Rob Norris
Head of Engineering at Pharmaron- Claim this Profile
Click to upgrade to our gold package
for the full feature experience.
Topline Score
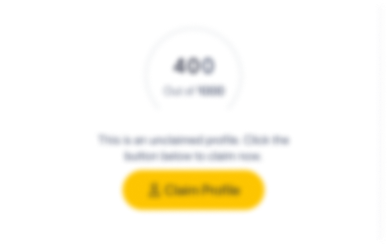
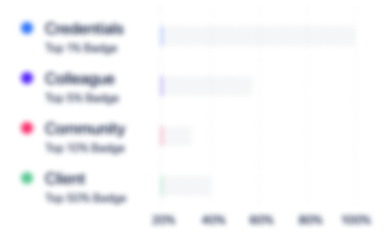
Bio


Experience
-
Pharmaron
-
China
-
Pharmaceutical Manufacturing
-
700 & Above Employee
-
Head of Engineering
-
Feb 2023 - Present
-
-
-
Sterling Pharma Solutions
-
United Kingdom
-
Pharmaceutical Manufacturing
-
500 - 600 Employee
-
Strategic Projects Manager
-
Jan 2022 - Feb 2023
• Comply with Quality and HSE requirements • Ensure company safety rules and safe working practices are observed at all times • Manage strategic projects, leveraging local teams of contract project and process engineers, fully in line with site procedures and standards • Ensure compliance with COMAH critical aspects of the Process Safety Management System and Major Accident Prevention Policy • Organise and manage the safe design, installation & handover of all Strategic Projects • Manage Strategic CAPEX budgets with regular financial reporting • Assemble information and evaluate alternative solutions for each strategic CAPEX project area which can be used to make investment decisions • Prepare justifications for capital authorisation with specific responsibility for scope of work, cost definition and installation programmes • Manage compliance with the CDM regulations • Mentor Project Engineers on practical aspects of project processes • Manage the procurement of equipment and materials • Ensure EPCM and contract personnel fulfil their responsibilities with respect to quality and schedule achievement • Ensure project timelines are met and manage stakeholder expectations accordingly • Manage and maintain systems and procedures in relation to project engineering • Manage and direct multi-disciplined project teams on strategic capital projects with full accountability for all project aspects • Due to cross site responsibilities it is essential to influence and use in-direct management skills to maximise the potential of the role • Work as part of a cross-functional, multi-national team • Liase with the relevant Site Engineering and Operations teams to ensure all project aspects are communicated and understood • Coordinate site infrastructure interactions with relevant site departments Working as part of the Global Strategic Engineering Management Team this role has a major impact on company performance and critical in enabling successful growth of the organisation Show less
-
-
-
Sterling Pharma Solutions Ltd
-
Northumberland
-
Engineering Projects Manager
-
May 2014 - Jan 2022
• Comply with all Quality and HSE requirements • Ensure that company safety rules and safe working practices are observed at all times. • Ensure compliance with COMAH critical aspects of the Process Safety Management System and Major Accident Prevention Policy (Top tier COMAH site) • Organise and manage the safe design, installation & handover of all site projects • Manage department revenue and site CAPEX budgets • Lead the team in preparing designs and specifications and manage implementation • Preparation of capital authorisation with specific responsibility for scope of work, cost definition and installation programmes • Ensure the team prepare equipment & contract specifications • Provide information for validation purposes • Lead Project Engineers on practical aspects of design proposals, labour cost estimates, methods of installation and preparing material take-off lists • Manage the procurement of equipment and materials • Ensure that contract supervisors fulfil their responsibilities with respect to quality and schedule achievement • Manage and maintain standards with contractors in line with company procedures • Liaise with outside design and management contractors • Ensure project timelines are met and manage stakeholder expectations accordingly • Liaise with customers and clients • Manage and maintain all site systems and procedures in relation to project engineering My position has a major impact on site performance, quality, HSE and can have serious implications for customers, company profitability and future growth if timelines and delivery targets are not met. My current live capital project budget is £18.6M with a £36M spend over the previous 2 years. My team of 18 staff (supplemented by a contract labour base) have been key in the delivery of complex and time sensitive projects to enable the business to grow from almost zero to £96M annual sales through ingenuity, adaptability, flexibility and value engineering. Show less
-
-
-
Sterling Pharma Solutions
-
United Kingdom
-
Pharmaceutical Manufacturing
-
500 - 600 Employee
-
Central Engineering Services Manager
-
Aug 2013 - Apr 2014
Directing utilities management, controlling Engineering maintenance and administration functions to ensure service and support to the operations department is provided in an effective and professional manner. Accountabilities: • Comply with all HSE requirements including safety policies and procedures • Ensure compliance with Upper Tier COMAH critical aspects of the Process Safety Management System and Major Accident Prevention Policy where relevant • Conduct audits and investigations • Generate a high level of safety and environmental protection awareness • Manage CES systems to ensure that skills, manning and organisation meet production needs in an efficient and cost-effective and ensuring compliance with COMAH • Manage the physical assets of the Company to minimise life-cycle costs • Maximise plant utilisation by providing practical Engineering input into all project Engineering work, establishing and maintaining the correct level of spares, identifying and implementing programmes to continuously reduce plant downtime due to Engineering failure • Manage effective communication channels • Manage statutory and regulatory compliance • Manage the efficient operation of steam, utilities and nitrogen generation plant • Ensure that electrical, process control and instrument service functions are provided to the correct technical level • Install and manage an energy management programme • Ensure provision of Engineering data and information to assist in efficient plant operation • Ensure that Engineering stores function is provided to the correct technical level • Overall responsibility for all staff within CES to including appraisal, employee relations, development, reward, objective setting and communication • Oversee grievance and discipline matters • Set budgets, monitor expenditure and initiate cost reduction measures to meet targets • Responsible for capital expenditure within the area to ensure the company gains maximum benefit form investment Show less
-
-
-
Aesica pharmaceuticals Ltd
-
Cramlington, Northumberland
-
Site Engineering Manager
-
Jun 2012 - Aug 2013
• Managing the Site Engineering Department in order to meet and deliver site priorities across the functional areas. • Create and lead the team to achieve specific site key performance indicators. • Ensure consistency across the site by ensuring the right systems are in place. • Responsible for the setting and control of a Site Engineering expenditure budget of £4.2M as well as the site capital expenditure budget. • Apply the concepts of current GMP and other appropriate quality standards within the Pharmaceutical industry to maintenance activities. • Ensure that all planned maintenance activities are effectively planned in, and systems in place to ensure that they are filed and communicated with relevant internal stakeholders. • Ensure that plant fabric and facilities management such as the site fire system, refrigeration maintenance, Cooling tower maintenance is carried out efficiently and compliant with internal and external requirements. • Contribute to the process and project design phase of major and minor engineering projects to ensure that appropriate equipment is selected and that maintenance requirements are included. • Major focus on SH&E compliance with regards to site procedures, standards and improvement programs with direct contact with HSE specialists and inspectors. • Provided leadership focus, taking a position that hadn’t existed for over 5 years and assuming responsibility for all staff within the department including appraisal, development, reward, objective setting, communication, grievance and discipline matters. Show less
-
-
-
-
Process Team Leader
-
Feb 2007 - Jun 2012
• Management of shift process teams including engineers and manufacturing technicians with responsibility for planning, prioritising and coordination of production on two multi product plants and one pilot plant to ensure production targets are met. • Budget control and staff assessment through performance management. • Providing technical support to the process team and engineering department. • Ensuring plant operations comply with relevant standards i.e. cGMP, ISO and MHRA / FDA conformance. • Site incident controller during emergency situations coordinating site emergency response team and emergency services. • Hot work and confined entry permit authorization. • Sample analysis through quality controlled lab techniques. Achievements: • Developed a greater understanding of the Technical aspects of production • Continuous Improvement Leader for a period of 3 months in 2010 identifying capacity improvements of 48% and 25% on two production plants and leading to annual savings of £866K. Show less
-
-
-
Aesica Pharmaceuticals Ltd
-
United Kingdom
-
Pharmaceutical Manufacturing
-
100 - 200 Employee
-
I&E Engineer
-
Jan 2005 - Jan 2007
•Ensure that all electrical and instrument engineering operations are carried out safely on site in accordance with defined procedures and company standards. •Ensure that repair and maintenance are carried out to appropriate work procedures and engineering standards and in accordance with statutory and regulatory requirements. •To audit electrical and instrument engineering systems to ensure compliance with company and regulatory standards. •Provide electrical and instrument support to production operations. •Generate and maintain all Technical and Standard Maintenance Instructions •Maintain all process control system hardware requirements •Implement ideas for improving equipment reliability and reduce plant downtime •Provide an efficient, cost effective, maintenance and repair service in accordance with the planned maintenance programme. •Contribute to and lead specific electrical and instrument engineering projects. •Monitor and control costs within approved limits. •Assist in producing and executing business plans, including feasibility studies identifying costs and timescales for engineering solutions. •Supervise the work of electrical and engineering staff (in house and contract) as required to provide support to production, technical and other site functions as necessary to achieve production and other business targets. •Participate in multi-disciplinary plant teams as necessary to achieve production plan. •Assist with multi-disciplinary project work and provide technical support to technical, process and other site teams. •Install and commission all new electrical and instrument systems. Show less
-
-
-
-
-
Jan 2003 - Dec 2006
-
-
-
Sep 1994 - Dec 2004
•Ensure that all engineering tasks are performed safely by employing risk/manual handling and COSHH assessments.•Review method statements, risk assessments or work permits to ensure they are appropriate for the intended tasks•Ensure that incidents and near misses are reported promptly to the appropriate external/internal departments.•An understanding of the safety data sheets that should be consulted when dealing with chemicals and lubricants.•Use departmental and site procedures for carrying out all tasks.•Carry out all electrical & inst. Isolations and reinstatements as required.•Undertake planned maintenance across site including production, utilities, effluent treatment, tank farm, heating and ventilation system, laboratories, and offices.•Carry out checks on automated process systems (DCS), local control systems (PLC) and interlocks to ensure that they are functioning within established parameters.•Calibrate instruments on site, both individually and collectively.•Carry out repairs and react to breakdowns as directed through maintenance request orders issued by electrical & instrument plant engineer.•Plan the daily workload, taking into account the planned maintenance requirements and the demands of production.•To assess problems, aid in the diagnosis of faults and carry out necessary repairs•Complete planned maintenance request orders correctly including recording problems, route causes and actions taken to remedy the situation.•Ensure that testing equipment is used correctly and is within its own calibration schedule prior to use. •Participate in a culture of continual improvement in the standards of quality.•Work with contractors as necessary (e.g. HVAC contractors) and assist if required.•Install and commission all new instrument systems in conjunction with a Project Engineer. Show less
-
-
Education
-
The Open University
Professional Certificate in Management, Business Administration and Management, General
Community
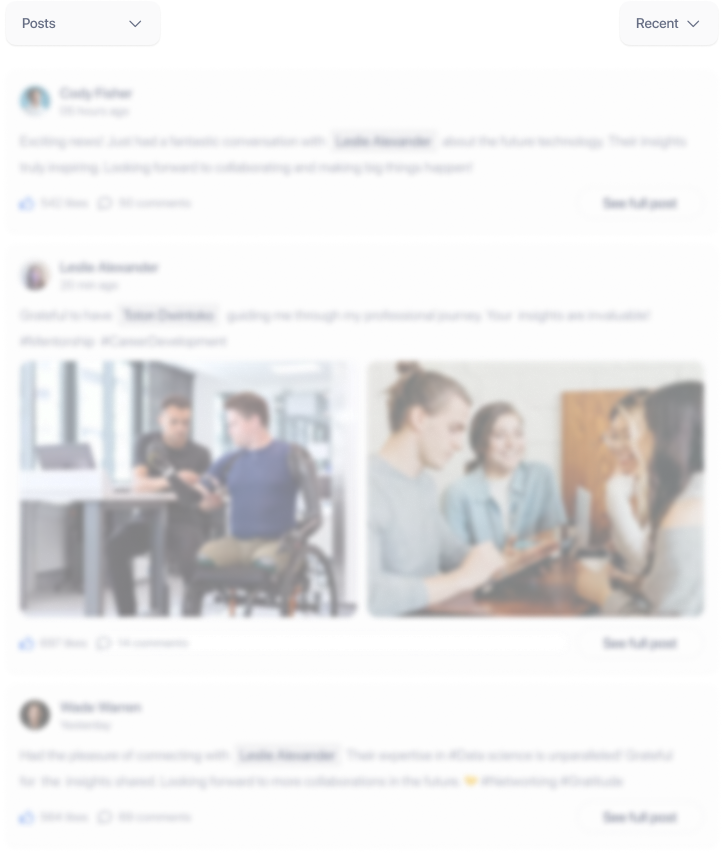