Robert Montgomery
Director Of Information Solutions at Phoenix Group Performance in Print- Claim this Profile
Click to upgrade to our gold package
for the full feature experience.
Topline Score
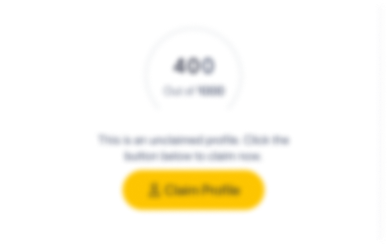
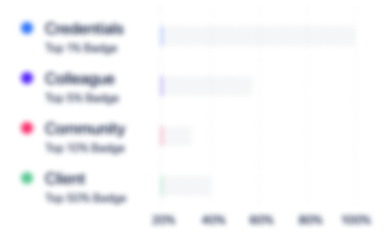
Bio


Experience
-
The Phoenix Group of Companies
-
United States
-
Printing Services
-
1 - 100 Employee
-
Director Of Information Solutions
-
Jan 2019 - Present
-
-
-
OPEX Corporation
-
United States
-
Automation Machinery Manufacturing
-
700 & Above Employee
-
Product Development Engineer
-
Jan 2016 - Dec 2018
• Consult with customers on best practices workflows for utilizing OPEX’s mail extraction, document scanning, sorting products, and material handling equipment. On-site customer visits across the U.S. and Europe. Recommend design changes, new features, and new products to upper management.• Researched, developed and designed a digital mail delivery system with Ricoh USA. The product leverages OPEX’s document scanning systems to identify and sort mail pieces that can be delivered electronically, disposed of as junk mail, or require physically delivery. Designed the mechanical and electronic system prototype of the mail transport, envelope diversion, barcode printer, envelope vision system and barcode verifier. https://www.opex.com/products/falconsts• Architected software features that converted the proprietary OPEX data file output format to a user configurable XML or tab delimited format. The feature also allows the user to select multiple image output formats like jpg, multi-page tiff, and PDF. This greatly reduced the cost of sales to our customers by eliminating the need to pay for third party integration.• Developed a color calibration method for OPEX document scanners. The method was developed in response to scanning medical records for the National Health Service (NHS) in the United Kingdom. Accurate reproduction of the color of the medical folders and forms is critical to the clinician’s interpretation of the digital forms. Show less
-
-
Manager of Support Engineering
-
Mar 1998 - Jan 2016
• Supervised a team of technical writers and illustrators and created service manuals and end user documentation of OPEX products. Created a method of converting paper-based documentation to secure PDF documents viewable on technician’s mobile Android tablets.• Supervised and performed in-house and on-line training of service technicians, 3rd party developers and customers. Utilized open source LMS Moodle for both self-study and interactive courses provided by a live instructor. Custom SCORM modules were created so students could simulate software setup of our products.• Supervised a group of 2nd level support engineers for new product development, beta testing, acceptance testing, and knowledge base creation. Performed testing and document results for management review and corrective action.• Created a paperless field service reporting system for Android tablets. The system automatically replenished field inventory, provided customer billing, logged reported problems and solutions implemented. The system provided failure rate data to justify continuation engineering projects. Field inventory carrying cost was reduced from $8 million to $5 million in 3 years. Show less
-
-
Manager of Continuation Engineering
-
Mar 1996 - Mar 1998
• Directed a team of engineers to design improvements to existing products to reduce service costs and increase customer satisfaction.• Designed low cost metal detector for finding stapled documents in envelopes at high speeds. Stapled documents cause automated, high speed extraction equipment to jam, so they need to be excluded from high speed processing. $5 million sold. U.S. Patent awarded.• Designed low cost audit trail printing system using piezo XAAR print head technology for high speed document extraction equipment. The design decreased the printhead cost by 70%.• Designed stepper motor-based extraction system. The stepper system replaced an existing clutch design that failed frequently. The annual savings to the service department was more than $200,000 per year. Show less
-
-
Technical Support Manager
-
Mar 1993 - Mar 1996
• Managed 24/7 technical support department to assist field repairs and configurations.• Created and implemented multi-tier technical support and escalation process. Utilized knowledge management tools and procedures.• Managed technical writers and illustrators to create service manuals, user manuals, service bulletins, retrofit procedures, and application notes.• Managed in-house technical training.
-
-
Reliability Engineer
-
May 1990 - Mar 1993
• Performed failure analysis, root cause determination and recommended corrective action plan on OPEX mail extractor, mail sorters and their components.• Reviewed and administered Engineering Change Orders (ECOs) to the field.• Determined optimal spare inventory levels using marginal assurance calculations.• Provided second level support of trouble-shooting complex field issues.
-
-
-
Gamble Industries / Ward Leonard Resistors
-
Delanco, NJ
-
Quality Control Manager
-
Apr 1987 - May 1990
• Manufacturer of precision and power wire wound resistors and a custom line of linear and switching power supplies. Experience with quality control best practices, statistical sampling, failure analysis, root cause determination, and corrective action plans. • Maintained environmental testing, test equipment calibration, and document procedures in accordance to MIL-SPEC requirements. This enabled their products to be QPL listed. • Performed equipment setup and on-site production training for manufacturing in Barbados. Show less
-
-
-
Gamble Industries / Ward Leonard Resistors,
-
Delanco, NJ
-
Production Manager
-
Apr 1983 - Apr 1987
• Supervised more than 30 employees is the manufacture of precision and power wire wound resistors and a custom line of linear and switching power supplies. • Responsible for meeting monthly production quota of $250,00 per month. • Innovated production methods for tight tolerance precision resistors. • Supervised more than 30 employees is the manufacture of precision and power wire wound resistors and a custom line of linear and switching power supplies. • Responsible for meeting monthly production quota of $250,00 per month. • Innovated production methods for tight tolerance precision resistors.
-
-
-
Gamble Industries
-
Delanco, NJ
-
Electronic Technician
-
Jun 1981 - Apr 1983
• Tested and repaired a custom line of linear and switching power supplies for Honeywell. • Calibrated lab, production and QC equipment to NBS Standards. • Conducted compliance and environmental testing for QPL listed resistor components. • Tested and repaired a custom line of linear and switching power supplies for Honeywell. • Calibrated lab, production and QC equipment to NBS Standards. • Conducted compliance and environmental testing for QPL listed resistor components.
-
-
Education
-
Drexel University
Bachelor’s Degree, Electrical and Electronics Engineering
Community
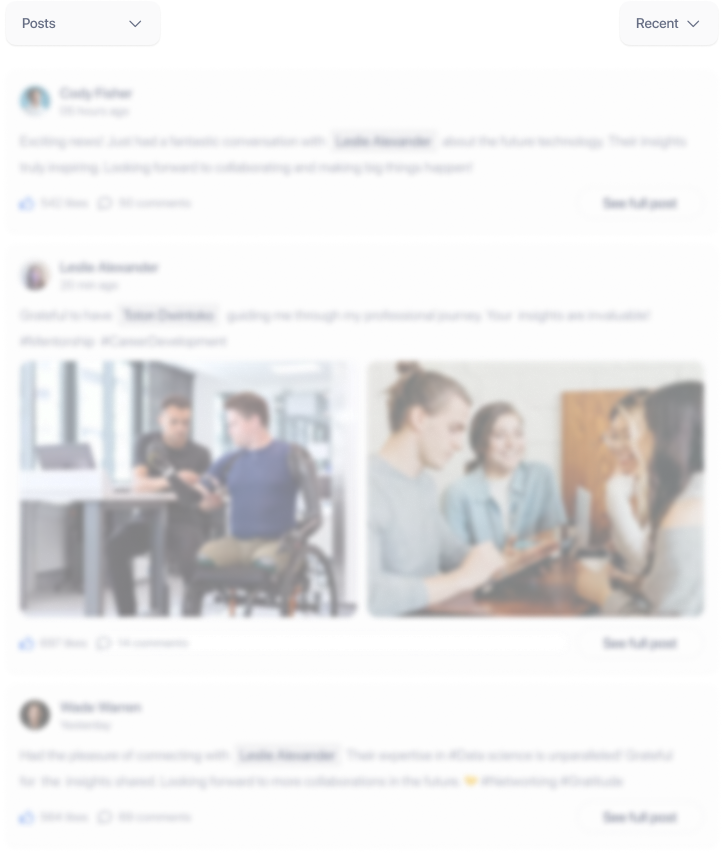