Robert Malkin
Quality Control Inspector at Ortho Solutions Group Ltd- Claim this Profile
Click to upgrade to our gold package
for the full feature experience.
Topline Score
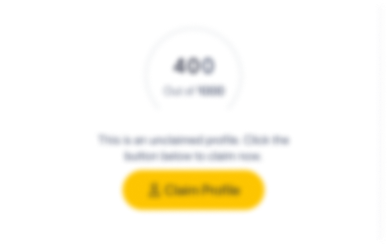
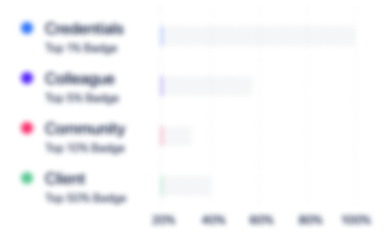
Bio


Experience
-
Ortho Solutions Group Ltd
-
United Kingdom
-
Medical Device
-
1 - 100 Employee
-
Quality Control Inspector
-
Jul 2022 - Present
-
-
-
A2E ORTOSOLUTIONS SL
-
Spain
-
Personal Care Product Manufacturing
-
Quality Control Inspector
-
Jul 2022 - Jul 2022
-
-
-
CURROCK ENGINEERING COMPANY LIMITED
-
United Kingdom
-
Aviation and Aerospace Component Manufacturing
-
1 - 100 Employee
-
Quality Control Inspector
-
Mar 2020 - Jul 2022
-
-
-
-
Production Manager
-
Feb 2019 - Dec 2019
Following relocation of all production to the Netherlands, I have been working for Sofis in the Netherlands as Production Manager of the assembly production department.I declined relocation on a permanent basis; as I have a young son and seek a permanent position closer to home (Tiptree, Essex) in the UK.During my time in the Netherlands my role was to advise the Dutch team, set up and train the assembly production personnel ensuring that all personnel have the appropriate skills required to ensure that the assembly of interlocks following transfer to the Netherlands was successful.In addition to managing the overall department, I was responsible for resource planning, setting up systems and processes for the future, identifying gaps in current personnel’s training and delivering training to address these areas. I have now completed my contract in the Netherlands and am available with immediate effect for work in the UK. Show less
-
-
Production Lead
-
Sep 2003 - Jan 2019
Production Lead, Sofis (formerly SmithFlow Control), Witham, Essex 2003 – January 2019 (redundant production moved to Holland).A diverse role, leading the Assembly Work Shop within which valve interlocks for the oil and gas industry are assembled.Initially when I joined the organisation I was employed as an Assembler. This involved assembly of interlocks, cabinets and flexi-drive systems.In 2012 I was promoted to the position of Production Lead, which has involved achieving and maintaining the company strict guidelines in relation to Health and Safety, Quality and Efficiency ensuring all personnel work within a safe manner and understand and follow company procedures.Key holder for the site, opening the site at the start of the day, and out of hours when personnel working overtime, securing the site at the end of the day.Leading the team, ensuring that they work together as efficiently as possible.Assessing training needs and providing training for direct reports.Ensuring adequate staffing to cover absenteeism, holidays and normal operations.Recording time and attendance of direct reports.Working at all times to strict deadlines as demanded to meet customer order requirements without compromising on attention to detail. Applying a ‘right first time’ approach along with a professional attitude.Consistently maintaining good working relationships at all levels within the organisation whilst maintaining the ability to lead a team, work within a team and to delegate when appropriate. Applying a hands-on approach to diagnose and resolve any technical issues. Show less
-
-
-
Beautimatic
-
United Kingdom
-
IT Services and IT Consulting
-
Injection Moulding Technician
-
Jun 2000 - Aug 2003
I held the position of Injection Moulding Technician. This involved tool and colour changes. Along with tool and machine maintenance. I held overall responsibility for the production line, preparing the machines for tool changes, carrying out tool changes in line with required timelines. Performing start up checks prior to QC approval and in line quality checks throughout the production run. Ensuring that the components are produced to the correct quality and quantity in accordance with agreed customer specifications. Maintaining a good standard of housekeeping, both in and around the machine and within the overall department. Accurately recording components produced on shift and any problems encountered. Ensuring the components were produced and packaged as per the customers’ requirements. Fault finding, and rectification as required. Maintaining good and consistent communication always. Show less
-
-
-
Betts UK
-
United Kingdom
-
Chemical Manufacturing
-
Machine Setter
-
Feb 1992 - May 2000
I held the position of Machine Setter within the Plastics Injection Moulding Department. Overall responsibility for the production lines assigned, preparing the machines for tool changes, carrying out tool changes in line with required timelines. Carrying out line clearance and pass to run procedures. Performing start up checks prior to QC approval and in line quality checks throughout the production run. Ensuring that the components are produced to the correct quality and quantity in accordance with agreed customer specifications. Maintaining a good standard of housekeeping, both in and around the machine and within the overall department. Accurately recording components produced on shift and any problems encountered. Ensuring the components were produced and packaged as per the customers’ requirements. Fault finding, and rectification as required. Maintaining good and consistent communication always. Show less
-
-
-
Woods Airmovement
-
Industrial Machinery Manufacturing
-
Goods Inwards Inspector
-
Sep 1989 - Jan 1992
Initially on YTS within the on-site Training School during which I learnt how to use bench tools, measuring equipment, lathe and mills. This also included a small amount of welding. Post completion, I was awarded a full-time position within the Quality Department and completed a period in each of the Quality Departments. My final position within the organisation was Goods Inwards Inspector within the Incoming Goods Inspection Department. Initially on YTS within the on-site Training School during which I learnt how to use bench tools, measuring equipment, lathe and mills. This also included a small amount of welding. Post completion, I was awarded a full-time position within the Quality Department and completed a period in each of the Quality Departments. My final position within the organisation was Goods Inwards Inspector within the Incoming Goods Inspection Department.
-
-
Education
-
Colchester Institute
City & Guilds, Mechanical Engineering -
St Benedicts Colchester
Community
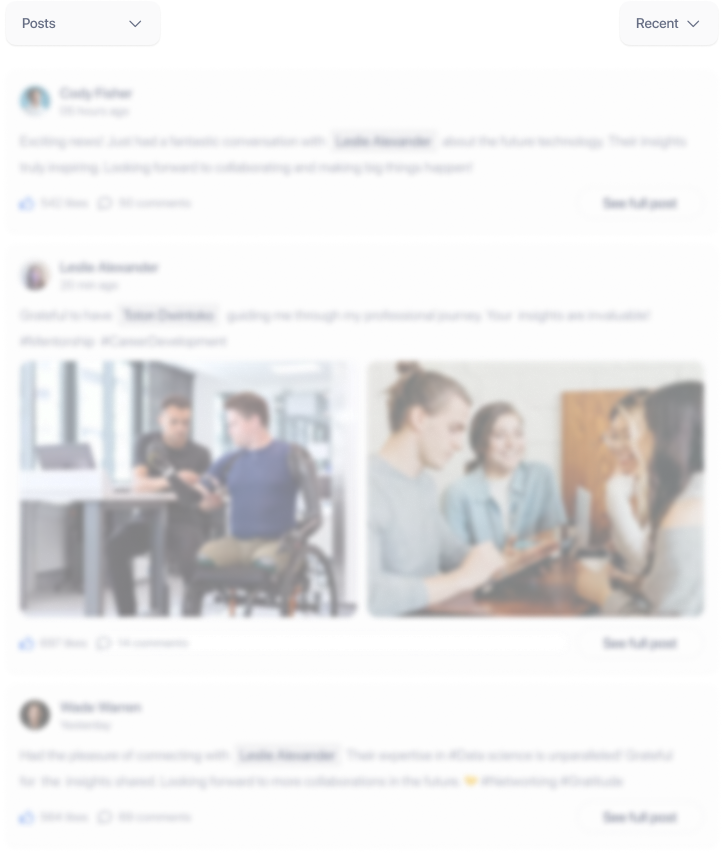