
Robert Dicks
Senior Quality Engineer at Closer Pets- Claim this Profile
Click to upgrade to our gold package
for the full feature experience.
Topline Score
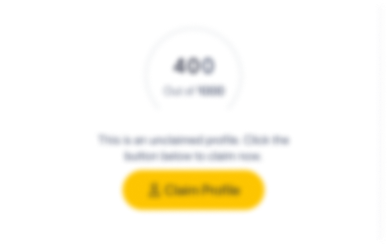
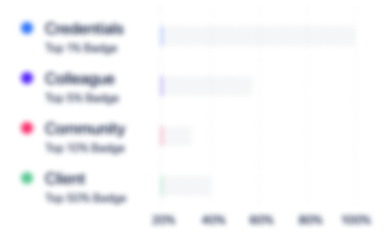
Bio

Mike Sankey
Rob is a fantastic colleague to work with - His desire to do things the 'right' way in Quality was refreshing, as was his hunger to challenge existing practise to improve. The work done on starting a Quality Management System showed great leadership On a personal level, great to work with - And a good mentor for others in 'Quality' and coaching in process and procedure

LinkedIn User
Rob and I worked together at FT Technologies for two years and not only is he a great professional, I regard him as a personal friend. When I first started at FT Technologies he helped me a lot to understand their internal processes. His work ethics is immaculate and was very good at finding solutions to problems. He goes out of his way when you ask for some help and guidance.

Mike Sankey
Rob is a fantastic colleague to work with - His desire to do things the 'right' way in Quality was refreshing, as was his hunger to challenge existing practise to improve. The work done on starting a Quality Management System showed great leadership On a personal level, great to work with - And a good mentor for others in 'Quality' and coaching in process and procedure

LinkedIn User
Rob and I worked together at FT Technologies for two years and not only is he a great professional, I regard him as a personal friend. When I first started at FT Technologies he helped me a lot to understand their internal processes. His work ethics is immaculate and was very good at finding solutions to problems. He goes out of his way when you ask for some help and guidance.

Mike Sankey
Rob is a fantastic colleague to work with - His desire to do things the 'right' way in Quality was refreshing, as was his hunger to challenge existing practise to improve. The work done on starting a Quality Management System showed great leadership On a personal level, great to work with - And a good mentor for others in 'Quality' and coaching in process and procedure

LinkedIn User
Rob and I worked together at FT Technologies for two years and not only is he a great professional, I regard him as a personal friend. When I first started at FT Technologies he helped me a lot to understand their internal processes. His work ethics is immaculate and was very good at finding solutions to problems. He goes out of his way when you ask for some help and guidance.

Mike Sankey
Rob is a fantastic colleague to work with - His desire to do things the 'right' way in Quality was refreshing, as was his hunger to challenge existing practise to improve. The work done on starting a Quality Management System showed great leadership On a personal level, great to work with - And a good mentor for others in 'Quality' and coaching in process and procedure

LinkedIn User
Rob and I worked together at FT Technologies for two years and not only is he a great professional, I regard him as a personal friend. When I first started at FT Technologies he helped me a lot to understand their internal processes. His work ethics is immaculate and was very good at finding solutions to problems. He goes out of his way when you ask for some help and guidance.

Experience
-
Closer Pets
-
Manufacturing
-
1 - 100 Employee
-
Senior Quality Engineer
-
Oct 2021 - Present
currently working as part of a small quality, supporting- supplier development - NPD & NPI- Quality system development
-
-
Quality Engineer
-
Sep 2020 - Oct 2021
-
-
-
Hydro Systems Company
-
United States
-
Defense and Space Manufacturing
-
1 - 100 Employee
-
Quality Engineer
-
Jun 2018 - Jul 2020
Responsible for looking after and improving product quality. - Global Complaints System (GCS) – reworking of the GCS system to enable analysis to take place to look at trends and understand what is happening globally. Allowing for quick analysis of data, leading to product improvements. Creation of process documents to explain how the process works.- Continuous Improvement – Involved in various improvement programs that helped to drive quality/ product improvements.- Production Part Approval Process (PPAP) – preparing and reviewing current PPAP documents and updating as required. - Scrap – reworking the scrap process for the UK to allow analysis of scrap and to monitor supplier quality and trends. Creation of process documents to explain how the process works.- Non-Standard Product Release (NSPR) – Working closely with the engineering team to document and develop customer specific versions of standard Hydro product.- Product quality and stabilising production methods, got agreement to implement - Gemba – the aim is to capture quality / production concerns for the cell and then systematically work through the issues.- Quality Meeting – Introduction of weekly quality meeting to highlight to production staff the current quality concerns, be they supplier, production or customer concerns.
-
-
-
FT Technologies Ltd
-
United Kingdom
-
Renewable Energy Semiconductor Manufacturing
-
1 - 100 Employee
-
Senior Quality Engineer
-
Jan 2016 - May 2018
Assisted with the maintenance ISO 9001 and ISO 14001 compliance and developing this into an Integrated Management System.- Failure Analysis – Development of three reports, capturing the data allowed us to take the first-time pass rate from 86% to 99% in 18 months. - Production Failure – taking data from the MRP system and developing a report that can detail production first time pass rate and spot trends.- Production Failure – Created a manual process for recoding build failures for stages that are not covered by MRP and helping to drive quality improvements.- Customer Returns – taking two existing reports one was provided by the sales department and the production department and developing one report that could handle both aspects. Now dealing with the software developer for our returns system to develop a report to be extracted from the system.- Change management - Taking two systems, Mod Request/ NCR system, and combining them into one system that allows the business to track the progress on a mod request through the various stages, from initial raising of request to full implementation- Scrap - Development of report to enable analysis of scrap and to monitor supplier quality and trends.- Production Processes – Re set-up of Production processes documents for standard and non-standard product to allow production operators to build product. - Gemba – Introduction of weekly Gemba walks for the production workshop.- Supported the following the Internal Audit program, Calibration system, CAPA system, weekly Quality meetings for production staff and pFMEA processes.- Supported customer and ETL audits, preparing data prior to audit, and engaging in the audit process. and supported the process after the audit.
-
-
Quality Engineer
-
Apr 2013 - Dec 2015
Assisted with the maintenance ISO 9001 and ISO 14001 compliance and developing this into an Integrated Management System.- Failure Analysis – Development of three reports, capturing the data allowed us to take the first-time pass rate from 86% to 99% in 18 months. - Production Failure – taking data from the MRP system and developing a report that can detail production first time pass rate and spot trends.- Production Failure – Created a manual process for recoding build failures for stages that are not covered by MRP and helping to drive quality improvements.- Continuous Improvement – Involved in various improvement programs that helped to drive quality/ product improvements.- Customer Returns – taking two existing reports one was provided by the sales department and the production department and developing one report that could handle both aspects. Now dealing with the software developer for our returns system to develop a report to be extracted from the system.- Change management - Taking two systems, Mod Request/ NCR system, and combining them into one system that allows the business to track the progress on a mod request through the various stages, from initial raising of request to full implementation- Scrap - Development of report to enable analysis of scrap and to monitor supplier quality and trends.- Production Processes – Re set-up of Production processes documents for standard and non-standard product to allow production operators to build product. - Gemba – Introduction of weekly Gemba walks for the production workshop.- Supported the following the Internal Audit program, Calibration system, CAPA system, weekly Quality meetings for production staff and pFMEA processes.- Supported customer and ETL audits, preparing data prior to audit, and engaging in the audit process. and supported the process after the audit.
-
-
-
FFEI
-
United Kingdom
-
Mechanical Or Industrial Engineering
-
1 - 100 Employee
-
Quality Engineer
-
Dec 2008 - Mar 2013
Working within a group of five multi skilled quality engineers designing and manufacturing high complexity low volume electro-mechanical products for the printing and Life Science industries. Liaising with all areas of the business, including engineering, sales and production. Assisted in in maintaining ISO 9001, ISO 13485 and ISO 14001.o Returns Material Authorisation (RMA) - As RMA Controller, developed a tracking system that has enabled the business to improve RMA processing times from 25 weeks to 5 weeks. The tracking system is used to track trends and analyse volume of parts and recurring faults. System is also used by accounts to monitor transactions. o Scrap – New system developed to allow the monitoring of scrap by business unit. Allowing manufacturing handling issues to be reduced, over a three-year period monthly scrap has been reduced from £5,250 to £1,180. (work out as a %)o Non-Conforming Material (NCM) - Led a cross-departmental team that reduced NCM's from 45 weeks to around 10 weeks. This exercise reduced the open NCM amount on SAP by £150,000. o Serial Number Database – Developed in accordance with ISO 13485. Developed in lieu of an expensive SAP upgrade. This system has been externally audited several times and passes all requirements of ISO 13485.o Supported the following the Internal Audit program, Line Audit, Calibration system, CAPA system, weekly Quality meetings for production staff and ETL compliance audits.o Developed Dashboard for QA KPI monitoring and process improvement, and management reports.
-
-
-
Bourne Leisure
-
United Kingdom
-
1 - 100 Employee
-
Commercial Team
-
2004 - 2008
Working in the commercial team in Warners, setting up offers on the reservations system. Moved to the commercial team in Haven ran the breaks availability report and mailed this to all parks every day. Working in the commercial team in Warners, setting up offers on the reservations system. Moved to the commercial team in Haven ran the breaks availability report and mailed this to all parks every day.
-
-
-
Bertrandt AG
-
Motor Vehicle Manufacturing
-
1 - 100 Employee
-
Team Leader
-
Mar 1999 - Mar 2002
Working with a harness manufacturer to produce cable harness channels for the Jaguar X400 and X350 programs.From initial conception through to rapid prototyping, dealing with customer and the prototype supplier, and running a team of 8 design engineers Working with a harness manufacturer to produce cable harness channels for the Jaguar X400 and X350 programs.From initial conception through to rapid prototyping, dealing with customer and the prototype supplier, and running a team of 8 design engineers
-
-
-
Yazaki Service
-
Motor Vehicle Manufacturing
-
300 - 400 Employee
-
EDS engineer
-
1998 - 1999
Working on the D car Mondeo plate form.Was the Yazaki engineer responsible for leasing between Ford and Yazaki on cost reduction with regards to wire harness with in the Mondeo family of cars. Working on the D car Mondeo plate form.Was the Yazaki engineer responsible for leasing between Ford and Yazaki on cost reduction with regards to wire harness with in the Mondeo family of cars.
-
-
-
Pentair - Schroff Europe
-
Germany
-
Computer Hardware Manufacturing
-
Design Engineer
-
1994 - 1998
Working as part of a small team. Implemented a new product range, prepared cad data for production, creation of bills of materials and inputting these into the business MRP system. Working as part of a small team. Implemented a new product range, prepared cad data for production, creation of bills of materials and inputting these into the business MRP system.
-
-
-
-
Inspector
-
Jul 1983 - 1993
As part of a team of three inspectors was responsible for goods in, patrolling inspection and final inspection. Undertook internal calibration and set up and run the system. As part of a team of three inspectors was responsible for goods in, patrolling inspection and final inspection. Undertook internal calibration and set up and run the system.
-
-
Education
-
Kings langley School, Hertfordshire
Community
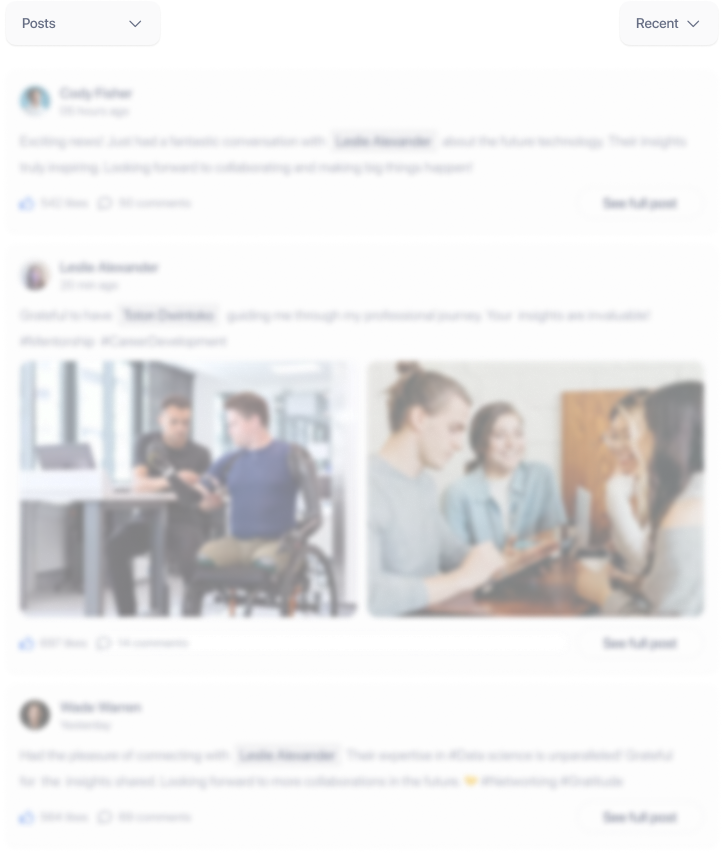