Robert George
Safety Manager at Reading Truck Body, LLC- Claim this Profile
Click to upgrade to our gold package
for the full feature experience.
Topline Score
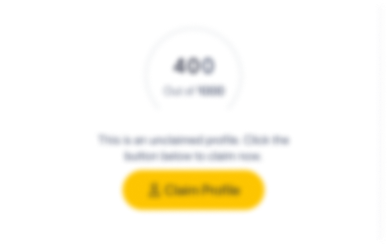
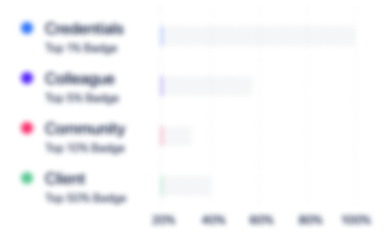
Bio

Vaughn Orbash
I retired out of the Air Force in 2014 and was finishing my safety qualifications when I first met Robert. His mentorship and guidance has been crucial to me over the past few years. He is by far one of the most knowledgeable safety professionals that I have met. This is, no doubt, due to his years of safety experience and his passion and dedication to the safety of others. His zest for safety is infectious and inspirational. I highly recommend making Robert a part of your safety team. Vaughn Orbash OTC Corporate Safety Manager

Brian Bronson
It has been my privilege to have worked closely with Robert in his role as a corporate safety manager for almost three years during my tenure as General Manager of Los Angeles Paper Box. When I first met him, I couldn’t believe that his passionate concern for the safety of others was genuine. He proved to me through his actions that not only was he sincere, he was also the most dedicated safety professional I had ever met. His help in guiding our site through three different ownership changes with their different cultures, policies, and expectations was vital to our success in improving our plant safety. His proactive management of even minor safety incidents led to a reduction in severity. He was available to us 24/7 365 to offer guidance. He made available a wealth of information to help us immediately implement actions so as to not have to re-invent. He worked tirelessly while in the plant to make the most of his time spent with the managers ensuring that we were focused on the things most impactful to the safety of our employees. He was respected and appreciated by the management team at LAPB. As a site leader responsible for safety, I can say without equivocation that the value that Robert brings is immeasurable. I strongly recommend him to any organization looking to make meaningful improvements to their safety culture.

Vaughn Orbash
I retired out of the Air Force in 2014 and was finishing my safety qualifications when I first met Robert. His mentorship and guidance has been crucial to me over the past few years. He is by far one of the most knowledgeable safety professionals that I have met. This is, no doubt, due to his years of safety experience and his passion and dedication to the safety of others. His zest for safety is infectious and inspirational. I highly recommend making Robert a part of your safety team. Vaughn Orbash OTC Corporate Safety Manager

Brian Bronson
It has been my privilege to have worked closely with Robert in his role as a corporate safety manager for almost three years during my tenure as General Manager of Los Angeles Paper Box. When I first met him, I couldn’t believe that his passionate concern for the safety of others was genuine. He proved to me through his actions that not only was he sincere, he was also the most dedicated safety professional I had ever met. His help in guiding our site through three different ownership changes with their different cultures, policies, and expectations was vital to our success in improving our plant safety. His proactive management of even minor safety incidents led to a reduction in severity. He was available to us 24/7 365 to offer guidance. He made available a wealth of information to help us immediately implement actions so as to not have to re-invent. He worked tirelessly while in the plant to make the most of his time spent with the managers ensuring that we were focused on the things most impactful to the safety of our employees. He was respected and appreciated by the management team at LAPB. As a site leader responsible for safety, I can say without equivocation that the value that Robert brings is immeasurable. I strongly recommend him to any organization looking to make meaningful improvements to their safety culture.

Vaughn Orbash
I retired out of the Air Force in 2014 and was finishing my safety qualifications when I first met Robert. His mentorship and guidance has been crucial to me over the past few years. He is by far one of the most knowledgeable safety professionals that I have met. This is, no doubt, due to his years of safety experience and his passion and dedication to the safety of others. His zest for safety is infectious and inspirational. I highly recommend making Robert a part of your safety team. Vaughn Orbash OTC Corporate Safety Manager

Brian Bronson
It has been my privilege to have worked closely with Robert in his role as a corporate safety manager for almost three years during my tenure as General Manager of Los Angeles Paper Box. When I first met him, I couldn’t believe that his passionate concern for the safety of others was genuine. He proved to me through his actions that not only was he sincere, he was also the most dedicated safety professional I had ever met. His help in guiding our site through three different ownership changes with their different cultures, policies, and expectations was vital to our success in improving our plant safety. His proactive management of even minor safety incidents led to a reduction in severity. He was available to us 24/7 365 to offer guidance. He made available a wealth of information to help us immediately implement actions so as to not have to re-invent. He worked tirelessly while in the plant to make the most of his time spent with the managers ensuring that we were focused on the things most impactful to the safety of our employees. He was respected and appreciated by the management team at LAPB. As a site leader responsible for safety, I can say without equivocation that the value that Robert brings is immeasurable. I strongly recommend him to any organization looking to make meaningful improvements to their safety culture.

Vaughn Orbash
I retired out of the Air Force in 2014 and was finishing my safety qualifications when I first met Robert. His mentorship and guidance has been crucial to me over the past few years. He is by far one of the most knowledgeable safety professionals that I have met. This is, no doubt, due to his years of safety experience and his passion and dedication to the safety of others. His zest for safety is infectious and inspirational. I highly recommend making Robert a part of your safety team. Vaughn Orbash OTC Corporate Safety Manager

Brian Bronson
It has been my privilege to have worked closely with Robert in his role as a corporate safety manager for almost three years during my tenure as General Manager of Los Angeles Paper Box. When I first met him, I couldn’t believe that his passionate concern for the safety of others was genuine. He proved to me through his actions that not only was he sincere, he was also the most dedicated safety professional I had ever met. His help in guiding our site through three different ownership changes with their different cultures, policies, and expectations was vital to our success in improving our plant safety. His proactive management of even minor safety incidents led to a reduction in severity. He was available to us 24/7 365 to offer guidance. He made available a wealth of information to help us immediately implement actions so as to not have to re-invent. He worked tirelessly while in the plant to make the most of his time spent with the managers ensuring that we were focused on the things most impactful to the safety of our employees. He was respected and appreciated by the management team at LAPB. As a site leader responsible for safety, I can say without equivocation that the value that Robert brings is immeasurable. I strongly recommend him to any organization looking to make meaningful improvements to their safety culture.

Experience
-
Reading Truck Body, LLC
-
United States
-
1 - 100 Employee
-
Safety Manager
-
May 2021 - Present
-
-
-
Graphic Packaging International, LLC
-
United States
-
Packaging and Containers Manufacturing
-
700 & Above Employee
-
Corporate Safety Manager
-
Apr 2020 - Mar 2021
Responsible for paperboard packaging facilities safety performance across four business units internationally. Canadian Business Unit, Beverage Business Unit (Worlds largest paperboard facilities), Southeast Business Unit, and Northeast Business Unit for a total of twenty one facilities. Responsible for paperboard packaging facilities safety performance across four business units internationally. Canadian Business Unit, Beverage Business Unit (Worlds largest paperboard facilities), Southeast Business Unit, and Northeast Business Unit for a total of twenty one facilities.
-
-
-
-
CPG (Consumer Packaging Group) Division Safety Manager
-
Sep 2016 - Apr 2020
Implement safety strategic safety plans to establish measureable goals. Plan, implement, coordinate, and assesses personal injury,, fire prevention, and occupational safety and health programs utilizing knowledge of industrial safety-related engineering discipline and operating regulations: Develop and recommend new procedures and approaches to safety and loss prevention based on reports of incidents, and other data gathered from close calls, first aids, and medical injuries. Disseminate safety information to department heads and others regarding data driven trends. Assisting department heads and administrators with implementation and accountability regarding safety policies and expectations. Measuring and evaluating the effectiveness of safety program, using established goals. Building employee owned safety programs through employee participation. Implementing a strong data driven Behavior Observation program that is value added and not a "check the box" activity. Build a program that engages employee ownership in safety. Show less
-
-
-
Sonoco
-
United States
-
Packaging and Containers Manufacturing
-
700 & Above Employee
-
Consumer Safety Coordinator
-
Oct 2013 - Sep 2016
2013 – 2016 Sonoco Products Company York Pa, Consumer Business Unit Safety Coordinator This position is responsible for coordinating safety training to support the Consumer Global Operations, investigate and report on any safety incidents in the operations. Report safety training and audit results to Director and applicable regulatory gaps identified as part of the audit process. Ensure that plants are in compliance with Federal and State safety laws. Design activities to reduce global injury rates and ensure that safety knowledge remains up to date and compliant to Federal laws. Primary Responsibilities: • Develop, implement and coordinate corporate safety training modules -Safety 101 Champions Training -Safety Leadership- Facilitate and Lead Training sessions to support Knowledge Base Model -Coordinate safety audits, develop 90 days plans, and follow-up for at-risk and underperforming operations -Review and coordinate follow-up as a result of OSHA violations and develop specific training to address -Key facilitator to help develop and mentor selected plant safety coordinators -Will act as part of integration team for acquisitions to support training and development needs -Participate in Division Safety Committees as “special representative” to address, interpret or clarify OSHA and/or Corporate related safety policy. Training and Development: • Maintain/provide minimum training curriculum for safety roles -Conduct compliance training as approved by OSHA Outreach Training Programs -Collaborate with safety and plant managers to develop safety training material which meets the goals and objectives in achieving world class safety performance as measured by defined metrics. (Injury Rate) Show less
-
-
Global Services Safety Manager
-
Oct 2000 - Oct 2013
Responsible for safety processes within Global Services which represents both Packaging Services and Sonoco CorrFlex. Support outside USA country regional safety coordinators as needed. This role is similar to previously held roles. Current recordable injury rate target is 0.09 to YTD rate of 0.08. - Trained in Global Food Safety practices and auditing to AIB (American Institute Baking) standards. GFSI (Global Food Safety Initiative) BRC and other food defense program parameters.- Responsible for corrective actions around quality control for product/processes. Responsible for quality/safety document control processes such as AGILE-I-Manage-ISO. Show less
-
-
-
Danone
-
France
-
Food and Beverage Manufacturing
-
700 & Above Employee
-
Shift Production Superintendent
-
Jan 2000 - Sep 2000
Responsible for the production of retail product. Managed a shift of 45 to 70 employees in Danone’s largest N/A high speed automated bottled water facility. This included the warehouse, maintenance, and production departments. Insure that safety/quality and production goals are met. Develop continuous improvements in production techniques, safety programs, and employee development. Responsible for the production of retail product. Managed a shift of 45 to 70 employees in Danone’s largest N/A high speed automated bottled water facility. This included the warehouse, maintenance, and production departments. Insure that safety/quality and production goals are met. Develop continuous improvements in production techniques, safety programs, and employee development.
-
-
-
Sonoco
-
United States
-
Packaging and Containers Manufacturing
-
700 & Above Employee
-
Production Lead/Safety Coordinator
-
Jul 1989 - Dec 1999
Lead operator/mechanic on four to eight high-speed retail/grocery plastic bag machines. Back-up supervisor on all four shifts, five departments (extrusion, maintenance, warehouse, quality department and the production department as needed (approximately 40-60 employees on each shift). Co-managed plant ink manufacturing kitchen, responsible for approximately 25,000 lbs of ink per month. This included ink inventory, ink mixing, ink recycling and cost reduction efforts. Also responsible for safety training of 210 employee workforce. DST (division safety team) member, responsible for safety auditing of all six HDFP facilities in the U. S. Co-team leader responsible for the facility receiving the first OSHA VPP Star awarded to a Sonoco Products Company facility. Show less
-
-
Education
-
High School
Community
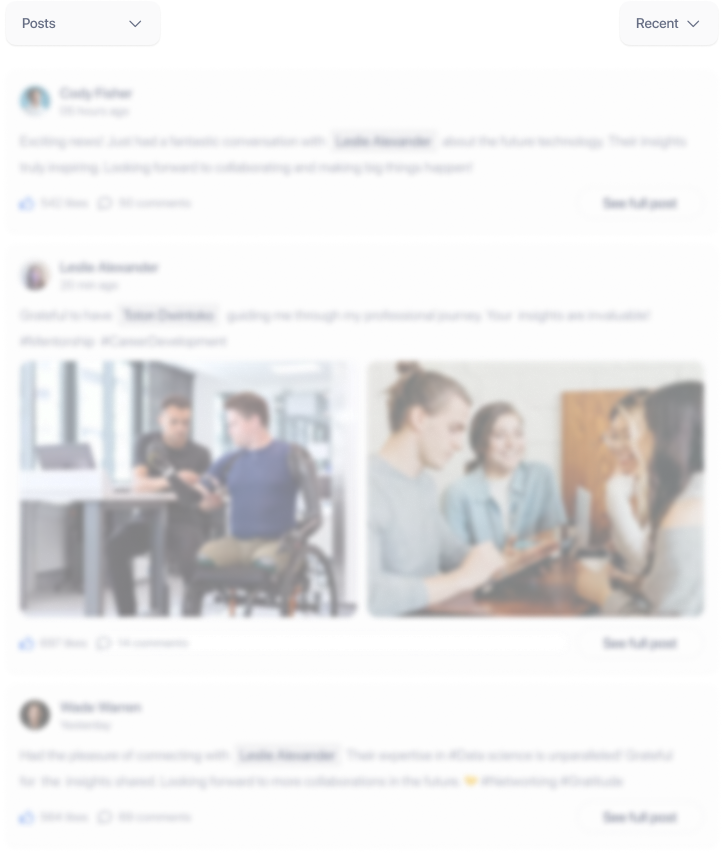