule and Clinical Inventory-Provide Guidance to team membersOperations Integrator (2011-2012)Support the transfer of an arterial pressure monitoring device to internal production facility in Puerto Rico.Responsibilities include:-Process Development (DOEs)/Improvement-Identify/implement yield improvements-Define/develop SOP-Lead/contribute in Validations: IQ, TFIQ, OQ, PQ Protocols and Reports-Develop/Manage project plans and timelines-Track tasks in a cross-functional organization-Develop/implement operations strategy-Develop/manage product Phase-in/Phase-out strategy Show less
-
-
-
BD
-
United States
-
Medical Equipment Manufacturing
-
700 & Above Employee
-
Project Engineer
-
Jan 2005 - Jan 2011
Manufacturing Lead (2008-2011) As project engineer, identify/develop and implement manufacturing equipment and process to produce a new high-volume disposable capillary blood containment and testing device (BD Microtube for Automated Process). Responsibilities included: -Develop/implement MFG strategy -Identified/drafted machine specifications/procured equipment -Manage vendors on time/cost/quality -Develop/Execute FAT/SAT Protocols/Reports -Develop non-disclosure agreements -Develop product cost analysis -Business plan development -Develop process development lab/equipment to prove process. -Lead/contribute in Validations: IQ, TFIQ, OQ, PQ Protocols and Reports -Develop/Manage project plans and timelines -Lead Process Development/GR&R/DOE activities -Manage Engineering Resources Project Leader (2007-2008) Assigned by WW Director of Manufacturing to increase the capacity of a highly demanded blood containment device by 25MM units/year within a 3 month time period. Responsibilities included: -Project management of cross-functional teams including QA, MFG, RA, and R&D resources from Corporate (New Jersey) and Puerto Rico. -Develop Project Plan/timeline/Define Scope. -Drafted machine specifications/procured equipment -Develop/Execute FAT/SAT -Track tasks, Present/communicate to Sr. Management -Design Control compliance -Lead/contribute IOPQ Manufacturing Lead (2005-2007) Lead for the project management and delivery of three large-scale automated manufacturing machines representing 10% of a $95M capital investment project required to produce $25MM in annual revenue of a new blood acquisition device. Responsibilities Included: -Manage vendors to time/cost and quality requirements -Develop/Execute FAT/SAT Protocols/Reports -Managed Delivery/installation of equipment -Trained personnel -IOPQ Protocols and Reports -Manage Engineering Resources -Developed and drove cross-functional tasks across three countries and between plant site in South Carolina and Corporate HQ Show less
-
-
-
DT Industries (Med Device Automation Assembly Equipment OEM)
-
Rochester, New York Area
-
Mechanical Engineer - Lead
-
Jun 1999 - Jul 2002
DT Industries - a mid-sized OEM providing mid-high volume automated assembly systems to the medical device industry. Assigned as lead mechanical designer on major projects sold to Becton Dickinson and Medtronic. Responsibilities Included: -Designed Automation Assembly Equipment and technologies -Worked with Controls Engineers to develop automation solutions -Developed and integrated inspection and detection systems -Led and developed internal process development lab to prove assembly concepts -Developed proposals for internal sales department/proposed to external clients -Completed documentation required to build equipment -Completed drawing files as per internal quality system requirements. -Specify Spare parts components -Managed build team to complete assembly of equipment per schedule. -Developed and integrated inspection and detection systems -Debugged equipment prior to Factory Acceptance Test by customers Show less
-
-
Education
-
University of Rochester - Simon Business School
Masters in Business Administration, Health Care Management, Strategy and Finance -
Rochester Institute of Technology
Bachelor of Science (B.S.), Mechanical Engineering
Community
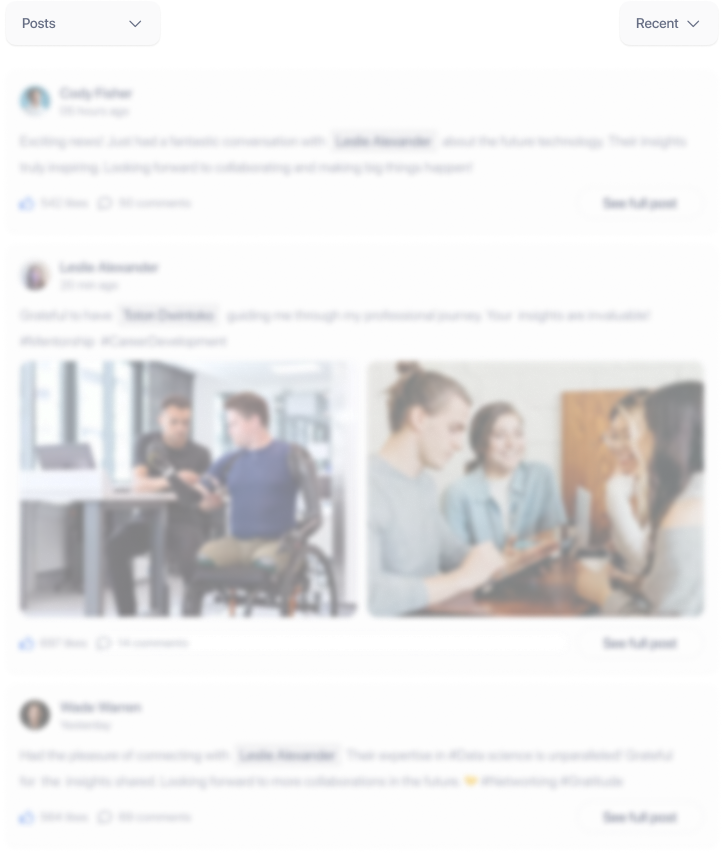