Robert Gage
Project Engineer at PPC Flexible Packaging- Claim this Profile
Click to upgrade to our gold package
for the full feature experience.
-
English -
Topline Score
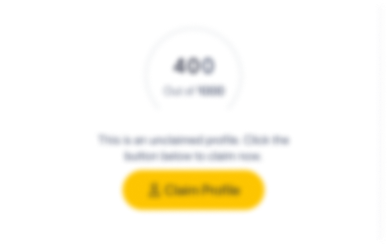
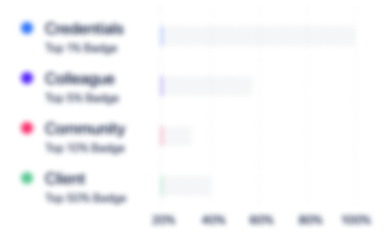
Bio


Experience
-
PPC Flexible Packaging
-
United States
-
Packaging and Containers Manufacturing
-
1 - 100 Employee
-
Project Engineer
-
Jan 2023 - Present
-
-
Project Engineer
-
Oct 2019 - Feb 2023
-
-
-
Harley-Davidson Motor Company
-
United States
-
Motor Vehicle Manufacturing
-
700 & Above Employee
-
Advanced Manufacturing Engineer II
-
Aug 2016 - Oct 2019
- Planned and executed model-year changeover of assembly line including decommissioning and retirement of assets, installation of incoming equipment and upgrades, modification of sub assembly workstation layouts and processes, and hardware and installation- Managed electrical and mechanical contractors from quotation, supplier selection, planning, and final installation of assets- Coordinated new part set up and inventory levels for accurate spare parts availability for new Front Mod, Tail Section, and Fuel Tank conveyors in MRO- Coordinated key stake holders such as Safety, Environmental, Maintenance, Ergonomic, and Process Engineers using the HD EIR process to complete installation and relocation of multiple assets throughout the facility- Scheduled electrical and mechanical bi-weekly, monthly, quarterly, and annual PMs for Front Mod, Tail Section, and Fuel Tank conveyors using SAP- Created purchase requisitions for capital and expense tooling, outside services for third party contractors, and parts spot buy using SAP- Validated correct product structure for new model launch of MY18 and MY19 products Show less
-
-
Manufacturing Process Analyst
-
Aug 2015 - Aug 2016
- Responsible for gap analysis of legacy systems to SAP and established manufacturing processes and procedures to prepare Harley Davidson for an ERP implementation - Directed the installation of the sub assembly SAP hardware and implementation of associated processes, at both the Crane 3PL and the Harley Davidson Operations plant - Created and defined all processes for the lineside SAP ECC sub assemblies and the post assembly parts cage repair and sub assembly orders- Coordinated activities to identify root cause and resolve manufacturing process issues within SAP with primary stakeholders including Work Group Advisors, Work Groups, Quality and Product Engineering, and Manufacturing Support Services- Validated BOM and product structure of all finished goods and sub-assemblies in SAP against AS400 legacy system Show less
-
-
-
Harmar
-
Medical Equipment Manufacturing
-
1 - 100 Employee
-
Production Manager
-
Apr 2014 - Mar 2015
- Managed all planning, scheduling, and production of accessibility products within the Lake Winnebago facility for over 40 employees and 4 value streams - Monitored production processes for efficiency and achievement of quality standards - Interviewed applicants for department positions and recommend candidates to for hiring - Conducted annual and probationary performance reviews for over 40 production associates - Developed the workplace safety training program and conduct plant safety audits daily, weekly, and quarterly Show less
-
-
-
Hillshire Brands
-
United States
-
Food and Beverage Manufacturing
-
700 & Above Employee
-
Training Coordinator
-
Dec 2011 - Apr 2014
Created, developed, and maintained over 90 instructor led classroom, e-learning training coursesand videos using content authoring software (PowerPoint, Articulate Presenter, SISTEMCreator)- Maintained Alchemy LMS database with employee training records as well as generated anddistributed reports from database for up to 240 employees- Assessed employee retention of information to determine effectiveness of trainers and trainingmaterials- Facilitated plant specific training on topics such as Safety, HACCP, and SQF- Performed training needs analysis to determine best practices and develop standardized work- Participated in the new professional orientation and guide employees through the initial on-boarding assessment for over 70 new employees- Facilitated and participated in Root Cause Problem Solving Processes and Kaizen events Show less
-
-
Production Technician
-
Jan 2011 - Dec 2011
Received 4 months initial training on the Armor Inox Cook/ Chill system directly from themanufacture representative during plant start up- Assembled, dis-assembled, and operated equipment throughout the Raw department using themanufacturing systems MES and SAP at 5 workstations- Participated in plant cost savings project utilizing GlenPro computer software- Demonstrated effective leadership and training of 4 new employees in the Armor Inox and Picklerooms
-
-
-
Sika
-
Switzerland
-
Chemical Manufacturing
-
700 & Above Employee
-
Production Supervisor- Automotive, Industrial, and Compound
-
Jan 2003 - Jun 2009
- Full accountability planning, scheduling, and coordinating a production team of up to 46 union employees over several business units- Consistently developed and redirected employees throughout the shift to meet budget, daily department sales goals and critical quality requirements- Participated in the initial implementation of SAP within the Grandview Operations plant- Used effective communication skills to negotiate grievances with union employees and stewards
-
-
Production Supervisor - Shipping and Receiving
-
Jan 2002 - Jan 2003
Consistently developed and redirected employees throughout the shift to meet budget, dailydepartment sales goals and critical quality requirements- Participated in the initial implementation of SAP within the Grandview Operations plant- Used effective communication skills to negotiate grievances with union employees and stewards; Directed and promoted a customer-focused collaborative team of up to 8 union employees in afast-paced environment while maintaining safety and high productivity levels- Input inventory, ran cycle count queries, print bills of lading, and sent ASN’s through the use ofBPCS and Future Three- Proactively redesigned and implemented inventory tracking and maintenance program forreceiving returnable containers from customer Show less
-
-
Production Supervisor- Industrial and Compound
-
Jan 2001 - Jan 2002
Effectively led diverse team of 42 union employees, 7 material handlers, leads, and moldchangers- Resourcefully implemented SMED and 5-S programs that reduced production line downtime by30%- Initiated team building techniques to raise pounds produced per hour by 34%- Facilitated the development of Problem Solving Process teams to resolve productivity issues- Trained and guided team implementation of plant-wide lean manufacturing practices and theToyota production systemIndustrial and Automotive Extrusion Lead; Planned, scheduled, and oversaw daily production with over 35 team members- Participated in label error proofing and scrap reduction Problem Solving Process projects- Researched and assessed cost reduction solutions such as implementing trial programs andprocedures- Recognized for contributions and subsequently promoted from union employee to companysupervisor- Performed and documented tasks in coordination with daily down time and available product- Demonstrated effective leadership and training of new employees resulting in promotion to leadposition Show less
-
-
Education
-
University of Central Missouri
Bachelor of Science, Business Administration; Management -
Metropolitan Community College-Business & Technology
Associates of Arts, Business Administration and Management, General
Community
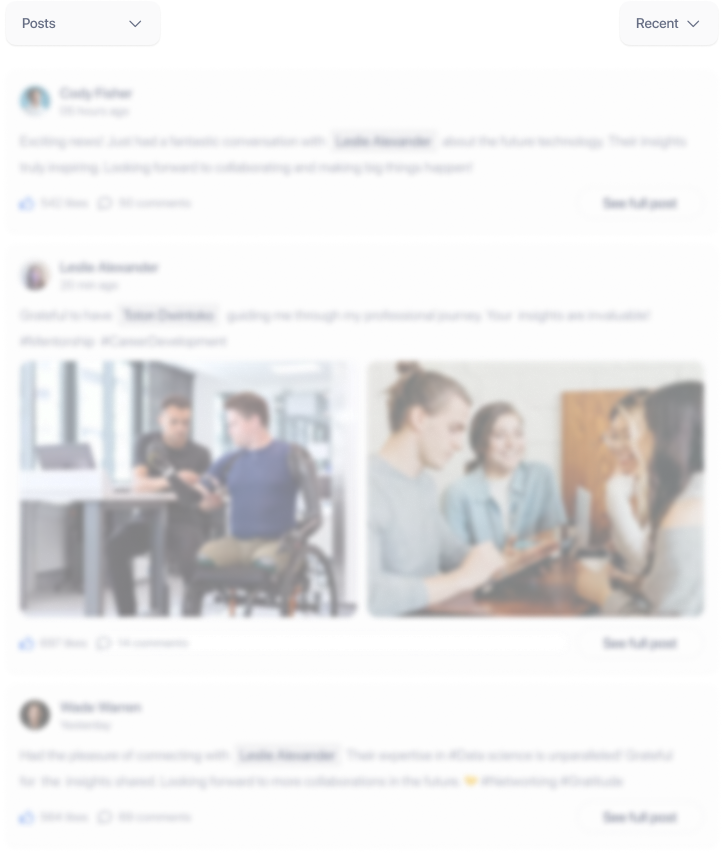