Robert DeGrange
Plant Manager at AMG Vanadium LLC- Claim this Profile
Click to upgrade to our gold package
for the full feature experience.
Topline Score
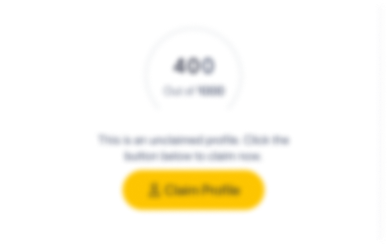
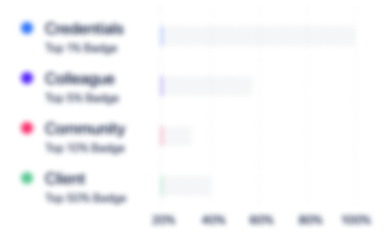
Bio

Matthew Farkas
Robert is a proactive and highly motivated manager that empowers the team around him to do their best. During the time we worked together, Rob helped the operations team engage in problem solving activities that increased production in order to meet delivery targets and accomplish financial objectives. I would recommend Robert for any position, as he rises to the occasion to meet and exceed any challenge presented.

Kim Blievernicht
Arconic was a complex maze of acquisitions and downsizing of facilities when Rob was moved from the Texas plant to Minnesota in a temporary Plant Manager role. The key to his success was driving productivity through this complexity rather than fighting it. He assessed the resistance to the new organization and difficult employee environment. Overcoming the resistance and sticking to the course set by Arconic was his objective. Rob has perseverance and used a variety of ways to get things done. His role was temporary and I admired that he accomplished what he could during this difficult time of change.

Matthew Farkas
Robert is a proactive and highly motivated manager that empowers the team around him to do their best. During the time we worked together, Rob helped the operations team engage in problem solving activities that increased production in order to meet delivery targets and accomplish financial objectives. I would recommend Robert for any position, as he rises to the occasion to meet and exceed any challenge presented.

Kim Blievernicht
Arconic was a complex maze of acquisitions and downsizing of facilities when Rob was moved from the Texas plant to Minnesota in a temporary Plant Manager role. The key to his success was driving productivity through this complexity rather than fighting it. He assessed the resistance to the new organization and difficult employee environment. Overcoming the resistance and sticking to the course set by Arconic was his objective. Rob has perseverance and used a variety of ways to get things done. His role was temporary and I admired that he accomplished what he could during this difficult time of change.

Matthew Farkas
Robert is a proactive and highly motivated manager that empowers the team around him to do their best. During the time we worked together, Rob helped the operations team engage in problem solving activities that increased production in order to meet delivery targets and accomplish financial objectives. I would recommend Robert for any position, as he rises to the occasion to meet and exceed any challenge presented.

Kim Blievernicht
Arconic was a complex maze of acquisitions and downsizing of facilities when Rob was moved from the Texas plant to Minnesota in a temporary Plant Manager role. The key to his success was driving productivity through this complexity rather than fighting it. He assessed the resistance to the new organization and difficult employee environment. Overcoming the resistance and sticking to the course set by Arconic was his objective. Rob has perseverance and used a variety of ways to get things done. His role was temporary and I admired that he accomplished what he could during this difficult time of change.

Matthew Farkas
Robert is a proactive and highly motivated manager that empowers the team around him to do their best. During the time we worked together, Rob helped the operations team engage in problem solving activities that increased production in order to meet delivery targets and accomplish financial objectives. I would recommend Robert for any position, as he rises to the occasion to meet and exceed any challenge presented.

Kim Blievernicht
Arconic was a complex maze of acquisitions and downsizing of facilities when Rob was moved from the Texas plant to Minnesota in a temporary Plant Manager role. The key to his success was driving productivity through this complexity rather than fighting it. He assessed the resistance to the new organization and difficult employee environment. Overcoming the resistance and sticking to the course set by Arconic was his objective. Rob has perseverance and used a variety of ways to get things done. His role was temporary and I admired that he accomplished what he could during this difficult time of change.
0
/5.0 / Based on 0 ratingsFilter reviews by:
Experience
-
AMG Vanadium LLC
-
United States
-
Mining
-
1 - 100 Employee
-
Plant Manager
-
Jul 2019 - Present
Zanesville Ohio Zanesville Ohio
-
-
-
Architectural Precast Innovations
-
United States
-
Construction
-
1 - 100 Employee
-
Plant Manager
-
Jul 2017 - Jul 2019
• Manage costs, inventory, logistics, and deliveries. Plan production and maintenance schedules. • Train workforce on continuous improvement, team building, and safety. • Establish and enforce policies and procedures. • Review profits and losses and look for opportunities for cost savings. • Manage costs, inventory, logistics, and deliveries. Plan production and maintenance schedules. • Train workforce on continuous improvement, team building, and safety. • Establish and enforce policies and procedures. • Review profits and losses and look for opportunities for cost savings.
-
-
-
Arconic
-
United States
-
Manufacturing
-
700 & Above Employee
-
Temporary Plant Manager
-
Apr 2016 - Dec 2016
Managed manufacturing transition to restructure people and processes. Maintained safety requirements. Managed manufacturing transition to restructure people and processes. Maintained safety requirements.
-
-
-
Alcoa Energy Systems (Formerly Alcoa Oil & Gas Inc. and RTI Energy Systems, Inc.)
-
United States
-
Oil and Gas
-
1 - 100 Employee
-
General Manager
-
Sep 2012 - Apr 2016
• Earned plant record for $86M in revenue in 2013. • Developed cost savings initiatives with savings up to $1.3M. • Oversaw all operations, including safety, maintenance, quality, production, profits and losses. • Maximized productivity and improved utilization by improving logistics. • Added capitol equipment to reduce outsourcing and increase capabilities and utilization. • Reduced variable cost 7% and increased operating income 9% in a declining energy market • Earned plant record for $86M in revenue in 2013. • Developed cost savings initiatives with savings up to $1.3M. • Oversaw all operations, including safety, maintenance, quality, production, profits and losses. • Maximized productivity and improved utilization by improving logistics. • Added capitol equipment to reduce outsourcing and increase capabilities and utilization. • Reduced variable cost 7% and increased operating income 9% in a declining energy market
-
-
-
RTI International Metals (Acquired by Alcoa on July 23, 2015)
-
Mining
-
200 - 300 Employee
-
General Manager
-
Aug 2008 - Sep 2013
• Received Corporate Safety and Continuous Improvement award for 2012 and 2013• Supervised 8 managers who oversaw a staff of over 300. • Received Corporate Safety and Continuous Improvement award for 2012 and 2013• Supervised 8 managers who oversaw a staff of over 300. • Managed Materials Processing, Titanium Processing, Ferro Alloys, and Niles Melt shop. • Operated a $313 million dollar budget. • Led team from facility start-up to a well-run facility by establishing safety and quality benchmarks. • Initiate quality improvements for the melt shop that resulted in a 10% improvement in chemistry. • Negotiated United Steelworkers contract extension.• Initiated and successfully implemented a drug policy for Niles, Ohio facility.• Achieved reduction in OSHA recordable accidents that exceeded the departmental safety goals. • Instituted continuous improvement culture resulting in improvements in all functional areas.
-
-
Plant Manager
-
Aug 2000 - Jul 2008
• Led transition from a start-up facility to full production. Managed operating budget of $23M. • Built continuous improvement culture, resulting in a $200K cost savings per year. • Managed all operations including safety, quality, productivity, and inventory. • Supervised 5 staff directly and indirectly supervised 50 employees. • Implemented team-base culture that aided union avoidance.
-
-
Materials Manager
-
Aug 1998 - Aug 2000
• Responsible for all inventories of raw materials, shipping and receiving and titanium turnings line • Managed water treatment problems and functions. • Supervised 4 staff directly and an additional 20 indirectly. • Developed policies and procedures for start-up operations including hiring, training, and team building. • Achieved ISO 9001, AS9100 REV c Certification.
-
-
-
Shieldalloy Metallurgical Corporation
-
United States
-
1 - 100 Employee
-
Deputy Plant Manager / Production Manager
-
Jul 1997 - Aug 1998
Acting Plant Manager during Plant Manager’s absence and as such was responsible for the operation and production of the Newfield, NJ site. This position expanded the responsibilities listed below for Superintendent.
-
-
Assistant Plant Manager
-
Apr 1990 - Aug 1998
-
-
Superintendent of Crushing
-
Sep 1995 - Jul 1997
-
-
Acting Plant Manager
-
Apr 1990 - Sep 1995
•$6.2 million operating budget for four departments, including production of ALTAB pucks, briquettes, powders and bulk crushing and packaging.•Responsible for all product quality, production and production scheduling, writing and implementing ISO Procedures and use of SPC training.•Responsible for all facets of employee relations, interfacing with the Union, and operating the facility in compliance with OSHA and the NJ Department of Environmental Protection and Energy.•Negotiated the Union Contract and Collective Bargaining Unit.•Trained staff on company policy/procedures and troubleshooting daily problems.; Promoted to this position from Shift Foreman.•Responsible for all budgeting for two departments in the production of ferroalloys.•Increased ferrotitanium production by 20% through teamwork effort.•Achieved 98.77% recovery for Ferrovanadium 80%.•Increased furnace life by 10% for 70% ferrotitanium through successful experimentation with furnace liners and implemented changes in the cleaning practices.•Achieved 100% non-OSHA recordable accidents and exceeded the departmental goals in 1994 for safety.
-
-
-
Silvi Concrete
-
United States
-
Freight and Package Transportation
-
Plant Manager
-
Jan 1989 - Apr 1990
All scheduling of personnel and trucks. •Maintenance of all equipment. •Reduced waste and brought material variance from 15% to 1.5% by utilizing computer system •Increased productivity while minimizing corporate overhead •Implemented a computer system and reduced office staff and company’s payroll costs over $50,000 yearly. All scheduling of personnel and trucks. •Maintenance of all equipment. •Reduced waste and brought material variance from 15% to 1.5% by utilizing computer system •Increased productivity while minimizing corporate overhead •Implemented a computer system and reduced office staff and company’s payroll costs over $50,000 yearly.
-
-
-
-
Assistant Plant Manager
-
Jul 1987 - Jan 1989
Responsible for directing and managing a staff of 14 in the batching and dispatching of Redimix concrete. Direct Account responsibility, including all scheduling from a varied client base of small to major corporations. Responsible for directing and managing a staff of 14 in the batching and dispatching of Redimix concrete. Direct Account responsibility, including all scheduling from a varied client base of small to major corporations.
-
-
-
Hocking College
-
United States
-
Higher Education
-
400 - 500 Employee
-
Resident Coordinator
-
Jun 1985 - Jul 1987
Member of the Hocking Heights Working Council, functioning to upgrade all operations. Received two promotions and a position supervising 11 employees and 7 work-study programs. Member of the Hocking Heights Working Council, functioning to upgrade all operations. Received two promotions and a position supervising 11 employees and 7 work-study programs.
-
-
Education
-
Ohio University
Bachelor of Science, Communications -
Hocking College
Associate's degree, Business Administration and Management, General
Community
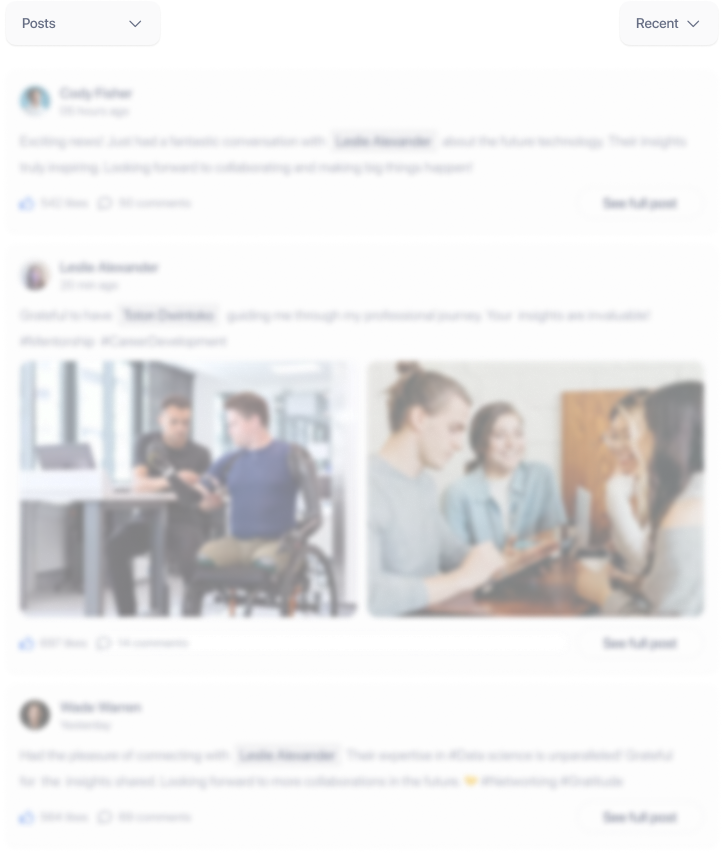